外文翻譯-點線嚙合齒輪傳動
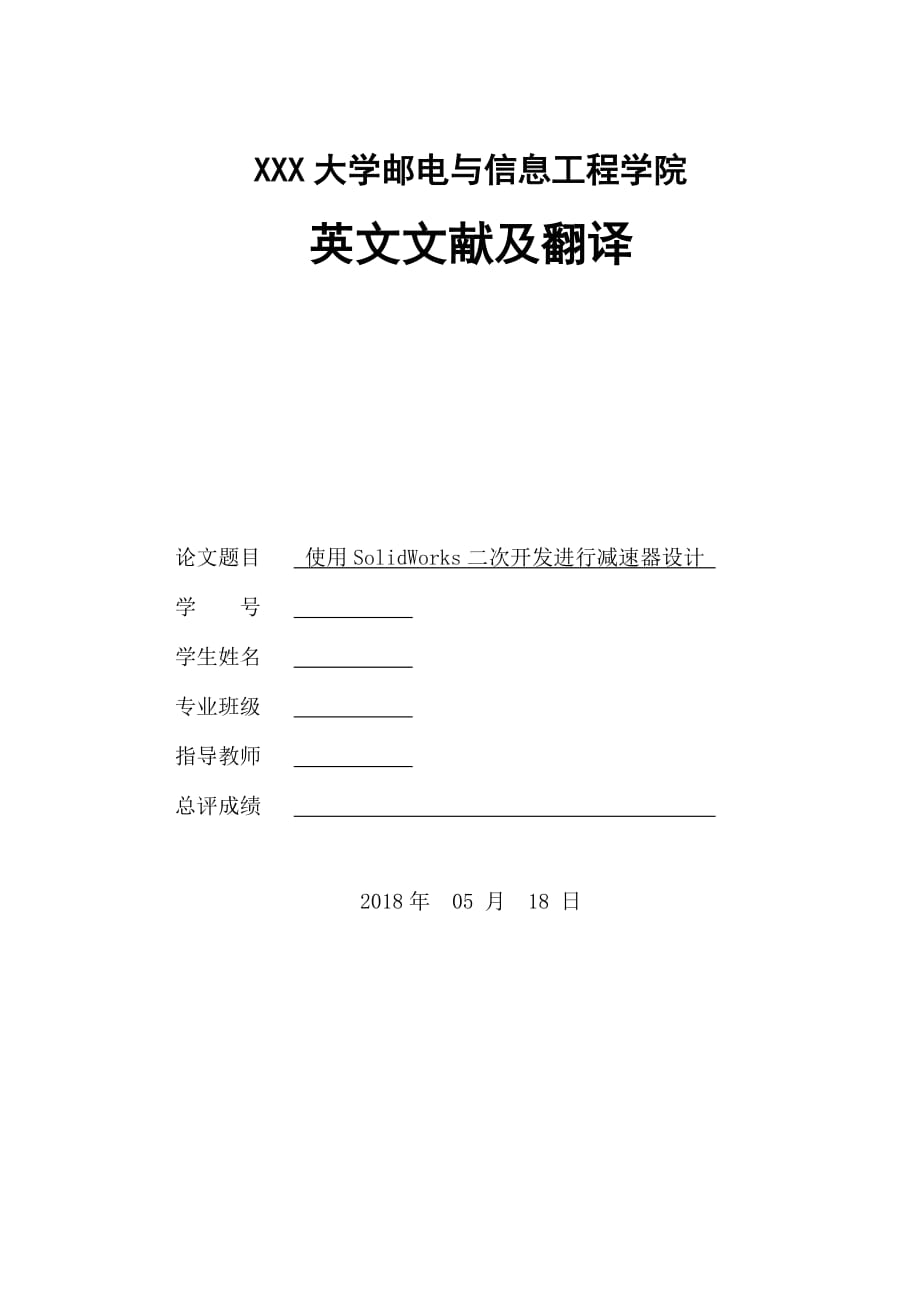


《外文翻譯-點線嚙合齒輪傳動》由會員分享,可在線閱讀,更多相關(guān)《外文翻譯-點線嚙合齒輪傳動(13頁珍藏版)》請在裝配圖網(wǎng)上搜索。
1、 XXX大學(xué)郵電與信息工程學(xué)院 英文文獻(xiàn)及翻譯 論文題目 使用SolidWorks二次開發(fā)進(jìn)行減速器設(shè)計 學(xué) 號 學(xué)生姓名 專業(yè)班級 指導(dǎo)教師 總評成績 2018年 05 月 18 日 外文資料翻譯 資料來源:Sprin
2、ger 文章名:Transmission of point-line meshing gear 書刊名:《Int J Adv Manuf Technol》 作 者:Qihan Luo, Haixiang Li, Junrong Wang, Yuchuan Zhang, Hai Huang 出版社:Springer-Verlag 分 類:ORIGINAL ARTICLE 頁 碼:P845~P855 文 章 譯 名: 點線嚙合齒輪傳動 姓 名: 學(xué) 號: 指導(dǎo)教師(職稱):
3、 專 業(yè): 班 級: 所 在 學(xué) 院: Transmission of point-line meshing gear Abstract The complexity of the design of multi-stage reducers lies in the strong and often intractable connections between the design variables defining its sub-systems. In other words, an optimal re
4、ducer is generally not an assembly of components optimized in isolation, a fact overlooked by many conventional design heuristics. For instance, the impact of a certain choice of gear width and center distance may yield a minimum mass gearing, but the selection of this gearing may cascade through su
5、bsequent steps of the design process (sizing of shafts, further stages, bearings, housing, etc.) to ultimately lead to a heavier reducer than if a slight compromise had been made on the choice of that first gearing. A typical example might be that selecting a smaller than optimal gear diameter (and
6、 a correspondingly greater contact width) could yield a somewhat heavier gearing,but a more compact layout and therefore a much lighter housing; it is worth mentioning though that in reality the impact on the overall objective tends to be much less direct and therefore much more obscure than in this
7、 example. Of course, in all but a few trivial cases, it is impossible to tell what that first compromise should have been, let alone what any subsequent choices should have been made with the overall goal in mind, instead of concentrating on the subsystem in hand. The chief reasons impeding a truly
8、 ‘holistic’ reasoning at every step of the design heuristic are the sheer number and the highly non-linear nature of the constraints and the objectives, the large number of design variables and the complexity of the interactions between them. Additionally,analytical models may not be available for t
9、hese interactions and constraints, precluding higher level analytical calculations that could predict the global effect of local design decisions. Point-line meshing gear is a new type of meshing transmission. It possesses the merit of involute gear that can be manufactured easily and separately. I
10、t also possesses the feature of high contact strength of arc gear wheel. Thus it has greater power, lower noise, and higher efficiency to bear the weight. Not only has single point-line meshing gear (similar to single arc gear wheel) and double point-line meshing gear (similar to double arc gear whe
11、el) been developed, but also a small tooth number of point-line meshing gear which can be only two or three. In this article, the meshing theory, design calculation, sealing graph of the parameter selection, manufacturing, bearing ability test and the example of its applications in various places ar
12、e introduced. The point-line meshing gear can be processed in common works, which process the ordinary involute gears, such as rolling tooth processing and milling tooth processing. Keywords Point-line gear . Gear wheel . Transmission 1 What is the point-line meshing gear? According to the meshin
13、g quality, gear transmission can be divided into two types. Type I is the line meshing gear. When they are meshing, the contact curve is a line or an arc line, such as involute or cycloid gear. Because its manufacture technology is simple, the involute gear is widely used in industry, and becomes do
14、minant. But the main application of involute gear is the meshing between convex profiles, where the contact stress is very large and the load capacity is low. Type II is the point meshing ransmission such as circular-arc gear. In the 1950s, circular-arc gear technology was imported from the Soviet U
15、nion. Circular-arc gear consists of two basic components: concave contour and convex contour. The contact curve is a point when meshing, and the curve after loading distortion is a surface meshing. Then the contour stress becomes smaller, and its load capacity becomes larger. But its manufacturing t
16、echnology is more complex, it needs the special hob, and the load capacity will descend when centre distance error exists. The pinion in the point-line meshing gear is a special modified short teeth. The top of the gear wheel is the convex contour of involute, its bottom is the concave contour of
17、the transitional curve. When they are meshing, there exists not only line meshing (the contact curve is a line) but also point meshing (the meshing is between concave and convex contour). So we call this type of gear transmission point-line meshing gear transmission (Fig. 1). It is a new type of mes
18、hing gear transmission. 2 The characteristics of point-line meshing gear Transmission 1. Easy manufacture The point-line meshing gear is processed by means of an ordinary involute gear cutting hobbing in common machine tools, or by means of an ordinary involute gear milling in a common grinding m
19、achine (Fig. 2); circular-arc gear is processed by special cutting hobbing. 2. Separability When there is a tolerance in manufacturing, transmission ratio and contact line are not changed, such as for involute gear. 3. Good performance of running in and little wear Idle running in the pair of gea
20、rs can completely mesh each other in the whole height and length very quickly, so there is little wear. 4. High strength and long life-span The contact strength of point-line meshing gear is about 2~3 times as much as that of involute gear. The bending strength is about 1.15 times that of involute
21、 gear. When broken down, the fracture of an involute gear tooth is slanting, and the fracture of a circular-arc gear tooth is crescent, while that of a point-line meshing gear tooth runs along the whole length of the tooth as shown in Fig. 3. 5. Very low noise Its noise is 5–10 dB(A) lower than th
22、at of involute gear. Involute gear’s noise becomes higher with more load, but point-line meshing gear is the opposite, its noise will descend 3–4 dB(A) from the no-load. 6. High efficiency The efficiency of the two grade reducer can reach 97% or more, and that of the gear pair can be more than 98%
23、. 3 The tooth profile equation of point-line meshing gear When point-line meshing gear is processed with the generation laws (rolling or mill tooth), its tooth profile equation are developed as follows. Equations of the involute curve of the point-line meshing gear can be stated as: Equations of
24、the transition curve of the point-line meshingcan be written as: 4 The teeth meshing theory of point-line gears When a pair of point-line gears are meshing, the meshing process includes two parts: part I is that the involute parts of the two gears mesh each other, forming line contact, with the we
25、ight right on the end face; and part II is that the involute of small and big gear wheels are in contact with the transition curve, forming point gearing. 1. Point-line meshing gear transmission fits basic law of tooth outline meshing When the point-line meshing gear is meshing, its mesh line N1N2
26、 becomes the inside tangent of two basic circles, and when it is diving, as shown in Fig. 4, the big and small wheel’s beginning mesh point is B2, and termination mesh point is J(B1) (point of intercession of the involute on big gear and the transition curve). So line meshing is formed between B2 an
27、d J, and point gearing is formed at the termination mesh points, while the mesh point moves parallel along the direction of the axis. All contact points of the common normal pass through the pitch point P, whose meshing accords with the basic law of tooth profile meshing. 2. The condition of contin
28、uous transmission If the involute tooth profile of the small gear wheel and the above parts of the big gear wheel’s point J achieve continuous transmission, we must satisfy: Under general circumstances, it can be fashioned as helical or spur tooth. 3. The correct meshing condition When the point
29、-line meshing gear is fashioned as helical gear, we must satisfy according to helical gear: 4. The weight right The weight right of the point-line meshing gear is the same as for helical tooth of cylindrical gear, and includes two parts: the weight right of the end surface and axial weight right.
30、 5. The change position factor The factor is decided according to the no-side crack meshing equation just as the change position gear transmission. 6. The curvature radius of the contact point When a pair of gears reach meshing terminal point J, the curvature radius of the small and big gear whee
31、l in the mesh point must be smaller than that of the big gear wheel in point J so as to enlarge the contact area in protruding and concave gears meshing and to avoid the interference. 5 Types of point-line meshing gear Point-line meshing gear accomplish the following three kinds of forms according
32、 to the teeth meshing principle: 1. Single point-line meshing gear—usually called just point-line meshing gear—can accomplish the oblique tooth, or the straight tooth, as shown in Fig. 5. 2. Double point-line meshing gear, namely, half of the concave tooth outline of the transition curve, the othe
33、r involute part is protruding tooth outline. After meshing the teeth mutually, they form double point meshes and the thread meshes. The double point-line meshing gear can also be accomplished as straight tooth and oblique tooth, as shown in Fig. 6. 3.‘Few tooth number’ of point-line meshing gear. L
34、owest tooth number of its small gear wheel can achieve 2–3 teeth, thus its drive ratio can be very large (see Fig. 7). The gear wheel of the three model types can function in the soft tooth surface, in middle rigidity tooth surface and in rigidity tooth surface gear wheel. 6 Size calculation of t
35、he point-line mesh gear Calculations for most part sizes are the same as for the involute gear. take the standard, while The radius of the graduation circle: The terminal pressure angle: The node circle radius: The theoretical centre distance: The real center distance: The terminal mesh
36、 angle: The top circle radius of the small gear: The top circle radius of the big gear: Coefficients of the pair gear changing their positions:xn1, xn2. 7 The sealing graph of point-line meshing gear 1. Why will sealing graph be drawn? The former Soviet Union scholar put forward the formulati
37、on of the sealing graph in which change of position coefficient of the involute gear is selected, and it has solved the relation between the change of position coefficient of the involute gear and the other influencing factors. The change of position coefficient of the involute gear in the sealing g
38、raph is not to be used to calculate the point-line meshing gear. Selection of the change of position coefficient for the point-line meshing gear is not decided by several kinds of factors of the involute gear. It is more complex, there are more influencing factors, it is not only related to the chan
39、ge of position coefficient (x1, x2) of the small and big gear, but also the helical angle. The sealing graph of the point-line meshing gear depends on the change of position coefficient of the big gear and the helical angle β. Gear can not run regularly if improper selection occurs because of bad i
40、nterference or the thickness of the gear is too thin to bear the load. Indicating on the basis of a large number of calculations, the sealing graph is independent of the center distance and modulus but chiefly dependent on the parameter of tooth number Z1, Z2 and tools. 2. The significance of every
41、 curve in the sealing graph The abscissa of the figure is “?X2” , and the Y ordinate is “β” . Each curves meaning can be seen in Fig. 8 with definitions as follows. (a) xn2max - The biggest change position coefficient of the big gear wheel (the root cutting of confinement curve of small gear wheel)
42、 (b) xn2min - Confinement curve of the root cutting of the big gear wheel (c) Sa1=0 or Sa1=0.25 mn - The confinement curve about the thickness of the tooth top of the small gear (d) C1=0 or C1=0.1 mn - The confinement curve about the 0~0.1 mn gap between the top of the big gear and the bottom of
43、the small gear (e) sj2=0.8 mn or 1.2 mn - The thickness of the tooth of point J where the big gear’s involute curve and the transition curve intersect (f) BP - The distance from the point where the top of the tooth of the big gear and the meshing line intersect the node PJ2 - The distance from wh
44、ere point J of the big gear and the meshing line intersect the node point BP=0 Indicates meshing in the node PJ2>0 BP<0 - Mesh outside the node PJ2>0 BP>0 - Mesh in front and behind the node (g) Drt=0.01 mn; 0.02 mn - Interference quantity between the transition curve of the big gear and the spir
45、al curve of the top of the small gear’s tooth (h) J1m=0.2 mn or 0.4 mn - Meshing arc length when the point J of the big gear meshes the top of the small’s tooth (i) h2= 1.7 mn; 1.9 mn - Full height of the big gear’s tooth (j) h1 = 1.6 mn; 1.8 mn - Full height of the small gear’s tooth (k) End su
46、rface meshing angle when big gear and small gear are meshing (l) ?=1; 1.2 - Weight right in the end surface (m) hja2=0.5 mn; 0.9 mn - Height of the involute curve part of the big gear (n) Curve whose slip ratio is equal for the big and small gear (m) cp1=12,13 - Rigidity of the single gear (o)
47、cr1=13,16 - Synthesis rigidity In the sealing graph, with the change of the tooth number, each curve changes concurrently. But it is not possible to display each curve. Its several main curves can form by the surrounding curve. So the parameters x2 and β can be selected in the closing graph and sho
48、uld be selected according to need. 8 Manufacturing process of point-line meshing gear For point-line meshing gear’s manufacturing, it is usually processed with the rolling tool that can handle the involute gear on the rolling or mill tooth machine. Its process method is the same as that for the in
49、volute gear. So it can be processed in common works, which use the ordinary involute gears. The new hobbing cutter does not need to be purchased or have been made to order. 1. The process of small gear wheel The small gear wheel is usually a special short tooth helical involute gear wheel which ha
50、s change of position; its process method is the same as the involute gear’s process. But the cutting depth is different from the involute gear, its depth is smaller than that of involute gear, and the tool must be adjusted when rolling tooth. 2. The process of big gear wheel The big gear wheel is
51、usually a helical involute gear wheel which has change of the position, but the height of the involute curve is just 1/3 of the whole tooth height, the other 2/3 is the transition curve. Its process method is the same as the involute gear’s process, although cutting tooth depth is different from inv
52、olute gear. 9 Testing point-line meshing gear Tests of soft tooth surface for point-line meshing gear. Tests of soft tooth surface for point-line meshing gear are done on the open test-bed, as shown in Fig. 9. The test reducer is the ZQ350 whose involute curve is applied in industry production. T
53、he involute gear wheel is changed into point-line meshing gear under center distance and the circumstance and the speed ratio are unchanged. All parameters are as in Table 2. The measurement of efficiency and noise is accomplished by installing two torque and rotation speed sensors at the front an
54、d back of a point-line meshing gear box, connecting them and a data recording instrument, and then printing the data directly while test drawing a graph (Fig. 10). The efficiency of the point-line mesh reducer can be as high as more than 97% and that of the gear pair can be more than 98%. For the no
55、ise test apply the 2203 instrument (B&K Precision, USA). In order to erase the surrounding noise, we use the test with the glass fiber to seal the motor; the test distance is 1 m, finding an average while testing nine-point noise. The noise curve can be seen in Fig. 11 with no load. It can be said t
56、hat the noise is 60 dB(A) when the rotation speed is under 1,000 r/ min. Under different power, the noise graph of the frequency spectrum analysis instrument (Fig. 12) displays the meshing frequency of the high-speed grade. It can be said that the meshing frequency of the highspeed grade is less tha
57、n 65 dB(A). The next test is for the load capacity. The sample is the soft tooth surface gear of the point-line meshing gear box; therefore, the fatigue deformation appears first and then bending rupture. Thus, we must test its contact fatigue strength, and later the bending fatigue strength. Loade
58、d data is as shown in Table 3. The test results indicate that point rust appears first on the big gear of the low speed grade while the small gear has the point rust only in the root of the tooth. Small and big gear of the high speed grade only have several points of rust. The torque of the low spe
59、ed grade compared with that of the involute gear is given byK=518.5/177.15=2.93. The load capacity of the point-line meshing gear is 2.93 times that of the involute gear. Bending rupture appears in the big gear of the low speed grade, rupturing along the whole tooth length as shown in Fig. 3. Deform
60、ation of the involute gear appears in the small gear of the low speed grade. The torque of the big gear is 906.9 Nm. Thus, K=1038.25/906.9=1.15. The bending strength is more than 15% that of the involute gear, though it may have more strength if suitable parameters are selected. The test of the mid
61、dle rigidity tooth surface. The test on efficiency and noise is done on the open test-bed as shown in Fig. 13 and parameters are listed in Table 4. The test results are given in Fig. 14. The data output indicates that the efficiency of the reducer may be up to 95.8%; the test distance is 1 m, the a
62、verage found while testing nine-point noise; and the average noise is 67.8 dB(A). Test on the load capacity is performed on the open test lab as shown in Fig. 15. The parameters are given in Table 5 when the circular times are up to 5107 of the high speed shaft in the reducer, and no deformation ap
63、pears on the gears. Here the power is 44 KW; the rating power is 17 KW as the involute gear. The load capacity of the point-line meshing gear is 2.588 times than that of the involute gear. Analysis of the two tests. Comparing the tests of the soft tooth surface and middle rigidity tooth surface, it
64、 can be said that the efficiency of the two kinds of gear are both higher, the noise is lower (5–10 dB(A)) than that of involute gear, and the load capacity is two or three times that of the involute gear. It also indicates that its load capacity is more than 1–2 times that of the involute gear. Te
65、st of the rigidity tooth surface point-line meshing gear. The test parameter are given in Table 6. The test is performed on the closed test-bed as shown in Fig. 16 with the test results given in Table 7. The test results indicate that when the rigidity tooth surface point-line meshing gear is loade
66、d to 64.11 KW, it still isn’t parted. In fact it has potential. Now the bending intensity of a high speed shaft is 1.56 times as much as the power of an involute gear such thatK=64.11/41.05=1.56. The measure of noise. When the gear was loaded to 483 N.m, the noise is 77.25 dB(A), as shown in Fig. 17. When the gear was loaded to 598 N.m the noise is 75.875 dB(A). The reducing noise is approximately 2 dB(A), as shown in Fig. 18. The test results indicate that the noise of the rigidity tooth surf
- 溫馨提示:
1: 本站所有資源如無特殊說明,都需要本地電腦安裝OFFICE2007和PDF閱讀器。圖紙軟件為CAD,CAXA,PROE,UG,SolidWorks等.壓縮文件請下載最新的WinRAR軟件解壓。
2: 本站的文檔不包含任何第三方提供的附件圖紙等,如果需要附件,請聯(lián)系上傳者。文件的所有權(quán)益歸上傳用戶所有。
3.本站RAR壓縮包中若帶圖紙,網(wǎng)頁內(nèi)容里面會有圖紙預(yù)覽,若沒有圖紙預(yù)覽就沒有圖紙。
4. 未經(jīng)權(quán)益所有人同意不得將文件中的內(nèi)容挪作商業(yè)或盈利用途。
5. 裝配圖網(wǎng)僅提供信息存儲空間,僅對用戶上傳內(nèi)容的表現(xiàn)方式做保護(hù)處理,對用戶上傳分享的文檔內(nèi)容本身不做任何修改或編輯,并不能對任何下載內(nèi)容負(fù)責(zé)。
6. 下載文件中如有侵權(quán)或不適當(dāng)內(nèi)容,請與我們聯(lián)系,我們立即糾正。
7. 本站不保證下載資源的準(zhǔn)確性、安全性和完整性, 同時也不承擔(dān)用戶因使用這些下載資源對自己和他人造成任何形式的傷害或損失。
最新文檔
- 110中國人民警察節(jié)(筑牢忠誠警魂感受別樣警彩)
- 2025正字當(dāng)頭廉字入心爭當(dāng)公安隊伍鐵軍
- XX國企干部警示教育片觀后感筑牢信仰之基堅守廉潔底線
- 2025做擔(dān)當(dāng)時代大任的中國青年P(guān)PT青年思想教育微黨課
- 2025新年工作部署會圍繞六個干字提要求
- XX地區(qū)中小學(xué)期末考試經(jīng)驗總結(jié)(認(rèn)真復(fù)習(xí)輕松應(yīng)考)
- 支部書記上黨課筑牢清廉信念為高質(zhì)量發(fā)展?fàn)I造風(fēng)清氣正的環(huán)境
- 冬季消防安全知識培訓(xùn)冬季用電防火安全
- 2025加強(qiáng)政治引領(lǐng)(政治引領(lǐng)是現(xiàn)代政黨的重要功能)
- 主播直播培訓(xùn)直播技巧與方法
- 2025六廉六進(jìn)持續(xù)涵養(yǎng)良好政治生態(tài)
- 員工職業(yè)生涯規(guī)劃方案制定個人職業(yè)生涯規(guī)劃
- 2024年XX地區(qū)黨建引領(lǐng)鄉(xiāng)村振興工作總結(jié)
- XX中小學(xué)期末考試經(jīng)驗總結(jié)(認(rèn)真復(fù)習(xí)輕松應(yīng)考)
- 幼兒園期末家長會長長的路慢慢地走