液壓傳動課程設計.docx
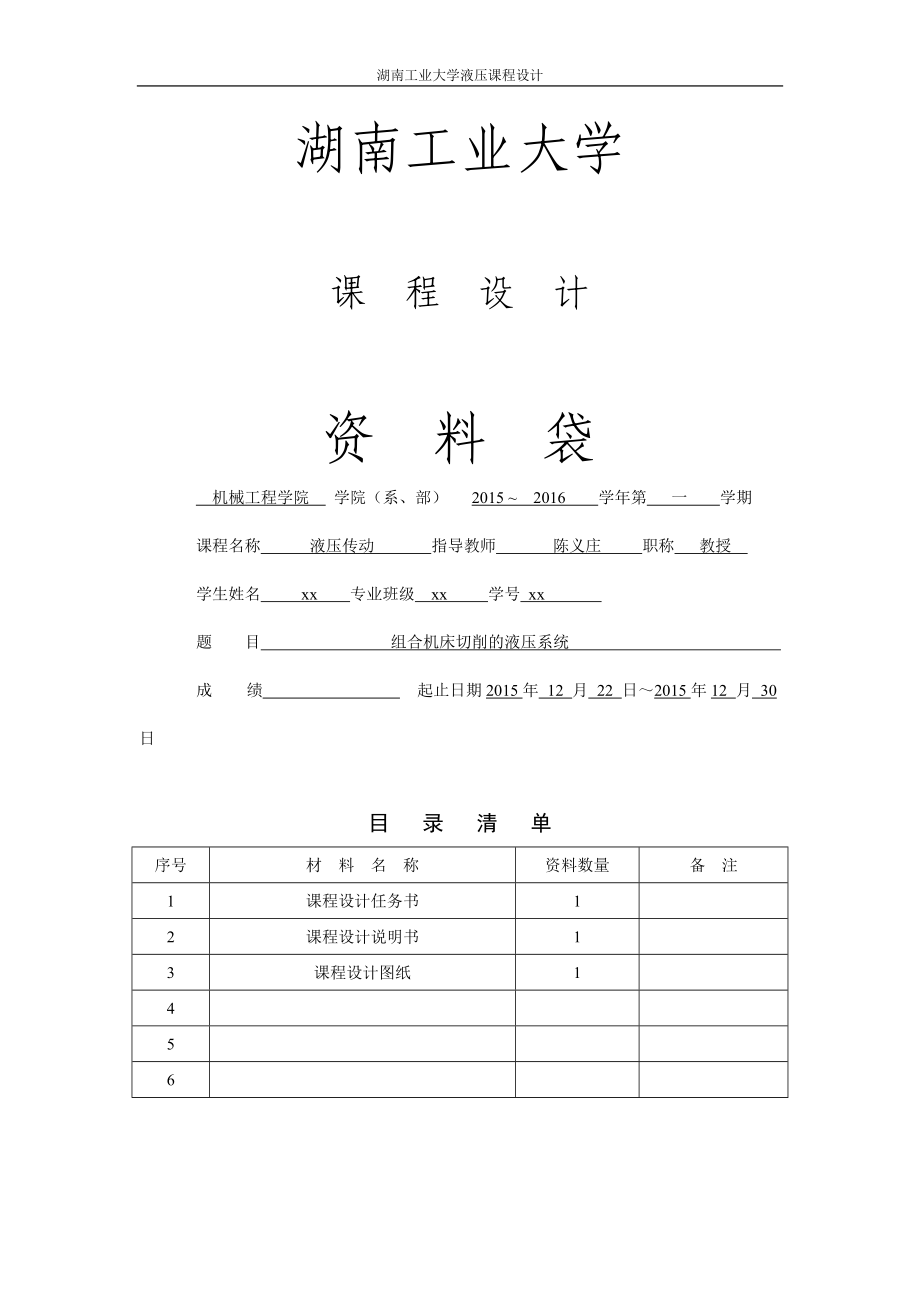


《液壓傳動課程設計.docx》由會員分享,可在線閱讀,更多相關《液壓傳動課程設計.docx(19頁珍藏版)》請在裝配圖網上搜索。
1、湖南工業(yè)大學液壓課程設計 湖南工業(yè)大學 課 程 設 計 資 料 袋 機械工程學院 學院(系、部) 2015 ~ 2016 學年第 一 學期 課程名稱 液壓傳動 指導教師 陳義莊 職稱 教授 學生姓名 xx 專業(yè)班級 xx 學號 xx 題 目 組合機床切削的液壓系統(tǒng) 成 績
2、起止日期2015年 12 月 22 日~2015年12 月 30日 目 錄 清 單 序號 材 料 名 稱 資料數量 備 注 1 課程設計任務書 1 2 課程設計說明書 1 3 課程設計圖紙 1 4 5 6 《液壓與氣壓傳動》課程設計 設計說明書 題 目 名 稱: 組合機床切削的液壓系統(tǒng) 學 院(部): 機械工程學院 專
3、 業(yè): 機械工程 學 生 姓 名: xx 班 級: xx 學號 xx 指導教師姓名: xx 評 定 成績: 目 錄 0.設計任務書 …………………………………………………………2 1. 設計要求及工況分析 ………………………
4、………………………3 2. 主要參數的確定 ……………………………………………………6 3. 液壓系統(tǒng)圖的擬定 ………………………………………………9 4. 液壓元件的計算與選擇 ……………………………………10 5. 液壓系統(tǒng)的性能驗算………………………………………………13 6. 參考資料……………………………………………………………15 7.設計總結 ……………………………………………………………16 課程設計任務書 2015 —2016學年第 1學期 機械工程 學院(系、部) 機械工程 專業(yè)x
5、x 班級 課程名稱: 液壓與氣壓傳動 設計題目: 組合機床切削的液壓系統(tǒng) 完成期限:自 2015年 12 月 22 日至 2015 年 12月 30 日共 1 周 內 容 及 任 務 一、 設計的任務與主要技術參數 設計一組合機的液壓系統(tǒng)。組合機床切削過程要求實現:快進→工進→快退→停止,由動力滑臺驅動工作
6、臺。最大切削力F=30000N,移動部件總重量G=3000N;行程長度400mm(工進和快進行程均為200mm),快進、快退的速度均為4m/min,工作臺的工進速度可調(50~1000)mm/min;啟動、減速、制動時間△t=0.5s;該動力滑臺采用水平放置的平導軌。靜摩擦系數fs=0.2;動摩擦系數fd=0.1。 二、設計工作量 1)明確設計要求,進行工況分析; 2)主要參數的確定; 3)擬定液壓系統(tǒng)圖; 4)計算與選擇液壓原件 5)液壓系統(tǒng)的性能驗算; 6)繪制工作圖、編寫技術文件。 進 度 安 排 起止日期 工作內容 12.22 明確設計要求
7、,進行工況分析 12.23- 液壓傳動設計 12.28-12.30 繪制工作原理圖,整理說明書 主要 參考 資料 [1] 劉忠偉.液壓傳動與氣動.北京:化學工業(yè)出版社,2014. [2] 張利平.液壓控制系統(tǒng)及設計.北京:化學工業(yè)出版社,2006. [3] 丁樹模.液壓傳動.第二版.北京:機械工業(yè)出版社,1999. 指導教師: xx 2015 年12 月 10 日 系(教研室)主任: 2015 年12 月 10 日 1. 設計要求及工況分析 1.1
8、設計要求 要求設計的機床動力滑臺液壓系統(tǒng)實現的工作循環(huán)是“快進→工進→快退→停止”。主要性能參數與性能要求如下:最大切削力F=30000N,移動部件總重量G=3000N;行程長度400mm(工進和快進行程均為200mm),快進、快退的速度均為4m/min,工作臺的工進速度可調(50~1000)mm/min;啟動、減速、制動時間△t=0.5s;該動力滑臺采用水平放置的平導軌。靜摩擦系數fs=0.2;動摩擦系數fd=0.1;液壓系統(tǒng)中的執(zhí)行元件是液壓缸。 1.2負載與運動分析 (1)工作負載 由設計要求可知最大工作的負載F=30000N (2)慣性負載 Fm=Gg?v?t=30009.
9、8460*0.5=40.82≈41N (3)摩擦負載 因為采用的動力滑臺式是水平導軌,因此作用在上面的正壓力N=G=3000N。 靜摩擦阻力 Ffs=fs?N=0.2*3000=600N 動摩擦阻力 Ffd=fd?N=0.1*3000=300N 取液壓缸的機械效率ηm=0.90,得出的液壓缸在各工作階段的負載如表1.2.1所示。 工況 負載組成 負載值F/N 推力F/ηm/N 啟動 加速 快進 工進 快退 F=Ffs F=Ffd+Fm F=Ffd F=Ffd+F F=Ffd 600 341 300 30300 300 66
10、7 379 333 33667 333 表1.2.1 液壓缸在各工作階段的負載值 根據液壓缸上述各階段的負載可繪制如圖1.2.1(另附)所示的推力循環(huán)圖F-l。速度圖中,快進、快退v1=v3=4m/min,快進行程l1=200mm,工進行程長度l2=200mm,快退l3=l1+l2=400mm,工進速度取可調最?。ù螅┧俣葀2=50(1000)mm/min 2. 主要參數的確定 2.1初選液壓缸工作壓力 所設計的動力滑臺在工進時負載最大,在其他工況負載都不高,參考《液壓與氣壓傳動》中的表9-2和9-3初選液壓缸的工作壓力p1=4MPa。
11、2.2計算液壓缸的主要尺寸 鑒于動力滑臺要求快進、快退的速度相等,液壓缸可選用單桿式的并在快進時作差動連接。此時液壓缸無桿腔的工作面A1積應該是有桿腔A2的兩倍,即活塞外徑d與液壓缸的內徑D有d=22D的關系。 在切削加工時,液壓缸回油路上必須有背壓P2,以防止切削完畢后因負載 變小而濡染往前沖??扇2=0.8MPa??爝M時液壓缸雖然作差動連接,但是由于油管中有壓降?p存在,有桿腔的壓力必須大于無桿腔,估算時可取?p約為0.5MPa。快退時回油腔有背壓,這時P2也可按0,5MPa估算。 由工進時的推力計算液壓缸的面積 Fηm=A1p1-A2p2=A1p1- A12
12、p2 A1=Fηmp1-p22=336674-0.82=0.0094m2=94cm2 D=4A1π=10.94cm d=0.707D=7.73cm 當按GB 2348-1980將這些直徑圓整成接近標準值得D=11cm,d=8cm。由此求得液壓缸兩腔的實際有效面積A1=πD24=95.03cm2,A2=πD2-d24=44.77cm2。經檢驗,活塞桿的強度和穩(wěn)定性均符合要求。 根據上述D和d的值,可以估算液壓缸在不同階段的壓力、流量和功率,如表2.2.1。并據此畫出如圖2.2.1所示的液壓缸工況圖(另附),其中紅筆所畫、黑筆所畫和鉛筆所畫線分別表示P、q、p。
13、 工況 負載 F/N 回油腔壓力 p2/MPa 進油腔壓力p1/MPa 輸入流量 q/L?min-1 輸入功率 P/Kw 計算式 快進 (差動) 啟動 667 0 0.578 - - p1=(F+A2?p)/(A1-A2) q=(A1-A2)v1 P=p1q 加速 3379 1.021 0.521 - - 恒速 333 1.012 0.512 20.104 0.17 工進 33667 0.8 3.92 0.48-9.5 0.031- 0.621 p1=(F+A2p2)/A1 q=A1v2
14、 P=p1q 快退 啟動 667 0 0.149 - - p1=(F+A1p2)/A2 q=A2v3 P=p1q 加速 349 0.5 1.146 - - 恒速 333 1.136 17.908 0.339 表2.2.1 液壓缸在不同工作階段的壓力、流量和功率值 3. 液壓系統(tǒng)圖的擬定 3.1選擇基本回路 (1)選擇調速回路 由圖2.2.1中的曲線得知,這臺機床液壓系統(tǒng)的功率小,滑臺的速度低,工作負載變化小,采用進口節(jié)流閥的調速形式,為了防止切削時滑臺突然前沖的現象
15、,回油路上應設置背壓閥。 由圖2.2.1可知,液壓缸交替地要求油泵提供低壓大流量和高壓小流量的液壓油。最大流量和最小流量之比約為42,而快進、快退所需要的時間t1和工進時間t2分別為 t1=l1v1+l3v3=9(s) t2=l2v2=12~240(s) 即t2t1≈(1~27)。因此,為了提高效率、節(jié)省能量,選用如圖3.1.1所示(另附)的雙聯式葉片泵。 (2)選擇快速運動和換向回路 快進回路選用差動連接,選用如圖3.1.2所示(另附)的形式?;赜颓徊捎脝蜗蜷y來實現差動鏈接。 (3)選擇速度換接回路 滑臺快進到工件時,輸入液壓缸的流量由20.096L/min下降到0.48(9
16、.5)L/min,滑臺速度變化很大,所以選用行程閥來控制速度的換接,以減少液壓沖擊,初步如圖3.1.3所示(另附)。 (4)選擇調壓回路和卸荷回路 液壓系統(tǒng)調壓可由雙聯葉片泵實現,卸荷可通過中衛(wèi)機能解決。 3.2組成液壓系統(tǒng) 方案一:將上面選出的液壓基本回路組合,可得初步的液壓基本回來,如圖3.2.1所示(另附),但是回路中還存在許多問題需要更正。 在圖3.2.1中,改進(1):在液控單向閥下方需要加一個背壓閥,實現工進背壓,同時還需要并聯一個單向閥以便于實現快退功能。改進(2):在回油路中,背壓閥的存在會導致差動連接中的單向閥被頂開無法使油液回流到油箱,所以將差動連接中的單向閥更換
17、成順序閥,并且該順序閥的頂開壓力必須大于背壓閥的壓力。改進(3):將液控單向閥的外控k口必須接在調速閥和液壓缸之間,否則在剛開始的差動連接油路無法實現其功能。改進(4):在快退回路的回油路中,電磁閥可能有一部分時間處于左位,回油路只能經過調速閥,無法快退,所以應該在調速閥旁邊并聯一個單向閥。改進(5):在液壓缸的無桿腔的接口處還需要加一個壓力繼電器已便于控制三位四通換向閥換向。如圖3.2.2所示(另附)。 其電磁閥和電磁閥動作順序如表3.2.1所示。 動作名稱 電磁鐵 電磁閥 1YA 2YA 快進 + - - 工進 + - + 死檔鐵停留 + - + 快退
18、 - + 原位停止 - - - 表3.2.1 方案一電磁鐵和電磁閥動作順序 液壓系統(tǒng)工作原理及動態(tài) (1)快進 按下啟動按鈕,1YA通電,電磁閥5左位接入系統(tǒng)。主油路接通。此時處于空載,系統(tǒng)壓力低,順序閥3處于關閉狀態(tài),兩泵同時供油,液壓缸快進。此時液壓油由電磁閥10右位進入液壓缸左位,液控單向閥8關閉,順序閥11接通,液壓缸差動連接。 主油路的油液流動路線: 進油路:雙聯葉片泵2→換向閥(左位)5→電磁閥(右位)10→液壓缸(無桿腔)14 回油路:液壓缸(有桿腔)14→順序閥11→液壓缸(無桿腔)14 (2)工進 當滑臺到達預定位置,觸碰到電磁閥
19、開關13以此控制電磁閥 10接通左位,1YA繼續(xù)通電,換向閥5左位接通,液壓油由調速閥9進入液壓缸 14左腔,此時由于負載變大,系統(tǒng)壓力升高,液控單向閥8打開,順序閥3打 開,低壓大流量泵2A經順序閥3回油箱,系統(tǒng)只由高壓小流量泵2B供油,液壓 缸工進?;赜蜁r由于背壓閥6的壓力小于順序閥11的壓力,所以油液不會經過 順序閥11回到進油路。(由計算數據可調順序閥11的壓力為1.0MPa,背壓閥6 的壓力為0.5MPa) 進油路:高壓小流量泵2B→換向閥5(左位) →調速閥9→液壓缸14(無桿腔) 回油路:液壓缸14(有桿腔)→液控單向閥8→背壓閥6→換向閥5(左位) →油箱
20、 (3)死擋鐵停留 工進到達預定位置后,碰上死擋鐵,滑臺停止運動,實 現死擋鐵停留 (4)快退 滑臺碰上死擋鐵,運動停止,系統(tǒng)壓力繼續(xù)升高,當壓力達 到壓力繼電器12調定壓力時,換向閥2的右位接通控制右路。此時因為空載, 回油無背壓,系統(tǒng)壓力很低,雙聯葉片泵2兩泵同時供油,滑臺實現快退。這時 的主油路路線: 進油路:雙聯葉片泵2→換向閥(右位)→單向閥7→液控單向閥8→液壓缸(有桿腔)14 回油路:液壓缸(無桿腔)14→單向閥15→換向閥(右位)5→油箱 (5)原位停止 快到原位時,行程擋鐵壓下終點行程開關,所有電磁鐵 斷電,換向閥處于中位,系統(tǒng)
21、處于卸荷狀態(tài)。此時的主油路的流油路線: 雙聯葉片泵2→換向閥5(中位)→油箱 方案二:在方案一中速度換接被放置在液壓缸的無桿腔一側支路,在方案二中將速度換接回路放置在有桿腔一側支路,如圖2.3.3所示(另附)。其電磁閥和電磁閥動作順序如表3.2.2所示。 動作名稱 電磁鐵 行程閥 1YA 2YA 快進 + - - 工進 + - + 死檔鐵停留 + - + 快退 - + 原位停止 - - - 表3.2.2方案二電磁鐵和行程閥動作順序 液壓系統(tǒng)工作原理及動態(tài) (1)快進 按下啟動按鈕,1YA得電,電磁閥6左位接入系統(tǒng),主油路接通。此
22、時處于空載,系統(tǒng)壓力低,順序閥3處于關閉狀態(tài),兩泵同時供油,液壓缸快進。由于系統(tǒng)壓力低無法打開液控單向閥10,順序閥11接通,液壓缸差動連接。 主油路的油液流動路線: 進油路:雙聯葉片泵2→換向閥(左位)6→液壓缸(無桿腔)13 回油路:液壓缸(有桿腔)13→順序閥11→液壓缸(無桿腔)13 (2)工進 當滑臺到達預定位置,觸碰到行程閥12時,行程閥12被壓下,上位接入系統(tǒng),此時由于負載變大,系統(tǒng)壓力升高,液控順序閥3和液控單向閥10打開,低壓大流量泵2A經過順序閥3回油箱,系統(tǒng)只由高壓小流量泵2B供油,液壓缸工進。回油時由于行程閥接上位,調速閥9接入系統(tǒng)。并且,由于背壓閥7的調定
23、壓力小于順序閥11的壓力,所以油液不會經過順序閥11回到進油路。(順序閥11的調定壓力位1.0MPa,背壓閥7的調定壓力位0.5MPa) 進油路:高壓小流量泵2B→換向閥(左位)6→液壓缸(無桿腔)13 回油路:液壓缸13(有桿腔)→液控順序閥10→調速閥9→背壓閥7→換向閥(左位)6→油箱 (3)死擋鐵停留 工件到達預定位置后,碰上死擋鐵,滑臺停止運動,實現死擋鐵停留。 (4)快退 滑臺碰上死擋鐵后,運動停止,系統(tǒng)壓力繼續(xù)升高,當壓力達到壓力繼電器14調定的壓力時,換向閥6的右位接入系統(tǒng)右路。此時因為空載,回油路沒有背壓,系統(tǒng)壓力很低,雙聯葉片泵同時供油,滑臺實現快退。這時的主
24、油路路線: 進油路:雙聯葉片泵2→換向閥6→單向閥8→單向閥11→液控順序閥10→液壓缸(有桿腔)13 回油路:液壓缸(無桿腔)13→油箱 (5)原位停止 快到原位時,行程擋鐵壓下終點所有行程開關,所有電磁鐵斷電,換向閥處于中位,系統(tǒng)處于卸荷狀態(tài)。此時的主油路的流油路線: 雙聯葉片泵2→換向閥6(中位)→油箱 綜上所述:行程閥的閥口是逐漸關閉(或開啟)的,速度換接比較平穩(wěn),速度換接的平穩(wěn)性、可靠性以及精度都比方案一好,適合用于組合機床切削的液壓系統(tǒng)中,所以最終確定采用方案二。
25、 4. 液壓元件的計算及選擇 4.1確定液壓泵的規(guī)格和電動機功率 液壓缸整個工作循環(huán)中的最高壓力為3.92MPa,如果進油路上的壓力損失為0.8MPa,壓力繼電器調整壓力高出系統(tǒng)最高壓力位0.5MPa,則小流量泵的最高工作壓力壓力為: pp1=3.92+0.8+0.5=5.22MPa 大流量泵在快進運動時才向液壓缸14供油的,由圖2.2.1可知,快退時液壓缸中的工作壓力比快進時候大,若取進油路上的壓力損失為0.5MPa,則大流量泵的最高工作壓力為: pp1=1.126+0.5=1.636MPa 兩個液壓泵應向液壓缸提
26、供的最大流量為20.096L/min,如圖2.2.1可知,若回油路中的泄露按輸入流量的10%估算,則兩泵的總流量qp=1.1*20.96=22.1056L/min。而溢流閥最小聞流為3L/min,工進時最小輸入流量為0.48L/min,所以小流量泵的流量規(guī)格最小應為3.48L/min。 由以上壓力和流量的數值查閱產品樣本,最后確定選取PV2R12型雙聯葉片泵。 由于液壓缸在快退時輸入功率最大,即泵輸出壓力位1.636MPa,流量25L/min時的情況,如果取雙聯葉片泵的總效率ηp=0.75,則液壓泵的驅動原動機所需的功率為 P=pp?qpηp=1.636*106*25*10-3600.7
27、5≈0.91Kw 根據此數值查閱電機產品樣本,最后選定Y90S-4型電動機,其額定功率為1.1Kw。 4.2確定其他元件及輔件 (1)確定控制元件和輔助元件 根據液壓系統(tǒng)的工作壓力和通過各個控制閥類元件和輔助元件的實際流量,可以選出這些元件的規(guī)格和型號,表4.2.1為選用的型號和規(guī)格。 序號 元件名稱 估計通過流量 /L?min-1 型號 規(guī)格 1 濾油器 25 YYL-105-10 21MPa,90L/min 2 雙聯葉片泵 - PV2R12 14MPa,35.5和4.5L/min 3 液控順序閥 20 XF3-E10B
28、16MPa,10通徑 4 單向閥 25 AXQF-E10B 5 溢流閥 4.5 YF3-E10B 6 三位四通電磁閥 45 7 背壓閥 <1 XF3-E10B 8 單向閥 25 AF3-Ea10B 9 調速閥 <1 AXQF-E10B 31.5MPa,10通徑 10 液控單向閥 25 DFY-L10H3 0.35MPa,10通徑 11 單向閥 25 X3F-B10H 31.5MPa,10通徑 12 單向閥 25 AF3-E10B 16MPa,10通徑 13 液壓缸 - - - 14 壓力繼電器
29、 - PF-L8C 14MPa,8通徑 表4.2.1 選用元件型號和規(guī)格 (2)確定油管 各元件管道的規(guī)格按元件接口處的尺寸確定,液壓缸進、出油管按輸入、輸出的最大流量計算。由于液壓泵具體選定后液壓缸在各個階段的進、出流量已經與原定數值不同,所以要重新計算得到表4.2.2所示的數據。 項目 快進 工進 快退 輸入流量 /L?min-1 47.27 0.48 25 輸出流量 /L?min-1 22.27 0.23 53.07 運動速度 /m?min-1 4.98 0.051 5.58 表4.2.2 液壓缸的進、出流量 當液壓油的速度取
30、3m/min時,可得到液壓缸有桿腔和無桿腔相連的油管內分別為: d=247.27*106π*3*103*60=17.3mm d=225*106π*3*103*60=13.3mm 為統(tǒng)一規(guī)格,按產品樣本選取油管內徑15mm,外徑20mm的10號冷拔鋼管。 (3)油箱 油箱的容積V按V=aqv計算。當經驗系數取6的時候,油箱的容積V=150L,按GB 2876-1981規(guī)定,取標準值250L。 5. 液壓系統(tǒng)的性能驗算 5.1回路壓力損失驗算 1選定管道內徑15mm,進、回油管道的長
31、度估計為2m,取液壓油粘度v=1*10-4mm/s,油密度ρ=900kg/m3。取最大速度(流量)估算: Re=vdv=4qπdv=4*47.27*10-33.14*60*15*10-3*1*10-4=668.83<2300 所以,各工況流動都為層流。 層流沿程阻力系數λ=75Re=75πdv/4q,管道油液流速v=4qπd2。則沿程阻力損失為: ?pλ=λld*ρv22=4*75*900*1*10-4*22π20*10-34q≈5.4*107q 局部壓力損失: ?pξ=0.1?pλ 由上式計算各工況進、回油路壓力損失,如表5.1.1。 油路 各工況下的壓力損失/MPa 快
32、進 工進 快退 進油 ?pλ 0.0425 0.0004 0.0225 ?pξ 0.0043 0 0.0023 ?pw 0.0468 0.0004 0.0248 回油 ?pλ 0.0205 0.0002 0.0478 ?pξ 0.0020 0 0.0048 ?pw 0.0225 0.0002 0.526 表5.1.1 各工況下的壓力損失 由上表計算可是,各個工況的總壓力損失?pw,將其與各工況工作壓力比較,均小于工作壓力,故系統(tǒng)可正常工作。 5.2發(fā)熱溫升驗算 工進在整個工作循環(huán)中所占用的時間達96%,所以系統(tǒng)發(fā)熱和液壓油溫升主要
33、是計算工進時的。 工進液壓缸的有效功率為: P0=p2q2=Fv=30300*0.0560*103=0.0253Kw 這時大流量泵通過液控順序閥卸荷,小流量泵在高壓下供油,所以兩個泵的總輸出功率為: Pi=pp1qp1+pp2qp2η=0.84Kw 則液壓系統(tǒng)的發(fā)熱量為: Hi=Pi-P0=0.81 求此時液壓油溫升的近似值 ?T=Hi3V2*103≈20℃ 查閱《液壓與氣壓傳動》資料可知:一般機床為25~30℃,工程機械為35~40℃。 溫度額沒有超出允許范圍,系統(tǒng)不需要設置冷凝器。
34、 6. 參考資料 [1]劉忠偉.液壓傳動與氣動.北京:化學工業(yè)出版社,2014. [2]張利平.液壓控制系統(tǒng)及設計.北京:化學工業(yè)出版社,2006. [3]丁樹模.液壓傳動.第二版.北京:機械工業(yè)出版社,1999. 7. 設計總結 通過本次的液壓傳動的課程設計,讓我對液壓傳動有了更為深刻的理解,同時也掌握了更多關于液壓傳動中的一些知識。 針對機械設備中的一種動力傳動裝置設計,剛拿到手的時候的確不知道該如何下手,但是通過對《液壓與氣壓
35、傳動》相關內容的閱讀,自己慢慢有了思緒,對照著書上模板的樣子,結合自己的課題,然后運動自己所學到的一些知識開始設計。當然,在設計過程中肯定有我們暫時無法解決的問題,這就需要我們自己查閱相關資料來解決問題,當然小組成員通過交流也可以解決一部分的問題。 對我來說,收獲最大的是方法和能力.那些分析和解決問題的方法與能力.在整個過程中,我發(fā)現像我們這些學生最最缺少的是經驗,沒有感性的認識,空有理論知識,有些東西很可能與實際脫節(jié).總體來說,我覺得做這種類型的作業(yè)對我們的幫助還是很大的,它需要我們將學過的相關知識都系統(tǒng)地聯系起來,從中暴露出自身的不足,以待改進.有時候,一個人的力量是有限的,合眾人智慧,我相信我們的作品會更完美! - 16 -
- 溫馨提示:
1: 本站所有資源如無特殊說明,都需要本地電腦安裝OFFICE2007和PDF閱讀器。圖紙軟件為CAD,CAXA,PROE,UG,SolidWorks等.壓縮文件請下載最新的WinRAR軟件解壓。
2: 本站的文檔不包含任何第三方提供的附件圖紙等,如果需要附件,請聯系上傳者。文件的所有權益歸上傳用戶所有。
3.本站RAR壓縮包中若帶圖紙,網頁內容里面會有圖紙預覽,若沒有圖紙預覽就沒有圖紙。
4. 未經權益所有人同意不得將文件中的內容挪作商業(yè)或盈利用途。
5. 裝配圖網僅提供信息存儲空間,僅對用戶上傳內容的表現方式做保護處理,對用戶上傳分享的文檔內容本身不做任何修改或編輯,并不能對任何下載內容負責。
6. 下載文件中如有侵權或不適當內容,請與我們聯系,我們立即糾正。
7. 本站不保證下載資源的準確性、安全性和完整性, 同時也不承擔用戶因使用這些下載資源對自己和他人造成任何形式的傷害或損失。
最新文檔
- 2025年防凍教育安全教育班會全文PPT
- 2025年寒假安全教育班會全文PPT
- 初中2025年冬季防溺水安全教育全文PPT
- 初中臘八節(jié)2024年專題PPT
- 主播直播培訓提升人氣的方法正確的直播方式如何留住游客
- XX地區(qū)機關工委2024年度年終黨建工作總結述職匯報
- 心肺復蘇培訓(心臟驟停的臨床表現與診斷)
- 我的大學生活介紹
- XX單位2024年終專題組織生活會理論學習理論學習強黨性凝心聚力建新功
- 2024年XX單位個人述職述廉報告
- 一文解讀2025中央經濟工作會議精神(使社會信心有效提振經濟明顯回升)
- 2025職業(yè)生涯規(guī)劃報告自我評估職業(yè)探索目標設定發(fā)展策略
- 2024年度XX縣縣委書記個人述職報告及2025年工作計劃
- 寒假計劃中學生寒假計劃安排表(規(guī)劃好寒假的每個階段)
- 中央經濟工作會議九大看點學思想強黨性重實踐建新功