IE基礎知識培訓教材(PPT 130頁)
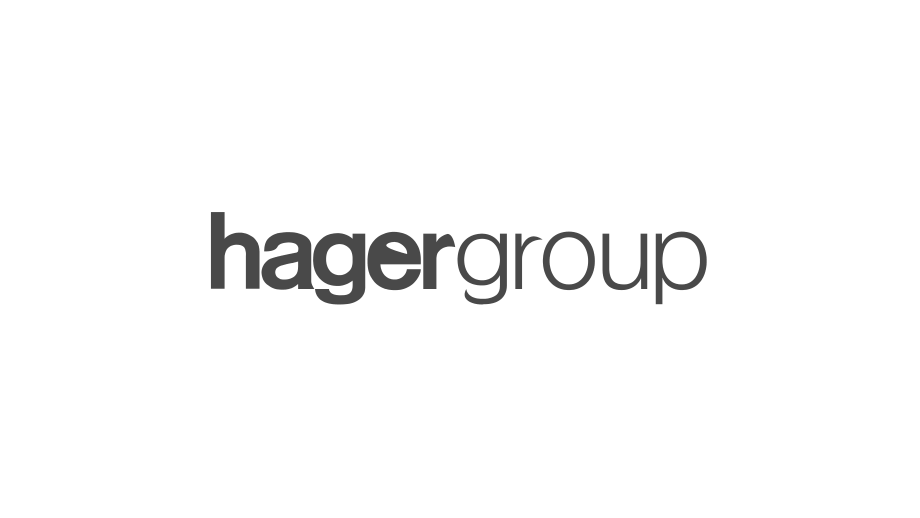


《IE基礎知識培訓教材(PPT 130頁)》由會員分享,可在線閱讀,更多相關《IE基礎知識培訓教材(PPT 130頁)(130頁珍藏版)》請在裝配圖網(wǎng)上搜索。
1、IE基礎知識Date: 2018.5.24Author: Robin Li精益講堂精益講堂課程形式計劃時間IE基礎知識內(nèi)訓5月、6月各一批TPM內(nèi)訓6月柔性化生產(chǎn)內(nèi)訓7月SMED內(nèi)訓8月低成本智能自動化(LCIA)外訓+內(nèi)部推廣5月目的:公司q 培訓并發(fā)展一批擁有精益技能的人才。q 據(jù)此推動公司的精益意識及文化建設。q 進而增加客戶滿意度,提升公司的綜合競爭力。個人q 豐富技能q 增強能力q 提升自身價值組名:組長:口號:造型:5分鐘 備戰(zhàn) (WA、MSG、EL、LP、MPD2)Agenda01 七大浪費02 改善的突破點03 VSM04 運轉分析05 工序分析06 LOB分析07 動作分析0
2、8 搬運分析重點學習及訓練精益七大浪費801 Back to agenda (optional)精益生產(chǎn)的核心消除一切 浪費 ! 發(fā)現(xiàn)并消除浪費是精益的基礎與核心思想,也是精益改善活動的出發(fā)點。改善的突破點1102 Back to agenda (optional)微利時代-賺一塊錢看別人的臉色 ,省一塊錢看自己的角色。 -富士康科技集團 郭臺銘 精益的研究對象是?l 當前狀況銷售增加50%成本降低50%銷售10000成本8000利潤2000利潤增加-?15000100001200040003000600050%300%看到什么?如何找到突破點 ?沒有問題就是最大的問題各小組案例演示項目改善點
3、有哪些?改善點如何識別出來的?項目各改善點的改善原理?過剩生產(chǎn)的浪費等待的浪費搬運的浪費加工本身的浪費不良品浪費動作的浪費庫存的浪費VSM運轉分析工序分析LOB分析動作分析搬運分析動作經(jīng)濟原則ECRS左邊和右邊有什么聯(lián)系?七七大浪費大浪費20%的人手里掌握著80%的財富20%的人身上集中了人類80%的智慧給一個公司帶來80%利潤的是20%的客戶改善活動中使用P/Q分析的目的:決定改善對象,從效果大的產(chǎn)品開始進行產(chǎn)品ABCD月生產(chǎn)數(shù)量(PCS)所用工時(H)售價(RMB)毛利潤(%)101180821891.20.50.731.210%10%10%10%524087600150134523300
4、3 Back to agenda (optional)這是一個關于收到訂單交貨所間隔時間的故事 VSM-用于識別整個過程中的浪費縮短間隔時間(Lead- time)VSM 現(xiàn)狀圖VSM 未來圖運轉分析3404 Back to agenda (optional)區(qū)分區(qū)分內(nèi)容內(nèi)容示例示例作業(yè)作業(yè)主作業(yè)直接參與材料和部品的變形或變質(zhì),達到創(chuàng)造附加價值的目的的作業(yè)v 切削加工,螺絲加工v 部品的組裝(螺母的擰緊)v 機械的手動操作附屬作業(yè)作為主體作業(yè)的附屬,伴隨主體作業(yè)的每周期, 但間接作用于工作目的的要素v 材料的分離v 加工物品的尺寸測試 v 加工物品的定位準備作業(yè)為主作業(yè)而做的準備,結束,搬運等
5、的作業(yè)在每批或幾周期內(nèi)定期發(fā)生的要素v 作業(yè)前材料的準備v 加工物品的搬到加工物品的存放區(qū)域v 準備(每批次)1.運轉分析概要區(qū)分區(qū)分內(nèi)容內(nèi)容示例示例非作業(yè)非作業(yè)作業(yè)余量作業(yè)中不規(guī)則的偶然發(fā)生的因素.主要原因在于機械,工具,材料等加工途中把折的工具換下來修理材料的細微的缺陷 不 定期材料的補充管理余量與作業(yè)無關的,以管理為目的發(fā)生的延遲會議及早會作業(yè)途中的作業(yè)指示5分清掃等規(guī)定的清掃個人余量為滿足人的生理的需求因素上衛(wèi)生間喝水擦汗疲勞余量為恢復由作業(yè)環(huán)境引起的疲勞產(chǎn)生的延遲因素室內(nèi)溫度高潮濕的環(huán)境中作業(yè)灰多的環(huán)境中作業(yè)重量物的移動無作業(yè)有管理者責任的非作業(yè)和作業(yè)者責任的非作業(yè) 停電,機械故障,
6、物料無庫存 閑談,未遵守開始和結束時間 作業(yè)等待1.運轉分析概要1) 運轉分析?通過一天或長時間觀測某一項工作, 分析生產(chǎn)內(nèi)容與非生產(chǎn)內(nèi)容,為改善更好的生產(chǎn)體系或為制定標準時間,設定適當?shù)挠嗔繛橹饕康牡姆椒?2) 運轉分析的目的(1) 消除或減少作業(yè)者在機械或工程中的等待等非生產(chǎn)性要素,使生產(chǎn)能夠按計劃進行.(2) 分析各時間,日期的生產(chǎn)量或工作的變化,使進一步提高生產(chǎn)效率,資源的有效利用率(3) 改進準備作業(yè),末尾作業(yè)(4) 決定適當?shù)娜?設備,方法(5) 設定標準時間時決定適當?shù)母綄僮鳂I(yè)時間或余量(6) 檢驗標準時間的適合性或作業(yè)標準1.運轉分析概要3) 運轉分析系統(tǒng)設備運轉日報4) 運
7、轉分析的方法運轉分析 Work Sampling (作業(yè)取樣分析)觀測分析資料分析作業(yè)日報連續(xù)觀測分析用STOP WATCH或攝像機連續(xù)觀測運轉狀態(tài)選擇小部分的作業(yè)者或機械,詳細掌握發(fā)生的工作種類可以詳細分析觀測者付出的努力多一些 不能同時觀測很多對象用眼睛瞬間的多次觀測對象一次可觀測多數(shù)對象 觀測者可并行做其 它業(yè)務只觀測表面現(xiàn)象,不能詳細分析種類Work sampling連續(xù)觀測選擇多數(shù)的作業(yè)者或機械,概括地掌握發(fā)生的工作種類觀測方法目 的優(yōu) 點缺 點1.運轉分析概要1)1)Work samplingWork samplingWork sampling是指瞬間觀測人或機械的運行狀態(tài)及種類,
8、對其結果進行收集整理,運用統(tǒng)計的抽樣理論對觀測對象的時間構成比率及運轉率進行調(diào)查和分析的技巧以制造現(xiàn)場為對象的Work sampling分析(例) 料件插入焊接檢查檢查用車搬運材料作業(yè)的事前協(xié)議移動余量材料的分離 / / / / / 25 8.9 / / / 28 10.0 / / / / 28 10.0 / / / / / / / 104 37.1 / / / / / 25 8.9 / / / 11 3.9 / / / 17 6.1 / / 12 4.3 / / / / 30 10.8 10 10 10 10 10 10 10 280 100計計08:05 08:17 08:39 08:42
9、 09:02 16:17 16:24 計計 %單位作業(yè)單位作業(yè)2.Work Sampling2) Work sampling2) Work sampling的原理的原理( (實際狀態(tài)實際狀態(tài)) )(Work sampling)(Work sampling) Work sampling的運轉率= 29/50*100 = 58% 連續(xù)運轉測定= 36.5/(12*5)*100 = 60.8% 誤差 = 60.8% - 58% = 2.8%3) W/S3) W/S的用途的用途(1) 掌握設備或人的運轉內(nèi)容 掌握余量 改進作業(yè)分工提高運轉率作業(yè)者 A B C D E12345678910計運轉4333
10、12433329非運轉122243122221 NO 糾正作業(yè)者或事務員工作中的均衡度 研討能否增加設備、增員 掌握流程作業(yè)中的平衡度2.Work Sampling (3) 作為決定延遲余量的基礎資料. 因為對發(fā)生不規(guī)則、多種類、內(nèi)容豐富的延遲要素來說,想求出各時間是不可能的,所以 對全體用表示。 4) Work sampling (W/S)有效作業(yè)的特性重復性少的作業(yè)的現(xiàn)狀分析 作業(yè)范圍廣,運轉頻率高的作業(yè)的現(xiàn)狀分析 Work sampling 的基礎在于概率的. 如果抽樣數(shù)多抽樣特性的曲線與全集的分布曲線幾乎是一致的, 增加抽樣數(shù)時相應的調(diào)查費用也將會增加.因此從經(jīng)濟性與可信性考慮需要規(guī)定
11、抽樣數(shù)(觀測點數(shù)) 抽樣時要求公正,對組成某集團的要素,抽樣的機會應均等(2) 作為設定標準時間的基礎資料. 對個別的不規(guī)則性大的作業(yè)特別有效2.Work SamplingN =一般情況下求觀測點數(shù)N時無特別的理由時取可信度為95%.因此上式為一般取觀測點數(shù)N值的基準Work sampling 的目的N1. 一般目的(確認問題時)2. 特定的管理目的(分析等待的原因時)3. 特定的活動分析(求出準備或延遲的比率)4. 人或機械的運轉率5. 求標準時間,余率,運轉率等時要求高精密度時100600S P2Z (1-P)2N =S P24 (1-P)2000400010,000以上 E : 絕對誤差
12、 S : 希望的精密度(相對誤差) P : 選擇對象的出現(xiàn)幾率(求出的比率) N : 抽樣的大小(觀測點數(shù)) Z : 對應可信度的標準化系數(shù) Work sampling的觀測點數(shù) 2.Work Sampling為調(diào)查設備運轉率,利用 Work sampling 技術預備調(diào)查(sampling數(shù)為100次)的結果設備運轉率為 75%(非運轉率: 25%), 可信度95%期望的精密度為10%為達到所期望的條件,需要觀測多少次?練習題練習題1 1N =4 (1-P)S P2=2.Work Sampling6) 觀測時間的決定方法 隨機抽樣法 (1)1日的觀測點數(shù) 每天的觀測點數(shù)受到必要觀測點數(shù)與調(diào)查
13、時間的影響.例如 余率的調(diào)查是20天內(nèi)完成 3,600個樣品時一天需要 3,600 OVER 20日 = 180個/日 (2)選擇觀測時間 sampling采用隨機表,使全部的時間都有機會成為觀測時間. a. 為提高隨機性,巡回的出發(fā)點,路徑也用隨機表隨機地抽取. b. 巡回觀測時,觀測時間有部分相同時實際上不妨礙結果.2.Work Sampling 使用最簡單隨機表的例簡單的隨機表上表中從任意數(shù)字開始,依次選擇縱或橫的數(shù)字3 個為一組,換算觀測時間例如950 9 : 30 (0.50 60 = 30)622 6 : 13 (0.22 60 = 13.2)220 2 : 12 (0.20 60
14、 = 12)950622 220985 742942 783807 907093989408 037183 133869 326689 485451194660 687432 674192 695066 899093785915 610163 310163 171067 096126978142 269577 907093 742942 783807326355 358421 172294 978308 497013763328 349067 262095 742942 71138052.Work Sampling問題的定義及調(diào)查目的得到現(xiàn)場責任者的承認及向作業(yè)者說明意圖決定期待的精密度預備觀
15、測/制定觀測計劃實施正式觀測結果整理/檢驗精密度結果整理(圖表) 作業(yè)內(nèi)容理解 作業(yè)內(nèi)容分工 定義要素作業(yè) 預測發(fā)生頻率 計算觀測點數(shù) 計算1日巡回次數(shù) 決定觀測時間 設定巡回路徑 準備觀測用紙7) work sampling順序2.Work Sampling針對主作業(yè),適當?shù)卣{(diào)整作業(yè)的分工及分配.消除擾亂作業(yè)者狀態(tài)的非正規(guī)作業(yè)或不必要的作業(yè).根據(jù)每小時生產(chǎn)量的時間變化曲線,調(diào)查狀態(tài)與疲勞的關系,研討中間插入休息時間方法 消除不是由此作業(yè)者做的作業(yè),如拿工具,工具修理,材料產(chǎn)品的搬運等分工. 研究布局消除作業(yè)者的不必要的走動.制定因作業(yè)單調(diào)引起的生產(chǎn)降低預防對策.準備作業(yè)的標準化、分工化2.改
16、進的著眼點減少作業(yè)余量的對策(消除失敗作業(yè),工具、材料等其它的突發(fā)偶發(fā)現(xiàn)象)排除降低現(xiàn)場士氣的原因排除機械設備的停工原因加強現(xiàn)場巡察和管理等待中進行有效的作業(yè) 研討自動測試,自動調(diào)節(jié),自動化的必要性發(fā)生突發(fā)事故時 明確應急措施,連絡,指示順序工序分析5005 Back to agenda (optional)1). 工序分析的定義原材料按照一定的順序進行各種加工、搬運、檢查、等待等作業(yè),最終形成產(chǎn)品上市,這種產(chǎn)品生產(chǎn)過程被稱之為“工序”,對這一系列工序進行調(diào)查、分析和改善的手法,被稱之為“工序分析”工序分析是工序管理、搬運管理、布局研究、LOB等基礎資料獲取的必要手法2). 工序分析的目的(1
17、)整理工序流程(2)工序流程中是否存在“3不” 不一致 不均衡 不合理的現(xiàn)象(3)工序順序是否合理(4)工序流程是否流暢,設備配置、搬運方法是否合理(5)工序中的作業(yè)是否必要,是否可以取消,是否可以找到更好的作業(yè)方法1.工序分析概要工序分析概要3). 工序分析的種類工序分析法產(chǎn)品工序分析法作業(yè)人員工序分析法聯(lián)合工序分析法事務工序分析法人機聯(lián)合分析法人人聯(lián)合分析法以產(chǎn)品為分析主體當作業(yè)是通過多個工序進行連續(xù)加工時適用以作業(yè)人員為分析主體當特定的作業(yè)人員在移動的同時連續(xù)作業(yè)時使用以作業(yè)人員和機器為分析主體當查找“待工”或“玩”時適用以數(shù)名作業(yè)人員為分析主體相互間查找“待工”時適用以事務工作流程為分
18、析主體4). 工序圖記號(基本圖記號&補助圖記號)序號主要工序記號名稱記號意思1加工加工使原材料、零部件或產(chǎn)品的形狀、性質(zhì)發(fā)生改變的過程2搬運搬運使原材料、零部件或產(chǎn)品的位置進行改變的過程3停滯貯藏將原材料、零部件或產(chǎn)品按計劃貯藏的過程4滯留原材料、零部件或產(chǎn)品未能按計劃進行而處在滯留狀態(tài)5檢查數(shù)量檢查對原材料、零部件或產(chǎn)品的數(shù)量進行檢查6質(zhì)量檢查檢驗原材料、零部件或產(chǎn)品的品質(zhì)特性JIS(日本工業(yè)規(guī)格)中的Z8206 規(guī)定,工業(yè)管理、質(zhì)量管理都有使用- 基本圖記號(為了表示主要工序記號)- 基本記號組合圖號(為了表示一個工序同時執(zhí)行兩個不同的職能)序號記號意思1以質(zhì)量檢查為主,同時也進行數(shù)量檢
19、查2以數(shù)量檢查為主,同時也進行質(zhì)量檢查3以加工為主,同時也進行數(shù)量檢查4以加工為主,同時也進行質(zhì)量檢查5以加工為主,同事也進行搬運4). 工序圖記號(基本圖記號&補助圖記號)2.產(chǎn)品工序分析法1). 產(chǎn)品工序分析法的定義產(chǎn)品工序分析法是以原材料、零部件或產(chǎn)品為對象,分析工序是如何進行的,是將著眼點放到物流上來進行分析調(diào)查的一種方法。2). 產(chǎn)品工序分析法的意義和目的產(chǎn)品工序分析的目標放在物流上,以設計或改善作業(yè)順序為目的,確保生產(chǎn)出高品質(zhì)、高效率、低成本的產(chǎn)品。是否有不必要的停滯搬運次數(shù)是否太多搬運距離是否太長搬運方法是否存在問題加工和檢查是否可以同時進行設備配置是否合理作業(yè)順序是否正確作業(yè)分
20、配是否均勻4). 產(chǎn)品工序分析法的步驟預備調(diào)查繪制工序流程圖測定并記錄各工序中的必要項目整理分析結果制定改善方案改善方案的實施和評價改善方案標準化2.2.產(chǎn)品工序分析法產(chǎn)品工序分析法5). 5). 案例案例 (別針的制作工藝)(別針的制作工藝)標題標題別針的制作(改善前)別針的制作(改善前)日期日期年年 月月 日日No作業(yè)名稱流程機器距離時間人員工序符號M分人1別針的定尺切割、倒角切割機6012搬運吊車20523測定長短、檢查倒角游標卡尺1024暫時放置袋7025搬運吊車10326外徑研磨研磨機1517搬運吊車20528外徑測定游標卡尺529搬運吊車205210嵌入手術刀模具檢查10211搬運
21、吊車154212暫時放置60113保管倉庫2次5次3次3次合計13個工序852522175分22分25分130分(1)產(chǎn)品工序表(2)現(xiàn)場平面流程圖(3)改善前整理表工序工序工序數(shù)工序數(shù)時間(分)時間(分)距離(距離(M)人員(人)人員(人)加工275-2搬運5228510檢查325-6停滯3130-3合計132528521價值價值浪費浪費(5)改善后產(chǎn)品工序表標題標題別針的制作(改善前)別針的制作(改善前)日期日期年年 月月 日日No作業(yè)名稱流程機器距離時間人員工序符號M分人1別針的定尺切割、倒角切割機6012搬運吊車20523測定長短、檢查倒角游標卡尺1024搬運吊車10325外徑研磨研磨
22、機1516搬運吊車20527外徑測定、嵌入手術刀模具檢查游標卡尺1528搬運吊車15429保管倉庫2次4次2次1次合計9個工序651171475分22分25分130分(6)改善后平面流程圖(7)改善后整理表工序工序工序數(shù)工序數(shù)時間(分)時間(分)距離(距離(M)人員(人)人員(人)加工275-2搬運417658檢查225-4停滯1-合計91176514(8)改善前后的比較工序工序工序數(shù)工序數(shù)時間(分)時間(分)距離(距離(M)人員(人)人員(人)前后效果前后效果前后效果前后效果加工22075750-220搬運541221758565201082檢查32125250-642停滯312130013
23、0-3-3合計139425211713585652021147LOB分析分析(產(chǎn)線平衡率分析)(產(chǎn)線平衡率分析)6306 Back to agenda (optional)工序標準作業(yè)時間(秒)標準人員節(jié)拍時間(秒)151526.516.53616441453.513.5LOB=UPPH( 單位人時產(chǎn)能 )=77%110.8 pcs工序標準作業(yè)時間(秒)標準人員節(jié)拍時間(秒)181825.515.534.514.54153556166243875.515.5861691226105.515.511515125.515.5工序標準作業(yè)時間(秒)標準人員節(jié)拍時間(秒)182425.515.534.
24、514.54153556166244675.515.5861691226105.515.511515125.515.5LOB=UPPH( 單位人時產(chǎn)能 )=LOB=UPPH( 單位人時產(chǎn)能 )=75.4%26.5 pcs89.9%31.6 pcs工序標準作業(yè)時間(秒)標準人員節(jié)拍時間(秒)1616261636164616561666167616880891226106161161612616LOB=UPPH( 單位人時產(chǎn)能 )=76.9%37.5 pcs瓶頸工位:6+6+6+6+6+6+6+8+12+6+6+68*13X 100% =76.9%各工序標準作業(yè)時間之和 節(jié)拍瓶頸時間 x 人及主設
25、備數(shù)之和產(chǎn)線平衡率改善思路:瓶頸改善合并改善打破平衡分擔轉移、改善夾具工具、操作機械化、提高設備能力、增加作業(yè)人員、提高作業(yè)技能、調(diào)換作業(yè)者對工時短的作業(yè)進行合并,使其合并后工序作業(yè)時間接近瓶頸工時,減少資源消耗對整條生產(chǎn)線的資源(比如人員)進行重新編排、分配、形成新的分配方式和順序簡易自動化(LCA)對困難、累、不便、危險的作業(yè)推進 LCA(Low Cost Auto-mation) 使其脫離作業(yè)者。 LCA盡量要小、簡單、易于裝卸 313421244423373425354521024681012141618工位1工位2工位3工位4工位5動作1動作2動作3動作4動作5動作6時間動作分析動作
26、分析7307 Back to agenda (optional)1.動作分析慎密分析工作中的各細微身體動作(作業(yè)者的身體移動/腳的移動,手的移動等)刪除其無效動作,促進其有效之動作,使作業(yè)者疲勞度最小化, 提高作業(yè)效率的經(jīng)濟性及作業(yè)距離的最小化 定義 動作分析目的(1)如實把握作業(yè)人員身體各部位進行動作的順序、方法;(2)發(fā)現(xiàn)人員在動作方面的無效或浪費(3)簡化操作方法,減少工作疲勞,進而制定標準操作方法及標準動作時間2.動作要素2.2.動作要素動作要素2.1 動作要素的檢核表動作要素改善著眼點伸手及移物1.這些動作可否刪除? 2.距離是否最適當? 3.有否應用適當?shù)拿浇?如手,鑷子及輸送器等
27、。 4.是否應用了正確的身體部位,如手指,前臂和上臂。 5.能否使用滑道或輸送器? 6.輸送單位增大是否較有效率 ? 7.能否用腳操作的裝置來輸送? 8.輸送是否因接下來有較難做的對準而緩慢下來? 9.工具的使用是否處于附近? 10.較常使用的零件是否置于使用點附近? 11.有否使用適當?shù)耐斜P或箱子?操作是否經(jīng)過正常地排列? 12.前一動作和后一動作是否與此地動作互相關聯(lián)? 13.能否避免突然的轉變方向?能否去除障礙物?14.對于物的移動是否使用身體最耐久的部位? 15.有無可刪除的身體移動? 16.手臂之移動能否同時,對稱而依相反方向行之? 17.能否以滑動代替拾取? 18.眼球的移棟是否與
28、手的動作配合?握取1.是否可以一次握住一件以上之物件?2.能否以觸取代替拾取? 3.儲物箱的前緣能否減化握取的動作要素? 4.工具或零件能否預對,以便握取容易? 5.能否使用特殊的螺絲起子或其他工具? 6.能否使用真空,磁鐵,橡皮指尖等工具 ? 7.物體是否由一只手移至另一只手? 8.工具和夾具的設計是否使用零件移動的握取較為容易? 動作要素改善著眼點對準1.對準是否必要? 2.容差能否增大? 3.方形邊能否避免? 4.能否使用導軌,漏斗,托架,定位木箱,彈簧?5.能否使用手臂扶架來穩(wěn)定手,以減少對準的時間?6.握取的物件是否易于對準? 7.能否應用腳操作的簡單夾具?裝配、拆裝、應用1.能否使
29、用工具或夾具? 2.能否使用自動儀器或機器? 3.裝配能否交互進行?制造程序能否交互進行? 4.是否能夠使用更有效率的工具? 5.當機器在切削時,其他工作能否進行? 6.能否使用動力工具? 7.能否使用凸輪或空氣操作的工具?放手1.能否刪除此動作? 2.能否使物體自由墜落? 3.能否于運動中放手? 4.是否需要小心地放開物件?能否避免如此? 5.能否使用排出器? 6.材料盒是否經(jīng)過適當?shù)脑O計? 7.在放手的末端,手或輸送工具是否在最有利的位置,以便此動作的進行? 8.能否使用輸送器?2.1 動作要素的檢核表動作要素改善著眼點選擇1.是否布置得當以減少尋找物體的浪費? 2.工具和材料是否能標準化
30、? 3.零件和材料是否給于適當?shù)臉擞? 4.排列是否良好,以便易于選擇?例如用托盤預置零件,使用透明容器等。5.一般零件的排列是否有互損性? 6.零件和材料是否混在一起? 7.亮度是否良好? 8.在前一操作里,是否可以同時把零件預對好? 9.能否利用顏色來使零件易于選擇?檢驗1.能否刪除。 2.能否使用多重量規(guī)或試驗器? 3.能否增加照明強度,或重新安排光源,以減少檢驗時間? 4.目視檢驗能否代替機器檢驗? 5.操作者使用眼鏡是否有益? 預對1.物體能否于運送中預對? 2.能否使工具平衡,使其把柄處于直立位置? 3.持住的裝置是否使工具把柄處于適當位置? 4.工具能否懸掛起來? 5.工具能否存
31、放于工作之適當位置? 6.能否使用導軌?7.物體的設計能否使其各邊相同? 8.能否使用加料管道? 持住1.能否使用夾鉗,架子,夾具或其他機械裝置? 2.能否應用粘性摩擦? 3.如持住不能避免,能否提供手臂扶架?2.1 動作要素的檢核表基本原則詳細內(nèi)容基本原則詳細內(nèi)容1.減少動作1.消除不必要的動作.2.減少視線的移動.3.組合2個以上的動作.4.兩個以上的工具組合成一個.5.材料或工具放在作業(yè)者前.6.材料或工具保持容易使用狀態(tài).7.材料或部品利用容易取用的容器或器械.8.材料或工具按作業(yè)順序放置.9.利用動作數(shù)少的簡單的器械.10.機器操作采用操作簡單的機器.3.減少動作距離1.動作由身體最
32、佳部位去完成.2.采用最短距離的動作.3.作業(yè)范圍盡量小一些.4.材料的取用時利用重力或機械力.2.同時動作1.兩手同時開始同時結束.2.兩手的動作方向采用反對稱方向.3.采用兩手同時動作的配置.4.采用兩手同時動作的夾具.5.簡單的作業(yè)或加力的動作時利用腳的器械4.動作要舒適1.動作盡量采用舒適的動作.2.動作采用重力或其它力.3.多利用慣性或彈性力量.4.動作的方向或其變換要靈活.5.作業(yè)的高度應適當. 6.用夾具或GUIDE控制一定的移動路徑.7.手柄部位保持容易拿取的狀態(tài).8.從能見的位置轉變?yōu)榉奖闶褂玫奈恢?9.機器的移動方向與操作方向相一致.10.工具要輕便容易取用.3.動作經(jīng)濟的
33、四條基本原則取消(Eliminate)首先考慮該項工作有無取消的可能性。如果所研究的工作、工序、操作可以取消而又不影響半成品的質(zhì)量和組裝進度,這便是最有效果的改善。例如,不必要的工序、搬運、檢驗等,都應予以取消,特別要注意那些工作量大的裝配作業(yè);如果不能全部取消,可考慮部分地取消。例如,由本廠自行制造變?yōu)橥赓?,這實際上也是一種取消和改善。合并(Combine)合并就是將兩個或兩個以上的對象變成一個。如工序或工作的合并、工具的合并等。合并后可以有效地消除重復現(xiàn)象,能取得較大的效果。當工序之間的生產(chǎn)能力不平衡,出現(xiàn)人浮于事和忙閑不均時,就需要對這些工序進行調(diào)整和合并。有些相同的工作完全可以分散在不
34、同的部門去進行,也可以考慮能否都合并在一道工序內(nèi)。重排(Rearrange)重組也稱為替換。就是通過改變工作程序,使工作的先后順序重新組合,以達到改善工作的目的。例如,前后工序的對換、手的動作改換為腳的動作、生產(chǎn)現(xiàn)場機器設備位置的調(diào)整等。簡化(Simplify)經(jīng)過取消、合并、重組之后,再對該項工作作進一步更深入的分析研究,使現(xiàn)行方法盡量地簡化,以最大限度地縮短作業(yè)時間,提高工作效率。簡化就是一種工序的改善,也是局部范圍的省略,整個范圍的省略也就是取消。4.改善四原則E(取消)(1)剔除所有可能的作業(yè),步驟或動作(包括身體,足,手臂或眼)。 (2)剔除工作中的不規(guī)律性,使動作成為自發(fā)性,並使各
35、種物品置放於固定地點。(3)剔除以手作為持物工具的工作。(4)剔除不方便或不正常的動作。(5)剔除必須使用肌力才維持的姿勢。(6)剔除必須使用肌力的工作,而以動力工具取代之。(7)剔除必須克服動量的工作。 (8)剔除危險的工作。(9)剔除所有不必要的閒置時間。C(合并)(1)把必須突然改變方向的各個小動作結合成一個連續(xù)的曲線動作。(2)合並各種工具,使成為多用途。(3)合並可能的作業(yè)。(4)合並可能同時進行的動作。R(重排)(1)使工作平均分配於兩手,兩手之同時動作最好呈對稱性。(2)組作業(yè)時,應把工作平均分配於各成員。(3)把工作安排成清晰的直線順序。S(簡化)(1)使用最低級次的肌內(nèi)工作。
36、(2)減少視覺動作並降低必須注視的次數(shù)。(3)保持在正常動作範圍內(nèi)工作。(4)縮短動作距離。(5)使手柄,操作桿,足踏板,按鈕均在手足可及之處。(6)在須要運用肌力時,應盡量利用工具或工作物的動量。(7)使用最簡單的動素組合來完成工作, (8)減少每一動作的復雜性。實例1 通過固定電烙鐵減少動作數(shù)實例2 利用反射鏡減少眼的移動角度實例3 用透明有機玻璃觀看窗口減少眼的活動實例4 合并兩個印章減少蓋印次數(shù)實例5 用雙管注射器減少涂覆樹脂動作實例6 指定工具、物料的放置位置實例7:改變工具材質(zhì)減輕重量實例8 通過改變作業(yè)現(xiàn)場的布置取消“變換工件方向”的動作實例9 按便于作業(yè)的順序布置工具實例10:
37、用波紋板簡化抓取動作實例11:合并萬用表的測頭實例12:通過布置左右對稱的作業(yè)現(xiàn)場使雙手能同時作業(yè)實例13:通過夾具實現(xiàn)雙手同時操作帶尾墊圈的彎曲作業(yè)實例14:通過把物料箱布置成圓弧形縮短動作距離實例15:用橋式操作臺縮短動作范圍實例16:利用傾斜貨架縮短動作距離實例17:通過改變作業(yè)順序減少涂漆作業(yè)的注意力實例18:取消對粘貼透明膠帶動作的限制實例19:利用慣性力分離工件與切屑實例20:利用高度調(diào)整機構固定作業(yè)高度實例21:利用導柱簡化重疊鋼板作業(yè)視頻分析-分組討論改善點視頻1視頻2搬運搬運分析分析10508 Back to agenda (optional)(1 1)搬運分析與搬運改善)搬
38、運分析與搬運改善1、搬運改善的目標:搬運改善的目標:搬運損耗時間和成本,降低效率,卻不增加任何附加價值制造費用的25%40%用于搬運工程所需時間的40%屬于搬運和滯留時間安全事故的80%是在搬運過程中發(fā)生的搬運使不良品增加了20%目標:增加有效的生產(chǎn)加工時間,提高效率縮減生產(chǎn)過程時間,交期縮短減少停滯,倉儲空間減少搬運費用降低搬運減少,安全事故也減少搬運造成的品質(zhì)不良得到控制減輕作業(yè)者搬運負擔,能改善士氣2 2、搬運改善的著眼點、搬運改善的著眼點整理整頓規(guī)劃通道,去除多余物品物品擺放定量定位,改善搬運秩序,獲得安全作業(yè)環(huán)境操作改善減少抓、提、調(diào)整、捆、定位等動作是改善搬運的重要著眼點。應用動作
39、分析加以改善擺放的方法搬運活性:使后續(xù)搬運更容易消除空洞搬運在中空的部分裝入其他的物品,以提高搬運效率搬運的舒適化和安全化搬運通道上不應有障礙物消除搬運通道的凹凸不平盡量不要有斜坡,即使有也應該使坡度更為平緩物品在搬運中的重心必須處于支撐面內(nèi)而且盡量低,減少傾倒的可能減少急停和轉彎盡量使用自然力和機械進行搬運搬運活性指數(shù)狀態(tài)說明處理的工作操作的次數(shù)活性指數(shù)集中立起舉起移動任意放置任意地放置于地面上、臺上、棚架上 40集中集中放置于容器、箱子、袋子,或捆扎起來 31附有枕木放置于搬運臺、枕木上、裝貨臺上面,可以很快拿起來 22車上放置于車子上面13移動中放置于移動中的輸送帶043 3、搬運改善常
40、用的方法、搬運改善常用的方法A.提高搬運活性a.改善設計,是物品容易搬運b.把物品盡量集中(運用箱子、推車、棧板等)c.減少再操作(如直接放在容器內(nèi),裝滿后直接放到裝載平臺上)B.自動化a.利用重力b.利用機械c.提高機械利用率C.改善搬運路線a.減少通道的逆行和轉彎b.合理地縮短工作站之間的距離c.作好機械設備的布置D.提高安全性a.消除費力的搬運b.搬運作業(yè)標準化搬運分析搬運分析1、搬運分析記號基本記號放置記號動力記號移動線其他記號2 2、搬運通路分析、搬運通路分析平面流動圖立體流動圖在不同的樓層之間移動物品時M1M2M3M4M5 3 3、搬運工程分析分類、搬運工程分析分類直線式搬運工程分
41、析使用搬運記號分解制品流動過程再將內(nèi)容、搬運重量、搬運距離、所需時間、使用的工具等一一記錄下來分析,找出改善的著眼點布置圖式搬運工程分析圖布置圖式搬運工程分析圖4 4、搬運過程分析的程序、搬運過程分析的程序確定分析的目的縮短搬運時間縮短搬運距離減輕搬運作業(yè)的疲勞使搬運路線更合理減少搬運次數(shù)提高搬運活性確定分析范圍將所要分析的工作場所確定清楚確定制品因為不同制品,其工藝內(nèi)容不同,流動方式不同分析準備觀測的器具記錄用紙平面布置圖準備分析用紙將觀察日期、觀察人、作業(yè)現(xiàn)場、制品名稱計入分析用紙觀測并記錄記入分析表整理結果擬訂改善方案結合其他工程分析一起實施,效果更好搬運分析整理表項目次數(shù)重量距離(m)時間(分)裝卸6300kg10搬運人工50kg4020工具605自動202停滯420視頻分享Auto-Quality是什么?是什么? 提提 問問 任務書:1.選定改善對象(提供選擇依據(jù))30分鐘2.LOB分析即改善方向3.動作分析及改善方向結果要求:1.改善點20個以上,立刻改善點至少5個2.改善對象改善完成后,效率提升5%以上提醒:我們正在進行一整天的脫產(chǎn)培訓!現(xiàn)場改善,小組成員在一起!不要分開!小組呈現(xiàn)
- 溫馨提示:
1: 本站所有資源如無特殊說明,都需要本地電腦安裝OFFICE2007和PDF閱讀器。圖紙軟件為CAD,CAXA,PROE,UG,SolidWorks等.壓縮文件請下載最新的WinRAR軟件解壓。
2: 本站的文檔不包含任何第三方提供的附件圖紙等,如果需要附件,請聯(lián)系上傳者。文件的所有權益歸上傳用戶所有。
3.本站RAR壓縮包中若帶圖紙,網(wǎng)頁內(nèi)容里面會有圖紙預覽,若沒有圖紙預覽就沒有圖紙。
4. 未經(jīng)權益所有人同意不得將文件中的內(nèi)容挪作商業(yè)或盈利用途。
5. 裝配圖網(wǎng)僅提供信息存儲空間,僅對用戶上傳內(nèi)容的表現(xiàn)方式做保護處理,對用戶上傳分享的文檔內(nèi)容本身不做任何修改或編輯,并不能對任何下載內(nèi)容負責。
6. 下載文件中如有侵權或不適當內(nèi)容,請與我們聯(lián)系,我們立即糾正。
7. 本站不保證下載資源的準確性、安全性和完整性, 同時也不承擔用戶因使用這些下載資源對自己和他人造成任何形式的傷害或損失。
最新文檔
- 物業(yè)管理制度:常見突發(fā)緊急事件應急處置程序和方法
- 某物業(yè)公司冬季除雪工作應急預案范文
- 物業(yè)管理制度:小區(qū)日常巡查工作規(guī)程
- 物業(yè)管理制度:設備設施故障應急預案
- 某物業(yè)公司小區(qū)地下停車場管理制度
- 某物業(yè)公司巡查、檢查工作內(nèi)容、方法和要求
- 物業(yè)管理制度:安全防范十大應急處理預案
- 物業(yè)公司巡查、檢查工作內(nèi)容、方法和要求
- 某物業(yè)公司保潔部門領班總結
- 某公司安全生產(chǎn)舉報獎勵制度
- 物業(yè)管理:火情火災應急預案
- 某物業(yè)安保崗位職責
- 物業(yè)管理制度:節(jié)前工作重點總結
- 物業(yè)管理:某小區(qū)消防演習方案
- 某物業(yè)公司客服部工作職責