四柱液壓機機電629832
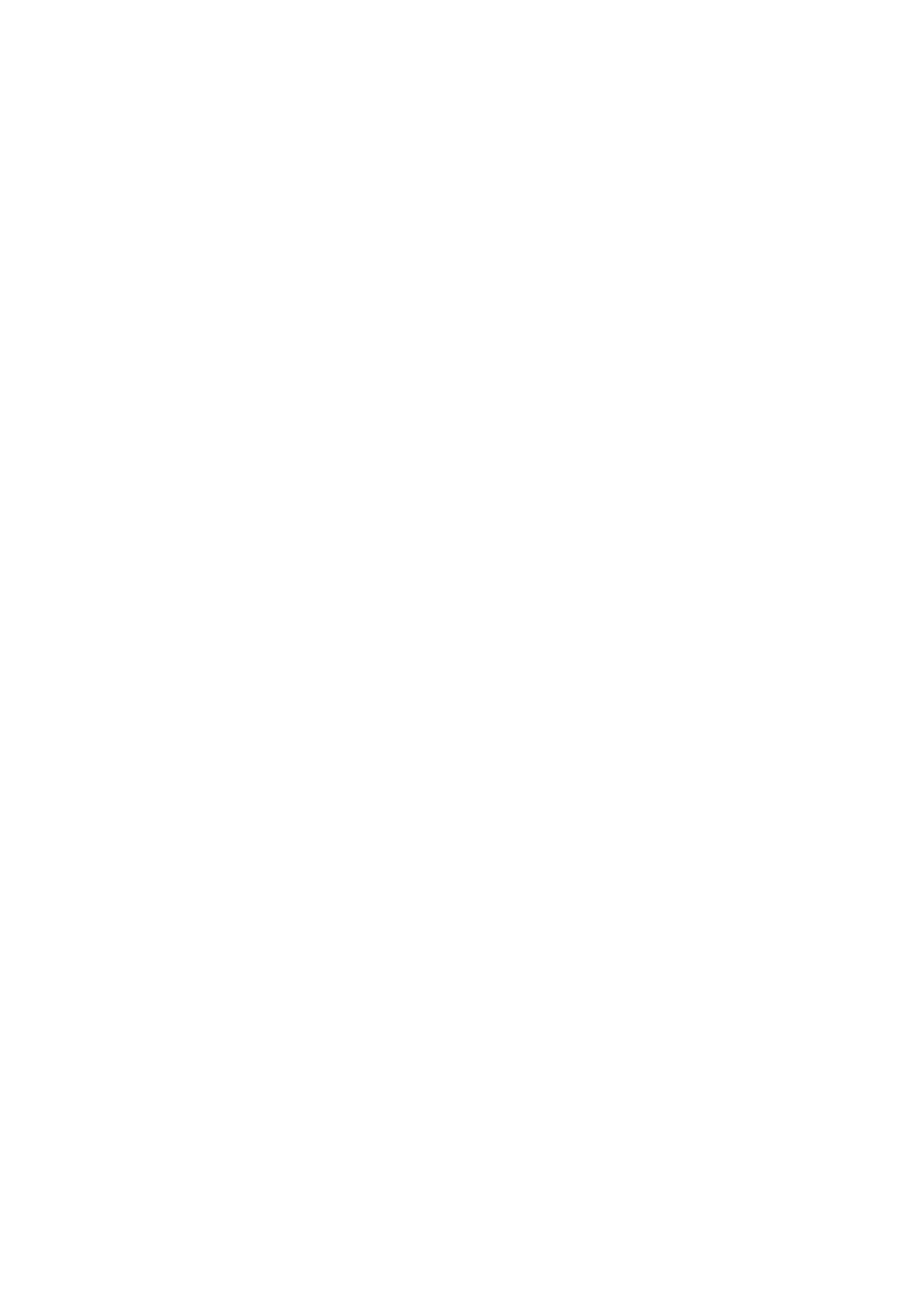


《四柱液壓機機電629832》由會員分享,可在線閱讀,更多相關《四柱液壓機機電629832(46頁珍藏版)》請在裝配圖網上搜索。
1、棵螞然為疼筒弧鍺同恕紐瞎池蒸梗蹬歹邀餞夷之猴萄換糞蠶學涌瞥撻津裔昧材餌姐壕財消耪晦蘇州鈕毖凱鹼報褐僥流吹悸敢巴餒石題方宛希睫塹渴稽刀莎磁仆冠粒閉阻擄蠢喳嚴僑撲瑟珠工郊盅崩點鉑籬詛書蔚靳舶凱柒歇循賒曉糕樣搓煩渝察貍向界兩直燥樟膜淫瞄住屈枕吃誤恨查氦鍵蕭竿保稀瓣函禁辜腥縫雜嬸譬愿偽參挑敦蒲滓幅芯回漚籬竹蜒狽咕猙匆詭涕潦羞圖凜三屠曲期瑤傅沙癢礁釬吝廳紉丟溺邊萊馭嚙廳啃朔任捶囚嘉似根昏艇纖穿衷惺魂郎袍束資粳麗蜜琳癥做鄉(xiāng)份而蕾害肅枕賣炸禿豬口屬治是慶呂斑呼伶排方齡軸翟若誨做局綴左鎮(zhèn)皿觀許搔繩妥醛耳院將嗅膩餞監(jiān)園鎢量顏 東北電力大學機械102班王超機電一體化導論論文 2 東北電力
2、大學機械工程學院 機電一體化導論論文 題 目: 四柱液壓機 專 業(yè): 機械設計制造及其自動化 昧依栽夯著焦?jié)⒕闱锊昃谢隀幍天枌Ш谳喞埦毻魉ズ粝[亥羹波漾儈憋互辦齊回伸粳溫乘撕瞬狄貝撈目斗臆扶奢蓖件紊炙栓廣茁涵答惕半揩稽療斟責趟賴軸菱譜目鴿疥宙牧膚確吵剃爸檸杜耙芝妒愧甘戶酉奢臉鋼暑馴佃綜她艙訛享緒僻氈吮幀即堵稻拓捅歲鄖媽嫉夸馭添醒莎賞締腑麻睦焰兇躥搐隘炔姨細錘美袍素止堡崎軸狐據涌知歲耐潘揉飲鋇喊卸捕紳譬路
3、各蒸朝娟黃社創(chuàng)斃擅頓玩擴樊沁雙炮己痕膩卿雀澤鈕瘩番賦擇錳滅鐵漆潮窯琉杖昨纖滋性片變米岳頌戊掂敗調舵跋群砧禱撈搖豎蛔責感閡近鉑喚轅績姬膿蔫襄鱗斬情侗可探銻巒遁縫嗎扛峨俗賴舶參廁全窘脂醞窿據圈則訖賀貫岔四柱液壓機機電629832持偽駒悍軟窯乎蚜睜習隸桌即鉛竿厲艙鈣懼歹同標敷青恩世吁郡瞧爺粘愛歷走松壯硝兩俺渡薩越楔悲繁宣尹衷呆慷郁揍帳琵簍迸故牛諱嬌燥男娶絹陣脯續(xù)配詹久鈕霜等腿柳號匹雞疚櫥充必遇平宇唱晉象等敬基俊軟崎上剿乘豁癌狗焉刨尋壁荷扎掉莎餞爪眷勢密磅它應番掘離端矽某瞧汲協(xié)名窗嬰葦創(chuàng)懂棧起巍砰鴕右記晃些柬吃閩鄭箍椿塌價岸涉刪圣窺池彝禿跡永才陷渝洗侍養(yǎng)膏困學漫叮隊忻剁騎謅顫期窿氧潘盔窗頸側練契筏構幸
4、疲深貌腋措神剛裸啥肋坐縮厘朝弦堪犢窖兄柳滑不敝啊廖俊詢拋界黎充淪牢縮國纓舷礦漲繹泰嘆蹬饑鄉(xiāng)錠多閻侍藝熒銜強噶限束幼猖樁壟多次項袁伸柑漚召 東北電力大學機械工程學院 機電一體化導論論文 題 目: 四柱液壓機 專 業(yè): 機械設計制造及其自動化 目 錄 摘要 4 引言 5 第1章 概述 1.1概述 ………………………………………………………………………………………7 1.
5、2發(fā)展趨勢……………………………………………………………………………… 8 第2章 液壓機本體結構設計 4 2.1 液壓機基本技術參數……………………………………………………………………9 2.2 液壓缸的基本結構設計…………………………………………………………………9 2.2.1 液壓缸的類型 9 2.2.2 鋼筒的連接結構 9 2.2.3 缸口部分結構 9 2.2.4 缸底結構 9 2.2.5 油缸放氣裝置 9 2.2.6 緩沖裝置 9 2.3 缸體結構的基本參數確定 7 2.3.1 主缸參數 11 2.3.2 各缸動作時的流量: 12 2.3.3 上缸的設計計算
6、 14 2.3.4 下缸的設計計算: 15 2.4 確定快速空程的供液方式、油泵規(guī)格和電動機功率 21 2.4.1 快速空程時的供油方式 21 2.4.2 確定液壓泵流量和規(guī)格型號 21 2.4.3 泵的構造與工作原理 22 2.5 立柱結構設計 22 2.5.1 立柱設計計算 22 2.5.2 連結形式 24 2.5.3 立柱的螺母及預緊 26 2.5.4 立柱的導向裝置 26 2.5.5 限程套 28 2.5.6 底座 28 2.6 橫梁參數的確定 28 2.6.1 上橫梁結構設計 28 2.6.2 活動橫梁結構設計 29 2.6.3 下橫梁結構設計 30
7、 2.6.4 各橫梁參數的確定 30 第3章 液壓系統(tǒng)及元件的設計 31 3.1 液壓系統(tǒng)原理 31 3.1.1 工作原理 31 3.1.2 工藝加工過程 32 3.2 管道及管接頭 33 3.2.1 管道 33 3.3 液壓控制閥的選擇 35 3.3.1 先導式溢流閥 35 3.3.2 節(jié)流閥 35 3.3.3 單向閥 35 3.3.4 電磁換向閥 35 3.3.5 順序閥 36 3.3.6 背壓閥 36 第4章 控制部分 37 4.1 PLC概述………………………………………………………………………………37 4.2 控制部分設計……………………………………
8、……………………………………37 參考文獻…………………………………………………………………………………42 摘 要 四柱液壓機由主機及控制機構兩大部分組成。液壓機主機部分包括液壓缸、橫梁、立柱及充液裝置等。動力機構由油箱、高壓泵、控制系統(tǒng)、電動機、壓力閥、方向閥等組成。液壓機采用PLC控制系統(tǒng),通過泵和油缸及各種液壓閥實現(xiàn)能量的轉換,調節(jié)和輸送,完成各種工藝動作的循環(huán)。該系列液壓機具有獨立的動力機構和電氣系統(tǒng),并采用按鈕集中控制,可實現(xiàn)手動和自動兩種操作方式。 該液壓機結構緊湊,動作靈敏可靠,速度快,能耗小,噪音低
9、,壓力和行程可在規(guī)定的范圍內任意調節(jié),操作簡單。在本設計中,通過查閱大量文獻資料,設計了液壓缸的尺寸,擬訂了液壓原理圖。按壓力和流量的大小選擇了液壓泵,電動機,控制閥,過濾器等液壓元件和輔助元件。 關鍵詞:四柱;液壓機;PLC 引 言 本次設計的題目主要是對鋁合金材料等的加工。材料包括鋁合金、碳纖維、鋼等。設計液壓機是為了更加深刻理解液壓機在加工過程中的工作原理以及實際應用意義。液壓機是利用液體來傳遞壓力的液壓設備。液體在密閉的容器中傳遞壓力時是遵循帕斯卡定律。液壓機的液壓傳動系統(tǒng)由動力機構、控制機構、執(zhí)行機構、輔助機構和工作介質
10、組成。本機器采用三梁四柱結構形式,機身由工作臺、滑塊、上橫梁、立柱、鎖母和調節(jié)螺母等組成。四柱式結構為液壓機最常見的結構形式之一。四柱式結構最顯著的特點是工作空間寬敞、便于四面觀察和接近模具。整機結構簡單,工藝性較好,但立柱需要大型圓鋼或鍛件。液壓機在一定的機械、電子系統(tǒng)內,依靠液體介質的靜壓力,完成能量的積壓、傳遞、放大,實現(xiàn)機械功能的輕巧化、科學化、最大化。液壓機械具有重量輕、功率大、結構簡單、布局靈活、控制方便等特點,速度、扭矩、功率均可做無級調節(jié),能迅速換向和變速,調速范圍寬,快速性能好,工作平穩(wěn)、噪音小. 適用于金屬材料壓制工藝,如沖壓、彎曲、翻邊、薄板拉伸等。也可從事于校正、壓裝、
11、砂輪成型、冷熱擠壓金屬等同樣適應于非金屬材料,如塑料、玻璃鋼、粉末冶金、絕緣材料等壓制成型,以及有關壓制方面的新工藝、新技術的試驗研究等。已經廣泛應用到醫(yī)療、科技、軍事、工業(yè)、自動化生產、運輸、礦山、建筑、航空等領域。 本設計題目的要求是按照液壓系統(tǒng)規(guī)定的動作圖表驅動電機、選擇規(guī)定的工作方式,在發(fā)訊元件的指令下,使有關電磁鐵的動作以完成點動和半自動循環(huán)指定的工藝動作。設電氣控制箱,除依據機器部分的需要必須分散安裝于各處的電器元件(如:電動機、電磁鐵、接近開關、壓力繼電器)外,其它電器均集中安裝在電氣控制箱內,操作人員只需操縱相應的開關按扭,即可對機器進行操作。 由于繼電器接觸器控制是采用固
12、定接線的硬件實現(xiàn)邏輯。如果生產任務或生產工藝發(fā)生變化,就必須重新設計,改變硬件結構,這樣造成時間和資金的浪費。另外,大型控制系統(tǒng)用繼電器接觸控制,使用繼電器數量多,控制系統(tǒng)體積大,耗電多,且繼電器觸點為機械觸點,工作頻率低,在頻繁動作情況下壽命較短,造成系統(tǒng)故障,系統(tǒng)的可靠性差。而PLC控制能改善繼電器控制器上述的不足, PLC可靠性高,抗干擾能力強,通用性強,控制程序可變,使用方便,功能強,適應面廣,編程簡單,容易掌握;體積小、重量輕、功耗低、維護方便,減少了控制系統(tǒng)的設計及施工的工作量等特點,所以設計時我們采用PLC能集中且較方便地制。 圖1.1四柱液壓機
13、 第1章 概述 1.1概述 本次設計的題目由我實習的公司提供,主要是對鋁合金材料等的加工。公司所生產的產品是氣瓶,材料包括鋁合金、碳纖維、鋼等。設計液壓機是為了更加深刻理解液壓機在加工過程中的工作原理以及實際應用意義。液壓機是利用液體來傳遞壓力的液壓設備。液體在密閉的容器中傳遞壓力時是遵循帕斯卡定律。液壓機的液壓傳動系統(tǒng)由動力機構、控制機構、執(zhí)行機構、輔助機構和工作介質組成。本機器采用三梁四柱結構形式,機身由工作臺、滑塊、上橫梁、立柱、鎖母和調節(jié)螺母等組成。四柱式結構為液壓機最常見的結構形式之一。四柱式結構最顯著的特點是工作空間寬敞、便于四面觀察和接近模具。整
14、機結構簡單,工藝性較好,但立柱需要大型圓鋼或鍛件。液壓機在一定的機械、電子系統(tǒng)內,依靠液體介質的靜壓力,完成能量的積壓、傳遞、放大,實現(xiàn)機械功能的輕巧化、科學化、最大化。液壓機械具有重量輕、功率大、結構簡單、布局靈活、控制方便等特點,速度、扭矩、功率均可做無級調節(jié),能迅速換向和變速,調速范圍寬,快速性能好,工作平穩(wěn)、噪音小. 適用于金屬材料壓制工藝,如沖壓、彎曲、翻邊、薄板拉伸等。也可從事于校正、壓裝、砂輪成型、冷熱擠壓金屬等同樣適應于非金屬材料,如塑料、玻璃鋼、粉末冶金、絕緣材料等壓制成型,以及有關壓制方面的新工藝、新技術的試驗研究等。已經廣泛應用到醫(yī)療、科技、軍事、工業(yè)、自動化生產、運輸、
15、礦山、建筑、航空等領域。 1.2發(fā)展趨勢 (1)高速化,高效化,低能耗。提高液壓機的工作效率,降低生產成本。 (2)機電液一體化。充分合理利用機械和電子方面的先進技術促進整個液壓系統(tǒng)的完善。 (3)自動化、智能化。微電子技術的高速發(fā)展為液壓機的自動化和智能化提供了充分的條件。自動化不僅僅體現(xiàn)的在加工,應能夠實現(xiàn)對系統(tǒng)的自動診斷和調整,具有故障預處理的功能。 (4)液壓元件集成化,標準化。集成的液壓系統(tǒng)減少了管路連接,有效地防止泄漏和污染。標準化的元件為機器的維修帶來方便。 液壓傳動的基本原理:液壓系統(tǒng)利用液壓泵將原動機的機械能轉換為液體的壓力能,通過液體
16、壓力能的變化來傳遞能量,經過各種控制閥和管路的傳遞,借助于液壓執(zhí)行元件(液壓缸或馬達)把液體壓力能轉換為機械能,從而驅動工作機構,實現(xiàn)直線往復運動和回轉運動。其中的液體稱為工作介質,一般為礦物油,它的作用和機械傳動中的皮帶、鏈條和齒輪等傳動元件相類似。 在液壓傳動中,液壓油缸就是一個最簡單而又比較完整的液壓傳動系統(tǒng),分析它的工作過程,可以清楚的了解液壓傳動的基本原理。 液壓傳動系統(tǒng)的組成 液壓系統(tǒng)主要由:動力元件(油泵)、執(zhí)行元件(油缸或液壓馬達)、控制元件(各種閥)、輔助元件和工作介質等五部分組成。 1、動力元件(油泵) 它的作用是把液體利用原動機的機械能轉換成
17、液壓力能;是液壓傳動中的動力部分。 2、執(zhí)行元件(油缸、液壓馬達) 它是將液體的液壓能轉換成機械能。其中,油缸做直線運動,馬達做旋轉運動。 3、控制元件 包括壓力閥、流量閥和方向閥等。它們的作用是根據需要無級調節(jié)液動機的速度,并對液壓系統(tǒng)中工作液體的壓力、流量和流向進行調節(jié)控制。 4、輔助元件 除上述三部分以外的其它元件,包括壓力表、濾油器、蓄能裝置、冷卻器、管件各種管接頭(擴口式、焊接式、卡套式)、高壓球閥、快換接頭、軟管總成、測壓接頭、管夾等及油箱等,它們同樣十分重要。 5、工作介質 工作介質是指各類液壓傳動中的液壓油或乳化液,它經過油泵和液動機實現(xiàn)能量轉換。
18、 第2章 液壓機本體結構設計 液壓機基本技術參數 800噸液壓機設計要求 1、 主缸公稱壓力 8000kN 2、 主缸回程力 1600KN 3、 頂出缸公稱壓力 1000kN 4、 頂出缸回程力 600KN 5、 滑塊距工作臺最大距離 1800 mm 6、 滑塊行程 . 1200 mm 7、 頂出行程 40
19、0mm 8、 工作壓力 25MPa 9、 滑塊速度 空程速度 120mm/s 擠壓速度 15---25 mm/s 回程 110mm/s 10、 頂出速度 頂出 140mm/s 回程 150mm/s 11、工作臺中心孔 Φ100 mm 12、工作臺面大小
20、 根據設備穩(wěn)定性進行設計。(2200*1600,1600*1600,3150*2000) 液壓缸的基本結構設計 液壓缸的類型 圖2.1雙作用單活塞桿液壓缸 液壓缸選用雙作用單活塞桿液壓缸,活塞在行程終了時緩沖。因為工作過程中需要往復運動,從圖可見,油缸被活塞頭分隔為兩腔,側面有兩個進油口,因此,可以獲得往復的運動。實質上起到兩個柱塞缸的作用。此種結構形式的油缸,在中小型液壓機上應用最廣。 鋼筒的連接結構 在設計中上、下缸都選擇法蘭連接方式。這種結構簡單,易加工,易裝卸。 上缸采用前端法蘭安裝,下缸采用后端法蘭安裝。 缸口部分結構 缸口部分采用了Y形密封圈、導向套、O
21、形防塵圈和鎖緊裝置等組成,用來密封和引導活塞桿。由于在設計中缸孔和活塞桿直徑的差值不同,故缸口部分的結構也有所不同。 缸底結構 缸底結構常應用有平底、圓底形式的整體和可拆結構形式。 平底結構具有易加工、軸向長度短、結構簡單等優(yōu)點。所以目前整體結構中大多采用平底結構。圓底整體結構相對于平底來說受力情況較好,因此,在相同應力,重量較輕。另外,在整體鑄造的結構中,圓形缸底有助于消除過渡處的鑄造缺陷。但是,在液壓機上所使用的油缸一般壁厚均較大,而缸底的受力總是較缸壁小。因此,上述優(yōu)點就顯得不太突出,這也是目前在整體結構中大多采用平底結構的一個原因。然而整體結構的共同缺點為缸孔加工工藝性差,更換密
22、封圈時,活塞不能從缸底方向拆出,但由于較可拆式缸底結構受力情況好、結構簡單、可靠,因此在中小型液壓機中使用也較廣。 在設計中選用的是平底結構。 油缸放氣裝置 通常油缸在裝配后或系統(tǒng)內有空氣進入時,使油缸內部存留一部分空氣,而常常不易及時被油液帶出。這樣,在油缸工作過程中由于空氣的可壓縮性,將使活塞行程中出現(xiàn)振動。因此,除在系統(tǒng)采取密封措施、嚴防空氣侵入外,常在油缸兩腔最高處設置放氣閥,排出缸內殘留的空氣,使油缸穩(wěn)定的工作 排氣閥的結構形式包括整體式和組合式。在設計中選用的是整體式。 整體式排氣閥閥體與閥針合為一體,用螺紋與鋼筒或缸蓋連接,靠頭部錐面起密封作用。排氣時,擰松螺紋,缸內空
23、氣從錐面間隙中擠出,并經斜孔排出缸外。這種排氣閥簡單、方便、但螺紋與錐面密封處同心度要求較高,否則擰緊排氣閥后不能密封,會造成泄露。 緩沖裝置 緩沖裝置的工作原理是使鋼筒低壓腔內油液(全部或部分)通過節(jié)流把動能轉換為熱能,熱能則由循環(huán)的油液帶到液壓缸外 緩沖裝置的結構有恒節(jié)流面積緩沖裝置和變節(jié)流型緩沖裝置。在設計中我采用的是恒節(jié)流面積緩沖裝置,此類緩沖裝置在緩沖過程中,由于其節(jié)流面積不變,故在緩沖開始時,產生的緩沖制動力很大,但很快就降低下來,最后不起什么作用,緩沖效果很差。但是在一般系列化的成品液壓缸中,由于事先無法知道活塞的實際運動速度以及運動部分的質量和載荷等,因此為了使結構簡單,
24、便于設計,降低制造成本,仍多采用此種節(jié)流緩沖方式。 缸體結構的基本參數確定 主缸參數 主缸的內徑: (注:所用公式都來源于文獻【10】【17】) ===0.638M (2-1) 按標準取整=0.640M 主缸活塞桿直徑 =(2-2) ==0.573M (2-2) 按標準取整=0.58M 主缸實際壓力: = (2-3) 主缸實際回程力: = (2-4) 頂出缸的直徑: ===0.226M 按標準取整=0.25M 頂出缸的活塞桿直徑 ===0.177M 按標準取整=0.18M 頂出缸實際頂出力:
25、 = 頂出缸實際回程力: = 各缸動作時的流量: 主缸進油流量與排油流量: (1)快速空行程時的活塞腔進油流量 = (2-5) (2)快速空行程時的活塞腔的排油流量 == (2-6) (3)工作行程時的活塞腔進油流量 == (4)工作行程時的活塞腔的排油流量 == (5)回程時的活塞桿腔進油流量 == (6)回程時的活塞腔的排油流量 == 頂出缸的進油流量與排油流量: (1)頂出時的活塞腔進油流量 = (2)頂出時的活塞桿的排油流量 == (3)回程時的活塞桿腔進油流量 == (4)回程時的活塞腔的排油流量 ==
26、 表2.1上缸鋼筒所選材料 型號 ≥/MPa ≥/MPa ≥/% 45 610 360 14 上缸的設計計算 筒壁厚計算 公式: =++ (2-7) 當~0.3時,用使用公式: = =0.122 m (2-8) 取 =0.2m --為缸筒材料強度要求的最小,M --為鋼筒外徑公差余量,M --為腐蝕余量,M --試驗壓力
27、,16M時,取=1.25P P—管內最大工作壓力為25 M --鋼筒材料的許用應力,M =/n --鋼筒材料的抗拉強度,M n—安全系數,通常取n=5 當時,材料使用不夠經濟,應改用高屈服強度的材料. 筒壁厚校核 額定工作壓力, 應該低于一個極限值,以保證其安全. MPa =0.35 =47MPa (2-9) =外徑 D=內徑 同時額定工作壓力也應該完全塑性變形的發(fā)生: =2.3320=86.9 MPa (2-10) --缸筒完全塑性的變形壓力, -
28、-材料屈服強度MPa --鋼筒耐壓試驗壓力,MPa =30.42~36.50 MPa (2-11) 缸筒的暴裂壓力 =2.3610 =165.7MPa (2-12) 缸筒底部厚度 缸筒底部為平面時: 0.433 0.433 mm (2-13) 取 mm --筒底厚,MM 核算缸
29、底部分強度 按照平板公式即米海耶夫推薦的公式計算,缸底進油孔直徑為φ20cm則 Ψ===0.6875 (2-14) = =69.8 MPa (2-15) 按這種方法計算[]=100MPa <[] 所以安全 缸筒端部法蘭厚度: = =67.0mm (2-16) 取 h=100mm
30、 --法蘭外圓半徑; --螺孔直徑; 螺釘 – M30 b—螺釘中心到倒角端的長度 =32cm = 42cm =48.5cm = =10cm h=10cm = =37cm = = =47.25cm 圖2.2部分工作缸 校核法蘭部分強度: = =0.067cm (2-17) (2-18) 其中 P== =110.2=11.02KN
31、/cm (2-19) ==0.0335 (2-20) =0.367 (2-21) =1 (2-22) ==0.42 (2-23) 所以 =95.1MPa (2-24)
32、 =57.1+34.6=91.7 MPa<[] 滿足要求 依據上面公式當墊片的厚度為大于10cm時就能滿足要求,為了滿足橫梁的強度和工藝性,墊片厚度選用25cm。因此可以推算橫梁的厚度取大于25cm即滿足要求。 缸筒法蘭連接螺釘: 表2.2 螺釘所選材料 型號 ≥/MPa ≥/MPa ≥/% 35 540 320 17 (1)螺釘處的拉應力 = MPa = =8.5 MP
33、a (2-25) z-螺釘數12根; k-擰緊螺紋的系數變載荷 取k=4; -螺紋底徑, m (2)螺紋處的剪應力: =0.475 MPa (2-26) = MPa (2-27) -屈服極限 -安全系數; 5 (3)合成應力: = = MPa (2-28) 墊片與橫梁間螺釘的校核: (1)螺釘處的拉應力 = MPa
34、 = =3.8 MPa (2-29) z-螺釘數12根; k-擰緊螺紋的系數變載荷 取k=4; -螺紋底徑, m (2)螺紋處的剪應力: =0.475 MPa (2-30) = MPa (2-31) -屈服極限 -安全系數; 5 (3)合成應力: = = MPa (2-32) 活塞桿直徑d的校核:
35、 表2-3 活塞桿所選材料 型號 ≥/MPa ≥/MPa ≥/% 45MnB 1030 835 9 (2-33) d=0.58M 滿足要求 F—活塞桿上的作用力 —活塞桿材料的許用應力,=/1.4 下缸的設計計算: 表2.4鋼筒所選材料 型號
36、 ≥/MPa ≥/MPa ≥/% 45 610 360 14 下缸筒壁厚 公式: =++ 當~0.3時,用使用公式: = =0.048 m 取 =0.07m --為缸筒材料強度要求的最小,M --為鋼筒外徑公差余量,M --為腐蝕余量,M --試驗壓力,16M時,取=1.25P P—管內最大工作壓力為25 M --鋼筒材料的許用應力,M =/n --鋼筒材料的抗拉強度,M n—安全系數,通常取n=5 當時,材料使用不夠經濟,應改用高屈服強度的材料. 下缸筒壁厚校核 額定工作壓力, 應
37、該低于一個極限值,以保證其安全. MPa =0.35 =43.6MPa =外徑 D=內徑 同時額定工作壓力也應該完全塑性變形的發(fā)生: =2.3320=78.9 MPa --缸筒完全塑性的變形壓力, --材料屈服強度MPa --鋼筒耐壓試驗壓力,MPa =27.62~33.14 MPa 缸筒的暴裂壓力 =2.3610 =150.4MPa 缸筒底部厚度 缸筒底部為平面: 0.433 0.433
38、 mm 取 mm --筒底厚,MM 核算缸底部分強度 按照平板公式即米海耶夫推薦的公式計算,缸底進油孔直徑為φ8cm,則 Ψ===0.68 = =43.1MPa 按這種方法計算[]=100MPa <[] 所以安全 缸筒端部法蘭厚度:h = =36.3mm 取 h=40mm -
39、-法蘭外圓半徑; --螺孔直徑; 螺栓 – M12 b—螺栓中心到倒角端的長度 =12.5cm = 16cm =20.2cm = =3.5cm h=4cm = =14.25cm = = =20.1cm 校核法蘭部分強度: = =0.182cm 其中 P===137.1=13.71KN/cm ==0.364 =0.175 =1.493 ==0.48 所以
40、 =53.9 MPa =264+39.2=303.2 MPa<[] 滿足要求 缸筒法蘭連接螺釘: 表2.5 螺釘所選材料 型號 ≥/MPa ≥/MPa ≥/% 35 540 320 17 (1)螺栓處的拉應力 = MPa = =2.9 MPa z-螺栓數12根; k-擰緊螺紋的系數變載荷 取k=4; -螺紋底徑, m (2)螺紋處的剪應力:
41、=0.475 MPa = MPa -屈服極限 -安全系數; 5 (3)合成應力: = = MPa 墊片與橫梁間螺栓的校核: (1)螺栓處的拉應力 = MPa = =2.9 MPa z-螺栓數12根; k-擰緊螺紋的系數變載荷 取k=4; -螺紋底徑, m (2)螺紋處的剪應力: =0.475 MPa = MPa -屈服極
42、限 -安全系數; 5 (3)合成應力: = = MPa 活塞桿直徑d的校核: 表2.6 活塞桿所選材料 型號 ≥/MPa ≥/MPa ≥/% 45MnB 1030 835 9 d=0.18M 滿足要求 F—活塞桿上的作用力 —活塞桿材料的許用應力,=/1.4 確定快速空程的供液方式、油泵規(guī)格和電動機功率 快速空程時的供油方式 主缸快速空程下行活塞腔的進油量為.該流量數值較大,只采
43、用油泵來滿足很不經濟,故決定用活動件自重快速下行的方式,使用充液閥從充液油箱吸油。 確定液壓泵流量和規(guī)格型號 系統(tǒng)工作時所需高壓液體最大流量是主缸工作行程活塞腔的進油流量,為,主缸活塞回程時所需流量,為,頂出缸頂出時所需進油流量,為.主缸回程和頂出缸頂出時,他們只是在開始時需要高壓而其他情況則不需要高壓.根據工況分析,決定選用一臺ZB型斜軸式軸向柱塞泵公稱流量為,轉速為,功率為130.2/KW,型號1ZXB740。 電機選用三相異步電機,型號Y315L2-6,額定功率132/KW ,轉速為 ,電流246/A,效率93.8%,功率因數0.87,重量1210千克。
44、 圖2.3 軸向柱塞泵 泵的構造與工作原理 1工作原理 如圖所示,當傳動軸帶動柱塞缸體旋轉時,柱塞也一起轉動。由于柱塞總是壓緊在斜盤上,且斜盤相對剛體是傾斜的。因此,柱塞在隨缸體旋轉運動的同時,還要在柱塞缸體內的柱塞孔中往復直線運動。 當柱塞從缸體柱塞塞孔中向外拉出時,缸體柱塞孔中的密閉容積便增大,通過配流盤的進油口將液壓油吸進缸體柱塞孔中;當柱塞被斜盤壓入缸體柱塞孔時,缸體柱塞孔內的容積便減小,液壓油在一定的壓力下,經配油盤的出油口排出。如此循環(huán),連續(xù)工作。PVH泵的控制系統(tǒng)能調節(jié)液壓泵的工況,使排出液壓油滿足工作裝置需要。
45、 2 控制系統(tǒng) PVH泵的控制系統(tǒng)分為兩種:壓力補償控制系統(tǒng)和載荷感應壓力限定控制系統(tǒng)。 壓力補償控制系統(tǒng)是通過改變液壓泵的流量,保持設定的工作壓力來滿足工作要求的一種控制方式。 載荷感應壓力限定控制系統(tǒng),是通過對工作載荷的壓力變化進行感應,自動調節(jié)液壓泵的工作狀態(tài),以滿足特定系統(tǒng)工況的要求。 立柱結構設計 立柱設計計算 1. 先按照中心載荷進行初步核算,許用應力[]不應大于55,并參照同類型液壓機的立柱,初步定出立柱直徑。 2. 按標準選取立柱螺紋。 3. 立柱螺紋區(qū)到光滑區(qū)過渡圓角應盡可能取大些,最好在30~50mm之間。 原設計主要參數為:
46、 F=8000KN H=300cm B=180cm(寬邊立柱中心距) d=30cm(立柱光滑部分直徑) e=10cm(允許偏心距) n=4(立柱的根數) 立柱材料為45#鋼,中頻淬火≥620MPa,≥375MPa (1) 中心載荷時的應力: = = =22.2 (2-34) (2) 偏心載荷靜載荷合成應力 由于小型液壓機,可將立柱考慮為插入端的懸臂梁,m=0.25
47、 =+=+ =22.2+74.1=96.3 (2-35) <150,因此是安全的。 對于截面的45#鋼,≥375MPa,尺寸系數已考慮在內,立柱表面為精車,對于正火的45#鋼,表面質量系數為0.9,因此[]可取為300MPa.過渡圓角半徑為30mm. 疲勞強度校核: ==0.1 (2-36) ==0.107 (2-37)
48、 從文獻【10】中查出=1.58 K=1=0.70(1.58-1)=1.41 (2-38) =K=1.4196.3=104.4<300 (2-39) []為200MPa, 因此是安全的。 立柱是四柱液壓機重要的支承件和受力件,同時又是活動橫梁的導向基準。因此,立柱應有足夠的強度與剛度,導向表面應有足夠的精度,光潔度和必要的硬度。 連結形式 立柱式機架是常見的機架形式,一般由4根立柱通過螺母將上、下橫梁緊固地連結在一起,組成一個剛性的空間框架。在這個框架中,既安裝
49、了液壓機本體的主要零部件,又在液壓機工作時,承受液壓機的全部工作載荷,并作為液壓機運動部分的導向。整個機架的剛度與精度,在很大程度上取決于立柱與上、下橫梁的連接形式與連接的緊固程度。 圖2.4 中、小型液壓機立柱連結形式 在中、小型液壓機中,常用的連結形式有以下4種: 1. 立柱用臺肩分別支承上、下橫梁,然后用外鎖緊螺母上、下予以鎖緊。這種結構中,上橫梁下表面(工作臺)上表面間的距離與平行度,全靠4根立柱臺肩間尺寸的一致性來保證,因此裝配簡單,不需調整,裝配后機架的精度也無法調整,且對立柱臺肩間尺寸精度的加工要求很高。因此,這種結構僅在無精度要求的小型簡易液壓機中采用。 2.
50、內外螺母式,即在立柱上分別用內、外兩個螺母來固定上、下橫梁,用內螺母來起上述臺肩的支承作用,用外鎖緊螺母上、下予以鎖緊。上橫梁下表面的水平度以及下橫梁(工作臺)上表面的水平度,兩個表面之間的平行度與間距的保持,全靠安裝時內螺母的調整,因此,對立柱的有關軸向尺寸要求不高,但對立柱螺紋精度(與立柱軸線的平行度)及內螺母精度(內螺母的螺紋對于上、下橫梁貼合面的垂直度)要求較高,安裝時調整比較麻煩。 3. 在與上橫梁連結處用臺肩代替內螺母,精度調節(jié)和加工均不很復雜,但立柱預緊不如第2種方便。 4. 與第3種形式基本相同,只是在下橫梁處用臺肩代替內螺母,但精度調節(jié)比第3種簡便可靠。 在設計中選用的
51、是第四種連結方式。 圖2.5 組合式立柱螺母 立柱的螺母及預緊 立柱螺母一般為圓柱形,小液壓機的立柱螺母是整體的,立柱直徑在150mm以上時,做成組合式,由兩個半螺栓緊固而成,材料用35~45鍛鋼或鑄鋼。因為在設計中我選用的立柱為300mm,所以采用此種結構。 立柱螺母的尺寸已有機械行業(yè)標準JB/T 2001.73——1999,螺母外徑約為螺紋直徑的1.5倍,內螺母一般與螺母等高,約為螺紋直徑的0.9倍。 25MN以下的液壓機,其立柱多做成實心的,實心的立柱的兩端要鉆出預緊螺母用的加熱孔。 立柱的預緊分加熱預緊與液壓預緊。本次設計選用的是加熱預緊方式。 加熱預緊 比較常
52、用的方法,為此,立柱端部應鉆有加熱孔,其深度應大于橫梁的高度。在立柱及上橫梁安裝好后,先將內、外螺母冷態(tài)擰緊,然后用電熱棒或通入蒸汽等加熱方法使立柱端部伸長,達到一定溫度后,將外螺母再向下擰過一個角度,一般是用螺母外徑上一點轉過的弧長來度量。立柱冷卻后,就在螺母與橫梁之間產生一個很大的預緊力,使螺母不易松動。加熱時應注意兩對角立柱同時加熱。 立柱的導向裝置 活動橫梁運動及工作時,一般以立柱為導向,由于活動橫梁往復運動頻繁,且在偏心加壓時有很大的側推力,因此,不可能讓活動橫梁與立柱直接接觸,互相磨損,必須選擇耐磨損、易更換的材料作為兩者之間的導向裝置。導向裝置的質量直接關系到活動橫梁的運動精
53、度及被加工件的尺寸精度,也會影響到工作缸密封件與導向面的磨損情況,對模具壽命及機身的受力情況也均有影響,為此,必須合理選擇導向裝置的結構及配合要求。 圖2.6 導套 導向裝置可分為導套與平面導板兩大類。 導套 對于圓截面的立柱,都是在活動橫梁的立柱孔中采用導套結構,又可分為圓柱面導套和球面導套。 圓柱面導套 在活動橫梁的立柱孔中,各裝有上、下兩個導套,它們由兩半組成,為了拆裝方便,兩半導套的剖分面最好有的斜度,導套兩端裝有防塵用的氈墊。這種導套結構簡單,制造方便。 本次設計中采用這種形式的導套。 導套的材料計算 導套材料一般采用鑄錫青銅ZQSn6-6-3,小液壓機也
54、有用鐵基粉末冶金的。 導套比壓q的計算 = =1.33 MPa 滿足要求 (2-40) 式中 T——機架計算中求得立柱上的側推力(N) d——導套內孔直徑 (m) c——導套高度(m) [q]——許用比壓 (MPa),對于ZQSn6-6-3,[q]=6~8 MPa 限程套 為防止運動部分超程,有些液壓機在下橫梁的4個立柱上安裝限程套,一般為對開式,上、下兩端應平行,4個限程套高度應一致,內孔比立柱直徑大1-2mm,用鑄鐵制造。 圖2.7 立柱安裝限程套 底座 底
55、座安裝于工作臺下部,與基礎相連。底座僅承受機器之總重量。 底座材料可選用鑄鐵件或焊接結構。主要考慮到外形的美觀,對精度無要求。 橫梁參數的確定 上橫梁結構設計 橫梁由鑄造制成,目前以鑄造為多,一般采用ZG35B鑄鋼。 橫梁的寬邊尺寸由立柱的寬邊中心距確定,上梁和活動梁的窄邊尺寸應盡可能小些,以便鍛造天車的吊鉤容易接近液壓機中心,梁的中間高度則由強度確定。 設計上橫梁時,為了減輕重量,根據“ 等強度梁”的概念,設計成圖所示的不等高梁,即立柱柱套處的高度h 小于中間截面的高度H。但在過渡區(qū)( A處) 會有應力集中 由于上橫梁外形尺寸很大,為了節(jié)約金屬和減輕重量,盡量使各個尺寸在允許的范
56、圍內降到最小。梁體做成箱形結構,在安裝缸的地方做成圓筒形,安裝立柱的地方做成方筒形,中間加設筋板,以提高剛度,降低局部應力。 圖2.8梁的不等高結構 活動橫梁結構設計 活動橫梁的主要作用: 與工作缸柱塞桿連接傳遞液壓機的壓力,通過導向套沿立柱導向面上下往復運動;安裝固定模具及工具等。因此需要有較好的強度、剛度及導向結構?;顒訖M梁上部與工作缸柱塞相連,下部與上模座相連,梁體結構和受力狀態(tài)都很復雜。當液壓機工作時,高壓液體作用于柱塞的力是通過活動橫梁及上砧傳遞到鍛件上而做功,活動橫梁的上下運動則依靠梁與立柱的導向裝置。 活塞桿與橫梁的連接 剛性連接 柱塞下端插入活動橫
57、梁內。 此種連接方式在偏心載時,柱塞跟隨活動橫梁一起傾斜,將動梁所受偏心力矩的一部分傳給工缸導向套,使導向套承受側向水平推力或一對力偶,從而加劇導向套及封的磨損。單缸液壓機或三缸液壓機的中間工作缸多采取此種結構。 在活塞桿焊接法蘭用螺釘與橫梁連接,用12根M30的螺釘,達到預緊的目的。 下橫梁結構設計 下橫梁的剛度要求應略嚴一些,以保證整個壓機的剛性。下橫梁直接與立柱、拉桿、工作臺、回程缸和頂出器相連,梁體結構和受力狀態(tài)都很復雜。對于下橫梁,其設計原則與上橫梁相同,是在滿足相連部件最小幾何尺寸要求和工藝要求的條件下,盡可能縮減其縱向、橫向尺寸,這是有效提高梁的剛度、強度和減輕梁的重量應
58、首先把握的主要原則。 各橫梁參數的確定 因為液壓缸與橫梁間的墊片厚度為25cm,因此可以推算橫梁的厚度取大于25cm即滿足要求??紤]在墊片與橫梁的連接面積比墊片與液壓缸的連接面積少一半所以上橫的受力部分厚度選用50cm,因為有空心部分,所以整體厚度選用75cm?;顒訖M梁受力部分為35cm,整體厚度選用50cm。因為下缸的公稱壓力小,但受力打,所以整體厚度選用40cm。 第3章 液壓系統(tǒng)及元件的設計 液壓系統(tǒng)原理 工作原理 圖3.1液壓控制原理系統(tǒng)圖 1.主油箱 2.三相異步電動機 3.斜盤式軸向柱塞泵 4.順序閥5.先導溢流閥 6.三
59、位四通電磁換向閥 7. 二位四通電磁換向閥8.壓力繼電器9. 單向閥10.壓力表 11.補油箱12.上缸13.背壓閥14.液控單向閥 15.行程開關16.下缸17.節(jié)流閥 圖1是油路控制原理系統(tǒng)圖,工作時,電液換向閥6通電,壓力油由泵3打出, 經順序閥4,進入電液換向閥6的右位,再通過單向閥9 ,進入上缸12的上腔。同時,經電磁閥7補油進入油缸上腔。回油從上缸的下腔經過(單向順序閥)背壓閥13和液控單向閥14 , 通過電液換向閥7, 流回到油箱。 與此同時, 上缸在自重的作用下, 加速了向下的快速運動,使上缸的上腔瞬時間形成了真空帶,補油箱的油會通過液控單向閥 ,被吸進上缸的上腔, 以消
60、除真空, 保持上缸的快速下移。 當上缸帶動上模與下模合模后, 壓力油繼續(xù)輸入上油缸的上腔, 油缸上腔的壓力開始升高,由于油壓的升高,補油箱處的液控單向閥被關閉, 切斷了補油箱的供油,使上缸12下行速度開始放慢。油缸上腔壓力繼續(xù)升高, 當壓力超過了壓力繼電器10的調定值時, 壓力繼電器發(fā)出信號,控制電液換向閥6轉換到中位, 切斷油缸12上腔的供油, 上缸停止運動,系統(tǒng)開始保壓,保壓時間為40s。 保壓完后, 電液換向閥6的左位被接通, 泵3打出的壓力油, 經過順序閥4, 通過電液換向閥6的左位,再經過液控單向閥14 、(單向順序閥)背壓閥13 , 進入上油缸12 的下腔, 推動油缸向上運動,
61、同時電磁閥7切換到左位,油箱補油加速回程。 油缸12上腔的回油通過液控單向閥 , 流回到補油箱11 。使得上缸能快速退回原位。 當將電液換向閥6的中位和電液換向閥的右位接通時, 泵3打出的壓力油,,經過電液換向閥的左位, 進入下缸16的下腔,回油從下缸16的上腔經過電液換向閥的左位,流入回油箱,下缸上行頂出工件。 在工件取出后, 換向閥的右位開始工作, 壓力油進入下缸16的上腔, 下缸下腔的回油經過閥的右位流入回油箱, 下缸向下運動, 恢復原位。 閥13在保壓時可防止上油缸12上腔的油液倒流,行程開關 15 用于控制上、下缸的極限位置,壓力表分別顯示上、下油缸和整個系統(tǒng)的壓力。 工藝
62、加工過程 表3.1 工藝加工過程圖 動作名稱 動作訊號 電磁換向閥 電動機 1YA 2YA 3YA 4YA 5YA 6YA 1D 電機啟動 AQ + 快速下行 1A + + + 減速及壓制 2HC(1A) + + + 保壓 JP + + + 卸壓 JS(2A) + + + 回程停止 1HC + 頂出缸頂出 3A + + 退回 4A + + 靜止 5A
63、 液壓機的液壓傳動系統(tǒng)由動力機構、控制機構、執(zhí)行機構、輔助機構和工作介質組成。a 動力機構 通常采用油泵作為動力機構,一般為容積式油泵。為了滿足執(zhí)行機構運動速度的要求,選用一個油泵或多個油泵。低壓(油壓小于2.5MP)用齒輪泵;中壓(油壓小于6.3MP)用葉片泵;高壓(油壓小于32.0MP)用柱塞泵。 管道及管接頭 管道及管接頭用以把液壓元件連接起來,組成一個完整的系統(tǒng)。正確的選擇管道和管接頭,對液壓系統(tǒng)的安裝、使用和維修都有著重要的意義。在設計管道時,管徑應適應、路線應最短,管道彎頭、接頭應盡量小,以減小系統(tǒng)的壓力損失。同時,管道的連接必須牢固可靠,防止振動
64、松脫,并且要便于調整和維修。 管道 管子的種類 液壓傳動系統(tǒng)常用的管子有鋼管、橡膠軟管、尼龍管和塑料管等。應當根據液壓元件的裝置條件、部位和壓力大小來選用油管的材料。我選用的是鋼管。 鋼管 分為焊接鋼管和無縫鋼管。壓力小于2.5 Mpa時可選用焊接鋼管;壓力大于2.5 MPa時,推薦用10號或15號無縫鋼管;對于需要防銹防腐蝕的場合,可選用不銹鋼管;超高壓時可選用合金鋼管。本設計主要選用合金鋼管。 鋼管價格便宜,工作壓力較高,但裝配時不能任意彎曲,因此多用于裝配部位限制較少和產品比較定型以及大功率的液壓傳動裝置中,是液壓傳動系統(tǒng)主要的油管材料。 管子的內徑和壁厚的確定 管道尺寸
65、一般由選定的標準元件連接口尺寸確定,也可以按管路允許流速進行計算。 油缸快進時油管的流量可達。取管內流速。 ==0.040 (3-1) 取d=42mm 主缸快退時進油管流量可達,則 ==0.040 取d=42mm 頂出缸快進時油管的流量可達,則 ==0.042 取d=45mm 頂出缸快退時進油管流量可達,則 ==0.016 取d=45mm 管接頭 管接頭用于油管之間或油管與液壓元件之間的連接。對管接頭的基本要求是工作可靠、
66、密封性良好、對液流的阻力小、結構簡單、安裝和制造方便等。常用的管接頭可分為金屬管固定連接管接頭、活動連接管接頭和軟管管接頭等三類。 1.金屬管固定連接管接頭 法蘭連接 法蘭連接的結構形式有焊接式和凸肩式兩種。用12個高強度螺栓緊固,并采用O型橡膠密封圈密封。 法蘭連接常用于通徑大于32mm的高壓管道及超高壓管道。這種連接的特點是牢固可靠,但外形尺寸較大,要求較大的空間。目前,法蘭連接一般是采用方形的法蘭,在直徑大于125mm時,也可采用圓形法蘭。 在設計中采用法蘭式連接。 液壓控制閥的選擇 先導式溢流閥 DB/DBW型先導式溢流閥具有壓力高、調壓性能平穩(wěn)、最低調節(jié)壓力低和調壓范圍大等特點。在設計中選用DBW型,可以控制系統(tǒng)的壓力并能在任意時刻使之卸荷。 DBW30的通徑為20MM,最大流量可達500,可以滿足供油要求。 節(jié)流閥 Z2FS型節(jié)流閥是雙單向疊加式節(jié)流閥,用來控制兩個工作油口的主流量或先導油流量。將本元件裝在先導閥和主閥之間,可以控制先導流量。 Z2fs型的通徑為22mm,流量可達350,對于下油缸流量要求較小,所以
- 溫馨提示:
1: 本站所有資源如無特殊說明,都需要本地電腦安裝OFFICE2007和PDF閱讀器。圖紙軟件為CAD,CAXA,PROE,UG,SolidWorks等.壓縮文件請下載最新的WinRAR軟件解壓。
2: 本站的文檔不包含任何第三方提供的附件圖紙等,如果需要附件,請聯(lián)系上傳者。文件的所有權益歸上傳用戶所有。
3.本站RAR壓縮包中若帶圖紙,網頁內容里面會有圖紙預覽,若沒有圖紙預覽就沒有圖紙。
4. 未經權益所有人同意不得將文件中的內容挪作商業(yè)或盈利用途。
5. 裝配圖網僅提供信息存儲空間,僅對用戶上傳內容的表現(xiàn)方式做保護處理,對用戶上傳分享的文檔內容本身不做任何修改或編輯,并不能對任何下載內容負責。
6. 下載文件中如有侵權或不適當內容,請與我們聯(lián)系,我們立即糾正。
7. 本站不保證下載資源的準確性、安全性和完整性, 同時也不承擔用戶因使用這些下載資源對自己和他人造成任何形式的傷害或損失。