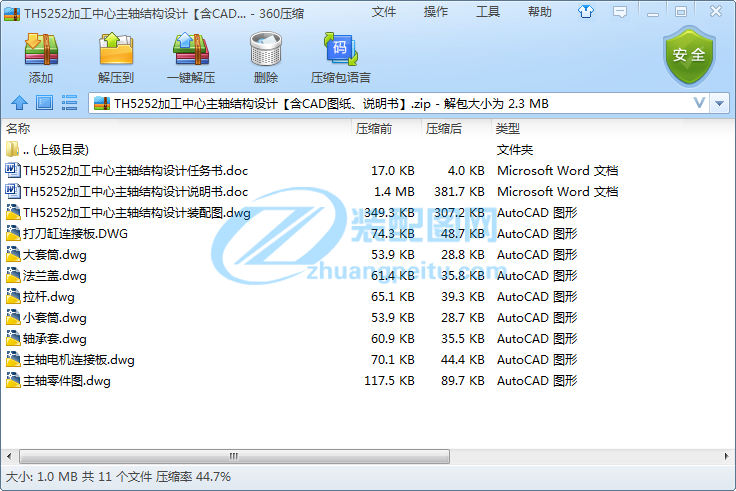
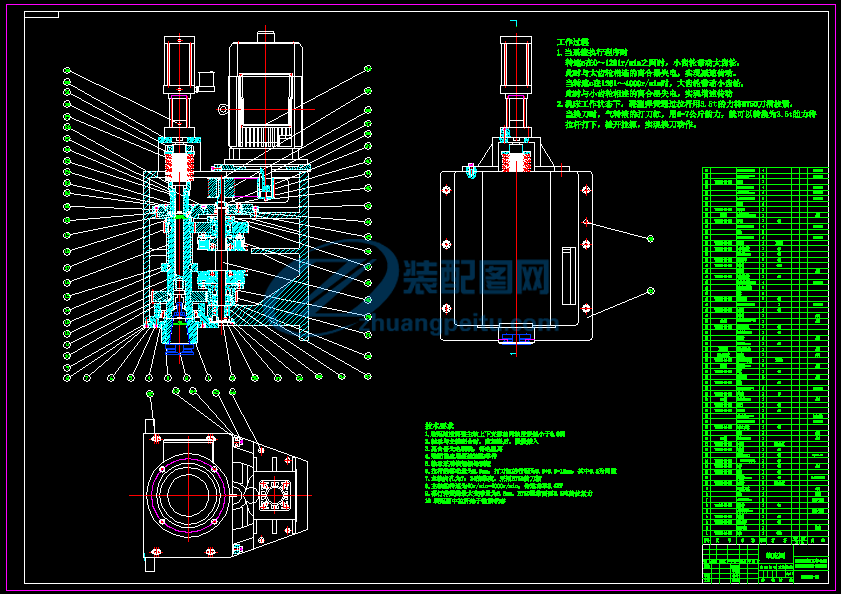
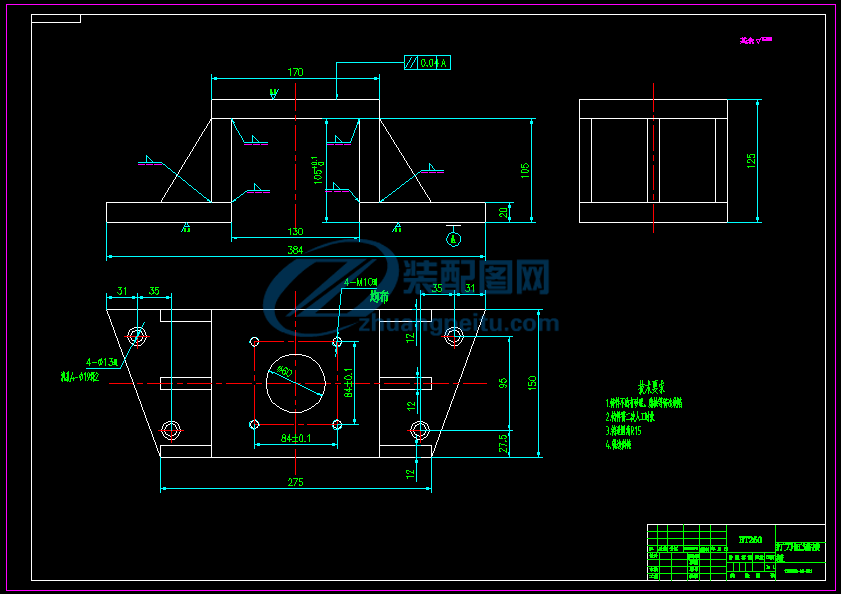
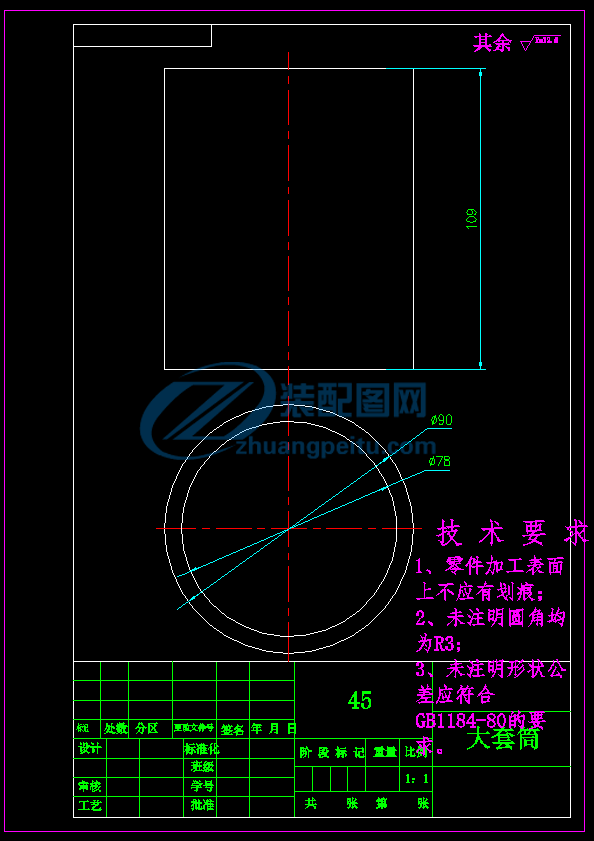
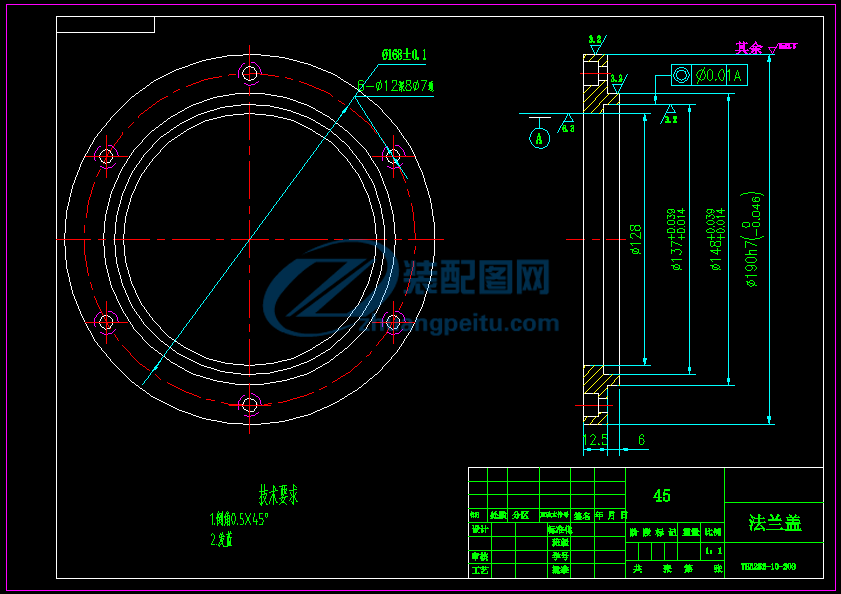
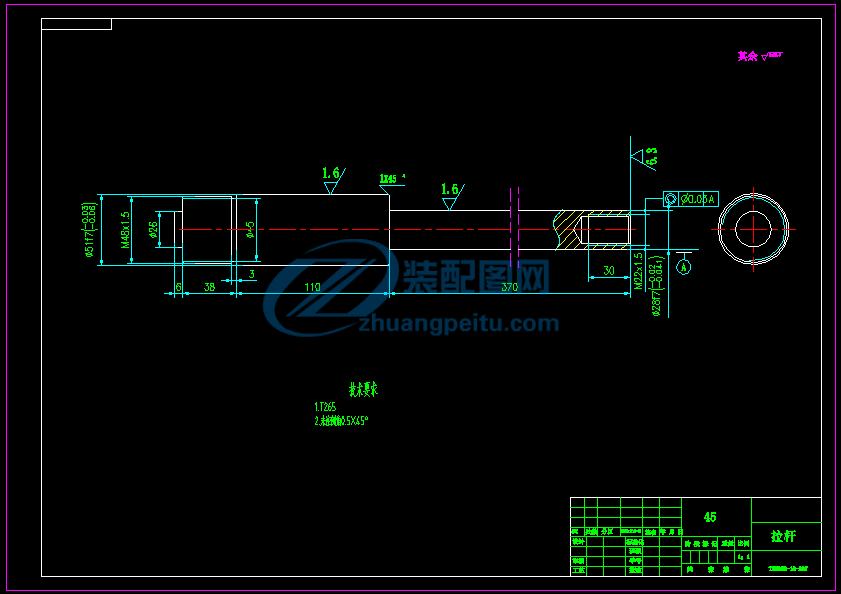
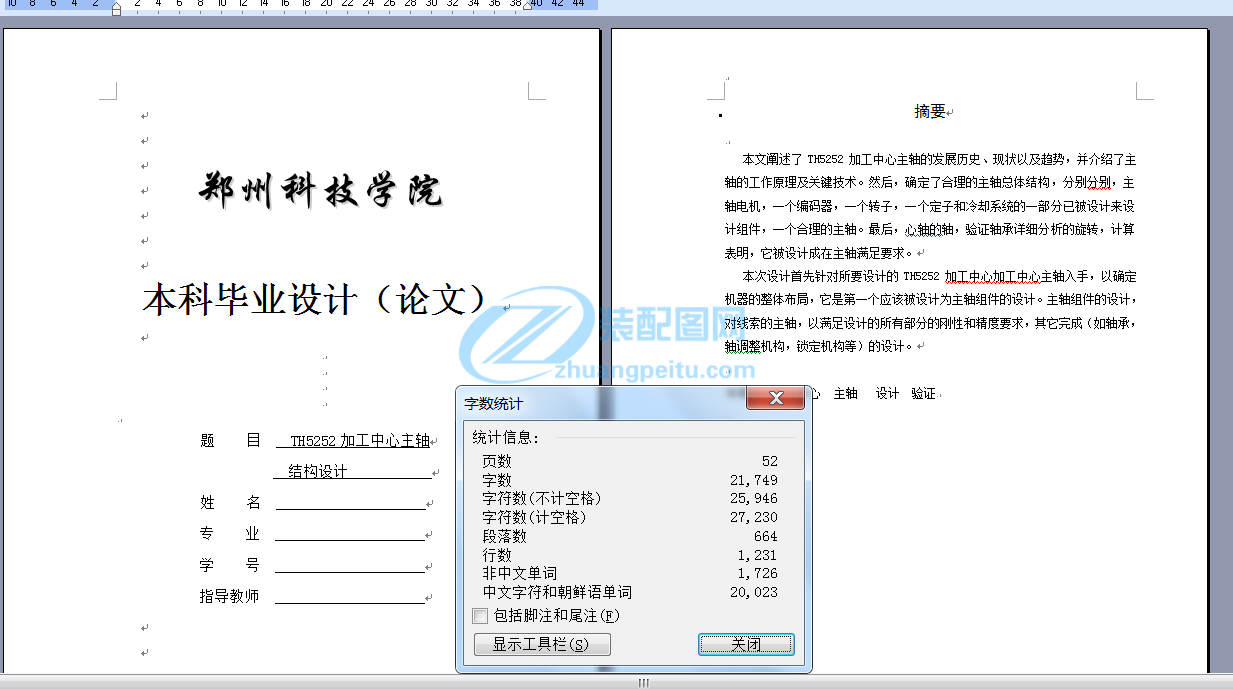
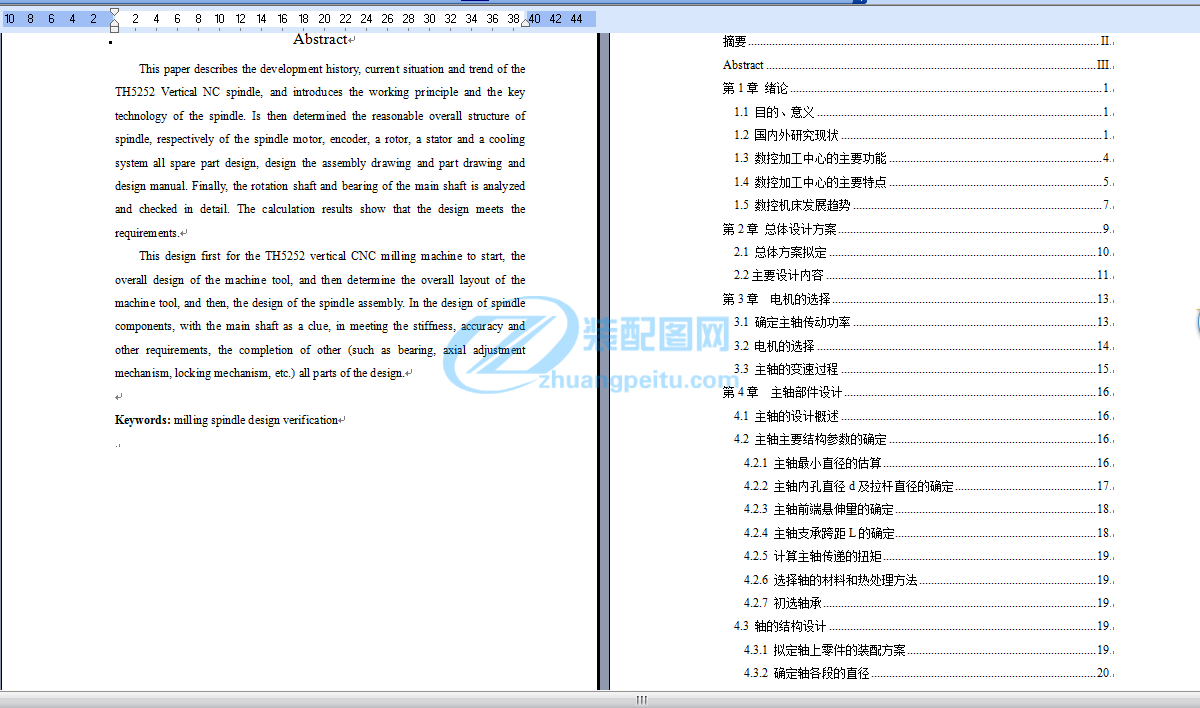
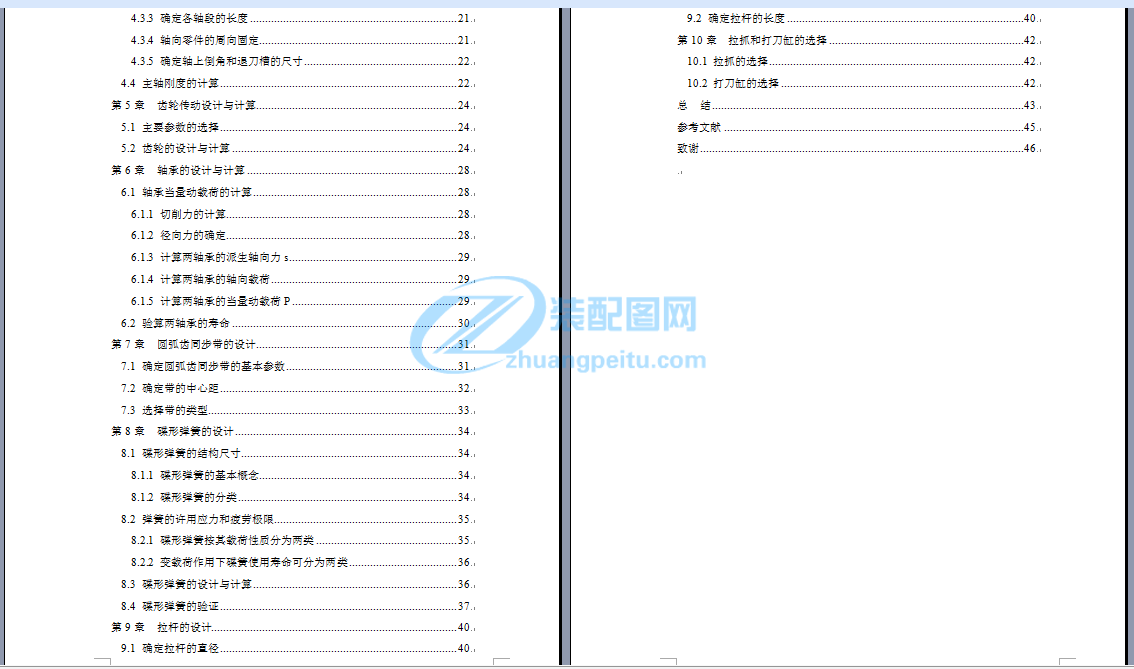
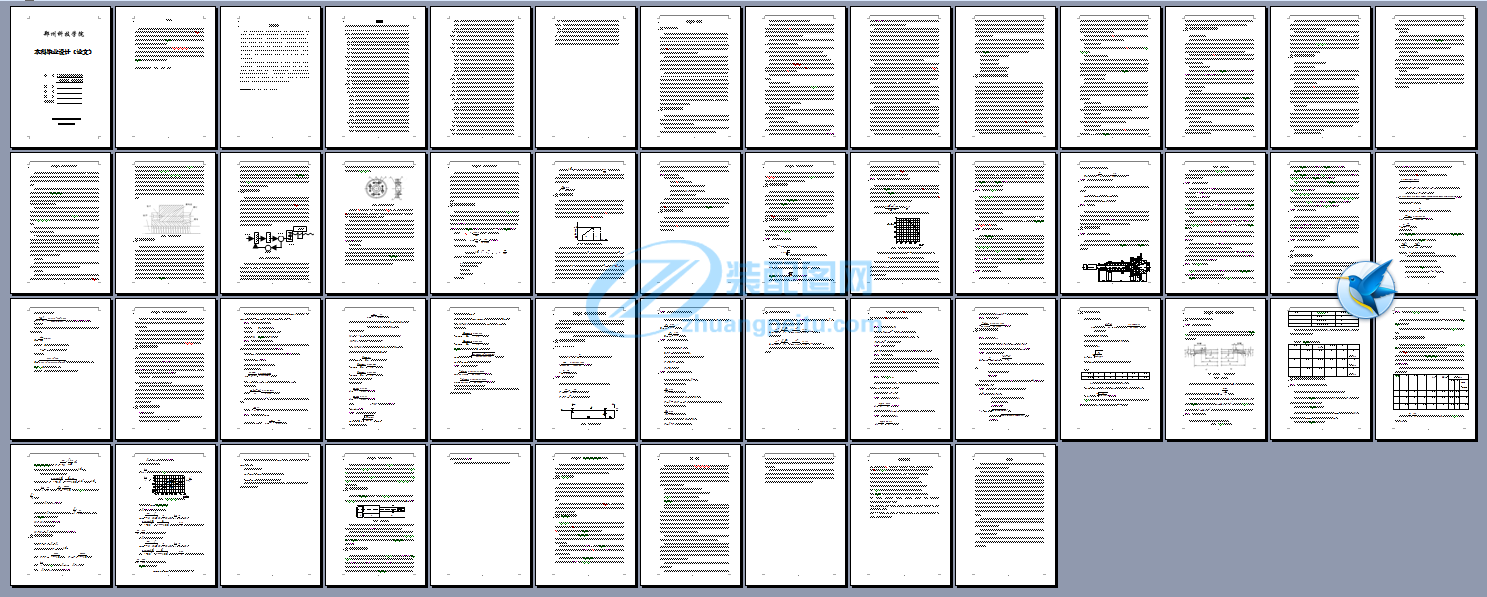
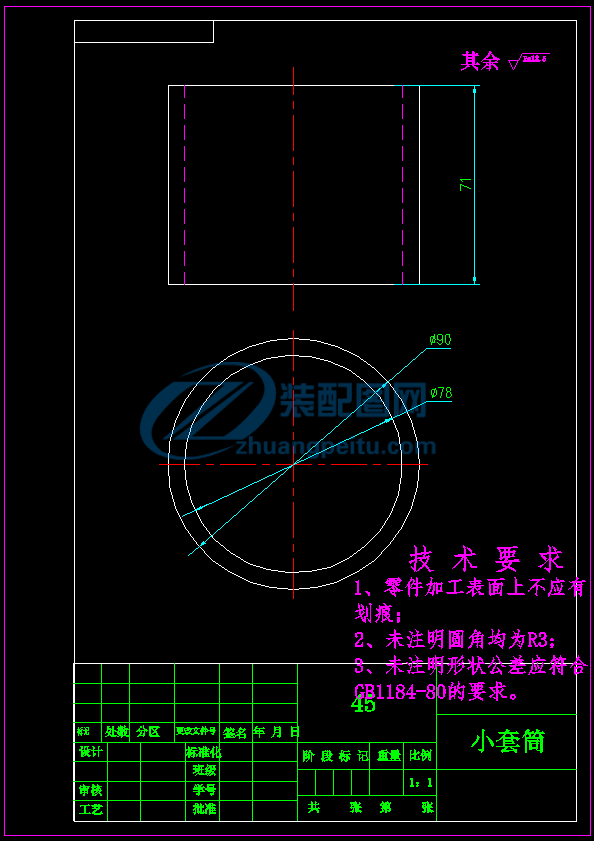
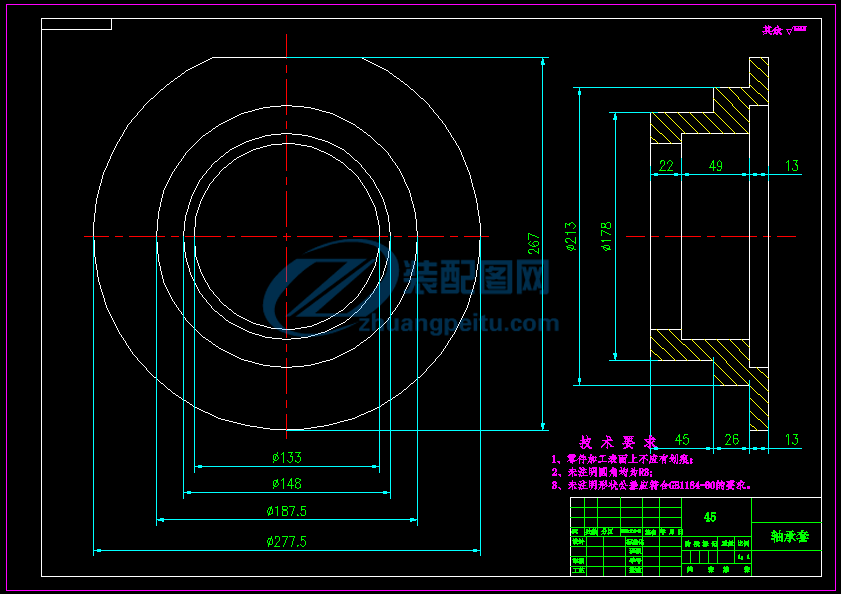

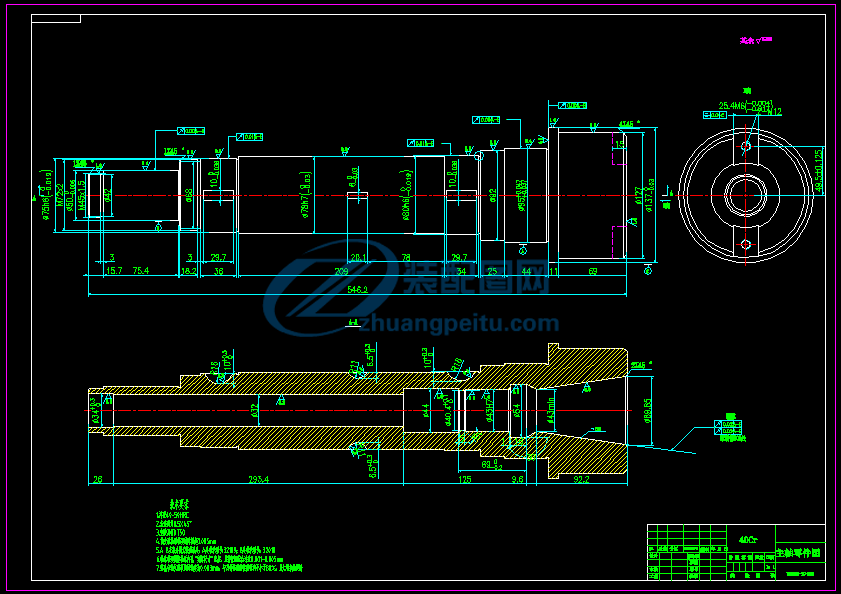
附表 5:鄭州科技學院畢業(yè)設計(論文)任務書題目 TH5252 加工中心主軸結(jié)構(gòu)設計 專業(yè) 學號 姓名 主要內(nèi)容、基本要求、主要參考資料等:1.主要內(nèi)容1)完成 TH5252 加工中心主軸結(jié)構(gòu)的設計:機械的尺寸設計,機械的主要零件、組成部分的設計2)機械結(jié)構(gòu)動力學分析:機械的運動學參數(shù)的確定,清掃機構(gòu)原理及結(jié)構(gòu)的分析3)機械總裝配圖一張和一些零件圖。4)編寫設計說明書、使用說明書,寫出文獻綜述,翻譯外文資料。2、基本要求設計出滿足要求的 TH5252 加工中心主軸結(jié)構(gòu),并完成其裝配圖與部分零件圖,查閱文獻資料不少于 15 篇,其中外文資料不少于 2 篇。1)文獻綜述一篇,不少于 3000 字,與專業(yè)相關的英文翻譯一篇,不少于3000 漢字。2)畢業(yè)設計說明書一份,內(nèi)容與字數(shù)都不少于規(guī)定的任務量。3)圖紙若干(折合后不少于 A0 圖紙 3 張,可以用計算機繪圖) 。4)包含本次設計的所有內(nèi)容的光盤一張。3、參考資料[1]成大先.機械設計手冊. 北京:化學工業(yè)出版社,2004.[2]鄧文英主編.金屬工藝學. 北京:高等教育出版社,2000.[3]戴志榮主編.工程材料及機械基礎. 北京:高等教育出版社,1992.[4]吳宗澤主編.機械結(jié)構(gòu)設計. 北京:機械工業(yè)出版社,1998.[5]盛曉敏,鄧朝輝主編. 先進制造技術. 北京:機械工業(yè)出版社,2000.完 成 期 限: 指 導 教 師 簽 名 : 專業(yè)負責人簽名: 填 表 日 期: 本科畢業(yè)設計(論文)題 目 _ TH5252 加工中心主軸結(jié)構(gòu)設計 _________姓 名 專 業(yè) 學 號 指導教師 鄭州科技學院電氣工程學院二○一六年四月II摘要本文闡述了 TH5252 加工中心主軸的發(fā)展歷史、現(xiàn)狀以及趨勢,并介紹了主軸的工作原理及關鍵技術。然后,確定了合理的主軸總體結(jié)構(gòu),分別對主軸的電機、編碼器、轉(zhuǎn)子、定子和冷卻系統(tǒng)等各零部件進行了設計,設計了裝配圖、零件圖與設計說明書等。最后,對主軸的旋轉(zhuǎn)軸和軸承進行了詳細的分析和校核,計算表明,該主軸設計符合要求。本次設計首先針對所要設計的 TH5252 加工中心加工中心主軸入手,對機床進行總體方案設計,進而確定機床的總體布局,隨后,對主軸組件進行設計。在設計主軸組件時,以主軸為線索,在滿足剛度、精度等要求下,完成其它(如軸承、軸向調(diào)節(jié)機構(gòu)、鎖緊機構(gòu)等)所有零件的設計。關鍵詞:加工中心 主軸 設計 校核IIIAbstractThis paper describes the development history, current situation and trend of the TH5252 Vertical NC spindle, and introduces the working principle and the key technology of the spindle. Is then determined the reasonable overall structure of spindle, respectively of the spindle motor, encoder, a rotor, a stator and a cooling system all spare part design, design the assembly drawing and part drawing and design manual. Finally, the rotation shaft and bearing of the main shaft is analyzed and checked in detail. The calculation results show that the design meets the requirements.This design first for the TH5252 vertical CNC milling machine to start, the overall design of the machine tool, and then determine the overall layout of the machine tool, and then, the design of the spindle assembly. In the design of spindle components, with the main shaft as a clue, in meeting the stiffness, accuracy and other requirements, the completion of other (such as bearing, axial adjustment mechanism, locking mechanism, etc.) all parts of the design.Keywords: milling spindle design verificationIV目錄摘要 .IIAbstract.III第 1 章 緒論 11.1 目的、意義 11.2 國內(nèi)外研究現(xiàn)狀 11.3 數(shù)控加工中心的主要功能 41.4 數(shù)控加工中心的主要特點 51.5 數(shù)控機床發(fā)展趨勢 7第 2 章 總體設計方案 92.1 總體方案擬定 102.2 主要設計內(nèi)容 .11第 3 章 電機的選擇 133.1 確定主軸傳動功率 133.2 電機的選擇 143.3 主軸的變速過程 15第 4 章 主軸部件設計 164.1 主軸的設計概述 164.2 主軸主要結(jié)構(gòu)參數(shù)的確定 164.2.1 主軸最小直徑的估算 .164.2.2 主軸內(nèi)孔直徑 d 及拉桿直徑的確定 .174.2.3 主軸前端懸伸量的確定 .184.2.4 主軸支承跨距 L 的確定 .184.2.5 計算主軸傳遞的扭矩 .194.2.6 選擇軸的材料和熱處理方法 .194.2.7 初選軸承 .194.3 軸的結(jié)構(gòu)設計 194.3.1 擬定軸上零件的裝配方案 .194.3.2 確定軸各段的直徑 .20V4.3.3 確定各軸段的長度 .214.3.4 軸向零件的周向固定 .214.3.5 確定軸上倒角和退刀槽的尺寸 .224.4 主軸剛度的計算 22第 5 章 齒輪傳動設計與計算 245.1 主要參數(shù)的選擇 245.2 齒輪的設計與計算 24第 6 章 軸承的設計與計算 286.1 軸承當量動載荷的計算 286.1.1 切削力的計算 .286.1.2 徑向力的確定 .286.1.3 計算兩軸承的派生軸向力 s.296.1.4 計算兩軸承的軸向載荷 .296.1.5 計算兩軸承的當量動載荷 P296.2 驗算兩軸承的壽命 30第 7 章 圓弧齒同步帶的設計 317.1 確定圓弧齒同步帶的基本參數(shù) 317.2 確定帶的中心距 327.3 選擇帶的類型 33第 8 章 碟形彈簧的設計 348.1 碟形彈簧的結(jié)構(gòu)尺寸 348.1.1 碟形彈簧的基本概念 .348.1.2 碟形彈簧的分類 .348.2 彈簧的許用應力和疲勞極限 358.2.1 碟形彈簧按其載荷性質(zhì)分為兩類 .358.2.2 變載荷作用下碟簧使用壽命可分為兩類 .368.3 碟形彈簧的設計與計算 368.4 碟形彈簧的校核 37第 9 章 拉桿的設計 409.1 確定拉桿的直徑 40VI9.2 確定拉桿的長度 40第 10 章 拉抓和打刀缸的選擇 4210.1 拉抓的選擇 4210.2 打刀缸的選擇 42總 結(jié) 43參考文獻 45致謝 46TH5252 加工中心主軸結(jié)構(gòu)設計1第 1 章 緒論1.1 目的、意義 數(shù)控技術水平的高低已成為衡量一個國家制造業(yè)現(xiàn)代化程度的核心標志,他實現(xiàn)加工機床及生產(chǎn)過程數(shù)控化,已成為當今制造業(yè)的發(fā)展方向。數(shù)控加工中心是一種加工功能很強的數(shù)控機床,目前迅速發(fā)展起來的加工中心、柔性加工單元都是在數(shù)控加工中心、數(shù)控鏜床的基礎上產(chǎn)生的,兩者都離不開銑削方式。由于數(shù)控銑削工藝最復雜,需要解決的技術問題也最多,因此人們在研究和開發(fā)數(shù)控系統(tǒng)及自動編程語言的軟件時,也一直把銑削加工作為重點。機械工業(yè)肩負著為國民經(jīng)濟各部門提供先進技術裝備的任務,而機床工業(yè)是機械工業(yè)的重要組成部分,是為機械工業(yè)提供先進制造技術和裝備的工業(yè)。機床擁有量、產(chǎn)量、品種和質(zhì)量、是衡量一個國家工業(yè)水平的重要標志之一。因此,機床在國民經(jīng)濟中占有極其重要的地位。與普通機床不同,數(shù)控機床加工零件的過程完全自動的進行,加工過程中人工不能干預。因此,首先必須將所加工的件的全部信息,包括工藝過程、刀具運動軌跡及走刀方向、位移量、工藝參數(shù)(主軸轉(zhuǎn)速、進給量、切屑深度)以及輔助動作(換刀、變速、冷卻、夾緊、松開)等,按加工順序采用標準或規(guī)定的程序指令編寫出正確的數(shù)控加工程序,然后輸入到數(shù)控設備的控制系統(tǒng)中,隨后控制系統(tǒng)按數(shù)控程序的要求控制數(shù)控機床對零件進行加工。所謂的數(shù)控編程,一般指包括零件圖樣分析、工藝分析與設計、圖形數(shù)學處理、編寫輸入程序清單、程序校驗的全部工作過程。數(shù)控編程可分為手工編程和全自動編程兩種方式。1.2 國內(nèi)外研究現(xiàn)狀建國 60 年來,在黨和國家領導人的關懷下,中國機床工業(yè)歷經(jīng)幾代人的拼搏,從無到有,從小到大,發(fā)生了天翻地覆的變化,如今發(fā)展成為產(chǎn)品布局合理,門類齊全,具有較大經(jīng)濟規(guī)模和較強技術實力的產(chǎn)業(yè)。中國機床工具行業(yè)已開始走出國門與國際市場競爭,在國際上有了舉足輕重的話語權(quán)和產(chǎn)業(yè)地位,正在向世界機床工具制造強國的目標邁進。TH5252 加工中心主軸結(jié)構(gòu)設計2機床是一切機械工業(yè)的基礎裝備,被稱之為“工作母機” 。中國機床工具行業(yè)一直在當合國家領導人的關懷中不斷發(fā)展壯大。如今,中國數(shù)控機床的品種已達到 2000 余中種。通過突破國外多年的技術封鎖,相繼開發(fā)出具有自主知識產(chǎn)權(quán)的各類數(shù)控機床,特別是研制出一批國際上首臺重型數(shù)控機床,滿足了國家重點工程的需要。一是成功研發(fā)了一大批多種類型,多種規(guī)格多坐標,智能,帶刀庫,帶A,B 軸五軸聯(lián)動的立式,臥式復合機床。二是成功研發(fā)了一大批大規(guī)格,大尺寸,大噸位多品種的重型,超重型機床,其中許多是世界首臺最大規(guī)格的數(shù)控機床。三是研發(fā)成功一大批高精,高速,高效的各類機床。四是功能部件,數(shù)控系統(tǒng),刃量具等方面產(chǎn)品研發(fā)。我國的機床工業(yè)在新中國成立后建立起來的,解放后 50 年來,我國機床工業(yè)獲得了高速發(fā)展,我國已制定了完整的機床系列,機床品種日趨齊全,能生產(chǎn)上千個品種。數(shù)控加工中心從結(jié)構(gòu)上可分為立式、臥式及立臥兩用三種。(1)立式數(shù)控加工中心立式數(shù)控加工中心主軸軸線垂直于水平面,這種加工中心占數(shù)控加工中心的大多數(shù),應用范圍也最廣。目前三坐標數(shù)控立銑占數(shù)控加工中心的大多數(shù),一般可進行三坐標聯(lián)動加工,也可以實行兩軸半控制,即在 X、Y 、Z 三個坐標軸中,任意兩軸都可以聯(lián)動。一般用來加工平面曲線的輪廓。但也可加一個回轉(zhuǎn)坐標,用來加工螺旋槽、葉片等立體曲面零件。(2)臥式數(shù)控加工中心臥式數(shù)控加工中心主軸的軸線平行于水平面。為了擴大加工范圍和擴充功能,臥式數(shù)控加工中心通常采用增加數(shù)控轉(zhuǎn)盤(或萬能數(shù)控轉(zhuǎn)盤)來實現(xiàn)四坐標、五坐標加工。(3)立臥兩用數(shù)控加工中心這類加工中心可在一臺機床上進行立式加工或臥式加工,同時具備立、臥式加工中心的功能。它的使用范圍更廣,功能更全。一般數(shù)控加工中心上指規(guī)格較小的升降臺式數(shù)控加工中心,其工作臺寬度多在 400mm 以下,規(guī)格較大的數(shù)控加工中心(工作臺寬度多在 500mm 以上) ,TH5252 加工中心主軸結(jié)構(gòu)設計3其功能已向加工中心靠近,進而演變成柔性制造單元。東歐這些國家的機床生產(chǎn)品種不全,配套件缺乏,而中國機床工業(yè)經(jīng)過這么多年的發(fā)展,已具備相當規(guī)模,產(chǎn)品門類齊全,數(shù)控機床的品種從幾百種發(fā)展到近倆千種,全行業(yè)開發(fā)出一批市場急需的新產(chǎn)品,填補了國內(nèi)空白。一批高精,高速,高效,一批多坐標,復合,智能型的數(shù)控機床新產(chǎn)品滿足了國家重點用戶需求。面前中國機床工業(yè)正在通過調(diào)整產(chǎn)業(yè)結(jié)構(gòu),產(chǎn)品結(jié)構(gòu),提高自主創(chuàng)新能力。以精密、柔性、成套、綠色需求為方向,以改革、改進、改組、設計為動力。購并國際名牌企業(yè)和產(chǎn)品,努力提高國產(chǎn)機床占有率。不斷提高國產(chǎn)機床市場占有率,不斷拓寬機床工具產(chǎn)品的發(fā)展空間。日本、美國、英國、德國、法國、意大利等六國1989年金屬切削機床的總產(chǎn)值與1980年比,僅增加54%,但同期數(shù)控機床的產(chǎn)值比1980年刪增加了256%。 1990年,日本數(shù)控機床的年產(chǎn)量已達61697臺,年產(chǎn)量的數(shù)控化率為31.8%,年產(chǎn)值的數(shù)控化率為76%。其他五國的年產(chǎn)量數(shù)控化率均在20%以上,年產(chǎn)值數(shù)控化率均在50%以上。上述六國擁有量數(shù)控化率在10%以上。1994年日本擁有量的數(shù)控化率為20.8%。工業(yè)發(fā)達國家的機床廠均生產(chǎn)數(shù)控機床,普通機床已逐步甩給第三世界營家去生產(chǎn)。在數(shù)控機床的生產(chǎn)中,生產(chǎn)最多的仍然是普通數(shù)控機床,特別是數(shù)控車床,但發(fā)展最快的則是可以自動換刀的加工中心。在近幾年的國際機床展覽會上,展品均以加工中心及由加工中心為主體的柔性加工單元及柔性制造系統(tǒng)為主。現(xiàn)在,日本、箍國、美國等三國生產(chǎn)的數(shù)控系統(tǒng)約占國際市場的三分之二。發(fā)展高端數(shù)控機床是本輪產(chǎn)業(yè)升級的必經(jīng)之路。隨著國內(nèi)勞動力成本上漲,環(huán)境減排的迫切需求,以及對人民幣長期升值,國內(nèi)需求不足的狀況。這將促使中國制造業(yè)得新一輪的產(chǎn)業(yè)升級必須將是高端制造業(yè)代替簡單制造業(yè),技術密集型代替勞動密集型。這種轉(zhuǎn)型將大大減少簡單機械的需求,增加更加高效、更加精確的數(shù)控機床需求。政府加大投資的領域包括以高速客運專線為主的鐵路建設,航空制造業(yè)尤其對高端數(shù)控機床提出了更高的要求。作為制造業(yè)母機的機床行業(yè),是產(chǎn)品升級的必經(jīng)之路。中國數(shù)控機床行業(yè)發(fā)展正當其時。中國機床出口盡管比例不高,總金額比較少,但增長速度遠高于進口產(chǎn)品增速。目前中國國產(chǎn)數(shù)控機床技術水平正在TH5252 加工中心主軸結(jié)構(gòu)設計4提高,在部分領域已經(jīng)能夠替代進口,占據(jù)國內(nèi)高端數(shù)控機床主要市場的進口產(chǎn)品即將面臨國產(chǎn)產(chǎn)品的沖擊。未來高端數(shù)控機床對進口產(chǎn)品的替代潛力巨大。面對外出口的市場現(xiàn)在還處于萌芽期,未來發(fā)展?jié)摿薮?。中國機械工業(yè)戰(zhàn)略定位為;從機械產(chǎn)品生產(chǎn)大國變成以市場競爭力為標志的機械工業(yè)強國;從機械設備進口大國變成產(chǎn)品貿(mào)易大國;從側(cè)重于出口為導向生產(chǎn)轉(zhuǎn)為向生產(chǎn)和消費雙重領域拓展。組織機構(gòu)由“過來橄欖型”向“啞鈴型”轉(zhuǎn)變。建立以大代小,以小保大的組織體系。1、 進一步加快機床產(chǎn)業(yè)機構(gòu)調(diào)整2、 進一步完善產(chǎn)業(yè)鏈3、 實施企業(yè)機構(gòu)調(diào)整4、 提高制造工業(yè)專業(yè)化生產(chǎn)水平5、 調(diào)整行業(yè)進出口貿(mào)易結(jié)構(gòu)1.3 數(shù)控加工中心的主要功能近年來,隨著計算機技術的發(fā)展,數(shù)字控制技術已經(jīng)廣泛應用于工業(yè)控制的各個領域,尤其是機械制造業(yè)中,普通機械正逐漸被高效率、高精度、高自動化的數(shù)控機械所代替。目前國外機械設備的數(shù)控化率已達到 85%以上,而我國的機械設備的數(shù)控化率不足 20%,隨著我國機制行業(yè)新技術的應用,數(shù)控技術的應用不但給傳統(tǒng)制造業(yè)帶來了革命性的變化,使制造業(yè)成為工業(yè)化的象征,而且隨著數(shù)控技術的不斷發(fā)展和應用領域的擴大,他對國計民生的一些重要行業(yè)(汽銑、輕工、醫(yī)療等)的發(fā)展起著越來越重要的作用,因為這些行業(yè)所需裝備的數(shù)字化已是現(xiàn)代發(fā)展的大趨勢。從目前世界上數(shù)控技術及其裝備發(fā)展的趨勢來看,其主要研究熱點有以下幾個方面。1.高速、高精加工技術及裝備的新趨勢 2.軸聯(lián)動加工和復合加工機床快速發(fā)展 3.智能化、開放式、網(wǎng)絡化成為當代數(shù)控系統(tǒng)發(fā)展的主要趨勢 4.重視新技術標準、規(guī)范的建立其中包括:a.關于數(shù)控系統(tǒng)設計開發(fā)規(guī)范 b. 關于數(shù)控系統(tǒng)設計開發(fā)規(guī)范,加強數(shù)控加工中心的整機設計中應該把握的主要問題的訓練。6、 研究此課題的意義在于:針對大學畢業(yè)生技能的需求,在培養(yǎng)過程中,加強實踐環(huán)節(jié),把自己置身于工程背景之中,以提高我們的專業(yè)水平。通過此設計,我們可以初步掌握設計一般加工中心的方法與步驟,可TH5252 加工中心主軸結(jié)構(gòu)設計5為我們今后工作打下良好的基礎。將大學三年所學到的知識進行匯總,考核我們所學知識的牢固度,檢驗我們運用知識的能力。7、 數(shù)控加工中心可以分為立式、臥式和立臥兩用式數(shù)控加工中心,數(shù)控加工中心的應用越來越廣泛,主要具有下列功能:8、 點位控制功能 利用這一功能,數(shù)控加工中心可以進行只需要作點位控制的磚孔、擴孔、忽孔、鉸孔和鏜孔等加工。9、 連續(xù)輪廓控制功能 數(shù)控加工中心通過直線和圓弧插補,可以實現(xiàn)對刀具運動軌跡的連續(xù)輪廓控制,加工出由直線和圓弧兩種幾何要素構(gòu)成的平面輪廓工件。對非圓曲線(橢圓、拋物線、雙曲線等二次曲線及對數(shù)螺旋線、阿基米德螺旋線和列表曲線等)構(gòu)成的平面輪廓,在經(jīng)過直線或圓弧逼近后也可以加工。除此之外,還可以加工一些空間曲面。10、刀具半徑自動補償功能 使用這一功能,在編程時可以很方便地按工件實際輪廓形狀和尺寸進行編程計算,而加工中可以使刀具中心自動偏離工件輪廓一個刀具半徑,加工出符合要求的輪廓表面。也可以利用該功能,通過改變刀具半徑補償量的方法來彌補銑刀制造的尺寸精度誤差,擴大刀具直徑選用范圍及刀具返修刃磨的允許誤差。11、刀具長度補償功能 利用該功能可以自動改變切削平面高度,同時可以降低在制造與返修時對刀具長度尺寸的精度要求,還可彌補軸向?qū)Φ墩`差。5、鏡像加工功能 鏡像加工也稱為軸對稱加工。對于一個軸對稱形狀的工件來說,利用這一功能,只要編出一半形狀的加工程序就可完成全部加工了。6、固定循環(huán)功能 利用數(shù)控加工中心對空進行鉆、擴、鉸、鍃和鏜加工時,加工的基本動作是:刀具無切削快速到達孔位—慢速切削進給—快速退回。對于這種典型化動作,可以專門設計一段程序(子程序)在需要的時候進行掉用來實現(xiàn)上述加工循環(huán),特別是在加工許多相同的孔時,應用固定循環(huán)功能可以大大簡化程序。TH5252 加工中心主軸結(jié)構(gòu)設計61.4 數(shù)控加工中心的主要特點1、高柔性及工序復合化數(shù)控加工中心具有柔性(可變性)高和工序復合化的特點。所謂“柔性”即靈活、通用和萬能性,可以適應加工不同形狀工件的自動化機床。數(shù)控加工中心的發(fā)展已經(jīng)模糊了粗、精加工工序的概念,打破了傳統(tǒng)的工序界限和分開加工的工藝規(guī)程,可最大限度地提高設備利用率。數(shù)控加工中心一般都能完成鉆孔、鏜孔、鉸孔、銑平面、銑斜面、銑槽、銑曲面(凸輪) 、攻螺紋等加工。而且,一般情況下,可以在一次裝夾中,完成所需的加工工序。2、加工精度提高目前數(shù)控裝置的脈沖當量(即每發(fā)出一個脈沖后滑板的移動量)一般為0.001mm。高精度的數(shù)控系統(tǒng)可達 0.0001mm,一般情況下可以保證工件的加工精度。另外,數(shù)控加工可避免工人的操作誤差,一批加工工件的尺寸同一性比較好(包括工件的主要尺寸和倒角等尺寸的同一性) ,而且還可以利用軟件進行精度校正和補償,大大提高了產(chǎn)品質(zhì)量。3、生產(chǎn)效率高零件加工所需要的時間包括機動時間和輔助時間量部分。數(shù)控加工中心能夠有效的減少這量部分時間,因而加工生產(chǎn)率比一般加工中心高得多。良好的結(jié)構(gòu)剛性允許數(shù)控加工中心大切削用量的強力切削,有效的節(jié)省了機動時間。數(shù)控加工中心移動部件的快速移動和定位采用了加速和減速措施,因而選用了很高的空行程運動速度,消耗在快進、快退和定位的時間要比一般加工中心少的多。數(shù)控加工中心的主軸轉(zhuǎn)速和進給量都是無級變速的。因此,有利于選擇最佳切削用量。4、減輕操作者的勞動強度數(shù)控加工中心對零件加工是按事先編好的程序自動完成的。操作者除了操作鍵盤、裝卸工件和中間測量及觀察機床運動外,不需要進行繁重的重復性手工操作,可大大減輕勞動強度。由于數(shù)控加工中心具有以上獨特的優(yōu)點,因此數(shù)控加工中心已成為機械制TH5252 加工中心主軸結(jié)構(gòu)設計7造業(yè)的主要設備。但是,數(shù)控加工中心的編程操作比較復雜,對編程人員的素質(zhì)要求較高。否則很難發(fā)揮數(shù)控加工中心的作用。本文根據(jù)公司生產(chǎn)加工需要改裝一臺加工中心,主要用于銑削平面和鉆孔,對主軸部件進行重新設計,但仍要用原來的主軸箱,要求主軸的轉(zhuǎn)速范圍為40r/min—4000r/min,查機械設計手冊確定典型的切削工藝可以求得主軸的切削功率為 5.4KW,根據(jù)切削功率 與主運動傳動鏈的總效率 η 確定機床傳動pc的功率P,然后,根據(jù)機床傳遞的功率P來選擇電機的類型。為了滿足主軸的轉(zhuǎn)速要求,選擇合適的傳動比和軸承。1.5 數(shù)控機床發(fā)展趨勢1. 高速、高效、高精度、高可靠性(1) 高速、高效加工進入 21 世紀,機床向高速化方向發(fā)展:大幅度提高加工效率、降低加工成本,提高零件的表面加工質(zhì)量和精度.上世紀 90 年代以來歐、美、日各國爭相開發(fā)應用新一代高速數(shù)控機床,加快機床高速化發(fā)展步伐。(2)高精度、超精密化加工當前,機械加工高精度的要求較普通的加工精度提高了一倍.達到 5 微米;精密加工精度提高了兩個數(shù)量級,超精密加工精度進入納米級(0.001 微米),主軸回轉(zhuǎn)精度要求達到 0.01-0.05 微米,加工圓度為 0.1 微米加工表面粗糙度Ra0.003 微米等從精密加工發(fā)展到超精密加工〔特高精度加工),是世界各工業(yè)強國致力發(fā)展的方向。其精度從微米級到亞微米級,乃至納米級(10nm).其應用范圍日趨廣泛(3)高可靠性是指數(shù)控系統(tǒng)的可靠性要高于被控設備的可靠性在一個數(shù)量級以上,但也不是可靠性越高越好,仍然是適度可靠對于每天工作兩班的無人工廠而言,如果要求在 16 小時內(nèi)連續(xù)正常工作,無故障率 P(t)=99%以上的話,則數(shù)控機床的平均無故障運行時間 MTBF 就必須大于 3000 小時.當前國外數(shù)控裝置的 MIBF值已達 60000 小時以上,驅(qū)動裝置達 30000 小時以上.2. 模塊化、智能化、柔性化和集成化TH5252 加工中心主軸結(jié)構(gòu)設計8(1)模塊化、專門化與個性化為了適應數(shù)控機床多品種、小批量的特點.機床結(jié)構(gòu)模塊化,數(shù)控功能專門化,機床性能價格比顯著提高并加快優(yōu)化。個性化是近幾午來特別明顯的發(fā)展趨勢.(2)智能化在數(shù)控系統(tǒng)中智能化的內(nèi)容包括①為追求加工效率和加工質(zhì)量方面的智能化:如自適應控制,工藝參數(shù)自動生成:②為提高驅(qū)動性能及使用連接方便方面的智能化,如前饋控制、電機參數(shù)的自適應運算等:③簡化編程、簡化操作方面的智能化:④智能診斷、智能監(jiān)控方面的內(nèi)容等。(3)柔性化和集成化數(shù)控機床向柔性自動化系統(tǒng)發(fā)展的趨勢是從點(數(shù)控單機、加工中心和數(shù)控復合加工機床) 、線(FMC 、FMS F、TL F、ML)向面(工段車間獨立制造島、工廠自動化 FA)、體(CIMS,分布式網(wǎng)絡集成制造系統(tǒng))的方向發(fā)展,另一方面向注重應用性和經(jīng)濟性方向發(fā)展.3. 開放性為適應數(shù)控進線、聯(lián)網(wǎng)、普及型個性化、多品種、柔性化及數(shù)控迅速發(fā)展的耍求,最重耍的發(fā)展趨勢是體系結(jié)構(gòu)的開放性,設計生產(chǎn)開放式的數(shù)控系統(tǒng),例如美國的 OMAC,歐共體的 OSACA 及日本的 OSEC 發(fā)展開觸式數(shù)控的計劃等。TH5252 加工中心主軸結(jié)構(gòu)設計9第 2 章 總體設計方案TH5252 加工中心加工中心要達到的技術要求:主軸轉(zhuǎn)速 40 r/min~4000r/min,換刀時間 0.6s,換刀的時間靠打刀缸的性能來保證。工作臺的行程 1000×500,工作臺所加工零件的類型為鋁件和一些鋼件。主軸采用BT50、的刀柄和拉抓。TH5252 加工中心加工中心具有加工中心的特點,能夠?qū)崿F(xiàn)自動換刀,自動變速,變速方法采用無級變速加有級變速。無級變速采用交流變頻調(diào)速電機,實現(xiàn)兩極變速,變速過程中齒輪的嚙合通過離合器的得電和失電來實現(xiàn)。為了滿足主軸的轉(zhuǎn)速要求選擇帶輪的傳動比為 2,減速傳動;齒輪的傳動比為1.78,兩對齒輪嚙合,一對齒輪實現(xiàn)增速傳動,另一對實現(xiàn)減速傳動。TH5252 加工中心加工中心主軸部件的設計主要有軸以及軸上零件、拉桿的設計,選擇合適的電機,滿足切削時的功率要求,選擇電機時根據(jù)典型切削工藝求得切削是需要的功率;打刀缸的選擇,首先根據(jù)換刀所要達到的時間,其次,根據(jù)碟形彈簧拉緊刀柄的力,打刀缸動作是所產(chǎn)生的力應稍大于彈簧的拉緊力。機械部分數(shù)控化設計需涉及電機的選擇、工作臺進給結(jié)構(gòu)、傳動比分配與計算等方面的內(nèi)容。1 伺服驅(qū)動元件 進給電機選用混合式步進電機,其不僅步距角小運行頻率高且功耗低低頻噪音小等優(yōu)點。廣泛用于開環(huán)控制系統(tǒng),不需要反饋裝置,結(jié)構(gòu)簡單可靠,壽命長。橫縱向進給電機均選用同一型號以便于設計和日后維修。脈沖當量 t=0.01mm/脈沖,選用步距角 θ=0.6° 。對原機床的主傳動系統(tǒng)均維持不變,以節(jié)約資金及縮短改裝時間。2 機床導軌的選擇由于原機床采用滑動導軌,在低速時容易發(fā)生“爬行”現(xiàn)象,直接影響運動部件的定位精度。較經(jīng)濟的處理方法是采用貼塑滑動導軌。3 進給傳動系統(tǒng)數(shù)控機床要求進給部分移動元件靈敏度高、精度高、反應快、低速時無爬行。因此本設計中采用滾珠絲杠可以滿足要求。滾珠絲杠螺母副由絲杠、螺母、滾珠、反向器組成。其工作原理為:當絲杠和螺母相對運動時,在螺母上設有TH5252 加工中心主軸結(jié)構(gòu)設計10滾珠循環(huán)返回裝置,使得滾珠沿滾道面運動后能通過這個裝置自動的返回其入口處,繼續(xù)參加工作。滾珠絲杠螺母副安裝時需要預緊,通過預緊可消除滾珠絲杠螺母副的軸向間隙,提高傳動剛度。本設計中的預緊方法是采用雙螺母墊片預緊式結(jié)構(gòu)。即通過改變兩個螺母的軸向相對位置,使每個螺母中滾珠分別接觸絲杠滾道的左右兩側(cè)來實現(xiàn)預緊。其特點是預緊結(jié)構(gòu)簡單,軸向剛度好,預緊可靠,軸向尺寸適中,工藝性好如圖 2-1。為消除傳動系統(tǒng)中的反向間隙,提高重復定位精度,傳動元件連接采用無鍵錐環(huán)連接。圖 2-1 滾珠絲桿的結(jié)構(gòu)2.1 總體方案擬定數(shù)控加工中心的結(jié)構(gòu)設計要求: 在設計中應盡可能保留原機床結(jié)構(gòu)。主傳動系統(tǒng)中保留主軸箱內(nèi)滑移齒輪變速機構(gòu),取消原操作手柄,實現(xiàn)主軸的正反轉(zhuǎn)及停止,改由數(shù)控系統(tǒng)直接控制主電機,當數(shù)控系統(tǒng)發(fā)出 M03 指令后,主電機正轉(zhuǎn),通過傳動系統(tǒng)實現(xiàn)主軸正轉(zhuǎn)。縱、橫進給系統(tǒng)均采用交流伺服電動機。用滾珠絲杠螺母機構(gòu)代替普通的滑動絲杠螺母機構(gòu),具有摩擦力小,運動靈敏, 無爬行現(xiàn)象, 也可以進行預緊, 以實現(xiàn)無間隙傳動,傳動剛度好,反向時無空程死區(qū)等特點??商岣邆鲃泳取к壭柩赜迷瓩C床的導軌,但因起精度較低,不適合數(shù)控機床。因而在原導軌上粘接四氟乙烯軟帶,使其有良好的耐摩性和較小的摩擦阻力,能預防爬行并具有自潤滑性。將原刀架和小托板拆除,將加工中心刀架換為四工位電動刀架,將刀架調(diào)整好高度安裝在中拖板上,由數(shù)控系統(tǒng)直接控制,減少輔助時間,提高效率。為保證加工螺紋時縱向進給運TH5252 加工中心主軸結(jié)構(gòu)設計11動與主軸的回轉(zhuǎn)運動有嚴格的運動關系,需要在主軸尾部安裝主軸脈沖發(fā)生器。主軸脈沖發(fā)生器與主軸同步旋轉(zhuǎn),同時發(fā)出與主軸轉(zhuǎn)角相對應的脈沖信號,使數(shù)控系統(tǒng)控制刀架的縱向移動量。2.2 主要設計內(nèi)容因要求設計后的加工中心為經(jīng)濟型數(shù)控加工中心。所以在保證具有一定加工精度的前提下,從設計成本考慮。應簡化結(jié)構(gòu),降低成本??刹梢圆竭M電動機為驅(qū)動裝置的開環(huán)系統(tǒng),但是考慮到加工精度的要求,應采用以伺服電動機為驅(qū)動的半閉環(huán)伺服系統(tǒng)。半閉環(huán)系統(tǒng)的環(huán)路短,剛性好,較容易獲得較高的精度和速度,目前大多數(shù)數(shù)控機床都采用半閉環(huán)系統(tǒng),而隨著機電一體化技術的發(fā)展,伺服電動機生產(chǎn)廠家在生產(chǎn)中就把電機和檢測元件直接安裝在一起,形成成套的產(chǎn)品,極大的方便了用戶,省去了安裝調(diào)整誤差。 (半閉環(huán)控制系統(tǒng)如下圖 2-2 所示)減速箱齒輪傳動初定傳動比為 2,可取 Z1=24 則 Z2=48,齒寬 B=16.在設計齒輪傳動時,為了提高傳動精度,必須消除齒輪副的間隙。數(shù)控機床進給系統(tǒng)由于經(jīng)常處于變向狀態(tài),反向時如果驅(qū)動鏈中的齒輪等傳動副存在間隔,就會使進給運動的反向滯后于指令信號,從而影響其傳動精度,因此 24/48 這一對齒輪還必須采取措施消除齒輪傳動中的間隙,以提高數(shù)控機床進給系統(tǒng)的傳動精度。齒輪間隙的調(diào)整采用圓柱薄片齒輪可調(diào)拉簧錯齒法來實現(xiàn),其結(jié)構(gòu)如圖 2-3所示。檢測器執(zhí)行件伺服放大器 伺服電機減速箱脈沖指令 比較線路圖 2-2 半閉環(huán)控制系統(tǒng)原理圖TH5252 加工中心主軸結(jié)構(gòu)設計12圖中,在 2 個薄片齒輪 1 和 2 上裝有螺紋的凸耳 4 和 8 ,彈簧的一段鉤在凸耳 4 上,另一端鉤在螺釘 5 上。彈簧 3 所受的張力大小可用螺母 6 來調(diào)節(jié)螺釘 5 的伸出長度,調(diào)整好后再用螺母 7 鎖緊。在選擇伺服電機時應考慮以下幾點:a、慣量匹配,即 0.25≤Jd/Jm≥1, 其中 Jd 為折算到到電動機的負載慣量,Jm 為電動機轉(zhuǎn)動慣量。b、轉(zhuǎn)矩伺服電機的額定轉(zhuǎn)矩必須滿足實際需要,但是不需要留有過多的余量,因為一般情況下,其最大轉(zhuǎn)矩為額定轉(zhuǎn)矩的 3 倍。c、短時間特性(加減速轉(zhuǎn)矩),工作負載轉(zhuǎn)矩大于電動機加減速轉(zhuǎn)矩。根據(jù)以上原則,取電動機型號為 1FT5066-0A01△【2】3.導軌設計因原機床的導軌精度不能滿足數(shù)控機床的要求。但設計的原則是盡量保持原機床的部件。故只能將導軌加以利用。導軌表面貼塑的方法可使得導軌精度提高。因此可在導軌上加四氟乙烯軟帶。其特點是,摩擦系數(shù)低,運動平穩(wěn),可吸收震動,維修方便,損壞后更換容易。在本次設計中采用美國霞板公司研制的德爾賽塑料導軌軟帶。圖 2-3 齒輪間隙的調(diào)整結(jié)構(gòu)圖TH5252 加工中心主軸結(jié)構(gòu)設計13第 3 章 電機的選擇現(xiàn)在的數(shù)控加工中心能夠?qū)崿F(xiàn)無級變速或無級變速加有級變速,數(shù)控加工中心一般都采用由直流或交流調(diào)速電動機作為驅(qū)動的電氣無級調(diào)速。由于數(shù)控加工中心的運動調(diào)速范圍較大,單靠調(diào)速電機無法滿足這么大的調(diào)速范圍,另一方面調(diào)速電機的功率扭矩特性也難于直接與機床的功率和轉(zhuǎn)矩要求相匹配。因此,數(shù)控機床主傳動變速系統(tǒng)常常在無級變速電機之后串聯(lián)機械有級變速傳動,以滿足機床要求的調(diào)速范圍和轉(zhuǎn)矩特性。3.1 確定主軸傳動功率數(shù)控加工中心的加工范圍一般都比較大,所傳動的額定功率可以根據(jù)典型切削工藝的情況計算,根據(jù)設計的加工中心主要的加工范圍,查機床設計手冊確定如下典型加工工藝:用高速剛圓柱平刀銑削灰鑄鐵工件平面,刀具直徑D=100mm,刀齒數(shù)為 10,工件材料為 HT200,硬度 190HBS,切削速度=23.5m/min ,進給速度為 160mm/min,背吃刀量 =5mm,切寬為 75mm。v ap由公式 = 計算得 =1200r/minnDv?10n則每齒進給量 = = =0.013mmsz6120?根據(jù)典型切削工藝公式:P 切=2.8× · · ·B· · ·2?t9.0sz74. n190HB式中: t—切削厚度,即被吃刀量(mm)—每齒進給量(mm)szB—切削寬度(mm)Z—刀齒數(shù)HB—材料硬度代入數(shù)值得 P 切=2.8× ×5 ×0.013 ×75×10×1200× =4300W=4.3KW102?9.074.0190TH5252 加工中心主軸結(jié)構(gòu)設計14主傳動的總效率一般可取為 η=0.70~0.85,數(shù)控機床的主傳動多用調(diào)速電機和有限的機械變速傳動實現(xiàn),傳動鏈較短,因此效率可取較大值,由此可求得主軸傳遞的功率為P= = =5.4kw?p切 8.0343.2 電機的選擇現(xiàn)在數(shù)控機床常用直流電動機和交流調(diào)頻電機兩種。目前,中小型數(shù)控機床中,交流調(diào)頻電機已占優(yōu)勢,有取代直流電機之勢。本文所設計的加工中心采用交流調(diào)頻電機調(diào)節(jié)電源頻率來達到調(diào)速的目的,額定轉(zhuǎn)速常為1500r/min,如圖 1-1 所示是變速電機的功率特性。從額定轉(zhuǎn)速 到最高轉(zhuǎn)nd速 的區(qū)域 Ⅰ為恒功率區(qū),從最低轉(zhuǎn)速 至 的區(qū)域Ⅱ為恒轉(zhuǎn)矩區(qū)。nmax nmid圖 3-1 變速電動機的功率特性 在設計數(shù)控加工中心主傳動時,必須考慮電機與機床主軸功率特性匹配問題。由于主軸要求的恒功率變速范圍 遠大于電機的恒功率變速范圍 ,Rnp Rdp所以在電機與主軸之間要串聯(lián)一個分級變速箱,以擴大其功率調(diào)速范圍,滿足低速大功率切削時對電機的輸出功率要求。為了簡化變速箱結(jié)構(gòu),變速級數(shù)應少些,變速箱公比 可取大于電機的恒功率調(diào)速范圍 ,即 〉 。?f dp?fdp這時,變速箱每擋內(nèi)有部分低轉(zhuǎn)速只能恒轉(zhuǎn)矩變速,主傳動系統(tǒng)功率特性圖中出現(xiàn)“缺口” ,稱之功率降低區(qū)。使用“缺口”范圍內(nèi)的轉(zhuǎn)速時,為限制轉(zhuǎn)矩過大,得不到電動機輸出的全部功率。為保證缺口處的輸出功率,電動機的功率應相應的增大。為了滿足主軸傳遞 5.4kw,最高轉(zhuǎn)速 4000r/min 的要求,選ⅠⅡ maxdmiP/KWTH5252 加工中心主軸結(jié)構(gòu)設計15擇上海富田電機生產(chǎn)的 IAG 系列變頻調(diào)速專用感應電動機,其型號為IAG132M—1500—7.5。其中:IAG—系列代號132—極座號(中心高)M—機座長度代號,有 S、M、L 三種類型1500—基本轉(zhuǎn)速 (單位:r/min)Nb7.5—額定功率(單位:kw)電機在 60—1500r/min 內(nèi),實現(xiàn)恒扭矩輸出,在 1500—4500r/min 內(nèi)實現(xiàn)恒功率輸出;最高轉(zhuǎn)速可以達到 6000r/min,當電機轉(zhuǎn)速達到 6000 r/min,扭矩特性不好,因此一般情況下轉(zhuǎn)速只達到 4500r/min3.3 主軸的變速過程為了實現(xiàn)數(shù)控加工中心的無級變速,采用交流調(diào)頻電機,本文所設計的加工中心所選擇的電機需要實現(xiàn)兩級變速,當通電時離合器脫離,小齒輪和大齒輪嚙合,實現(xiàn)增速傳動;當轉(zhuǎn)速下降到電機的計算轉(zhuǎn)速時,離合器吸合,大齒輪和小齒輪嚙合,實現(xiàn)增速傳動。TH5252 加工中心主軸結(jié)構(gòu)設計16第 4 章 主軸部件設計主軸部件是機床實現(xiàn)旋轉(zhuǎn)運動的執(zhí)行件,是機床上的一個重要部件。主軸部件由主軸、主軸支承和安裝在主軸上的傳動件、密封件等組成,對于加工中心主軸部件還有拉桿和拉抓。4.1 主軸的設計概述主軸是組成機械的一個重要零件,它支承其它回轉(zhuǎn)件并傳遞轉(zhuǎn)矩,同時它又通過軸承和支架連接,所有軸上零件都圍繞軸心線做回轉(zhuǎn)運動,形成一個以軸為基準的锝組合體—軸系部件,所以在軸的設計中不能只考慮軸的本身,還必須和軸系零件的整個結(jié)構(gòu)密切聯(lián)系起來。軸設計的特點:在軸系零部件的具體結(jié)構(gòu)未確定之前,軸上力的作用點和支點間的跨距無法精確的確定,故彎距大小和分布情況不能求出,因此在軸的設計中必須把軸的強度計算和軸系零件結(jié)構(gòu)設計交錯進行,邊畫圖,邊計算,邊修改。4.2 主軸主要結(jié)構(gòu)參數(shù)的確定主軸的主要結(jié)構(gòu)參數(shù)有:主軸前、后軸頸 D1 和 D2,主軸內(nèi)孔直徑 d,主軸前端懸伸量 a 和主軸主要支撐間的跨距 L。這些參數(shù)直接影響主軸旋轉(zhuǎn)精度和主軸的剛度。4.2.1 主軸最小直徑的估算當數(shù)值上 時,可按扭轉(zhuǎn)剛度估算最小軸徑,即:njP?……………………………………………(1)41jd?式中:d—主軸的最小直徑(cm)P—主軸傳遞的功率(kw),前面已算出 P=5.4kw—主軸的計算轉(zhuǎn)速(r/min),前面已給出 =160r/minnj nj代人數(shù)值得:d≥11× =11×0.4=4.4cm4160.5TH5252 加工中心主軸結(jié)構(gòu)設計17取主軸的最小直徑 =45mm,最小直徑本應該是后軸頸,但是考慮到軸承d1的軸向固定采用鎖緊螺母,應留鎖緊螺母的位置??紤]到軸上裝軸承,有配合要求,應將后軸頸的直徑圓整到標準直徑,同時要考慮到選擇軸承的類型,因此選擇后軸頸的直徑 =50,D24.2.2 主軸內(nèi)孔直徑 d 及拉桿直徑的確定主軸內(nèi)孔直徑與機床的類型有關,主要用來通過棒料、拉桿、鏜桿或頂出頂尖等,加工中心主要用于通過拉桿和拉抓,確定孔徑的原則是:為減輕主軸重量在滿足上述工藝要求及不削弱主軸剛度的前提下,盡量取較大值,孔徑 d對主軸剛度的影響影響是通過抗彎截面慣性矩而體現(xiàn)的,即主軸本身的剛度正比于抗彎截面慣性矩,其關系式為I空/I實= =1-64/)(Dd??4)(Dd根據(jù)上式可繪制出主軸孔徑對主軸剛度影響曲線,如圖 4-1空 /實圖 4-1 主軸孔徑對主軸剛度影響曲線D—主軸平均直徑,d—主軸平均孔徑, —直徑為D實心主軸剛度 ,實K—直徑為D,孔徑為 d 的空心軸的剛度??誎由圖 4-1 知:當 d/D≤0.5 時,內(nèi)孔 d 對主軸剛度幾乎無影響,通常取孔徑 d 的極限值 <0.7D。此時I空>0.75I實,即剛度消弱量小于 25%,max若孔徑再大主軸剛度急劇下降,一般加工中心主軸孔徑 d 可比刀具拉桿直徑大TH5252 加工中心主軸結(jié)構(gòu)設計185~10mm。由于機床使用場合多種多樣,為了適應加工工藝及刀具特點,機床工具行業(yè)已經(jīng)開發(fā)了多種軸端結(jié)構(gòu),并已形成專業(yè)標準,加工中心常用的主軸端部結(jié)構(gòu)前端帶有 7:24 的錐孔.供插入銑刀尾部錐柄定位,,拉桿從主軸后端拉緊刀具,常用的是 BT—50 刀柄,因此我們采用 BT—50 的外螺紋拉抓,查資料知BT—50 拉抓外螺紋的尺寸為 M22×P1.5,所以拉桿前端必須是 M22 的內(nèi)螺紋,為了滿足拉桿的剛性要求,取拉桿的直徑為 φ28mm,根據(jù)拉桿的直徑確定主軸內(nèi)孔的最小直徑為 φ32 即可.4.2.3 主軸前端懸伸量的確定主軸前端懸伸量 a 是指主軸前端面到前軸承徑向支反力作用中點(或前徑向支承中點)的距離。它主要取決于主軸端部結(jié)構(gòu)、前支承軸承和密封裝置的形式和尺寸,由結(jié)構(gòu)設計確定。由于前端懸伸量對主軸部件的剛度、抗振性影響很大,變形量與 a 的二次方或三次方成正比例關系。 ,因此在滿足結(jié)構(gòu)要求的前提下,設計時應盡量縮短該懸伸量。在確定主軸前端懸伸量時應該滿足以下結(jié)構(gòu)要求:主軸前端要留有裝切削液噴頭的位置;軸承的寬度 B=27;軸承擋環(huán)的厚度 b=8;主軸下支承的安裝位置以及軸肩的寬度。4.2.4 主軸支承跨距 L 的確定合理確定主軸主要支承間的跨距 L,是獲得主軸部件最大靜剛度的重要條件之一。支承跨距過小,主軸的彎曲變形固然較小,但因支承變形引起主軸前軸端的位移量增大;反之,支承跨距過大,支承變形引起主軸前軸端的位移量盡管減小了,但主軸的彎曲變形增大,也會引起主軸前端較大的位移。因此存在一個最佳跨距 ,在該跨距時,因主軸彎曲變形和支承變形引起主軸前軸L0端的總位移量為最小。一般取 =(2~3.5) ,本文所設計的主軸暫取0aL=2.5a=360,但是實際結(jié)構(gòu)設計時,由于結(jié)構(gòu)上的原因,以及支承剛度因磨損會不斷降低,主軸主要支承間的實際跨距 L 往往大于最佳跨距 。L0TH5252 加工中心主軸結(jié)構(gòu)設計194.2.5 計算主軸傳遞的扭矩根據(jù)電機的扭矩—功率特性圖知,當主軸的轉(zhuǎn)速為基準轉(zhuǎn)速時所傳遞的扭矩最大,即 n=n =1500r/min,則j=9.55×10 =9.55×10 =3.438×10 NTmax6nPmax61504.44.2.6 選擇軸的材料和熱處理方法選擇軸的材料為 40Cr, ,經(jīng)調(diào)質(zhì)處理, 其機械性能有設計手冊查得=700Mpa, =500Mpa, =185Mpa?bs?1?查機械設計手冊得[ ] =190Mpa1-b4.2.7 初選軸承本文所設計的加工中心主要用于銑削平面和打孔,軸承承受徑向載荷,還承受不大的軸向載荷,故選擇單列圓錐滾子軸承背對背的組合。根據(jù)工作要求及后軸頸的直徑(為 50mm),由軸承產(chǎn)品目錄中選取型號為 32010 的單列圓錐滾子軸承,其尺寸(內(nèi)徑×外徑×寬度)為 d×D×b=50×80×20。4.3 軸的結(jié)構(gòu)設計4.3.1 擬定軸上零件的裝配方案`本文所設計的主軸要用原有的主軸箱,根據(jù)主軸箱的結(jié)構(gòu)、軸上零件定位、加工要求以及不同的零件裝配方案, ,參考軸的結(jié)構(gòu)設計的基本要求,得出如圖所示的軸結(jié)構(gòu)。TH5252 加工中心主軸結(jié)構(gòu)設計20圖 4-2 主軸的結(jié)構(gòu)如圖 4-2 中,拉桿與 BT50 拉刀抓連接,從右側(cè)裝入內(nèi)孔,然后再裝入BT50 刀柄;齒輪、軸承、套筒、軸承套以及電磁鐵固定架從左側(cè)裝入,法蘭蓋從右側(cè)裝入,與軸承套用螺釘連接。4.3.2 確定軸各段的直徑根據(jù)前面的計算知:最小直徑 D=45mm,小軸承用鎖緊螺母進行軸向固定,所以取軸段 1 外螺紋的直徑 M =45mm;根據(jù)軸承的型號以及與軸的配合關系,1取軸段 2 的直徑 =50mm。D2軸段 4 處裝小齒輪,承受很大的徑向力,同時主軸是空心的,考慮到主軸的整體剛性,取軸段 4 的直徑 =75mm,小齒輪用鎖緊螺母壓緊,則軸段 44的直徑比軸段 3 的直徑大 2~3mm,所以取軸段 3 處的外螺紋直徑 M =72mm。4軸段 5 上有兩個軸套,軸套左側(cè)用于定位小齒輪,中間用來壓緊和定位電磁鐵固定架,考慮到拆卸方便,軸段 5 要比軸段 4 大 2~3mm,同時要比軸段 6小 2~3mm 因此取軸段 5 的直徑 =78mm,軸段 6 的直徑 =80mm。D6大齒輪主要靠軸段 7 的軸肩來定位的,為了保證定位可靠,軸段 7 要比軸段 6 的直徑大 5~10mm,但是考慮到主軸前端的內(nèi)孔交大,因此取軸段 7 的直徑為 =92mm。789101234567TH5252 加工中心主軸結(jié)構(gòu)設計21軸段 8 是前軸頸,主軸的直徑因與軸承的內(nèi)徑相等,考慮到軸承的型號以及與主軸的配合關系,取軸段 8 的直徑 =95mm,軸承的型號為 32109。D8主軸前端內(nèi)孔采用 7:24 的錐度,裝 BT50 的刀柄,內(nèi)孔較大,取軸段 10的外徑 =127mm,軸段 9 主要起定位作用,因比軸段 10 大 5~10mm,因此取D10軸段 9 的直徑為 =137mm。4.3.3 確定各軸段的長度軸段 4 和 6 的長度要比輪轂寬度(38mm)短 2~3mm,故這兩處軸段的長度取為 36mm。其中軸段 4 不包括退刀槽的長度。軸段 1 和 3 有外螺紋,裝徑向鎖緊螺母,故軸段 1 和 3 的長度比鎖緊螺母長 2~3mm,取軸段 1 的長度為 15.7mm,軸段 3 的長度為 18.2mm軸段 7 主要與軸承套配合,壓緊軸承,為了保證軸承套與大齒輪之間有一定的間隙,取軸段 7 的長度為 25mm;軸段 8 是后軸頸,所選軸承的寬度B=32mm,軸承擋環(huán)的寬度 T=8mm,故取軸段 8 的長度為 44mm。軸段 9 是一個軸肩,主要起定位作用,取軸段 9 的長度為 11 即可;主軸的前端面要裝端面鍵,同時主軸前端要留下裝切削液噴頭的位置,因此取軸段10 的長度為 69mm。主軸內(nèi)孔要裝拉桿、拉刀抓及 BT50 刀柄,整體裝配起來應該讓拉桿不要伸出主軸內(nèi)孔太長,否則加工中心的整體動剛度不好,根據(jù)主軸和主動軸的整體裝配關系,取軸段 1 的長度為 75.4mm,軸段 5 的長度為 209mm。綜上所述,主軸的跨距 L=373mm,懸伸量a=96mm4.3.4 軸向零件的周向固定齒輪、電磁鐵固定架與軸的周向定位均采用半圓鍵聯(lián)接。對于齒輪,由手冊查得半圓鍵的截面尺寸寬×高×直徑=10×13×32(GB/T1098-2003),鍵槽用鍵槽銑刀加工,長為 29。7mm(標準鍵長見 GB1096-79);對于電磁鐵固定架,由手冊查得半圓鍵的截面尺寸寬×高×直徑=6×9×22(GB/T1098-2003),鍵槽用鍵槽銑刀加工,長為 29.7mm(標準鍵長見 GB1096-79),軸承與軸的周向定位是采用過盈TH5252 加工中心主軸結(jié)構(gòu)設計22配合來保證的。4.3.5 確定軸上倒角和退刀槽的尺寸取主軸前端的倒角為 4×45°,其余倒角 1×45°;所有退刀槽的尺寸為2×14.4 主軸剛度的計算軸在載荷作用下,將產(chǎn)生彎曲和扭轉(zhuǎn)變形。若變形量超過允許的限度,就會影響軸上零件的正常工作,甚至會破壞加工中心的工作性能。因此在設計重要軸時,必須檢驗軸的變形量,這在軸的設計中稱為剛度計算剛度計算包括扭轉(zhuǎn)剛度計算和彎曲剛度計算兩種。前者以扭轉(zhuǎn)角 ψ 來度量;后者以撓度 y 和截面轉(zhuǎn)角 θ 來度量。本文以彎曲剛度校核,查機械設計手冊知:[y]=0.00025L;圓錐滾子軸承處的偏轉(zhuǎn)角[θ]=0.0016rad。主軸的簡化和彎曲剛度的計算1、如主軸前后軸承頸之間有數(shù)段組成,則當量直徑 dd= lldldn??2式中: 、 ; 、 ;…; 、 —分別為各段的直徑和長度12lndl—總長, = + +…+ (mm)l1= =78.6mmd373.289536802985.75.0 ???????2、主軸切削力 的計算切F根據(jù)公式 P= 得: = ,則當線速度 最小時 ,切削力最大切 v切 vPv= = =0.21m/smin601in?D?6014.3?= = =25.7KN切FvP2,4.53、撓度的計算主軸的前懸伸部分較粗,剛度較高,其變形可以忽略不計。后懸伸部分不TH5252 加工中心主軸結(jié)構(gòu)設計23影響剛度。當主軸前端作用一外載 ,則撓度切Fy= (mm )= ×10 (μm)EIlaF32切 Ila32切 3式中 —典型切削工藝的切削力切—前懸伸,等于載荷作用點至前支承點間的距離(mm)a—跨距,等于前后支承之間的距離(mm)lE—彈性模量,鋼?。牛?×10 (Mpa)5I—截面慣性矩,I=0.05( - ) (mm )4di4, —主軸的外徑和孔徑(mm)di將 E 和 I 的值待人,可得y= = =79μm≤0.0002L=0.09325mm)(3042idlaF?切 )( 4236.780915??4、偏轉(zhuǎn)角主軸切削工件時承受很大的切削力,主軸前端產(chǎn)生彎曲變形,查機床設計手冊得=?D)32(6alEIF?切式中 —主軸前端偏轉(zhuǎn)角(rad)、 、 、E、I與前面相同切 al代入數(shù)據(jù)得= ×(2×373+3×69)=0.0011 rad?D )( 45326.780.1269???所以 ≤[θ]=0.0016 rad綜上所述 主軸的剛度滿足條件,不必重新設計。TH5252 加工中心主軸結(jié)構(gòu)設計24第 5 章 齒輪傳動設計與計算一般,設計齒輪傳動時,已知的條件是:傳遞的功率 P=5.4KW,轉(zhuǎn)速n=40r/min—4000r/min,傳動比暫取 i=1.78;預定的壽命 5 年,每年工作300 天,每天 24 小時。設計開始時,往往不知道齒輪的尺寸和參數(shù),無法準確定出某些系數(shù)的數(shù)值,因而不能進行精確的計算。所以通常需要先初步選擇某些參數(shù),按簡化計算方法初步確定出主要尺寸,然后再進行精確的校核計算。當主要參數(shù)和幾何尺寸都已經(jīng)合適之后,再進行齒輪的結(jié)構(gòu)設計,并繪制零件工作圖。5.1 主要參數(shù)的選擇1、模數(shù) m 模數(shù)由強度計算或結(jié)構(gòu)設計確定,要求圓整為標準值,傳遞動力的齒輪傳動 m≥2。初步確定模數(shù)時,對于軟齒面齒輪(齒面硬度)350HBS)外嚙合傳動 m=(0.007~0.02)a;載荷平穩(wěn),中心距過大時取小值,本文所設計的主軸傳動采用已有的箱體,可以知道中心距 a=150mm,因此取模數(shù)m=0.015a=2.25mm,將模數(shù)圓整到標準值,取 m=2.5mm2、螺旋角 β β 角太小,將失去斜齒輪的優(yōu)點;但太大將會引起很大的軸向力。一般取 β=8 —15 ,此處取 β=13 。0 03、齒數(shù) z 當中心距一定時,齒數(shù)取多,則重合度 增大,改善了傳動?a的平穩(wěn)性。同時,齒數(shù)多則模數(shù)小、齒頂圓直徑小,并且又能減小金屬切削量,節(jié)省材料,降低加工成本。但是齒數(shù)增多則模數(shù)減小,齒輪的抗彎強度降低,因此,在滿足抗彎強度的條件下,宜取較多的齒數(shù)。5.2 齒輪的設計與計算5.2.1、選擇材料查機床設計手冊,小齒輪:20CrMnTi,滲碳淬火,硬度 45~55HRC大齒輪:20CrMnTi,滲碳淬火,硬度 45~55HRC 按 MQ 級質(zhì)量要求取值,查得=780N/mm , =820N/mm ; =620 N/mm , =640 ?1limH22limH2?1FE2?2FE