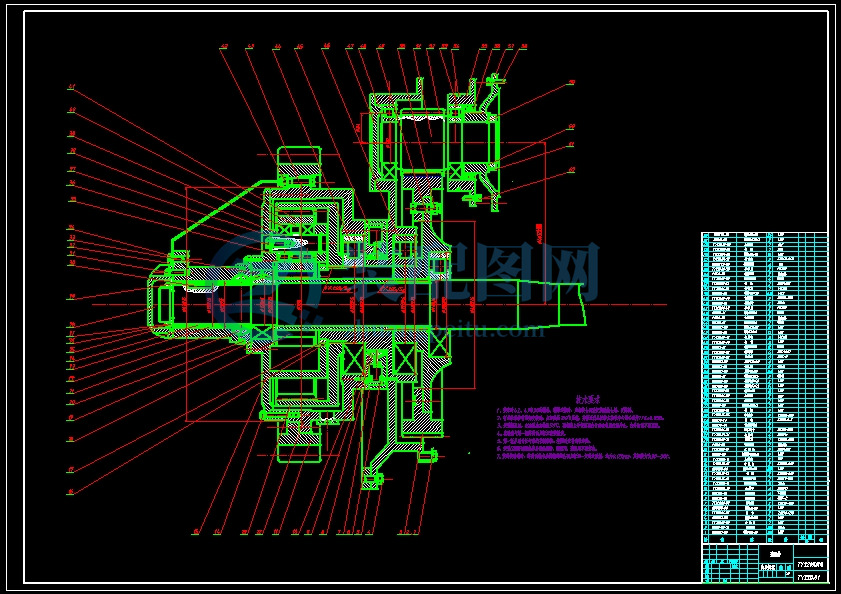
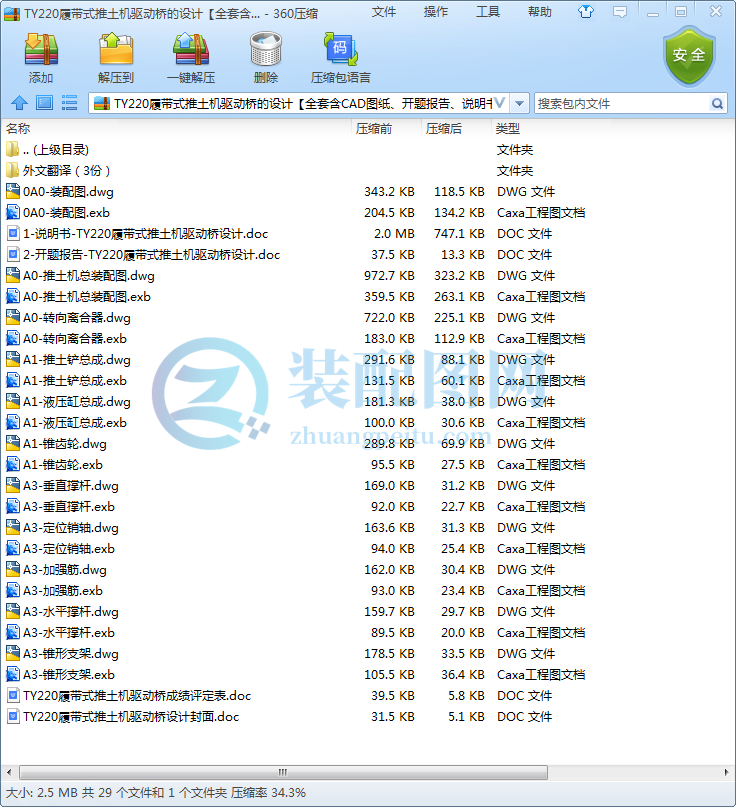











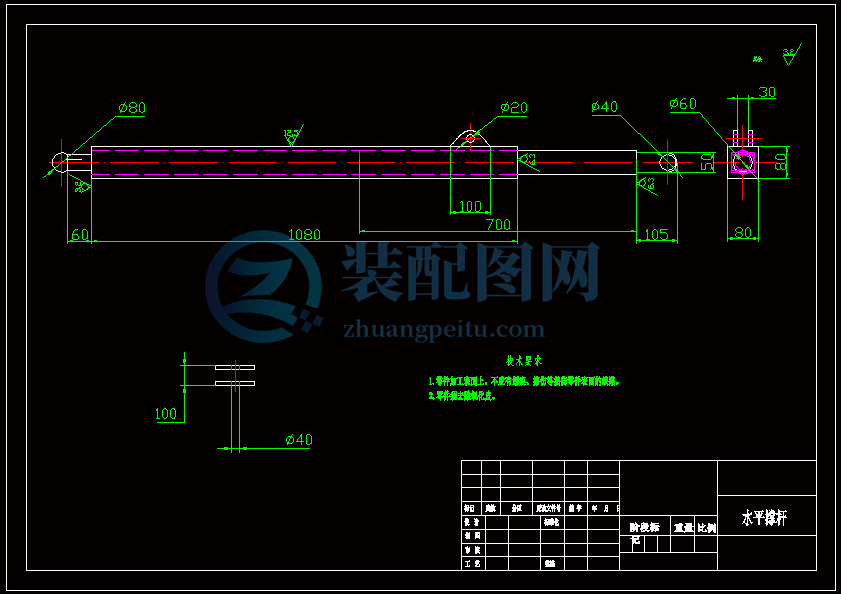


附件1:外文資料翻譯譯文
機(jī)械設(shè)計
摘要: 機(jī)器是由機(jī)械裝置和其它組件組成的。它是一種用來轉(zhuǎn)換或傳遞能量的裝置,例如:發(fā)動機(jī)、渦輪機(jī)、車輛、起重機(jī)、印刷機(jī)、洗衣機(jī)、照相機(jī)和攝影機(jī)等。許多原則和設(shè)計方法不但適用于機(jī)器的設(shè)計,也適用于非機(jī)器的設(shè)計。術(shù)語中的“機(jī)械裝置設(shè)計” 的含義要比“機(jī)械設(shè)計”的含義更為廣泛一些,機(jī)械裝置設(shè)計包括機(jī)械設(shè)計。在分析運(yùn)動及設(shè)計結(jié)構(gòu)時,要把產(chǎn)品外型以及以后的保養(yǎng)也要考慮在機(jī)械設(shè)計中。在機(jī)械工程領(lǐng)域中,以及其它工程領(lǐng)域中,所有這些都需要機(jī)械設(shè)備,比如:開關(guān)、凸輪、閥門、船舶以及攪拌機(jī)等。
關(guān)鍵詞: 設(shè)計流程 設(shè)計規(guī)則 機(jī)械設(shè)計
設(shè)計流程
設(shè)計開始之前就要想到機(jī)器的實(shí)際性,現(xiàn)存的機(jī)器需要在耐用性、效率、重量、速度,或者成本上得到改善。新的機(jī)器必需具有以前機(jī)器所能執(zhí)行的功能。
在設(shè)計的初始階段,應(yīng)該允許設(shè)計人員充分發(fā)揮創(chuàng)造性,不要受到任何約束。即使產(chǎn)生了許多不切實(shí)際的想法,也會在設(shè)計的早期,即在繪制圖紙之前被改正掉。只有這樣,才不致于阻斷創(chuàng)新的思路。通常,還要提出幾套設(shè)計方案,然后加以比較。很有可能在這個計劃最后決定中,使用了某些不在計劃之內(nèi)的一些設(shè)想。
一般的當(dāng)外型特點(diǎn)和組件部分的尺寸特點(diǎn)分析得透徹時,就可以全面的設(shè)計和分析。接著還要客觀的分析機(jī)器性能的優(yōu)越性,以及它的安全、重量、耐用性,并且競爭力的成本也要考慮在分析結(jié)果之內(nèi)。每一個至關(guān)重要的部分要優(yōu)化它的比例和尺寸,同時也要保持與其它組成部分相協(xié)調(diào)。
也要選擇原材料和處理原材料的方法。通過力學(xué)原理來分析和實(shí)現(xiàn)這些重要的特性,如那些靜態(tài)反應(yīng)的能量和摩擦力的最佳利用,像動力慣性、加速動力和能量;包括彈性材料的強(qiáng)度、應(yīng)力和剛度等材料的物理特性,以及流體潤滑和驅(qū)動器的流體力學(xué)。設(shè)計的過程是重復(fù)和合作的過程,無論是正式或非正式的進(jìn)行,對設(shè)計者來說每個階段都很重要。
最后,以圖樣為設(shè)計的標(biāo)準(zhǔn),并建立將來的模型。如果它的測試是符合事先要求的,則再將對初步設(shè)計進(jìn)行某些修改,使它能夠在制造成本上有所降低。產(chǎn)品的設(shè)計需要不斷探索和發(fā)展。許多方案必須被研究、試驗、完善,然后決定使用還是放棄。雖然每個工程學(xué)問題的內(nèi)容是獨(dú)特的,但是設(shè)計師可以按照類似的步驟來解決問題。
產(chǎn)品的責(zé)任訴訟迫使設(shè)計人員和公司在選擇材料時,采用最好的程序。在材料過程中,五個最常見的問題為:(a)不了解或者不會使用關(guān)于材料應(yīng)用方面的最新最好的信息資料;(b)未能預(yù)見和考慮材料的合理用途(如有可能,設(shè)計人員還應(yīng)進(jìn)一步預(yù)測和考慮由于產(chǎn)品使用方法不當(dāng)造成的后果。在近年來的許多產(chǎn)品責(zé)任訴訟案件中,由于錯誤地使用產(chǎn)品而受到傷害的原告控告生產(chǎn)廠家,并且贏得判決);(c)所使用的材料的數(shù)據(jù)不全或是有些數(shù)據(jù)不確定,尤其是當(dāng)其性能數(shù)據(jù)長期不更新;(d)質(zhì)量控制方法不適當(dāng)和未經(jīng)驗證;(e)由一些完全不稱職的人員選擇材料。
通過對上述五個問題的分析,可以得出這些問題是沒有充分理由而存在的結(jié)論。對這些問題的研究分析可以為避免這些問題的出現(xiàn)而指明方向。盡管采用最好的材料選擇方法也不能避免發(fā)生產(chǎn)品責(zé)任訴訟,設(shè)計人員和工業(yè)界按照適當(dāng)?shù)某绦蜻M(jìn)行材料選擇,可以大大減少訴訟的數(shù)量。
從以上的討論可以看出,選擇材料的人們應(yīng)該對材料的性質(zhì),特點(diǎn)和加工方法有一個全面而基本的了解。
在隨后生產(chǎn)和售后服務(wù)的幾年中,要接受新觀念的變化,或者由試驗和經(jīng)驗為基礎(chǔ),進(jìn)一步分析并改進(jìn)。
一些設(shè)計規(guī)則
在本節(jié)中,建議要運(yùn)用創(chuàng)造性的態(tài)度來替代和改進(jìn)。也許會創(chuàng)造出更實(shí)用、更經(jīng)濟(jì)、更耐用的產(chǎn)品。
為了激發(fā)創(chuàng)造性思維,下列是設(shè)計和分析的建議規(guī)則。前六個規(guī)則對設(shè)計者來說特別適用。
1. 要有創(chuàng)造性的利用所需要的物理性質(zhì)和控制過程。
2. 認(rèn)識負(fù)載產(chǎn)生的影響及其意義。
3. 預(yù)測沒有想到的負(fù)載。
4. 創(chuàng)造出對載荷更為有利的條件。
5. 提供良好的應(yīng)力分布和最小的剛度條件。
6. 運(yùn)用最簡單的方程來優(yōu)化體積和面積。
7. 選擇組合材料。
8. 仔細(xì)選擇所備的原料和不可缺少的組件。
9. 調(diào)整有效的設(shè)計方案,以適應(yīng)生產(chǎn)過程和降低成本。
10. 規(guī)定好準(zhǔn)確的位置條件為了使組件安裝時不干涉。
機(jī)械設(shè)計包括一下內(nèi)容:
1. 對設(shè)計過程、設(shè)計所需要公式以及安全系數(shù)進(jìn)行介紹。
2. 回顧材料特性、靜態(tài)和動態(tài)載荷分析,包括梁、振動和沖擊載荷。
3. 回顧應(yīng)力的基本規(guī)律和失效分析。
4. 介紹靜態(tài)失效理論和靜態(tài)載荷下機(jī)械斷裂分析。
5. 介紹疲勞失效理論并強(qiáng)調(diào)在壓力條件下接近高循環(huán)的疲勞設(shè)計,這通常用在旋轉(zhuǎn)機(jī)械的設(shè)計中。
6. 深入探討機(jī)械磨損機(jī)理、表面接觸應(yīng)力和表面疲勞現(xiàn)象。
7. 使用疲勞分析技術(shù)校核軸的設(shè)計。
8. 討論潤滑油膜與滾動軸承的理論和應(yīng)用。
9. 深入介紹直齒圓柱齒輪的動力學(xué)、設(shè)計和應(yīng)力分析,并簡單介紹斜齒輪、錐齒輪和渦輪有關(guān)方面的問題。
10. 討論彈簧設(shè)計、螺桿等緊固件的設(shè)計,包括傳動螺桿和預(yù)緊固件。
11. 介紹盤式和鼓式離合器以及制動器的設(shè)計和技術(shù)說明。
機(jī)械設(shè)計
一臺完整機(jī)器的設(shè)計是一個復(fù)雜的過程。機(jī)械設(shè)計是一項創(chuàng)造性的工作。設(shè)計工程師不僅在工作上要有創(chuàng)造性,還必須在機(jī)械制圖、運(yùn)動學(xué)、工程材料、材料力學(xué)和機(jī)械制造工藝學(xué)等方面具有深厚的基礎(chǔ)知識。
任何產(chǎn)品在設(shè)計時第一步就是選擇產(chǎn)品每個部分的構(gòu)成材料。許多的材料被今天的設(shè)計師所使用。對產(chǎn)品的功能,它的外觀、材料的成本、制造的成本作出必要的選擇是十分重要的。對材料的特性必須事先作出仔細(xì)的評估。
仔細(xì)精確的計算是必要的,以確保設(shè)計的有效性。在任何失敗的情況下,最好知道在最初設(shè)計中有有缺陷的部件。計算(圖紙尺寸)檢查是非常重要的。一個小數(shù)點(diǎn)的位置放錯,就可以導(dǎo)致一個本可以完成的項目失敗。設(shè)計工作的各個方面都應(yīng)該檢查和復(fù)查。
計算機(jī)是一種工具,它能夠幫助機(jī)械設(shè)計師減輕繁瑣的計算,并對現(xiàn)有數(shù)據(jù)提供進(jìn)一步的分析。互動系統(tǒng)基于計算機(jī)的能力,已經(jīng)使計算機(jī)輔助設(shè)計(CAD)和計算機(jī)輔助制造(CAM)成為了可能。心理學(xué)家經(jīng)常談?wù)撊绾问谷藗冞m應(yīng)他們所操作的機(jī)器。設(shè)計人員的基本職責(zé)是努力使機(jī)器來適應(yīng)人們。這并不是一項容易的工作,因為實(shí)際上并不存在著一個對所有人來說都是最優(yōu)的操作范圍和操作過程。另一個重要問題,設(shè)計工程師必須能夠同其他有關(guān)人員進(jìn)行交流和磋商。在開始階段,設(shè)計人員必須就初步設(shè)計同管理人員進(jìn)行交流和磋商,并得到批準(zhǔn)。這一般是通過口頭討論,草圖和文字材料進(jìn)行的。
如前所訴,機(jī)械設(shè)計的目的是生產(chǎn)能夠滿足人類需求的產(chǎn)品。發(fā)明、發(fā)現(xiàn)和科技知識本身并不一定能給人類帶來好處,只有當(dāng)它們被應(yīng)用在產(chǎn)品上才能產(chǎn)生效益。因而,應(yīng)該認(rèn)識到在一個特定的產(chǎn)品進(jìn)行設(shè)計之前,必須先確定人們是否需要這種產(chǎn)品。
應(yīng)當(dāng)把機(jī)械設(shè)計看成是機(jī)械設(shè)計人員運(yùn)用創(chuàng)造性的才能進(jìn)行產(chǎn)品設(shè)計、系統(tǒng)分析和制定產(chǎn)品的制造工藝學(xué)的一個良機(jī)。掌握工程基礎(chǔ)知識要比熟記一些數(shù)據(jù)和公式更為重要。僅僅使用數(shù)據(jù)和公式是不足以在一個好的設(shè)計中做出所需的全部決定的。另一方面,應(yīng)該認(rèn)真精確的進(jìn)行所有運(yùn)算。例如,即使將一個小數(shù)點(diǎn)的位置放錯,也會使正確的設(shè)計變成錯誤的。
一個好的設(shè)計人員應(yīng)該勇于提出新的想法,而且愿意承擔(dān)一定的風(fēng)險,當(dāng)新的方法不適用時,就使用原來的方法。因此,設(shè)計人員必須要有耐心,因為 所花費(fèi)的時間和努力并不能保證帶來成功。一個全新的設(shè)計,要求屏棄許多陳舊的,為人們所熟知的方法。由于許多人墨守成規(guī),這樣做并不是一件容易的事。一位機(jī)械設(shè)計師應(yīng)該不斷地探索改進(jìn)現(xiàn)有的產(chǎn)品的方法,在此過程中應(yīng)該認(rèn)真選擇原有的、經(jīng)過驗證的設(shè)計原理,將其與未經(jīng)過驗證的新觀念結(jié)合起來。
新設(shè)計本身會有許多缺陷和未能預(yù)料的問題發(fā)生,只有當(dāng)這些缺陷和問題被解決之后,才能體現(xiàn)出新產(chǎn)品的優(yōu)越性。因此,一個性能優(yōu)越的產(chǎn)品誕生的同時,也伴隨著較高的風(fēng)險。應(yīng)該強(qiáng)調(diào)的是,如果設(shè)計本身不要求采用全新的方法,就沒有必要僅僅為了變革的目的而采用新方法。
附件2:外文原文(復(fù)印件)
Mechanical Design
Abstract:
A machine is a combination of mechanisms and other components which transforms, transmits. Examples are engines, turbines, vehicles, hoists, printing presses, washing machines, and movie cameras. Many of the principles and methods of design that apply to machines also apply to manufactured articles that are not true machines. The term "mechanical design" is used in a broader sense than "machine design" to include their design. the motion and structural aspects and the provisions for retention and enclosure are considerations in mechanical design. Applications occur in the field of mechanical engineering, and in other engineering fields as well, all of which require mechanical devices, such as switches, cams, valves, vessels, and mixers.
Keywords: Mechanical Design mechanisms Design Process
The Design Process
Designing starts with a need real.Existing apparatus may need improvements in durability, efficiency, weight, speed, or cost. New apparatus may be needed to perform a function previously
done by men, such as computation, assembly, or servicing. With the objective wholly or partly
In the design preliminary stage, should allow to design the personnel fully to display the creativity, not each kind of restraint. Even if has had many impractical ideas, also can in the design early time, namely in front of the plan blueprint is corrected. Only then, only then does not send to stops up the innovation the mentality. Usually, must propose several sets of design proposals, then perform the comparison. Has the possibility very much in the plan which finally designated, has used certain not in plan some ideas which accepts.
When the general shape and a few dimensions of the several components become apparent, analysis can begin in earnest. The analysis will have as its objective satisfactory or superior performance, plus safety and durability with minimum weight, and a competitive cost. Optimum proportions and dimensions will be sought for each critically loaded section, together with a balance between the strengths of the several components. Materials and their treatment will be chosen. These important objectives can be attained only by analysis based upon the principles of mechanics, such as those of static for reaction forces and for the optimum utilization of friction; of dynamics for inertia, acceleration, and energy; of elasticity and strength of materials for stress and deflection; of physical behavior of materials; and of fluid mechanics for lubrication and hydrodynamic drives. The analyses may be made by the same engineer who conceived the arrangement of mechanisms, or, in a large company, they may be made by a separate analysis division or research group. Design is a reiterative and cooperative process, whether done formally or informally, and the analyst can contribute to phases other than his own. Product design requires much research and development. Many Concepts of an idea must be studied, tried, and then either used or discarded. Although the content of each engineering problem is unique, the designers follow the similar process to solve the problems.
Product liability suits designers and forced in material selection, using the best program. In the process of material, the most common problems for five (a) don't understand or not use about the latest application materials to the best information, (b) failed to foresee and consider the reasonable use material may (such as possible, designers should further forecast and consider due to improper use products. In recent years, many products liability in litigation, the use of products and hurt the plaintiff accused manufacturer, and won the decision), (c) of the materials used all or some of the data, data, especially when the uncertainty long-term performance data is so, (d) quality control method is not suitable and unproven, (e) by some completely incompetent persons choose materials.
Through to the above five questions analysis, may obtain these questions is does not have the sufficient reason existence the conclusion. May for avoid these questions to these questions research analyses the appearance indicating the direction. Although uses the best choice of material method not to be able to avoid having the product responsibility lawsuit, designs the personnel and the industry carries on the choice of material according to the suitable procedure, may greatly reduce the lawsuit the quantity.
May see from the above discussion, the choice material people should to the material nature, the characteristic and the processing method have comprehensive and the basic understanding.
Finally, a design based upon function, and a prototype may be built. If its tests are satisfactory, the initial design will undergo certain modifications that enable it to be manufactured in quantity at a lower cost. During subsequent years of manufacture and service, the design is likely to undergo changes as new ideas are conceived or as further analyses based upon tests and experience indicate alterations. Sales appeal.
Some Rules for Design
In this section it is suggested that, applied with a creative attitude, analyses can lead to important improvements and to the conception and perfection of alternate, perhaps more functional, economical,
and durable products.
To stimulate creative thought, the following rules are suggested for the designer and analyst. The first six rules are particularly applicable for the analyst.
1. A creative use of need of physical properties and control process.
2. Recognize functional loads and their significance.
3. Anticipate unintentional loads.
4. Devise more favorable loading conditions.
5. Provide for favorable stress distribution and stiffness with minimum weight.
6. Use basic equations to proportion and optimize dimensions.
7. Choose materials for a combination of properties.
8. Select carefully, stock and integral components.
9. Modify a functional design to fit the manufacturing process and reduce cost.
10. Provide for accurate location and noninterference of parts in assembly.
Machinery design covers the following contents.
1. Provides an introduction to the design process , problem formulation ,safety factors.
2. Reviews the material properties and static and dynamic loading analysis ,
Including beam , vibration and impact loading.
3. Reviews the fundamentals of stress and defection analysis.
4. Introduces fatigue-failure theory with the emphasis on stress-life approaches to high-cycle fatigue design, which is commonly used in the design of rotation machinery.
5. Discusses thoroughly the phenomena of wear mechanisms, surface contact stresses ,and surface fatigue.
6. Investigates shaft design using the fatigue-analysis techniques.
7. Discusses fluid-film and rolling-element bearing theory and application
8. Gives a thorough introduction to the kinematics, design and stress analysis of spur gears , and a simple introduction to helical ,bevel ,and worm gearing.
9. Discusses spring design including compression ,extension and torsion springs.
10. Deals with screws and fasteners including power screw and preload fasteners.
11. Introduces the design and specification of disk and drum clutches and brakes.
Machine Design
The complete design of a machine is a complex process. The machine design is a creative work. Project engineer not only must have the creativity in the work, but also must in aspect and so on mechanical drawing, kinematics, engineerig material, materials mechanics and machine manufacture technology has the deep elementary knowledge.
One of the first steps in the design of any product is to select the material from which each part is to be made. Numerous materials are available to today's designers. The function of the product, its appearance, the cost of the material, and the cost of fabrication are important in making a selection. A careful evaluation of the properties of a. material must be made prior to any calculations.
Careful calculations are necessary to ensure the validity of a design. In case of any part failures, it is desirable to know what was done in originally designing the defective components. The checking of calculations (and drawing dimensions) is of utmost importance. The misplacement of one decimal point can ruin an otherwise acceptable project. All aspects of design work should be checked and rechecked.
The computer is a tool helpful to mechanical designers to lighten tedious calculations, and provide extended analysis of available data. Interactive systems, based on computer capabilities, have made possible the concepts of computer aided design (CAD) and computer-aided manufacturing (CAM). How does the psychologist frequently discuss causes the machine which the people adapts them to operate. Designs personnel''s basic responsibility is diligently causes the machine to adapt the people. This certainly is not an easy work, because certainly does not have to all people to say in fact all is the most superior operating area and the operating process. Another important question, project engineer must be able to carry on the exchange and the consultation with other concerned personnel. In the initial stage, designs the personnel to have to carry on the exchange and the consultation on the preliminary design with the administrative personnel, and is approved. This generally is through the oral discussion, the schematic diagram and the writing material carries on.
If front sues, the machine design goal is the production can meet the human need the product. The invention, the discovery and technical knowledge itself certainly not necessarily can bring the advantage to the humanity, only has when they are applied can produce on the product the benefit. Thus, should realize to carries on before the design in a specific product, must first determine whether the people do need this kind of product
Must regard as the machine design is the machine design personnel carries on using creative ability the product design, the system analysis and a formulation product manufacture technology good opportunity. Grasps the project elementary knowledge to have to memorize some data and the formula is more important than. The merely service data and the formula is insufficient to the completely decision which makes in a good design needs. On the other hand, should be earnest precisely carries on all operations. For example, even if pla
A good design personnel should dare to propose the new idea, moreover is willing to undertake the certain risk, when the new method is not suitable, use original method. Therefore, designs the personnel to have to have to have the patience, because spends the time and the endeavor certainly cannot guarantee brings successfully. A brand-new design, the request screen abandons obsoletely many, knows very well the method for the people. Because many person of conservativeness, does this certainly is not an easy matter. A mechanical designer should unceasingly explore the improvement existing product the method, should earnestly choose originally, the process confirmation principle of design in this process, with has not unified it after the confirmation new idea.
ces wrong a decimal point position, also can cause the correct design to turn wrongly.
附錄1
驅(qū)動橋橋殼是汽車上的主要零件之一,非斷開式驅(qū)動橋的橋殼起著支承汽車荷重的作用,并將載荷傳給車輪.作用在驅(qū)動車輪上的牽引力,制動力、側(cè)向力和垂向力也是經(jīng)過橋殼傳到懸掛及車架或車廂上。因此橋殼既是承載件又是傳力件,同時它又是主減速器、差速器及驅(qū)動車輪傳動裝置(如半軸)的外殼。
在汽車行駛過程中,橋殼承受繁重的載荷,設(shè)計時必須考慮在動載荷下橋殼有足夠的強(qiáng)度和剛度。為了減小汽車的簧下質(zhì)量以利于降低動載荷、提高汽車的行駛平順性,在保證強(qiáng)度和剛度的前提下應(yīng)力求減小橋殼的質(zhì)量.橋殼還應(yīng)結(jié)構(gòu)簡單、制造方便以利于降低成本。其結(jié)構(gòu)還應(yīng)保證主減速器的拆裝、調(diào)整、維修和保養(yǎng)方便。在選擇橋殼的結(jié)構(gòu)型式時,還應(yīng)考慮汽車的類型、使用要求、制造條件、材料供應(yīng)等。
橋殼的結(jié)構(gòu)型式
橋殼的結(jié)構(gòu)型式大致分為可分式、整體式。
可分式橋殼
可分式橋殼的整個橋殼由一個垂直接合面分為左右兩部分,每一部分均由一個鑄件殼體和一個壓入其外端的半軸套管組成。半軸套管與殼體用鉚釘聯(lián)接。在裝配主減速器及差速器后左右兩半橋殼是通過在中央接合面處的一圈螺栓聯(lián)成一個整體。其特點(diǎn)是橋殼制造工藝簡單、主減速器軸承支承剛度好。但對主減速器的裝配、調(diào)整及維修都很不方便,橋殼的強(qiáng)度和剛度也比較低。過去這種所謂兩段可分式橋殼見于輕型汽車,由于上述缺點(diǎn)現(xiàn)已很少采用。
整體式橋殼
整體式橋殼的特點(diǎn)是將整個橋殼制成一個整體,橋殼猶如一整體的空心粱,其強(qiáng)度及剛度都比較好。且橋殼與主減速器殼分作兩體,主減速器齒輪及差速器均裝在獨(dú)立的主減速殼里,構(gòu)成單獨(dú)的總成,調(diào)整好以后再由橋殼中部前面裝入橋殼內(nèi),并與橋殼用螺栓固定在一起。使主減速器和差速器的拆裝、調(diào)整、維修、保養(yǎng)等都十分方便。
整體式橋殼按其制造工藝的不同又可分為鑄造整體式、鋼板沖壓焊接式和鋼管擴(kuò)張成形式三種。
驅(qū)動橋處于動力傳動系的末端,其基本功能是增大由傳動軸或變速器傳來的轉(zhuǎn)矩,并將動力合理地分配給左、右驅(qū)動輪,另外還承受作用于路面和車架或車身之間的垂直力力和橫向力。驅(qū)動橋一般由主減速器、差速器、車輪傳動裝置和驅(qū)動橋殼等組成。
驅(qū)動橋設(shè)計應(yīng)當(dāng)滿足如下基本要求:
(a)所選擇的主減速比應(yīng)能保證汽車具有最佳的動力性和燃料經(jīng)濟(jì)性。
(b)外形尺寸要小,保證有必要的離地間隙。
(c)齒輪及其它傳動件工作平穩(wěn),噪聲小。
(d)在各種轉(zhuǎn)速和載荷下具有高的傳動效率。
(e)在保證足夠的強(qiáng)度、剛度條件下,應(yīng)力求質(zhì)量小,尤其是簧下質(zhì)量應(yīng)盡量小,以改善汽車平順性。
(f)與懸架導(dǎo)向機(jī)構(gòu)運(yùn)動協(xié)調(diào),對于轉(zhuǎn)向驅(qū)動橋,還應(yīng)與轉(zhuǎn)向機(jī)構(gòu)運(yùn)動協(xié)調(diào)。
(g)結(jié)構(gòu)簡單,加工工藝性好,制造容易,拆裝,調(diào)整方便。
驅(qū)動橋的結(jié)構(gòu)型式按工作特性分,可以歸并為兩大類,即非斷開式驅(qū)動橋和斷開式驅(qū)動橋。當(dāng)驅(qū)動車輪采用非獨(dú)立懸架時,應(yīng)該選用非斷開式驅(qū)動橋;當(dāng)驅(qū)動車輪采用獨(dú)立懸架時,則應(yīng)該選用斷開式驅(qū)動橋。因此,前者又稱為非獨(dú)立懸架驅(qū)動橋;后者稱為獨(dú)立懸架驅(qū)動橋。獨(dú)立懸架驅(qū)動橋結(jié)構(gòu)叫復(fù)雜,但可以大大提高汽車在不平路面上的行駛平順性。
非斷開式驅(qū)動橋
普通非斷開式驅(qū)動橋,由于結(jié)構(gòu)簡單、造價低廉、工作可靠,廣泛用在各種載貨汽車、客車和公共汽車上,在多數(shù)的越野汽車和部分轎車上也采用這種結(jié)構(gòu)。他們的具體結(jié)構(gòu)、特別是橋殼結(jié)構(gòu)雖然各不相同,但是有一個共同特點(diǎn),即橋殼是一根支承在左右驅(qū)動車輪上的剛性空心梁,齒輪及半軸等傳動部件安裝在其中。這時整個驅(qū)動橋、驅(qū)動車輪及部分傳動軸均屬于簧下質(zhì)量,汽車簧下質(zhì)量較大,這是它的一個缺點(diǎn)。
驅(qū)動橋的輪廓尺寸主要取決于主減速器的型式。在汽車輪胎尺寸和驅(qū)動橋下的最小離地間隙已經(jīng)確定的情況下,也就限定了主減速器從動齒輪直徑的尺寸。在給定速比的條件下,如果單級主減速器不能滿足離地間隙要求,可該用雙級結(jié)構(gòu)。在雙級主減速器中,通常把兩級減速器齒輪放在一個主減速器殼體內(nèi),也可以將第二級減速齒輪作為輪邊減速器。對于輪邊減速器:越野汽車為了提高離地間隙,可以將一對圓柱齒輪構(gòu)成的輪邊減速器的主動齒輪置于其從動齒輪的垂直上方;公共汽車為了降低汽車的質(zhì)心高度和車廂地板高度,以提高穩(wěn)定性和乘客上下車的方便,可將輪邊減速器的主動齒輪置于其從動齒輪的垂直下方;有些雙層公共汽車為了進(jìn)一步降低車廂地板高度,在采用圓柱齒輪輪邊減速器的同時,將主減速器及差速器總成也移到一個驅(qū)動車輪的旁邊。
在少數(shù)具有高速發(fā)動機(jī)的大型公共汽車、多橋驅(qū)動汽車和超重型載貨汽車上,有時采用蝸輪式主減速器,它不僅具有在質(zhì)量小、尺寸緊湊的情況下可以得到大的傳動比以及工作平滑無聲的優(yōu)點(diǎn),而且對汽車的總體布置很方便。
斷開式驅(qū)動橋
斷開式驅(qū)動橋區(qū)別于非斷開式驅(qū)動橋的明顯特點(diǎn)在于前者沒有一個連接左右驅(qū)動車輪的剛性整體外殼或梁。斷開式驅(qū)動橋的橋殼是分段的,并且彼此之間可以做相對運(yùn)動,所以這種橋稱為斷開式的。另外,它又總是與獨(dú)立懸掛相匹配,故又稱為獨(dú)立懸掛驅(qū)動橋。這種橋的中段,主減速器及差速器等是懸置在車架橫粱或車廂底板上,或與脊梁式車架相聯(lián)。主減速器、差速器與傳動軸及一部分驅(qū)動車輪傳動裝置的質(zhì)量均為簧上質(zhì)量。兩側(cè)的驅(qū)動車輪由于采用獨(dú)立懸掛則可以彼此致立地相對于車架或車廂作上下擺動,相應(yīng)地就要求驅(qū)動車輪的傳動裝置及其外殼或套管作相應(yīng)擺動。
汽車懸掛總成的類型及其彈性元件與減振裝置的工作特性是決定汽車行駛平順性的主要因素,而汽車簧下部分質(zhì)量的大小,對其平順性也有顯著的影響。斷開式驅(qū)動橋的簧下質(zhì)量較小,又與獨(dú)立懸掛相配合,致使驅(qū)動車輪與地面的接觸情況及對各種地形的適應(yīng)性比較好,由此可大大地減小汽車在不平路面上行駛時的振動和車廂傾斜,提高汽車的行駛平順性和平均行駛速度,減小車輪和車橋上的動載荷及零件的損壞,提高其可靠性及使用壽命。但是,由于斷開式驅(qū)動橋及與其相配的獨(dú)立懸掛的結(jié)構(gòu)復(fù)雜,故這種結(jié)構(gòu)主要見于對行駛平順性要求較高的一部分轎車及一些越野汽車上,且后者多屬于輕型以下的越野汽車或多橋驅(qū)動的重型越野汽車。
多橋驅(qū)動的布置
為了提高裝載量和通過性,有些重型汽車及全部中型以上的越野汽車都是采用多橋驅(qū)動,常采用的有4×4、6×6、8×8等驅(qū)動型式。在多橋驅(qū)動的情況下,動力經(jīng)分動器傳給各驅(qū)動橋的方式有兩種。相應(yīng)這兩種動力傳遞方式,多橋驅(qū)動汽車各驅(qū)動橋的布置型式分為非貫通式與貫通式。前者為了把動力經(jīng)分動器傳給各驅(qū)動橋,需分別由分動器經(jīng)各驅(qū)動橋自己專用的傳動軸傳遞動力,這樣不僅使傳動軸的數(shù)量增多,且造成各驅(qū)動橋的零件特別是橋殼、半軸等主要零件不能通用。而對8×8汽車來說,這種非貫通式驅(qū)動橋就更不適宜,也難于布置了。
為了解決上述問題,現(xiàn)代多橋驅(qū)動汽車都是采用貫通式驅(qū)動橋的布置型式。
在貫通式驅(qū)動橋的布置中,各橋的傳動軸布置在同一縱向鉛垂平面內(nèi),并且各驅(qū)動橋不是分別用自己的傳動軸與分動器直接聯(lián)接,而是位于分動器前面的或后面的各相鄰兩橋的傳動軸,是串聯(lián)布置的。汽車前后兩端的驅(qū)動橋的動力,是經(jīng)分動器并貫通中間橋而傳遞的。其優(yōu)點(diǎn)是,不僅減少了傳動軸的數(shù)量,而且提高了各驅(qū)動橋零件的相互通用性,并且簡化了結(jié)構(gòu)、減小了體積和質(zhì)量。這對于汽車的設(shè)計(如汽車的變型)、制造和維修,都帶來方便。
由于非斷開式驅(qū)動橋結(jié)構(gòu)簡單、造價低廉、工作可靠,查閱資料,可參照國內(nèi)相關(guān)貨車的設(shè)計。
附錄2
Bridge-driven car shell is one of the main parts, non-drive off-shell bridge played a supporting role in the automotive load and load to the wheels. In the role of the drive wheels on the traction, braking force, lateral and vertical forces also spread to fly through the bridge and the shell or inside the frame. Therefore, the bridge carrying both pieces of shell-edge thing is, at the same time it is also the main reducer, and differential wheel drive transmission (such as the axle) of the shell.
In the car, the axle housing to bear the heavy load, the design must take into account the dynamic load under the axle housing have enough strength and stiffness. In order to reduce the spring under the car of lower quality in order to facilitate dynamic load, and improve the car's running smoothly, while ensuring the strength and stiffness on the premise of the bridge should seek to reduce the quality of the shell. Shell structure of the bridge should be simple and easy to create the benefit of lower costs. It should also ensure that the structure of the main reducer of disassembly, adjustment, repair and maintenance easy. Bridge in the selection of the shell structure, should also be given to the type of car, asked to use, manufacture, supply materials and so on.
A bridge of the shell structure
Bridge of the shell structure can be roughly divided into type
There are bridge-shell
There are bridge-shell as a whole from the shell of a bridge into the vertical joints around two parts, each part by the casting of a shell into the outside pressure and a side of the axle casing components. Half shell casing and connected with rivets. In the main reducer, and differential assembly after about two half-bridge through the shell in the joints of the Central Office of the bolt circle into a whole. It features a simple bridge shell manufacturing process, the main reducer bearing stiffness well. But the main reducer of the assembly, adjustment and maintenance are inconvenient, the bridge shell strength and stiffness will be lower. In the past the so-called two-axle housing can be found in the car light, as a result of these shortcomings is now rarely used.
Whole-axle housin
Bridge-shell as a whole is characterized by the entire bridge made of a shell as a whole, the bridge is like a shell of the hollow beam as a whole, its strength and stiffness than good. Bridge and the shell and the shell will be divided into two main reducer, the main reducer, and differential gears are mounted on the main independent slowdown shell, constitute a separate assembly, later adjusted by the bridge in front of the shell in the central bridge into the shell , And with the axle housing fixed together with bolts. It enables a reducer, and differential of disassembly, adjustment, repair, maintenance and so on is very convenient.
Bridge-shell as a whole according to their different manufacturing process can be divided into a whole-casting, stamping steel plates welded steel pipe and the expansion into three forms.
Bridge drive powertrain in the end, its basic function is to increase the transmission shaft or transmission from the torque and power reasonably allocated to the left and right wheel also bear on the role of road and the frame or body Between vertical and horizontal force strength. Driven by the main bridge in general reducer, and differential, gear wheels and drive axle housing component, and so on.
Drive bridge should be designed to meet the basic requirements are as follows:
(a) choice of the main reduction ratio should be able to ensure the car has the best power and fuel economy.
(b) smaller size, it is necessary to ensure that the ground clearance.
(c) transmission gears and other pieces of work in a smooth, small noise.
(d) in a variety of speed and load with a high transmission efficiency.
(e) to ensure sufficient strength, rigidity conditions, the quality should be as small, especially the quality of the next spring should be small in order to improve the car ride.
(f)-oriented suspension and body movement coordination, the drive to the bridge, but also with the agency to coordinate movement.
(g) simple structure, good process and create easy disassembly, easy adjustment.
Drive bridge structure in accordance with characteristics of the work, can be grouped into two broad categories, namely non-drive off the bridge and drive off the bridge. When the drive wheel of a non-independent suspension, the non-selection should be off-drive axle; when the drive wheel independent suspension, the choice should be off-drive axle. As a result, the former driver, also known as non-independent suspension bridge; the latter known as the independent suspension bridge driver. Independent suspension bridge structure called complex drive, but will be much more uneven in the car traveling on the road ride comfort.
Non-drive axle disconnect
General non-drive off the bridge, because it is simple, low-cost, reliable, widely used in a variety of truck, bus and a bus, in most of the off-road cars and car parts is also using this structure. Details of their structure, in particular, the shell structure of the bridge although different, but there is a common feature of the bridge is a shell around the drive wheel bearing on the rigid hollow beams, such as transmission gears and axle components to install it. At this time the entire drive axle, wheel and drive shaft are part of the quality of the next spring, next spring the quality of the larger car, which is one of its shortcomings.
Bridge drive size depends largely on the outline of the main type of reducer. In the tire size and drive under the bridge minimum ground clearance have been identified, will be limited to the main driven gear reducer diameter size. In a given ratio of the conditions, if the single-stage main reducer not meet the requirements of ground clearance, with the two-level structure. In the main two-stage reducer, usually two-stage gear reducer in a shell of the main reducer, can also slow down in the second grade as a round edge gear reducer. The round side reducer: off-road vehicle in order to improve the ground clearance, can constitute a pair of cylindrical gear wheel of the gear reducer at the top of the vertical driven gear; bus in order to reduce the vehicle's center of mass and a high degree of deck A high degree of order to enhance the stability and convenience of the passengers get off, can be round edge of the gear reducer at the bottom of the vertical driven gear; some double-decker bus in order to further reduce the deck height, cylinder gear used in the round edge Reducer, the main reducer, and differential assembly also moved to a wheel next to the driver.
In a small number of high-speed engine with a large bus, Bridge Multi-drive cars and super-heavy-duty truck, sometimes using the main worm-reducer, which not only has the quality in a small, compact size of the case could be a big transmission ratio, as well as the work of Smooth silent advantages, but also to the overall layout of the car easily.
Drive-off bridge
Off-drive off the bridge from the non-drive axle of the obvious characteristics is that the former do not have a connection about the drive wheels or beam rigid shell as a whole. Drive off-shell bridge is a section, and each other can do relative motion, such as the bridge-off. In addition, it is always with the independent match suspension, it is also known as the independent suspension bridge driver. This bridge in the middle of the main reducer, and differential, and so is mounting in the frame beams inside or on the floor or backbone frame-linked. The main reducer, and differential part of the drive shaft and the quality of the gear wheels are on the quality of the spring. Both sides of the drive wheel independent suspension as a result can be caused by site as opposed to one another or inside the frame for swinging up and down, and accordingly on the request of the gear wheel drive and its shell casing or swing accordingly.
Flying car assembly and its flexibility in the type of device components and vibration characteristics of the work is to determine a car ride a major factor, and the spring under the car the size of some of the quality of its ride quality is also significant. Off-drive axle of the quality of the spring under the smaller, independent suspension with the match, with the result that drive the wheels on the ground and contacts of all kinds of terrain and better adaptability, which can greatly reduce the car in the uneven pavement When traveling on the train vibration and tilt to improve vehicle ride and average speed, and reduce the wheel of Axle Load and move on the part of the damage and improve the reliability and service life. However, due to off-drive axle and independent suspension of the match with the structure of the complex, and they were mainly observed in the structure of the smooth running of the higher part of the car and a number of off-road vehicle, and the latter belongs to light more of the following off-road vehicle Bridge or drive the heavy-duty off-road vehicle.
Multi-Bridge-driven layout
In order to improve the loading and through, and some heavy-duty vehicles and medium-sized all over the off-road vehicle and are based on the multi-bridge driver, there is often used in 4 × 4,6 × 6,8 × 8, and other types of drivers. In the multi-bridge drivers, power points as actuators to drive the bridge in two ways. The two corresponding power transfer mode, multi-drive vehicle bridge the drive axle of the type of layout is divided into non-through-and through. In order to power by the former sub-actuator to the drive axle, respectively, to be divided by the actuator through the drive axle own dedicated power transmission shaft, so that not only the increase in the number of drive shaft and caused the driver of the bridge parts in particular Shell Bridge, the main axle, and other parts can not be universal. The 8 × 8 on the car, this non-drive-through is even more inappropriate for the bridge, a difficult layout.
In order to address these problems, and more modern bridges are built on a car driving through the drive-type layout of the bridge.
In the drive-through layout of the bridge, the bridge of the vertical shaft arranged in the same vertical plane and drive the bridge were not Shaft with their own sub-actuator directly connected, but located at the front of the actuator or Behind the bridge of the two adjacent shaft, the layout of the series is. Before and after the driver of the car at both ends of the bridge's driving force is divided by the actuator and through the middle of the bridge and pass. The advantage is not only a reduction of the number of drive shaft, but the driver raised the bridge parts commonality with each other and to simplify the structure, reducing the size and quality. This car's design (such as car variant), manufacturing and maintenance, are convenient.
Due to the non-drive off the bridge structure is simple, low-cost, reliable access to information relevant in the light truck designs.