【溫馨提示】壓縮包內(nèi)含CAD圖有下方大圖片預覽,下拉即可直觀呈現(xiàn)眼前查看、盡收眼底縱觀。打包內(nèi)容里dwg后綴的文件為CAD圖,可編輯,無水印,高清圖,壓縮包內(nèi)文檔可直接點開預覽,需要原稿請自助充值下載,所見才能所得,請見壓縮包內(nèi)的文件及下方預覽,請細心查看有疑問可以咨詢QQ:11970985或197216396
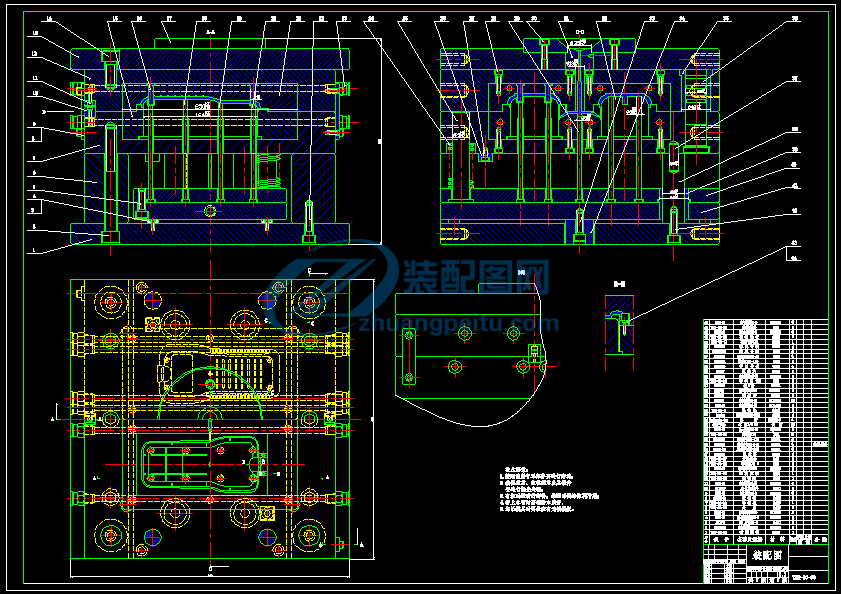
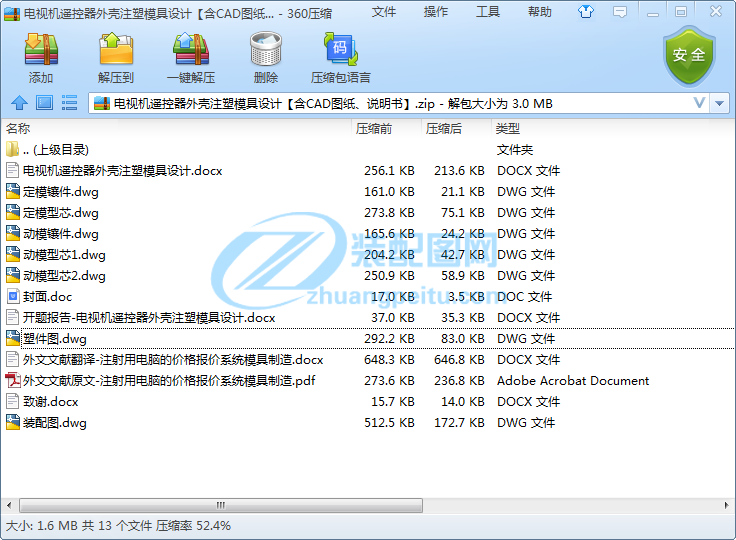
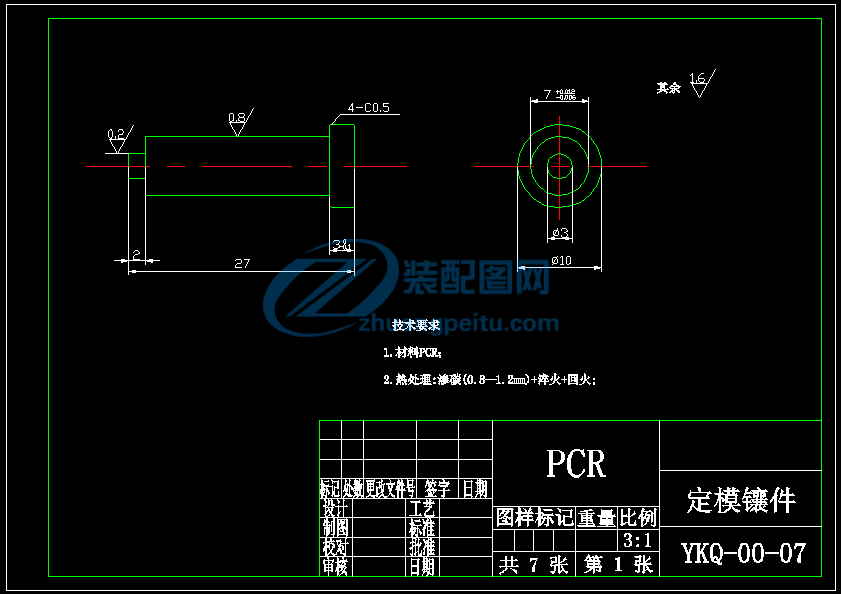
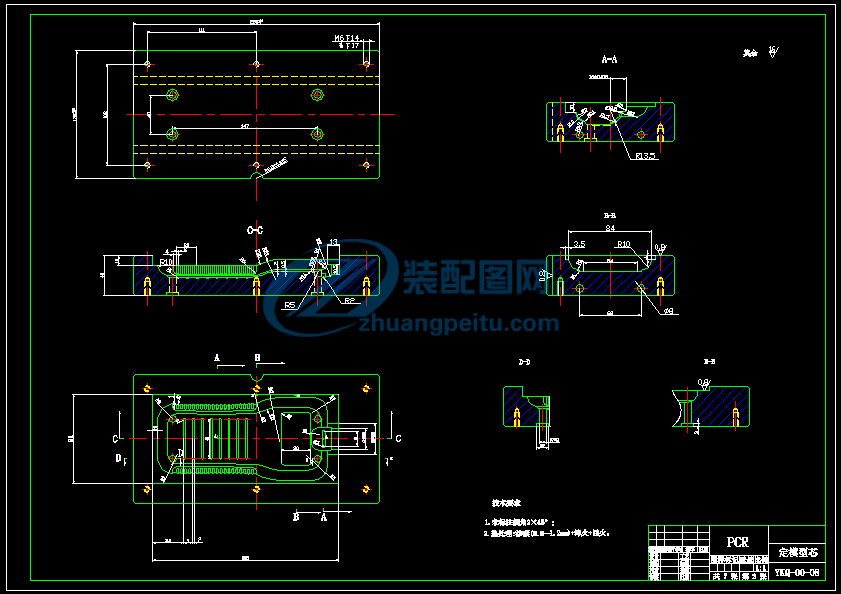
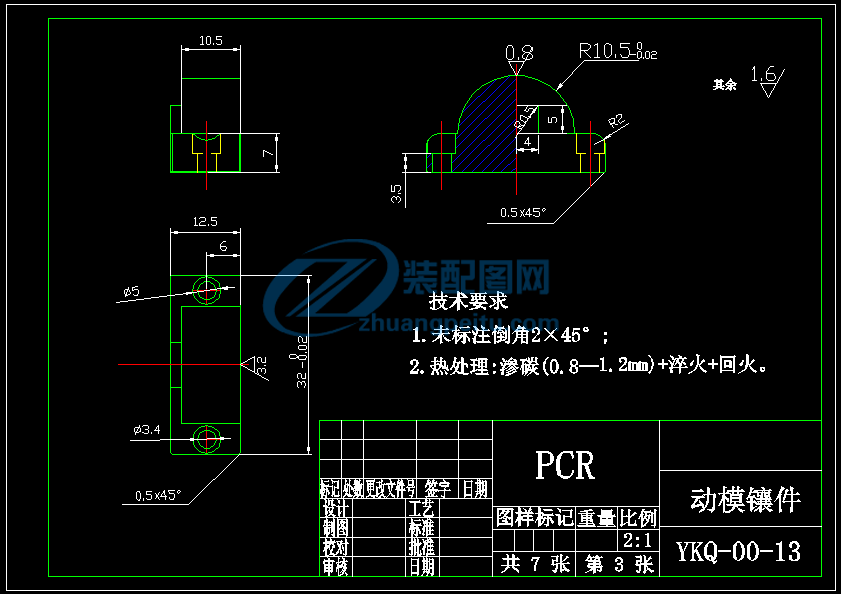
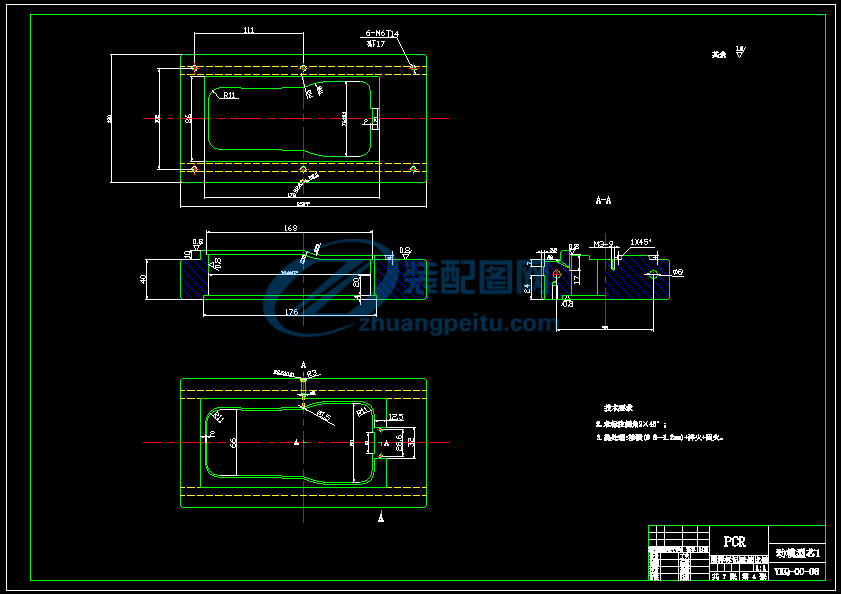
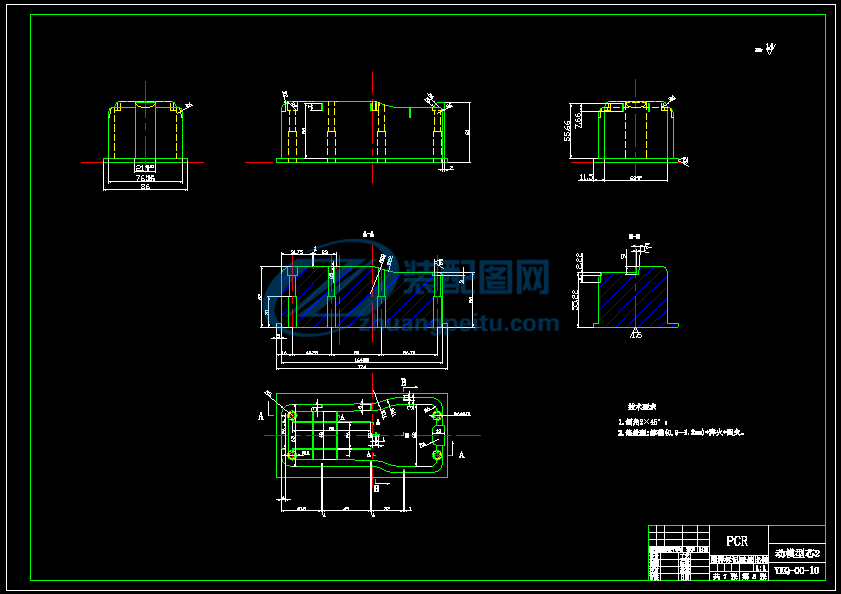
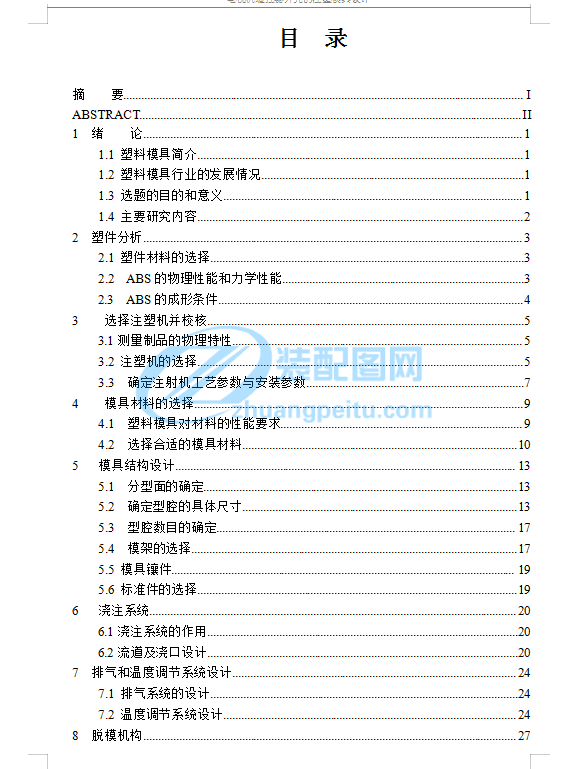
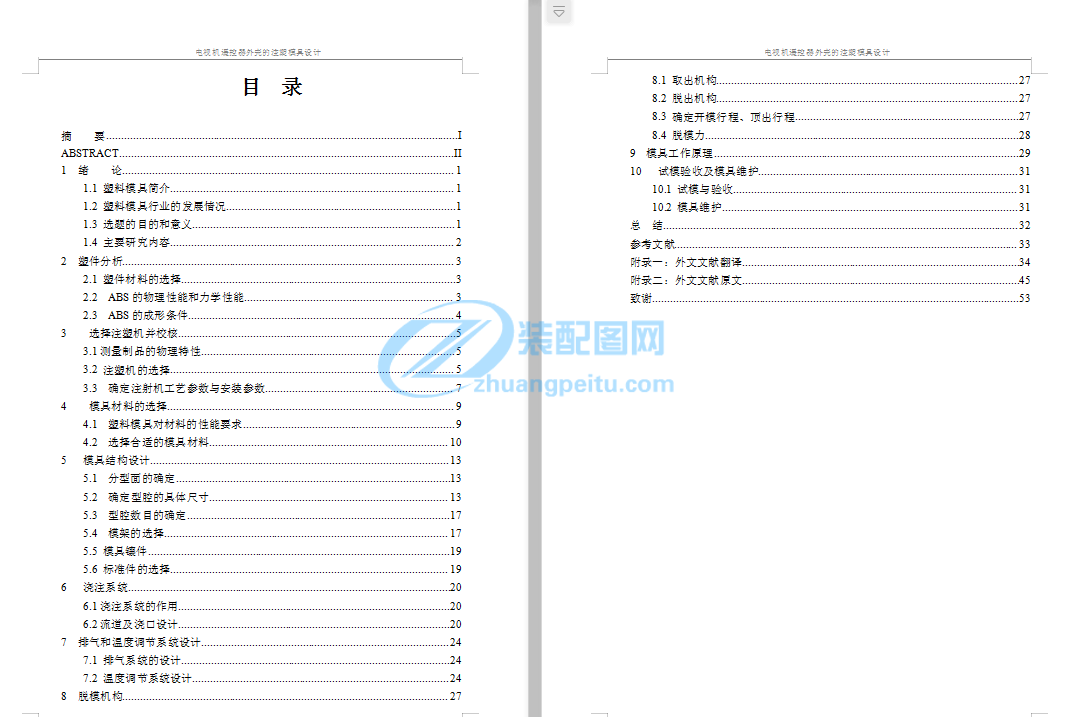

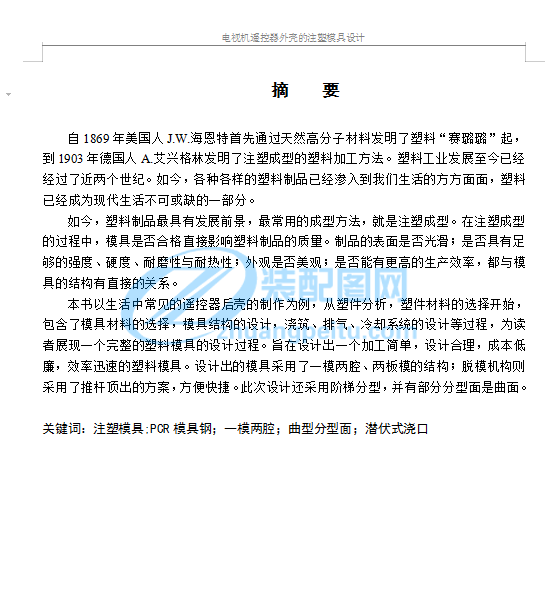
壓縮包內(nèi)含有CAD圖紙和說明書,咨詢Q 197216396 或 11970985
摘 要
自1869年美國人J.W.海恩特首先通過天然高分子材料發(fā)明了塑料“賽璐璐”起,到1903年德國人A.艾興格林發(fā)明了注塑成型的塑料加工方法。塑料工業(yè)發(fā)展至今已經(jīng)經(jīng)過了近兩個世紀。如今,各種各樣的塑料制品已經(jīng)滲入到我們生活的方方面面,塑料已經(jīng)成為現(xiàn)代生活不可或缺的一部分。
如今,塑料制品最具有發(fā)展前景,最常用的成型方法,就是注塑成型。在注塑成型的過程中,模具是否合格直接影響塑料制品的質(zhì)量。制品的表面是否光滑;是否具有足夠的強度、硬度、耐磨性與耐熱性;外觀是否美觀;是否能有更高的生產(chǎn)效率,都與模具的結(jié)構(gòu)有直接的關系。
本書以生活中常見的遙控器后殼的制作為例,從塑件分析,塑件材料的選擇開始,包含了模具材料的選擇,模具結(jié)構(gòu)的設計,澆筑、排氣、冷卻系統(tǒng)的設計等過程,為讀者展現(xiàn)一個完整的塑料模具的設計過程。旨在設計出一個加工簡單,設計合理,成本低廉,效率迅速的塑料模具。設計出的模具采用了一模兩腔、兩板模的結(jié)構(gòu);脫模機構(gòu)則采用了推桿頂出的方案,方便快捷。此次設計還采用階梯分型,并有部分分型面是曲面。
關鍵詞:注塑模具;PCR模具鋼;一模兩腔;曲型分型面;潛伏式澆口
ABSTRACT
Frpm 1869, J.W. Haunter from American has first invented the plastic "celluloid" through natural polymer materials, to 1903, A. Eichengreen from Germany invented the plastic injection molding process.the development of plastics industry has been going on for nearly two centuries. Nowadays, all kinds of plastic products have infiltrated into every aspect of our lives, and plastic has become an indispensable part of modern life.
Today, injection molding has become the most promising and most commonly used molding method for plastic products. In the process of injection molding, whether the mold is qualified directly affects the quality of plastic products. Whether the surface of the product is smooth; Whether it has sufficient strength, hardness, wear resistance and heat resistance; Whether the appearance is beautiful; Whether can have higher productivity, have direct relation with the structure of mold.
This book of life common after the remote shell as an example, from the plastic analysis, the choice of plastics materials, contains the mold material selection, mold structure design, casting, exhaust, cooling system design process, such as for the reader to show a complete design process of plastic mold. This book was aimed to design a plastic mould with simple processing, reasonable design, low cost and quick efficiency. The design of the mold adopted a two-cavity, two-plate mold structure; The ejection mechanism adopts the scheme of push rod, which is convenient and quick. The design also adopts the ladder parting, and the partial parting surface is the surface.
Key words: Injection mold; PCR mold steel; Two lumens; Curved parting surface; Latent gate.
III
目 錄
摘 要 I
ABSTRACT II
1 緒 論 1
1.1 塑料模具簡介 1
1.2 塑料模具行業(yè)的發(fā)展情況 1
1.3 選題的目的和意義 1
1.4 主要研究內(nèi)容 2
2 塑件分析 3
2.1 塑件材料的選擇 3
2.2 ABS的物理性能和力學性能 3
2.3 ABS的成形條件 4
3 選擇注塑機并校核 5
3.1測量制品的物理特性 5
3.2 注塑機的選擇 5
3.3 確定注射機工藝參數(shù)與安裝參數(shù) 7
4 模具材料的選擇 9
4.1 塑料模具對材料的性能要求 9
4.2 選擇合適的模具材料 10
5 模具結(jié)構(gòu)設計 13
5.1 分型面的確定 13
5.2 確定型腔的具體尺寸 13
5.3 型腔數(shù)目的確定 17
5.4 模架的選擇 17
5.5 模具鑲件 19
5.6 標準件的選擇 19
6 澆注系統(tǒng) 20
6.1澆注系統(tǒng)的作用 20
6.2流道及澆口設計 20
7 排氣和溫度調(diào)節(jié)系統(tǒng)設計 24
7.1 排氣系統(tǒng)的設計 24
7.2 溫度調(diào)節(jié)系統(tǒng)設計 24
8 脫模機構(gòu) 27
8.1 取出機構(gòu) 27
8.2 脫出機構(gòu) 27
8.3 確定開模行程、頂出行程 27
8.4 脫模力 28
9 模具工作原理 29
10 試模驗收及模具維護 31
10.1 試模與驗收 31
10.2 模具維護 31
總 結(jié) 32
參考文獻 33
附錄一:外文文獻翻譯 34
附錄二:外文文獻原文 45
致謝 53
1 緒 論
1.1 塑料模具簡介
塑料成型模具又稱塑料模,是指在高分子材料加工時用于塑料制品成型的模具。在現(xiàn)今高分子材料加工領域中,塑料模的優(yōu)化設計是十分重要的一部分。
在塑料制品的生產(chǎn)過程中,塑料模具設計對產(chǎn)品的品質(zhì)與產(chǎn)量都起著至關重要的作用。尤其當加工工藝、制品材料與制品結(jié)構(gòu)都已經(jīng)確定時,模具設計的重要性尤為明顯。例如,制品的尺寸、形狀精度;內(nèi)應力的高低;制品表面的質(zhì)量和物理力學性能等指標,均會受到模具的模腔、流道尺寸;分型面、進澆與排氣位置不同;脫模方式的選擇以及表面粗糙度等因素的影響。而且,制品加工時,操作的是否復雜也在很大程度上受塑料模具的結(jié)構(gòu)是否合理影響。另外,制品成本高低也在一定程度上受塑料模具的影響。一般情況下,制模的費用是非常高的;只有少量的簡易模具的制作成本較低。
所以,只有在裝上可以自動生產(chǎn)的模具的前提下,全自動化的高效設備才能將它的作用最大化的發(fā)揮出來。而且模具結(jié)構(gòu)的更新也是塑料制品更新的前提。由此可見,在實現(xiàn)塑料制品的加工工藝、使用要求、和外觀造型要求上,合理的塑料模具起著舉足輕重的作用。因此有人戲稱,塑料制品成型技術的“三大支柱”,就是先進的模具、高效率的設備以及合理的加工工藝。
1.2 塑料模具行業(yè)的發(fā)展情況
如今,國外的塑料模具先進水平還是在很大程度上領先于我國的。例如在模具材料方面,國外的專用塑料模具鋼的品種多于我國,規(guī)格也較全,質(zhì)量水平也相較我國更加穩(wěn)定。
同時也應該看到我國在塑料模具領域的進步。例如,我國已經(jīng)大規(guī)模地開發(fā)了塑料模具的各種設計和制造技術,同時CAPP、CAD等技術的應用也得到了大規(guī)模的普及??梢哉f,近幾年塑料模具在我國的發(fā)展非常迅速。
我國在2001年11月28日至12月1日派出代表團參加了EuroMold 2001模具技術展覽會。在展會上展示了例如先進的加工設備與軟件技術、激光焊接與檢測技術、無模成形與快速成形技術以及各種國外先進的模具技術等各種國外先進的模具技術。使我國深切的認識到我國的模具工業(yè)與世界先進水平的差距。我國也制定了明確的目標,大力發(fā)展我國的塑料模具領域。
1.3 選題的目的和意義
隨著當今社會的經(jīng)濟發(fā)展,人民的生活水平越來越高,電子產(chǎn)品已經(jīng)成為人民生活中不可或缺的一部分。而人們的需求也隨之多樣化。因此在現(xiàn)代的電子產(chǎn)品設計過程中,人性化設計也是設計人員的一個重要目標,因此遙控器的出現(xiàn)也就不足為奇了,而遙控器日益多變的結(jié)構(gòu)和形狀,也對模具結(jié)構(gòu)提出了更高的要求,作為一名機械專業(yè)的畢業(yè)生,在經(jīng)過對自身能力與模具工業(yè)的發(fā)展情況的綜合考慮之后,在老師的建議下,我選擇了《電視機遙控器外殼的注塑模具設計》作為我的畢業(yè)設計。希望我能運用我所學的知識,盡可能利用最簡單的模具來注出人們滿意的遙控器。
1.4 主要研究內(nèi)容
① 塑件材料的選擇
② 注塑機的選擇及參數(shù)校核
③ 模具材料選擇和模具機構(gòu)設計
④ 澆注系統(tǒng)設計
⑤ 試模驗收及模具維護
2 塑件分析
2.1 塑件材料的選擇
本次設計為電視機遙控器外殼的注塑模具,要求制品要有足夠的強度來保護內(nèi)部的元件,還應有一定的耐磨性,表面要光滑美觀等。考慮制品需要滿足的各項指標后,計劃選用ABS材料作為制品的材料。ABS材料的主要特性如下:
① 較高的強度和韌性,可有效地防止因碰撞引起的開裂。
② 具有較高的硬度和熱穩(wěn)定性,可保證在各種環(huán)境下可正常使用。
③ 具有良好的耐腐蝕性和絕緣性。
④ 價格低廉。
⑤ 易與有機玻璃熔接,易對其進行機械加工。
2.2 ABS的物理性能和力學性能
2.2.1 ABS的物理性能
①計算收縮率:0.3~0.8%;
②吸水率(24小時):0.2~0.4%;
③密度: 1.02~1.16g/cm3;
④比體積:0.86~0.98cm3/g。
2.2.2 ABS的力學性能
①抗剪強度: 24Mpa;
②彎曲彈性模量: 1.4Gpa;
③斷裂伸長率: 35%;
④屈服強度: 50Mpa;
⑤抗彎強度: 80Mpa;
⑥抗壓強度: 53Mpa;
⑦抗拉強度: 38Mpa;
⑧拉伸彈性模量: 1.8Gpa;
⑨沖擊韌度(無缺口):261 KJ/m2;
(有缺口):11 KJ/m2 ;
2.3 ABS的成形條件
① 預熱: 80—85℃, 2—3h;
② 料筒溫度: 后段: 150—170℃;
中段: 165—180℃;
前段: 18—200℃;
③噴嘴溫度: 170—180℃;
④模具溫度: 50--80 ℃;
⑤注射壓力: 60—100PMa;
⑥成型時間: 成型時間: 20—90s;
保壓時間: 0—5s ;
冷卻時間: 20—120s;
總周期: 50—220s ;
⑧螺桿轉(zhuǎn)速: 30r/min;
⑨后處理: 方式: 紅外線燈、烘箱;
溫度: 70度;
時間: 2—3小時。
3 選擇注塑機并校核
3.1測量制品的物理特性
塑件使用ABS材料制作,其相關性能可通過查手冊得知。
ABS收縮率: 0.3% - 0.8%
ABS密度: 1.09g/ cm3
ABS平均收縮率: 0.55%
對塑件進行三維建模,再用PRO.E測量其體積,測得塑件體積Vs=45 cm3,則塑件質(zhì)量可通過下式計算:
Ms=ρV=1.09×45=49.05g (3-1)
式中:ρ—塑料密度,單位是g/cm
3.2 注塑機的選擇
3.2.1 注塑機的分類
1.按注塑機成形能力分類
①超小型注塑機:合模力 < 160KN;理論注射量 < 16cm3。
②小型注塑機:合模力為160~2000KN;理論注射量16~630cm3。
③中型注塑機:合模力2000~4000KN;理論注射量800~3150 cm3。
④大型注塑機:合模力5000~12500KN;理論注射量4000~10000 cm3。
⑤超大型注塑機:合模力>16000KN;理論注射量>16000 cm3。
2.按塑化方法分類
通常情況下,注塑機按塑化方法可分為柱塞式注塑機和螺桿式注塑機兩大類。它們的優(yōu)缺點對比見表3.1。
表3.1柱塞式與螺桿式注塑機優(yōu)缺點對比
3.按外形結(jié)構(gòu)特征分類
塑料制品生產(chǎn)過程中,制品的工藝、生產(chǎn)的效率以及模具的設計都會受到注塑機的外形結(jié)構(gòu)的影響。按照注塑機的外形結(jié)構(gòu)特征,一般可以將其分為三類:
⑴立式注塑機 合模裝置的軸線與注射裝置的周線重合,并且垂直于地面即為立式注塑機。它的優(yōu)點是占地面積相較于其他兩種注塑機較小,而且模具的拆裝也相對更加容易、從而使嵌件的安裝更加方便、物料也能更加均勻的倒入料筒之中。但是立式注塑機也有一定的缺陷,主要表現(xiàn)在它的結(jié)構(gòu)不利于使操作更加機械化和自動化,它需要專門的工人在其推出制品后將模具取出,也會影響制品的生產(chǎn)效率。而且其機身較高,這就要求其生產(chǎn)空間要有合適的高度,另外其立式結(jié)構(gòu)也導致了它的穩(wěn)定性較差,原料不易補充等缺陷。故一般只有在生產(chǎn)注射量低于60cm3的制品時才會選用立式注塑機。
⑵臥式注塑機 注射和定模裝置置于設備的其中一側(cè),動模安裝板與合模裝置以及推出機構(gòu)置于設備的另一側(cè)即為臥式注塑機。臥式注塑機是應用最普遍的一種形式。其優(yōu)點主要為機器的高度較低,操作和原料的補充都較為方便,而且相對于立式注塑機,它的在推出制品后制品會自行落下,方便對其進行機械化操作,一般用于注射量較大的注塑機之中。其缺點主要是它的占地面積較大、不易于拆裝模具與安放嵌件。
⑶直角式注塑機 合模裝置的軸線垂直于注射裝置的軸線即為直角式注塑機。它的使用和安裝特點介于上述兩類注塑機之間,在生產(chǎn)一些小型塑料制品時,有些要求中心部分不允許留有澆口痕跡,這時就應使用直角式注塑機。
3.2.2 注塑機型號的確定
綜上所述,決定選用螺桿式、臥式注塑機。并據(jù)此確定注塑機的型號為SZG500/1500。其主要技術參數(shù)如下:
鎖模力: 1.5X106N;
注塑壓強: 193MPa;
螺桿轉(zhuǎn)速: 10~130r/min;
理論注射容量: 350cm3;
螺桿半徑: 22.5mm;
拉桿內(nèi)間距: 410X410mm;
最小模具厚度: 760mm;
噴嘴球直徑: φ39mm;
模具定位孔半徑: 80mm;
模具最大厚度: 400mm;
移模行程: 360mm。
3.3 確定注射機工藝參數(shù)與安裝參數(shù)
3.3.1 計算工藝參數(shù)
⑴ 計算注射量
最大注射容積為:
(3-2)
經(jīng)計算得最大注射質(zhì)量:
(3-3)
式中 ——流道與模具型腔的最大容量;
——模具中制品和凝料的最大質(zhì)量;
——分別為注射系數(shù);
——塑料的固態(tài)密度;
——注塑機的注射容積;
由前面的計算結(jié)果可知,塑件質(zhì)量為49.05g,由于擬采用一模兩腔結(jié)構(gòu),所以成型塑件總質(zhì)量為49.052=98.1g,而注塑機的注射質(zhì)量為305.2g,遠遠大于此值,故經(jīng)校核注射量符合預期設計要求。
⑵ 計算鎖模力
鎖模力可通過下式計算:
(3-4)
式中 F —— 注塑機的額定鎖模力,KN;
A —— 制品和流道在分型面上的投影面積之和,cm2;
—— 型腔的平均計算壓力,MPa;
K —— 安全系數(shù),通常取K=1.1~1.2。此處取1.05。
代入數(shù)據(jù),即:
而注塑機的額定鎖模力F=1500KN,顯而易見,該注塑機也滿足鎖模力的要求。
3.3.2 確定安裝參數(shù)
安裝參數(shù)即確保注塑機在模具上進行固定,并且在模具工作時保持穩(wěn)定,并能合理工作,完成預定任務的指標。其中包括螺孔尺寸、定位圈尺寸、噴嘴尺寸、模厚范圍等,其中,由于本次設計的塑件尺寸較小,所以模具尺寸也較小,故采用壓板即可順利固定,不需螺紋固定,故不需再做螺孔尺寸的計算。
同時其他幾項參數(shù)在模具設計與注塑機選擇時就已經(jīng)考慮到各項參數(shù)的影響,也不需再次計算。
3.3.3 推出機構(gòu)
要確定推出機構(gòu)是否符合要求需要將注塑機的最大開模行程與模具的脫模行程相比較,最大開模行程要大于模具的脫模行程才能符合設計要求。由上文可知本次所選注塑機的最大行程為360mm,而模具的脫模行程需要在后面模具設計時進行詳細的計算,故在此不做贅述。
4 模具材料的選擇
4.1 塑料模具對材料的性能要求
一般情況下,只有用剛作為材料,才能充分地保證模具的使用壽命。只有在充分考慮合金的成分與含量會對模具的性能產(chǎn)生的影響,并且保證存在相應的化學構(gòu)成使其符合相關要求的前提下,才能準確地在生產(chǎn)商提供的明細表中選擇出符合要求的鋼材。而不同的元素組成也會產(chǎn)生不同的反應,通常,鋼材應滿足的條件有
① 生產(chǎn)具有經(jīng)濟性(機械加工、放電加工、磨光、腐蝕和滾壓);
② 允許進行熱處理;
③ 有足夠的剛度和強度;
④ 抗熱和抗磨損能力;
⑤ 良好的熱傳導性及抗腐蝕性。
這些性能主要表現(xiàn)為以下幾個方面:
4.1.1 塑料模具對材料使用性能的要求
(1) 強度和硬度
塑料注射成形壓力通常在39—196MPa之間,閉模壓力一般為注射壓力的1.5—2倍,有時高達4倍左右,為了使塑料模具在使用中不變形,塑料模具用材應具有一定的強度。
作為遙控器的后殼,要求其能在承受一定沖擊力的情況下仍能保持其形狀不能發(fā)生太大變化,同時要保證在一定的彈性形變下不發(fā)生開裂現(xiàn)象,這就要求材料必須要有足夠的硬度。
(2) 韌性
在合理使用過程中,為保證模具不會出現(xiàn)開裂現(xiàn)象,韌性是一項非常重要的參數(shù)。
(3) 耐熱性
如今高速機械的應用越來越普遍,塑料產(chǎn)品的生產(chǎn)效率也愈加增快。因為模具的使用環(huán)境溫度會在20-350攝氏度之間頻繁波動,若塑料沒有足夠的流動性,模具的局部會在高速成形時經(jīng)受超過400攝氏度的高溫。因此,要求塑料模具材料的基體組織在這樣的高溫條件下也不會變化,同時它的強度也不能下降。
所謂耐熱性,包括高溫強度和抗氧化能力兩個方面,對于塑料模具的服役溫度來說,鋼、鋁合金、銅合金和鋅基合金的氧化是不成問題的,關鍵是材料的高溫強度。
(4) 尺寸穩(wěn)定性
在長期使用的條件下,模具的尺寸穩(wěn)定性對保證制品的精度非常重要。這就要求模具材料不僅要有充足的剛度,還應該保證具有足夠低的熱膨脹系數(shù)。
(5) 導熱性
為了提高制品生產(chǎn)的效率,模具應能使塑料在模具中盡快冷卻,這就要求模具材料應有良好的耐熱性。
4.1.2 塑料模具對材料加工性能的要求
⑴ 切削加工性
對模具材料進行加工時的難易程度即為切削加工性。是否易于切削加工會因不同的加工方法產(chǎn)生變化。通常用來衡量材料的切削加工性的指標有刀具耐用程度、加工質(zhì)量、單位切削力和斷屑性能。
⑵ 塑性加工性
一般用塑性加工方法來加工一些較小的多腔模。所以,在設計凹模和凸模時,需注意選用塑性加工性能比較好的塑模材料。
⑶ 電加工性
如今在模具的制造過程中,面對一些復雜形狀的零部件,經(jīng)常用到電加工方式(如電火花和線切割),所以材料應有良好的電加工性。
⑷ 熱處理性能
模具材料的熱處理性能也是塑料模具性能的一個非常重要的影響因素,它主要要求較小的淬透性、淬硬性以及熱處理變形。
⑸ 其它
此外,良好的可焊性、表面處理性能、鏡面加工性能等參數(shù)也在模具材料的指標范圍內(nèi)。
4.2 選擇合適的模具材料
為模具的制造選擇合適的材料可以按如下的幾個方法選擇:
⑴ 根據(jù)服役條件選擇
例如,在高溫的生產(chǎn)條件下制作ABS材料或者聚氯乙烯材料的塑料制品時,這些材料會產(chǎn)生腐蝕性氣體損壞模具,這時模具材料就要有良好的耐腐蝕性,或者在模具制作時應對材料做出相應的處理(如鍍鉻)以增加其耐腐蝕性。
在一些制作特殊的塑料制品時,會在材料中加入一些添加物,這些添加物可能會造成塑料的流動性降低,同時添加物本身的硬度也較高,這種情況下就極其容易磨損模具。這時就要求模具材料有較高的硬度。
根據(jù)塑料的種類不同,模具材料可根據(jù)表4.1來進行選用。
⑵ 根據(jù)加工方法選擇
⑶ 根據(jù)制品的質(zhì)量要求選擇
⑷ 根據(jù)塑料制品的預定產(chǎn)量選擇(見表4.2)
由于此次設計中塑件材料為ABS,正如上面所說,它會在成型過程中對模具產(chǎn)生腐蝕,因此要選擇耐腐蝕模具鋼來制作模具,根據(jù)表4.1和表4.2,預定使用PCR模具鋼來作為制作本次模具的主要材料,即用PCR模具鋼來制作模具的凸模和凹模部分,這令部分也是模具的最主要的部分。同時模具的其余零部件也要視具體情況選用不同材料,具體見下表。
5 模具結(jié)構(gòu)設計
5.1 分型面的確定
分型面的確定應考慮的因素有:
1. 分型面應設計在塑件的最大斷面處,這樣方便塑件脫模。
2.通常只設計一個分型面,且其方向應垂直于注塑機的開模方向。
3.一般情況下分型面應盡量使塑件在開模后與脫模機構(gòu)位于同一側(cè)。
圖5.1 塑件形狀示意圖
根據(jù)上文分型面的選取原則,同時考慮到塑件的結(jié)構(gòu)中有較多的曲面結(jié)構(gòu),并且含有一些斜面和厚度變化銜接,故選擇塑件的最大截面(曲面)作為分型面。
5.2 確定型腔的具體尺寸
綜合考慮各項因素后,本次設計的模具型腔采用階梯分型面的結(jié)構(gòu),并使用組合式型芯。因為這樣可以方便塑件的各種較為復雜的曲面結(jié)構(gòu),同時兼顧其厚度的突變。型腔的具體結(jié)構(gòu)如下圖5.2和圖5.3所示。
圖5.2 定模型芯1結(jié)構(gòu)
圖5.3 動模型芯2結(jié)構(gòu)
5.2.1 型腔壓力估算
型腔壓力估算公式為:
(5-1)
式中 ——型腔壓力,MPa;
——注射壓力,MPa;
——熔體流過注射機噴嘴的壓力變化,MPa;
——熔體流過澆注系統(tǒng)的壓力變化,MPa;
經(jīng)過估算,得出型腔的壓力約為30MPa。
5.2.2 型腔壁厚的計算
如今一般采用按強度計算或者按剛度計算兩種方法來計算塑料模具的側(cè)壁和底壁的厚度。這兩項參數(shù)的計算在模具設計中也是非常重要的問題。
模具型腔在制品注射并成型時,會在溶體的壓力作用下產(chǎn)生內(nèi)應力并發(fā)生變形。一旦內(nèi)應力超過模具材料的許用應力,會使型腔內(nèi)部被破壞,而且材料的剛度不足以發(fā)生過大的彈性變形,還會使塑料溢出導致脫模困難,制品的精度也會受到影響。溶體的壓力也是模具在工作時受到的主要作用力。
然而,在實踐過程中,在塑料模具設計時,對于較小的型腔,它的主要問題是強度不夠,故應該按照強度標準進行計算,即材料要滿足在工作時的多種受力條件下的許用應力;而一些比較大的型腔主要面臨的問題時剛度是否足夠,這時就應該按照剛度的要求進行計算。按照剛度進行計算時要注意,首先要確保塑件的精度在工作時符合要求,同時要保證溶體在模具總不會溢出,即保證其彈性變形在要求范圍內(nèi),并且要盡量的使脫模方便。綜上所述,在實踐時并不一定要同時兼顧強度和剛度的計算。
本塑件尺寸較小,強度問題是其主要面對的問題,所以應按照塑件的強度要求進行計算。只要確保材料的許用應力大于在模具工作時型腔內(nèi)的應力即可。
通常許用應力為 [σ]=1/2σs(MPa)
其中σs為材料的屈服極限,σs=1100MPa。
[σ]=550MPa
為了計算方便,在計算凹模體積時,可以將其轉(zhuǎn)化為方便計算的矩形來進行計算。經(jīng)計算其體積為:L×h×b=176×20×84mm3。
圖5-4 型腔壁厚示意圖
側(cè)壁的計算:
(5-2)
式中:PM —模腔壓力,MPa;
E—材料的彈性模量,MPa;
μ—材料的泊松比;
σp—材料的許用應力,MPa;
模腔壓力大概30MPa。材料的許用應力經(jīng)過計算得到550 MPa
凹模型腔的深度為20mm
系數(shù)a通過下表選取:
表5.1 系數(shù)a的選取
L/h
0.25
0.50
0.75
1.0
1.5
3.0
a
0.02
0.081
0.173
0.321
0.727
2.105
L取176mm,
h取20mm.
L/h=176/20=8.8 所以系數(shù)a取2.105
mm
側(cè)壁最薄為6.78mm
底部壁厚的計算:
(5-3)
系數(shù)c可通過下表選?。?
表5.1 系數(shù)c的選取
L/b
1.0
1.2
1.4
1.6
2.0
∞
c
0.3078
0.3834
0.4356
0.4680
0.4974
0.5000
L取176mm,
b取84mm,
L/b=176/84≈2.1
c值取0.5000。
mm
所以凹底壁最薄為13.87mm.
凹腔底部厚度為17mm,滿足 17mm>mm.
根據(jù)以上計算設計定模型芯的最小側(cè)壁厚大小為:
23mm>mm;
故經(jīng)計算設計型腔的強度符合預期設計。
模具采用一模兩腔結(jié)構(gòu),兩個型腔之間的距離,如圖5-5。通常是根據(jù)經(jīng)驗值來取。
經(jīng)驗公式為
≥. (5-4)
≥11.5
模具的兩個型腔分別由兩個不同的型芯組成,所以大小滿足要求。
5.3 型腔數(shù)目的確定
由于遙控器外表面不允許出現(xiàn)澆口痕跡,所以此次設計選擇了潛伏式澆口。考慮到澆注系統(tǒng)的平衡性,初步確定采用一模兩腔、兩板模的模具結(jié)構(gòu)。又考慮到每一次的注射量必須小于注射機最大注射量的80%,即型腔數(shù)目應滿足下式的關系:
n < (0.8Vg-Vj)/Vs (5-5)
式中:Vg—注塑機最大注塑量cm3或g
Vj—澆注系統(tǒng)凝料量cm3或g
Vs—單個塑件的容積或質(zhì)量cm3或g
所以 n < (0.8×350-3)/(45×2)=3.1
所以對此模具,一模兩腔結(jié)構(gòu)符合要求。
5.4 模架的選擇
綜上所述,確定型腔(凹模)的
根據(jù)標準模架手冊(大水口系統(tǒng)),確定出本設計及所使用的模架型號為3540型模架,查表得其主要參數(shù)為:
面板規(guī)格: ,
動模板厚度: 60mm,
定模板厚度: 60mm,
吊環(huán)螺紋孔直徑: M20。
模架結(jié)構(gòu)如下圖所示。
圖5.6 a)
圖5.6 b)
圖5.6 模具結(jié)構(gòu)示意圖
5.5 模具鑲件
本次設計中,遙控器尾部成型由定模型芯,頭部則成型于動模型芯成型。同時為了保證型腔的工藝性能,一般在模具設計時會加入鑲件,本模具中有二種鑲件結(jié)構(gòu),分別位于定模、動模上。其結(jié)構(gòu)如圖5.7所示。
a)動模鑲件
b)定模鑲件
圖5.7 鑲件結(jié)構(gòu)示意圖
根據(jù)本次設計的模具結(jié)構(gòu),模具一共需要10個鑲件,其中定模鑲件8個,動模鑲件2個。它們的具體的裝配位置在裝配圖體現(xiàn)。
5.6 標準件的選擇
模具的標準件可通過查閱《盤起標準件手冊》來選取。具體所選的標準件種類、規(guī)格、數(shù)量、裝配情況見裝配圖。
6 澆注系統(tǒng)
6.1澆注系統(tǒng)的作用
澆注系統(tǒng)分為主流道、分流道、澆口和冷料穴四部分,是指溶體自注塑機碰觸后流向模腔的通道。設計澆注系統(tǒng)時應遵循如下原則:
⑴ 綜合考慮型腔的布局,盡量選用平衡式分流道。
⑵ 為了使壓力損失與沖模時間最大化的減少,應使塑料的流程盡量短。
⑶ 澆口尺寸、位置和數(shù)量選擇應有利于熔體流動,并有利于排氣和原材料的補充。
⑷ 盡量減少溶體對模具型腔和嵌件的沖擊,以免發(fā)生變形或者位移。
⑸ 設計應使凝料與制品分開方便,或者使其方便切削。
⑹ 合理的選擇熔接痕的部位與形態(tài)。
⑺ 澆注系統(tǒng)的內(nèi)表面應保證合適的硬度與精度,尤其澆口處要保證合適的表面粗糙度。
⑻ 還要考慮到冷卻過程對澆注系統(tǒng)的影響。
⑼ 模板中心和主流道中心之間的距離要盡量縮小,條件允許的話二者要重合。
6.2流道及澆口設計
6.2.1 流道設計
6.2.1.1 主流道設計
自注射計的噴嘴開始到第一個分流道的這一段,叫做主流道。在模具工作時,主流道是溶體首先經(jīng)過的部分,它的各項指標直接影響制品的生產(chǎn)效率與制品質(zhì)量。其截面為圓形,截面面積的大小尤為重要。若截面面積過大,則模具中的壓力過小,容易產(chǎn)生氣泡,影響制品質(zhì)量;也不利于溶體的冷卻,延長冷卻時間,拖慢了制作效率;同時也在一定程度上加重了材料的浪費。若截面面積過小,則會加劇模具中的壓力浪費,還會使注射時間加長,熱量損失加重,影響制品質(zhì)量。
主流道形狀并不是圓形,而是設計成內(nèi)壁光滑,半錐角為1°的圓錐形。這種結(jié)構(gòu)可以時溶體冷卻凝固后更易于取出。其小端直徑,長取4~8。主流道大端處應呈的圓角,以減小料流轉(zhuǎn)向過渡時的阻力。襯套的球形凹坑深度常取,并且其半徑應滿足下式:
(6-1)
為了保護主流道在高溫環(huán)境下與注塑機的噴嘴碰撞損壞,一般情況下主流道會被設計成可拆卸的結(jié)構(gòu),稱作澆口套。由于主流道在穿過不同的模板使可能會由于精度不足等問題發(fā)生溢料等風險,所以也應設計成可拆卸的澆口套結(jié)構(gòu),澆口套的主要作用是:
1)有利于模具與注塑機更合理的連接,也保證不同模具零件的連接處不發(fā)生因裝配或精度問題引起的溢料或氣泡問題。
2)主流道作為澆注系統(tǒng)的一部分,要確保溶體合理完全的注入型腔,同時保證制品的品質(zhì),本身也應該拆卸方便。
澆口套的設計過程通常通過選取標準件來取代,由于注塑機噴嘴球半徑為18.5mm,根據(jù)以上要求,選取進料口半徑為20mm的澆口套,如圖6-1所示。
圖6.1 一般注塑機配對模具的主流道結(jié)構(gòu)圖
6.2.1.2 分流道設計
主流道與模具型腔之間的流道成為分流道,分流道是保證溶體順利流入型腔的關鍵,合理的分流道設計應使溶體在澆注系統(tǒng)中合理的分流轉(zhuǎn)向,順利地流入各個型腔并且保持合適的溫度和粘性,從而保證得到符合設計要求的制品。
1.分流道的截面形狀
分流道的截面形狀并不一定為圓形,而是根據(jù)設計要求的不同會有各種形狀,常見的分流道截面形狀有圓形、正方形、U型、正六邊形、梯形等。若要盡量增大其受熱面積,則應選用正方形截面;若要求盡量節(jié)省壓力損失,則圓形截面最能符合要求;若要考慮加工的方便快捷,則可以選用U型或者梯形截面。而在本次設計中,選擇半圓面作為分流道地截面形狀。
圖6.2 分流道直徑尺寸曲線
2.分流道的截面尺寸
在設計塑料模具分流道的尺寸時,主要考慮的影響因素有塑件的體積、塑件壁厚、分流道長度、所用塑料工藝特性、塑件形狀、注射速率等。截面尺寸過大,會使流道內(nèi)壓強過小,易混進空氣,產(chǎn)生氣泡,分流道截面過大,主流道截面就應更大,會造成材料損失;也不利于散熱冷卻,降低生產(chǎn)效率。截面尺寸不足,則會使流道內(nèi)壓力過大,對型腔的沖擊與摩擦過大造成磨損,同時與主流道之間的壓力差過大會損壞模具;注射時間過長,造成熔體溫度不足,流動性下降,造成壓力損失。
通常,當分流道截面為圓形時,其直徑一般根據(jù)制品要求不同在2-12mm之間選擇。就本次設計來看,所設計的模具分流道尺寸的選擇應綜合考慮塑件的材料、質(zhì)量。尺寸等因素后,由圖6-2所示的經(jīng)驗曲線來選定。
圖中從左至右分別為S=1,1.5,2,2.5,3,3.5,4,4.5,5所對應的曲線。S為制品壁厚。經(jīng)查圖可知,分流道直徑D=4.25mm。再查相關手冊可得修正系數(shù)=0.94,則分流道直徑經(jīng)修正后為 :
(6-2)
6.2.1.3 冷料穴與拉料桿設計
在注射間隔時會產(chǎn)生一些冷料頭,若冷料頭進入型腔會造成成品密度不均勻,影響制品質(zhì)量。設計冷料穴的作用就是放著這種情況發(fā)生
通常為了方便冷料流入,注塑機上的冷料穴的直徑應比主流道的直徑略大。注塑機為立式或者臥式時,冷料穴的位置一般都在主流道對面的動模上,也就是主流道的末端。若注塑機為直角式,一般以主流道的延長部分來作為冷料穴,也可以是分流道的延長部分。
綜合考慮各方面因素后,用于本次設計的模具選用的是倒錐形凹槽式的冷料穴。
6.2.2 澆口設計
在塑料模具中的澆注系統(tǒng)之中,分流道與模具型腔之間有一段狹窄部分,稱作澆口,也可以稱作進料口和內(nèi)流道。交口的作用主要是使溶體在進入型腔之前形成一個加速度,使塑料熔體迅速,全面的噴入型腔,不留氣泡,同時還可以保證熔體不會反向流出,起到控制方向的作用。澆口的設計也是塑件能否與流道中的材料順利分離的關鍵。
本次設計采用了潛伏式澆口,它的結(jié)構(gòu)如圖6.3所示。潛伏式澆口是由點澆口發(fā)展而來的,它除了具有點澆口的特點之外,由于他的澆筑點一般在塑件內(nèi)部,有利于形成光滑的外表面,也在冷卻后方便塑件與流道中的材料分離。
圖6.3 典型潛伏式澆口
7 排氣和溫度調(diào)節(jié)系統(tǒng)設計
7.1 排氣系統(tǒng)的設計
注塑機對模具進行注射時,必然會使流道和型腔內(nèi)的空氣被排出,若空氣沒有合理的排出,就會導致空氣排出不完全,產(chǎn)生氣泡甚至使塑件制品不完全,所以設計的排氣系統(tǒng)是否合理直接關系到模具是否能合理工作。設計合理的排氣系統(tǒng)的作用主要有:
⑴ 確保型腔被完全的緊密的充滿,降低熔體流動的阻力,保證塑件完整,棱邊清晰。
⑵ 保證塑件的力學性能,確保制品表面的光滑平整,不出現(xiàn)流動或熔接的痕跡。
⑶ 保證制品內(nèi)部充實完整,質(zhì)量達標,無氣泡、氣孔、剝層等缺陷。
⑷ 保證型腔內(nèi)的壓強與溫度合理穩(wěn)定,防止因氣體殘留導致壓強和溫度升高造成制品或模具的損壞。
⑸ 保證沖模速度,提高制品的生產(chǎn)效率。
在一些情況下,模具零部件之間的微小縫隙也可以起到排氣的作用。在制品尺寸較小,結(jié)構(gòu)較為簡單時,可在設計時將排氣口設置于分型面處,借助零件連接處的微小縫隙,也可以在保證排氣的同時保證塑件的質(zhì)量完好,方便了模具的生產(chǎn)加工。本次設計采用的是階梯分型面,而動模上的凸臺和定模上的凹槽的側(cè)面不是配合面,故也可以選用此種排氣方案設計。
7.2 溫度調(diào)節(jié)系統(tǒng)設計
在進行塑料制品的生產(chǎn)時,合理的控制溫度對制品的品質(zhì)起著至關重要的作用,而模具在塑料制品的生產(chǎn)過程中不僅僅起著定型作用,也在溫度的調(diào)節(jié)之中扮演著至關重要的角色。模具是否能合理的起溫度調(diào)節(jié)的作用直接影響著制品是否會發(fā)生變形,是否能保證要求的精度,是否有符合要求的表面質(zhì)量和力學性能。
通常溶體剛被注射到模具中時模具的溫度應保持在200度左右,而在冷卻后,溶體凝固取出前,模具內(nèi)的溫度應要降到60度左右,具體的材料溫度與模具溫度的選擇與制品的材料有關,可以通過表7.1查出具體的溫度。
模具的冷卻方式有風冷和水冷兩種方式,一般情況下采用最多的是水冷,即冷卻介質(zhì)是水。原因在于水的比熱容大,導熱性好,獲取方便。水冷可以在模具外或者型腔內(nèi)設置水道,使冷卻水不斷循環(huán)達到降低并保持溫度的作用。
表7.1 幾種塑料的成型溫度與模具溫度[4]
塑料名稱
塑料溫度/℃
模具溫度/℃
塑料名稱
塑料溫度/℃
模具溫度/℃
聚苯乙烯
200-250
40-60
醋酸纖維素
160-250
90-12
AS
200-260
40-60
硬聚氯乙烯
180-210
40-60
ABS
200-260
40-60
軟聚氯乙烯
170-190
45-60
塑料名稱
塑料溫度/℃
模具溫度/℃
塑料名稱
塑料溫度/℃
模具溫度/℃
丙烯酸樹脂
180-250
40-60
有機玻璃
220-270
45-60
聚乙烯
150-250
50-70
氯化聚醚
190-240
30-60
聚丙烯
160-260
40-60
聚苯醚
280-340
40-60
聚酰胺
200-300
55-65
聚砜
300-340
100-150
聚甲醛
180-220
80-120
PBT
250-270
60-80
聚碳酸酯
280-320
80-110
冷卻裝置有五種基本結(jié)構(gòu)形式,分別是簡單流道式、螺旋式、隔片導流式、噴流式和導熱桿及導熱型芯式。本模具設計選用簡單流道式作為冷卻裝置的結(jié)構(gòu),即在模具上直接打孔通水冷卻。本次設計采用了兩個并聯(lián)的循環(huán)通路對模具進行冷卻。冷卻系統(tǒng)的分布如圖7.1所示。
圖7.1 (a)
圖7.1 (b)
圖7.1 冷卻水道分布圖
8 脫模機構(gòu)
脫模分為兩個動作,分別是脫出和取出。脫出即在動模與定模分開后,先使制品與模具松動,方便取出。取出即將冷卻凝固的塑料成品從模具中取出。能否合理,快速的完成脫模動作是衡量脫模機構(gòu)時候設計合理的關鍵。
8.1 取出機構(gòu)
針對本次設計而言,最理想的取出方式是在制品脫出后,使制品能夠在重力作用下自行掉落,即制品自行完成取出動作。在第六章澆注系統(tǒng)設計中,采用的是潛伏式澆口設計,故塑件可以在脫出后在重力作用下自行取出。
8.2 脫出機構(gòu)
本次模具采用的是頂桿頂出的方案,具體設計結(jié)構(gòu)、尺寸及裝配形式見模具裝配圖。
8.3 確定開模行程、頂出行程
1. 頂出行程
頂出行程的估算公式為:
(8-1)
式中 —— 所需頂出行程,mm;
—— 型芯成型高度,mm;
—— 頂出行程富裕量,mm。
即
2. 開模行程
下式可以先對開模行程進行估算:
(8-2)
式中 —— 開模行程(mm);
—— 塑件及澆注系統(tǒng)在開模方向上的總投影高度,mm;
—— 動定模型芯突出分型面的高度總和,mm;
—— 取件及取出澆注系統(tǒng)凝料的開模行程富裕量,mm。
即
在實際操作時,還要根據(jù)實踐情況,合理的增減開模行程進行。
8.4 脫模力
脫模力為脫模機構(gòu)在使塑件脫出時需要的力的大小。力太小無法正常完成脫出動作,力過大會直接將模具頂出,甚至損壞模具。通過下式可先對脫模力進行估算:
(8-3)
式中 —— 脫模力(N);
—— 制品對型芯包緊的脫模阻力,N;
—— 使封閉殼體脫模需克服的真空吸力 ,N。
,這里0.1的單位為MPa,為型芯的橫截面積,mm2。
包緊力計算:
(8-4)
上式中 ——矩形型芯斷面的兩邊長度(mm);
E——塑料的拉身彈性模量(MPa);
——塑料的平均成形收縮率;
——塑料的泊松比;
——型芯脫模方向高度(mm);
——脫模斜度修正系數(shù);
——制品的計算系數(shù);
——比例系數(shù);
——制品壁厚(mm)。
計算出=649.5N,帶入式8-3得=3606.3N。另外,本模具結(jié)構(gòu)中有兩個型腔,所以實際的脫模力大約為。
9 模具工作原理
本此設計的塑件制品結(jié)構(gòu)較為簡單,故模具的動作與結(jié)構(gòu)較為簡單。主要結(jié)構(gòu)特點有兩塊模板,潛伏式澆口等。模具結(jié)構(gòu)如圖9.1所示。
圖9.1 模具結(jié)構(gòu)圖
1——頂桿Ⅰ 2——定模 3——動模
4——彈簧 5——復位桿 6——頂桿墊板
7——頂桿固定板 8——頂桿Ⅱ 9——導柱 10——頂模塊
注射過程完成后,經(jīng)過保壓和冷卻,模具在注射機的作用下開始分型。由于是兩板模,所以動模3、定模2直接分離,到達開模行程后,動模3停止運動,注射機頂出機構(gòu)開始動作,當螺桿接觸到定模塊10后,頂桿墊板6和頂桿固定板7開始推動頂桿1和推桿8運動。當它們的位移等于行程后,注塑機停止,操作人員將制品取出(由于是潛伏式澆口,所以凝料會在重力的作用下自動掉落)。頂出螺桿在經(jīng)過一段時間(一般為幾秒)的停留后快速退回,而頂桿墊板6和頂桿固定板7則在彈簧4的作用下回復到原位。
圖9.2 模具開模和頂出示意圖
上述動作完成后,注射機開始合模動作。合模過程中,導柱9起導向作用,當合模厚度等于預先調(diào)好的型厚值時,注射機停止動作,完成合模,全部動作結(jié)束,之后便開始下一次塑件的制作。
有關模具的開合模過程可參照圖9.1和圖9.2進行理解。
10 試模驗收及模具維護
10.1 試模與驗收
模具裝配完成后就要進行試模。在試模前,首先應再次檢查設計方案,檢查設計方案是否合理,計算是否正確,模具是否符合設計方案,同時要對制作出的模具進行仔細的檢查。檢查的內(nèi)容包括:
⑴ 模具的尺寸是否符合設計方案,注塑機的選擇是否符合條件。
⑵ 有無用于模具搬運的吊環(huán)。
⑶ 在模具搬運時是否設有鎖緊板來保證不會發(fā)生模具分開等緊急情況。
安裝好模具后也應該在一次驗算各種參數(shù),再次確定各項指標準確無誤。
10.2 模具維護
在模具的使用和維護過程中要做到:
① 合理安排操作規(guī)程,確保在安全前提下操作。
② 操作仔細,確保無人為操作失誤。
③ 愛護實用工具,嚴格按照工具的使用規(guī)程使用。
④ 操作過程中也要嚴格遵照操作規(guī)程進行。
⑤ 建立模具檔案。
總 結(jié)
本次設計包含了一個塑料模具的設計全過程,最終設計出了符合設計要求的注塑模具。本次設計出的注塑模具的特點是,采用一模兩腔結(jié)構(gòu),潛伏式澆口設計,有助于提高制品的質(zhì)量和提升制品的生產(chǎn)效率。
本次設計的主要內(nèi)容有塑件材料的選取、模具材料的選取、注塑機的選擇、模具結(jié)構(gòu)、澆注系統(tǒng)、排氣與溫控系統(tǒng)、脫模機構(gòu)的設計等過程。其中重點是注塑機的選擇、模具結(jié)構(gòu)和脫模機構(gòu)的設計。
注塑機主要根據(jù)塑件的大小和材料的特性來選擇,初步確定注塑機型號后要對注塑機的工藝參數(shù)、安裝參數(shù)與開模行程進行校核,確保注塑機能合格合理的完成工作。其中,注塑機的開模行程要在模具的脫模機構(gòu)設計完成后進行比較,保證注塑機的開模行程大于模具的需要開模行程。
模具結(jié)構(gòu)的設計中,重點是型腔尺寸、型腔壓力、型腔壁厚的計算,最終確定了一模兩腔的結(jié)構(gòu)。
澆注系統(tǒng)的設計重點在于主流道與分流道截面形狀的確定,截面尺寸的計算,流道結(jié)構(gòu)的設計、澆口設計等。為了保證塑件質(zhì)量采用了潛伏式澆口結(jié)構(gòu)。
總體而言,本次設計出的注塑模具結(jié)構(gòu)合理,同時結(jié)構(gòu)有所創(chuàng)新,鍛煉了自己的專業(yè)知識和實踐能力,達到了本次設計的初衷與要求。
我相信,本次畢業(yè)設計設計出的作品在將來的實踐生產(chǎn)值匯總會是一種出色的,各項性能處于相關同類型產(chǎn)品前列的作品。
總的來說,在這一次畢業(yè)設計中,我得到了眾多的寶貴的東西,不僅僅鞏固了我四年大學生活中學到的專業(yè)知識,還學習到了許多在校園里學不到的知識。而且,我還領悟到了許多做人的道理,相信這些收獲會是我在未來的發(fā)展之中的寶貴財富,會使我在將來擁有更加美好的未來。
參考文獻
[1]羅曉曄.塑料成型工藝與模具設計[M].浙江:浙江大學出版社,2008-1-1.
[2]王暉,李大成.模具拆裝及測繪實訓教程[M].重慶:重慶大學出版社,2007-10-01.
[3]胡曉楠.基于CAD/CAE的冰箱接水盒注塑模具設計[D].沈陽:東北大學,2008.
[4]譚國文.LED光學模具設計與分析[D].廣州:廣東工業(yè)大學,2014.
[5]吳宏獻.蛋糕該注塑模具的設計與制造[D].長沙:湖南大學,2013.
[6]宋滿倉.注塑模具設計[M].北京:電子工業(yè)出版社,2010:1-326.
[7]王加龍.熱塑性塑料注塑生產(chǎn)技術[M].北京:化學工業(yè)出版社.2004:1-195.
[4]李志剛.中國模具設計大典[M].南昌.第一版;李志剛,2003: 1-266.
[5]閆光榮和許鶴峰等譯.注射模具制造工程[M].北京.第一版;
GeorgMenges.Walter
,Michaeli.Paul.Mohren,2002:1-302.
[6]陳萬林等.實用塑料注射模設計與制造[M].北京.第一版;陳萬林等,2000:1-80.
[7]劉昌祺.塑料模具設計[M].北京.第一版;劉昌祺,2000:1-312.
[8]朱元吉等譯.模具工程[M].北京.第二版;H.瑞斯,2005:1-234.
[9]王永平.注塑模具設計經(jīng)驗點評[M].北京.第一版;王永平,2005:103-276.
[10]李大鑫,張秀棉.模具技術現(xiàn)狀與發(fā)展趨勢綜述[J].模具制造,2005,(02).
[11]趙昌盛,朱邦全.我國模具材料的應用發(fā)展[J].模具制造,2004,(11).
[12]朱鳴芳,于金,戴挺.金屬凝固過程數(shù)值模擬的最新進展——第10屆MCWASP國際學術會議論文述評[J].鑄造,2005,(02).
[13]朱先勇,劉耀輝,于思榮,鄂世舉,宋雨來.球墨鑄鐵模具的消失模制造技術及發(fā)展動態(tài)[J].鑄造,2006,(