【溫馨提示】壓縮包內(nèi)含CAD圖有下方大圖片預(yù)覽,下拉即可直觀呈現(xiàn)眼前查看、盡收眼底縱觀。打包內(nèi)容里dwg后綴的文件為CAD圖,可編輯,無水印,高清圖,壓縮包內(nèi)文檔可直接點(diǎn)開預(yù)覽,需要原稿請(qǐng)自助充值下載,所見才能所得,請(qǐng)見壓縮包內(nèi)的文件及下方預(yù)覽,請(qǐng)細(xì)心查看有疑問可以咨詢QQ:11970985或197216396
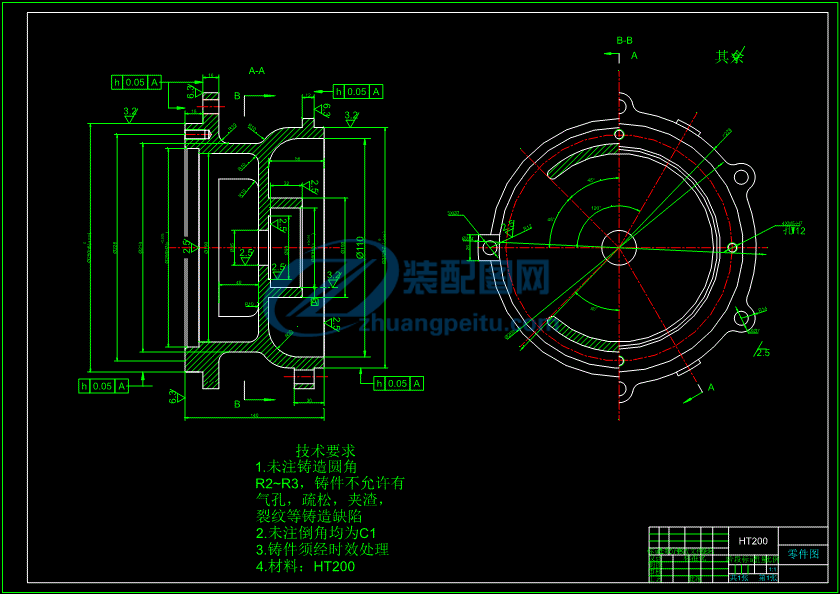
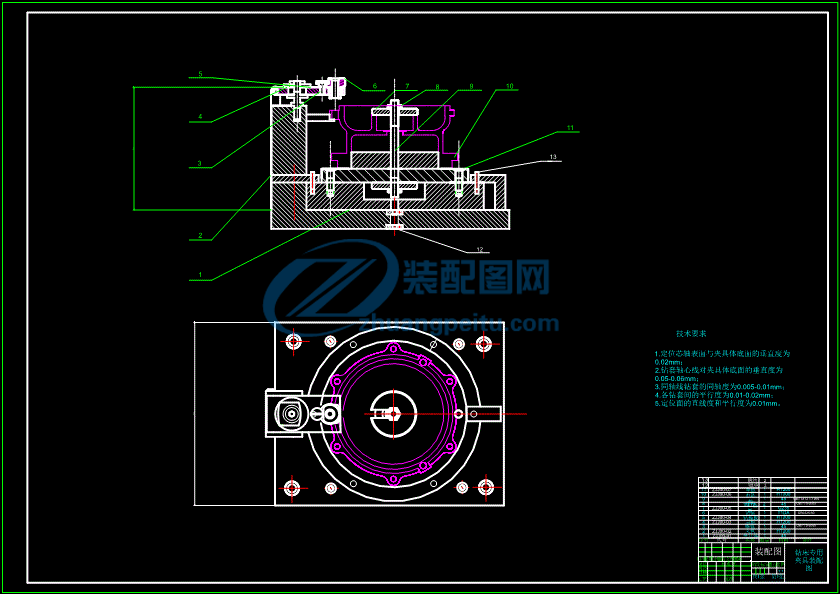
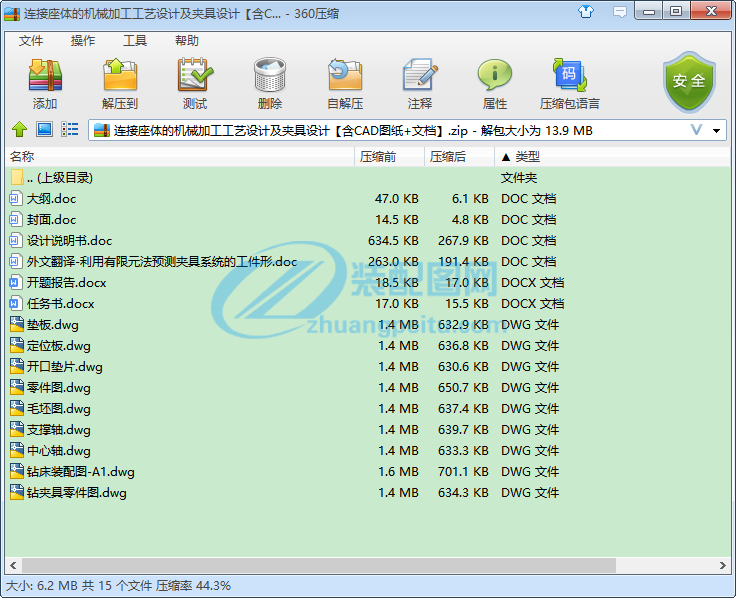
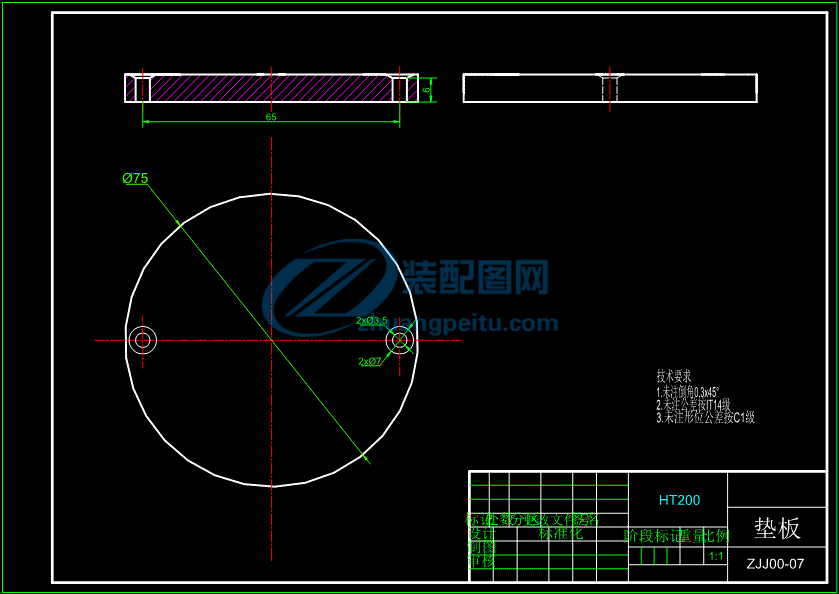
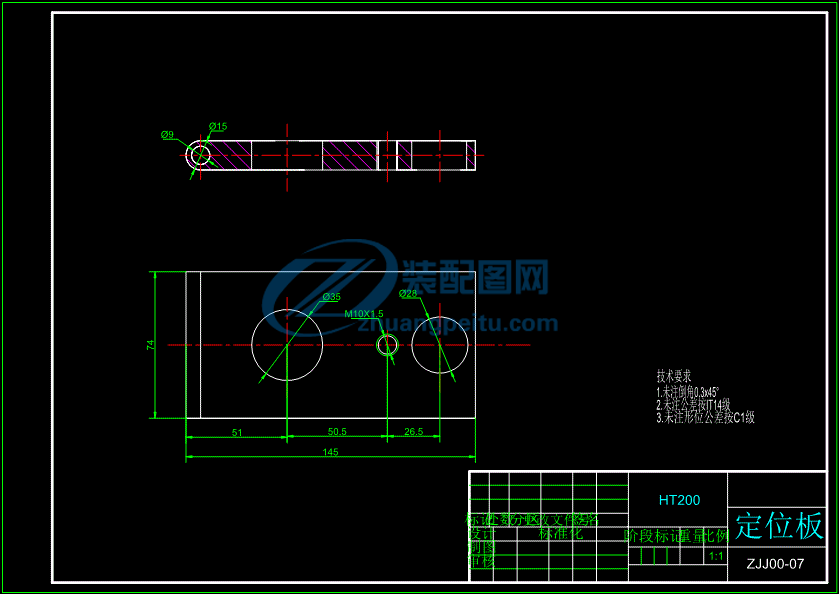
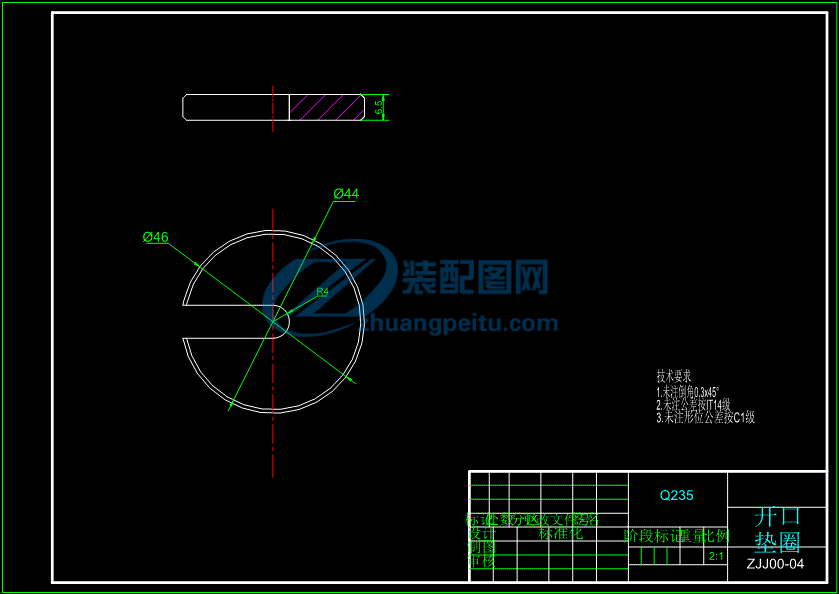
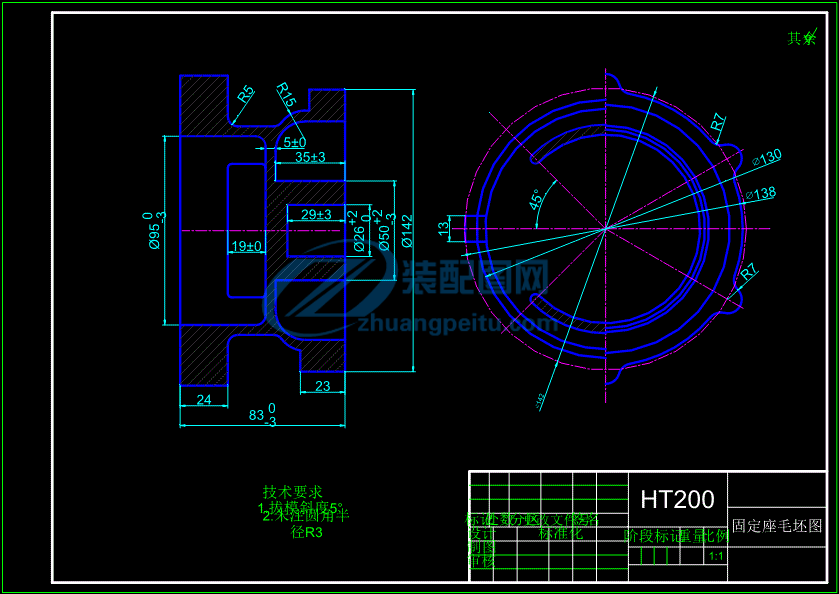
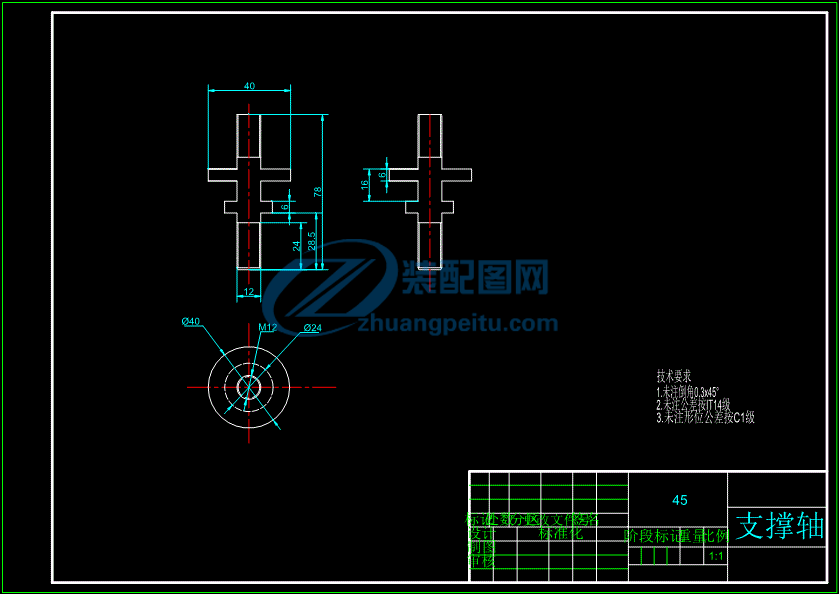
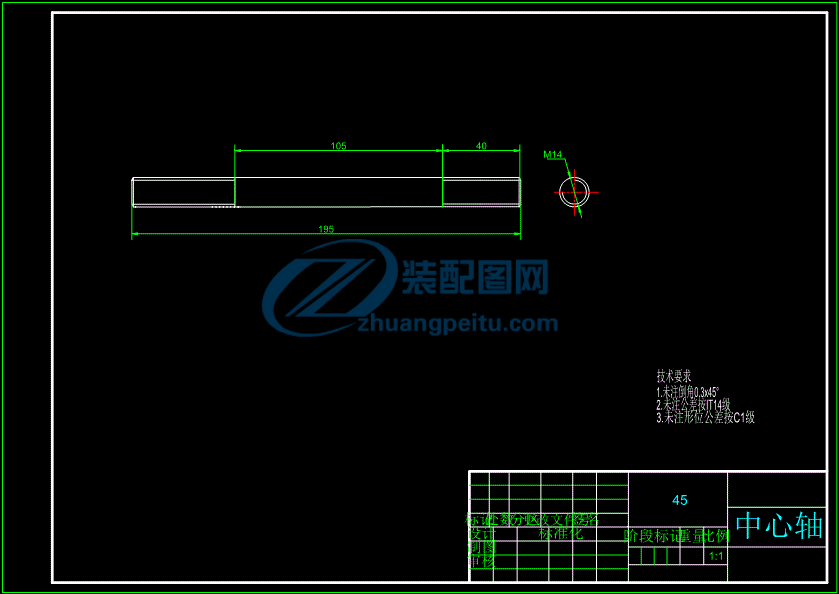
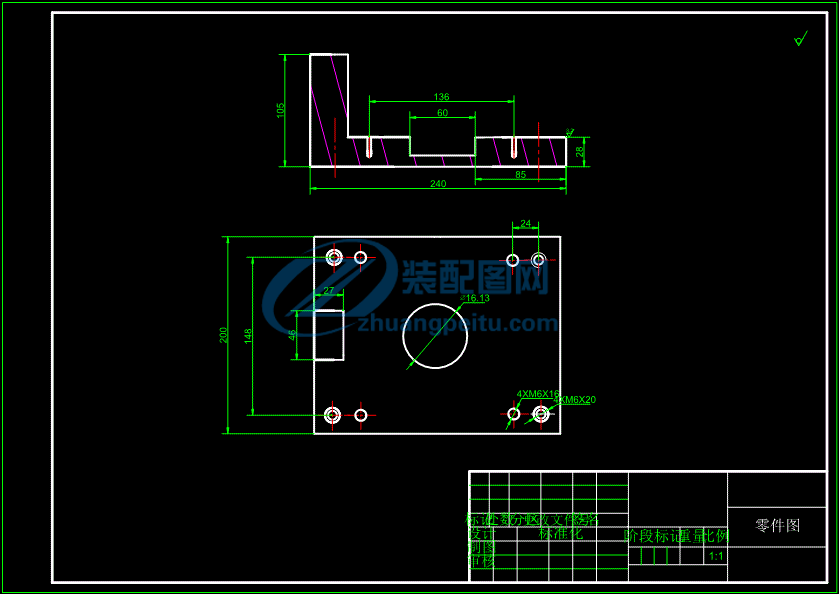
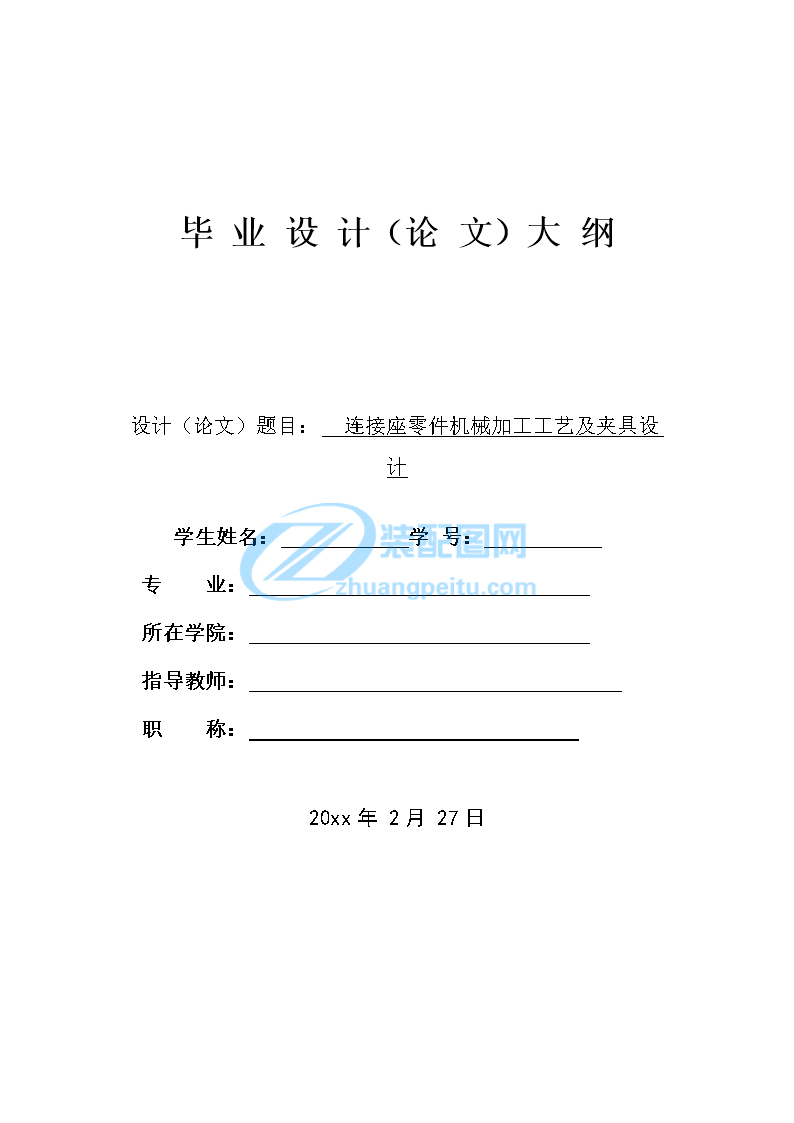
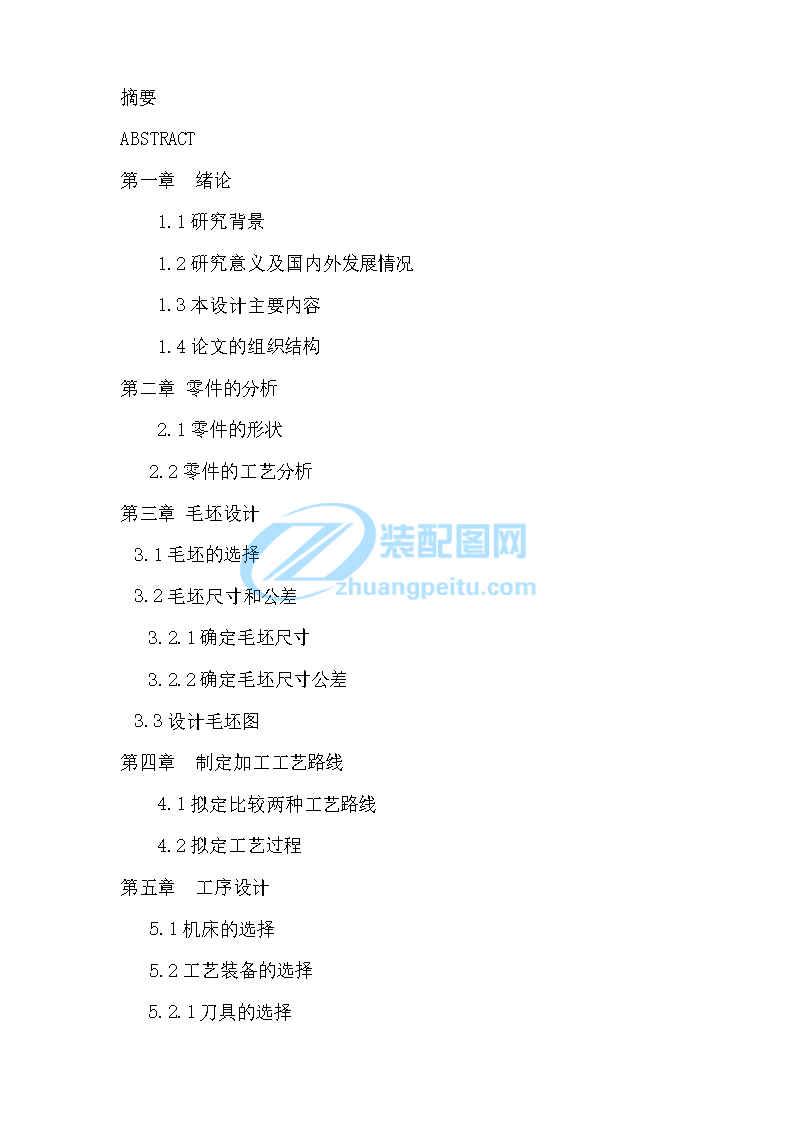
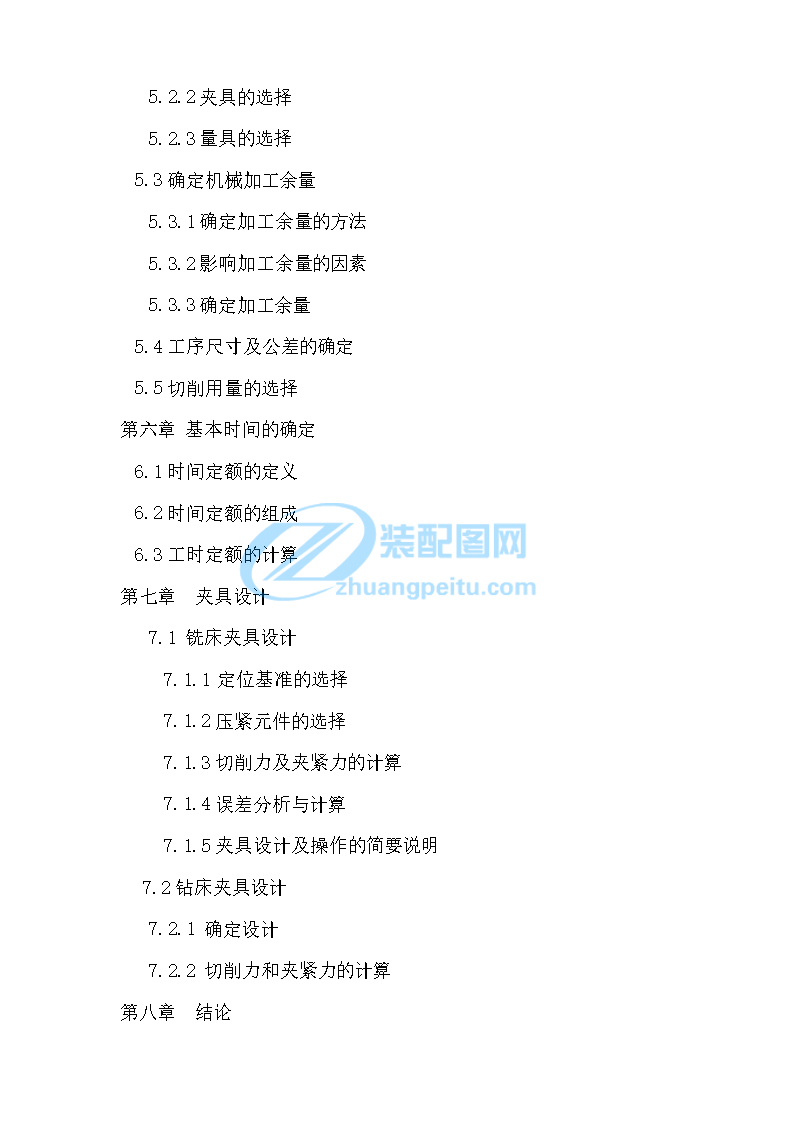
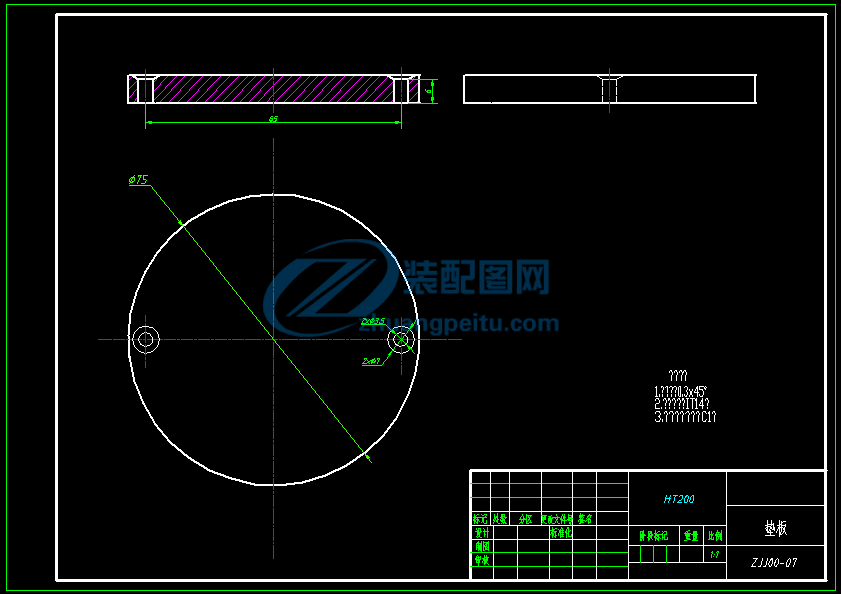
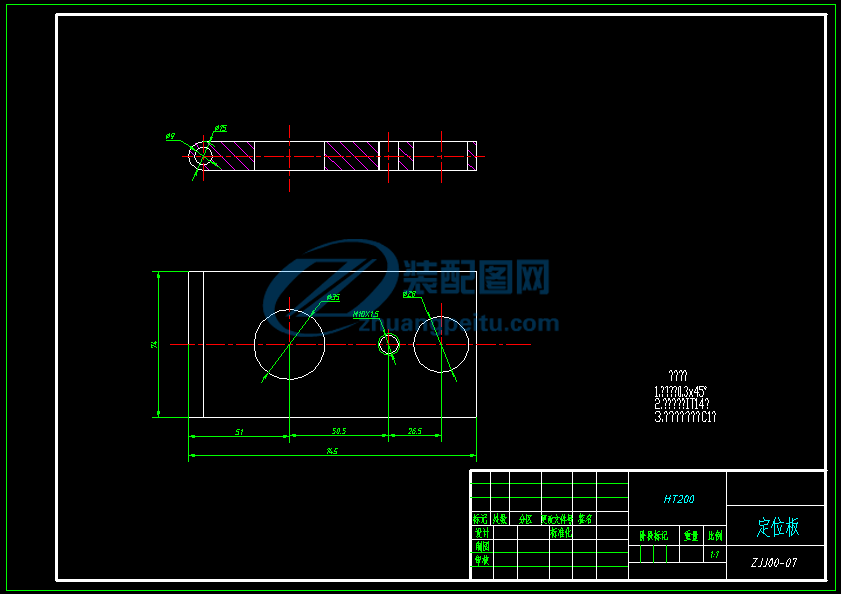
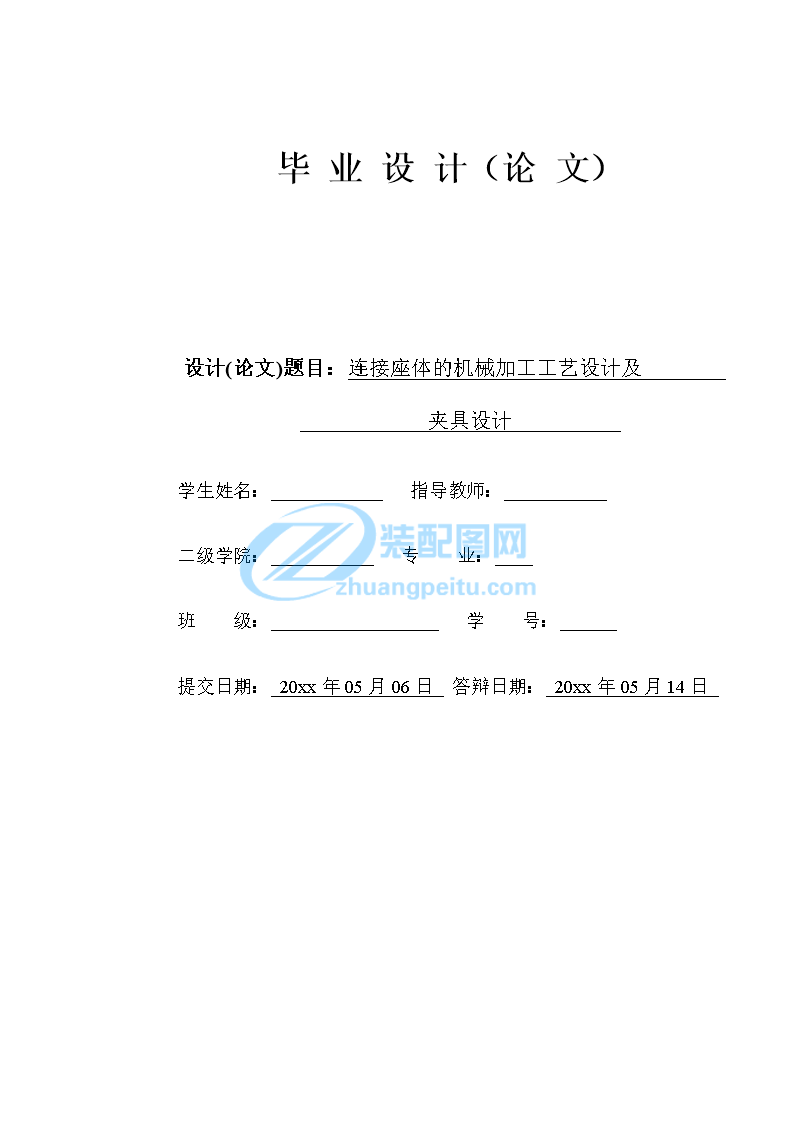
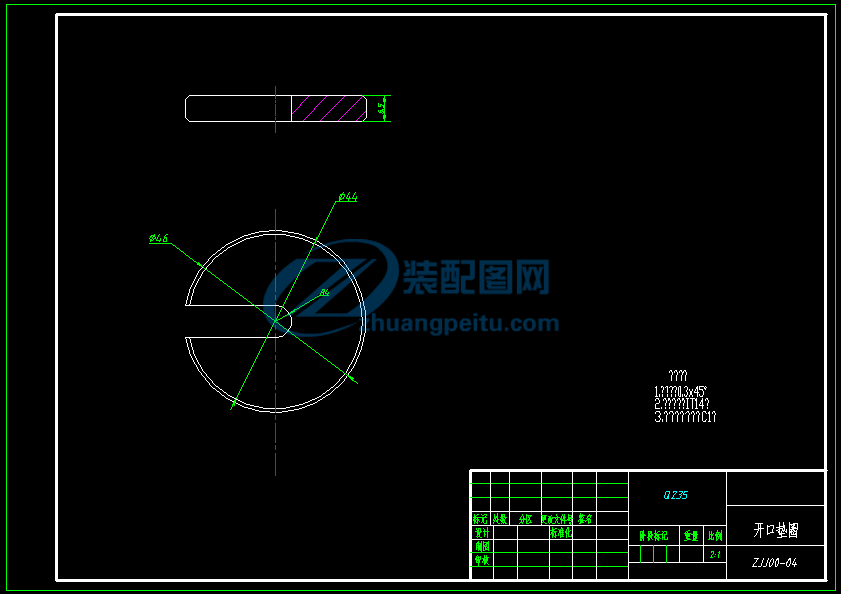
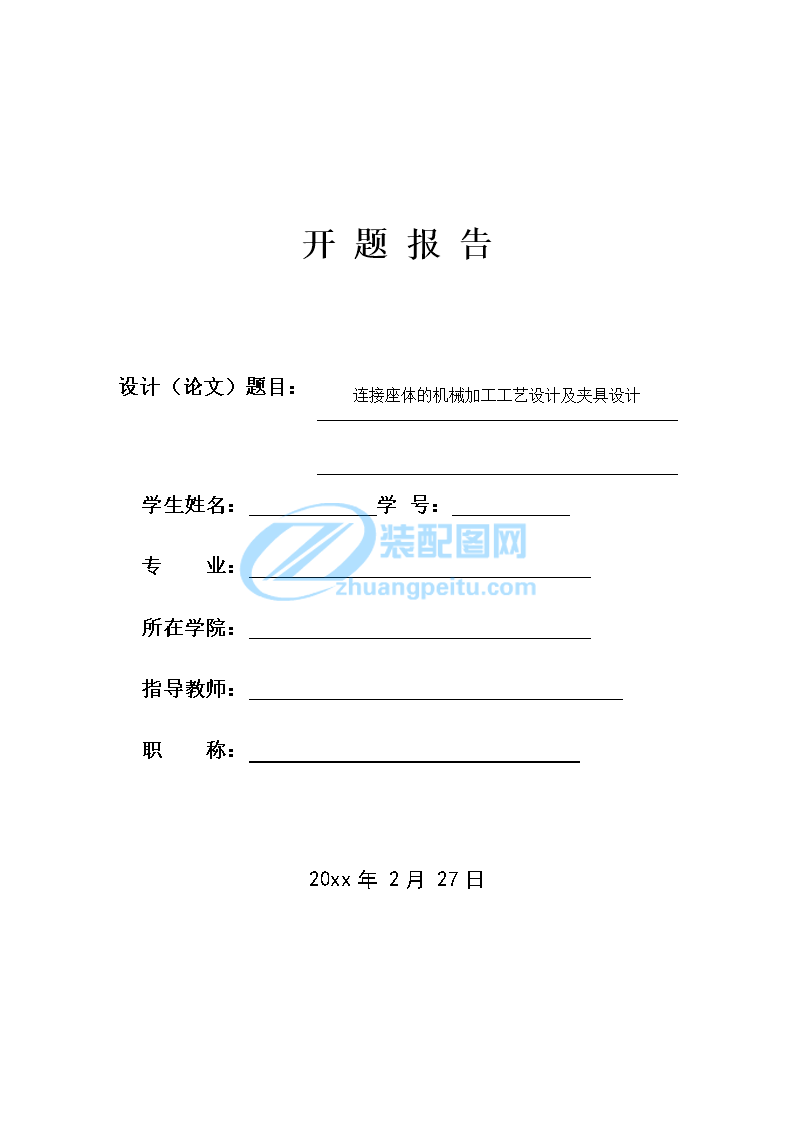
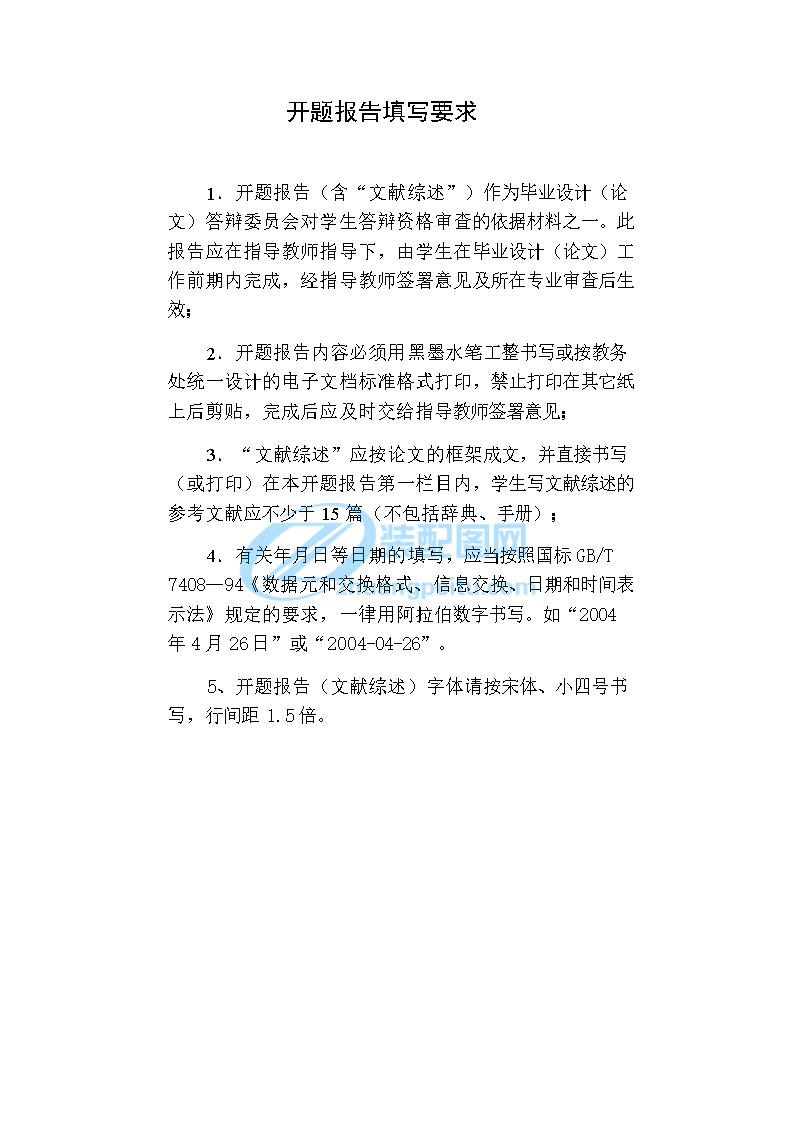
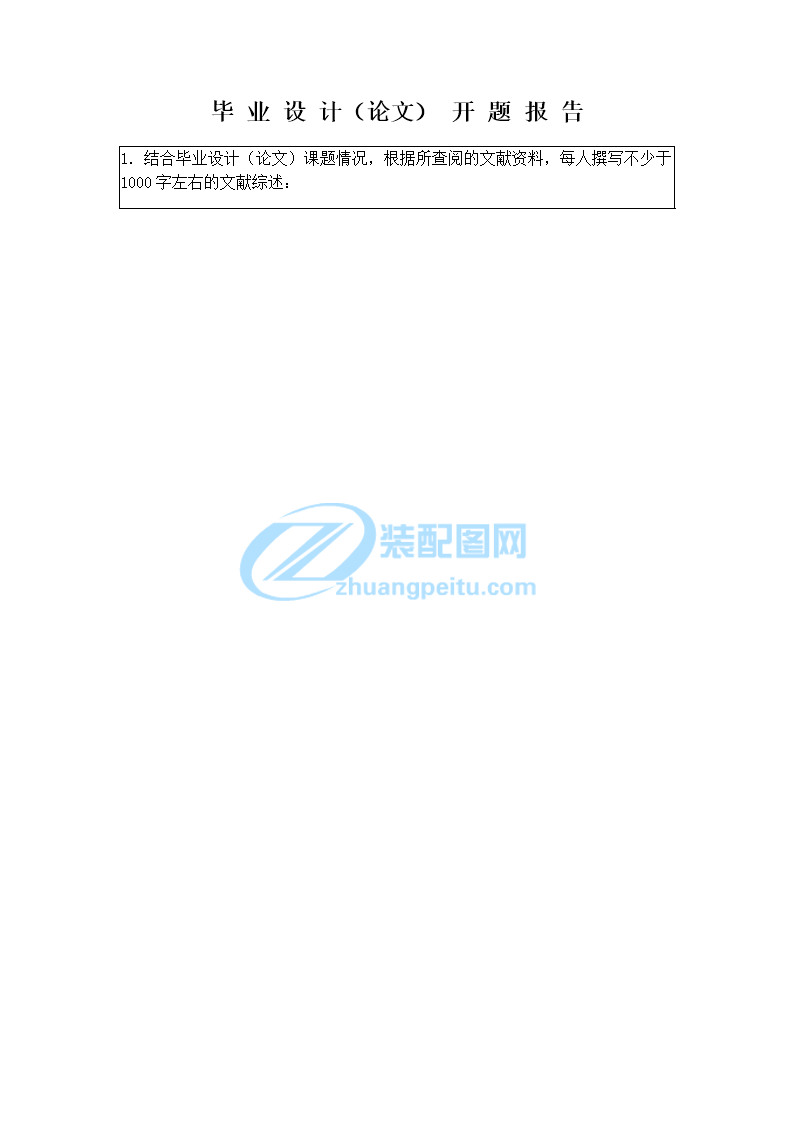
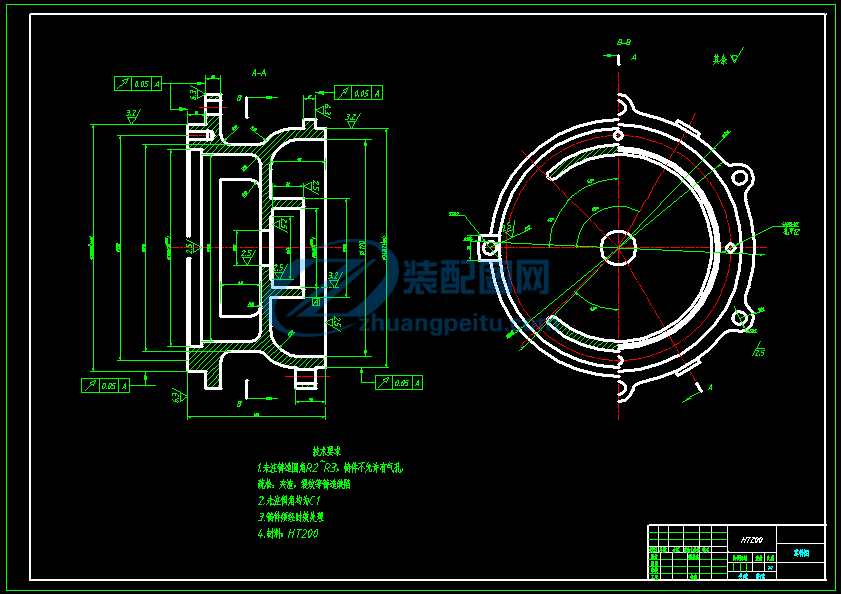
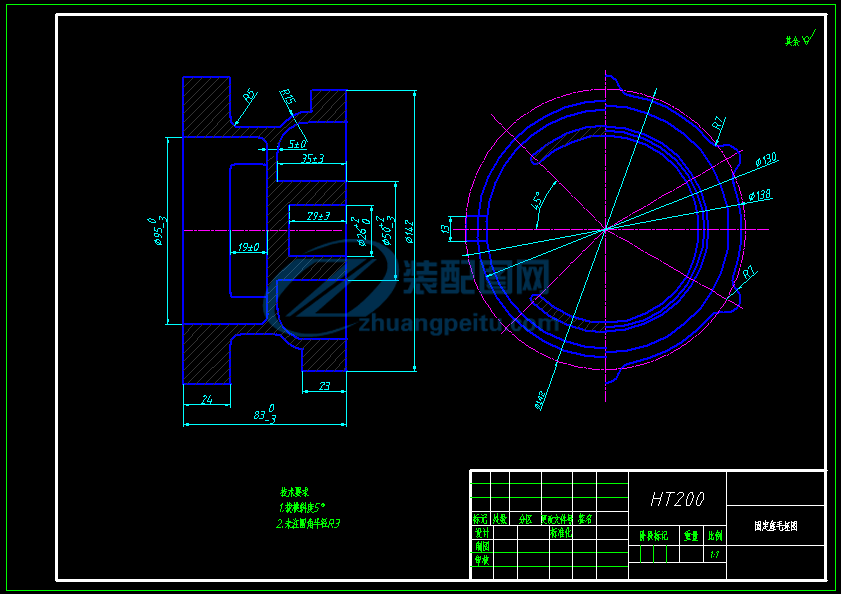

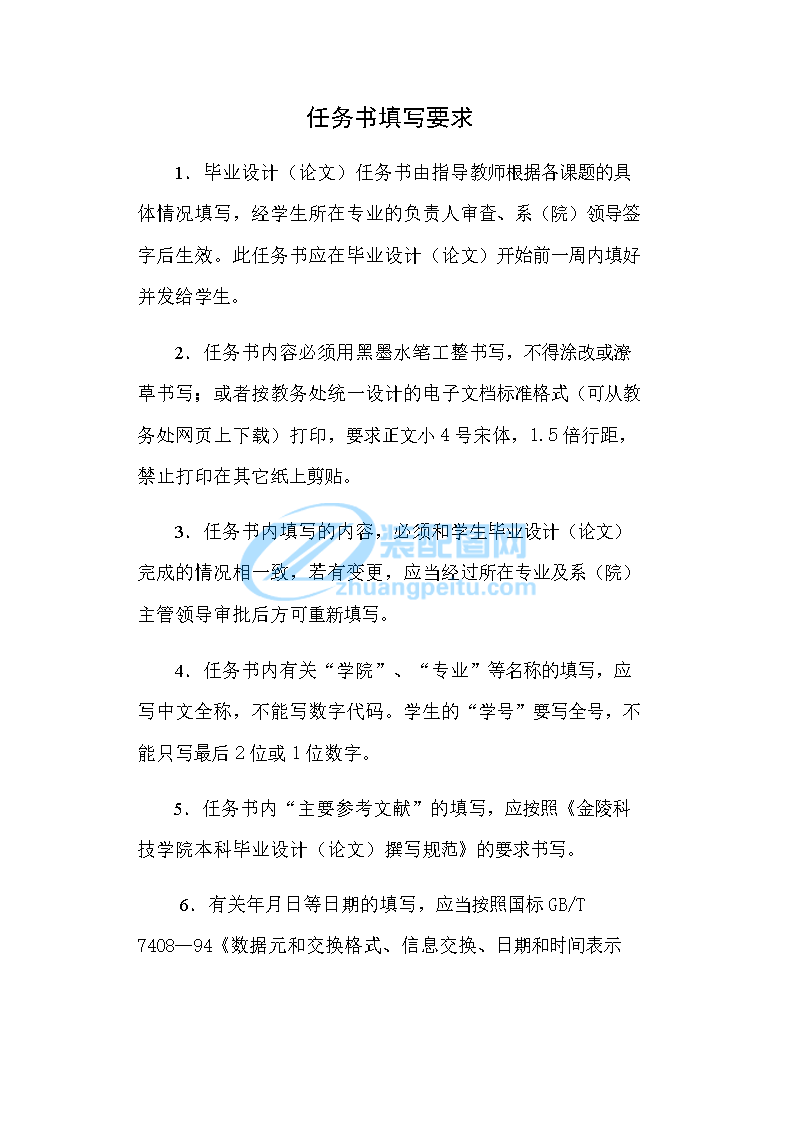
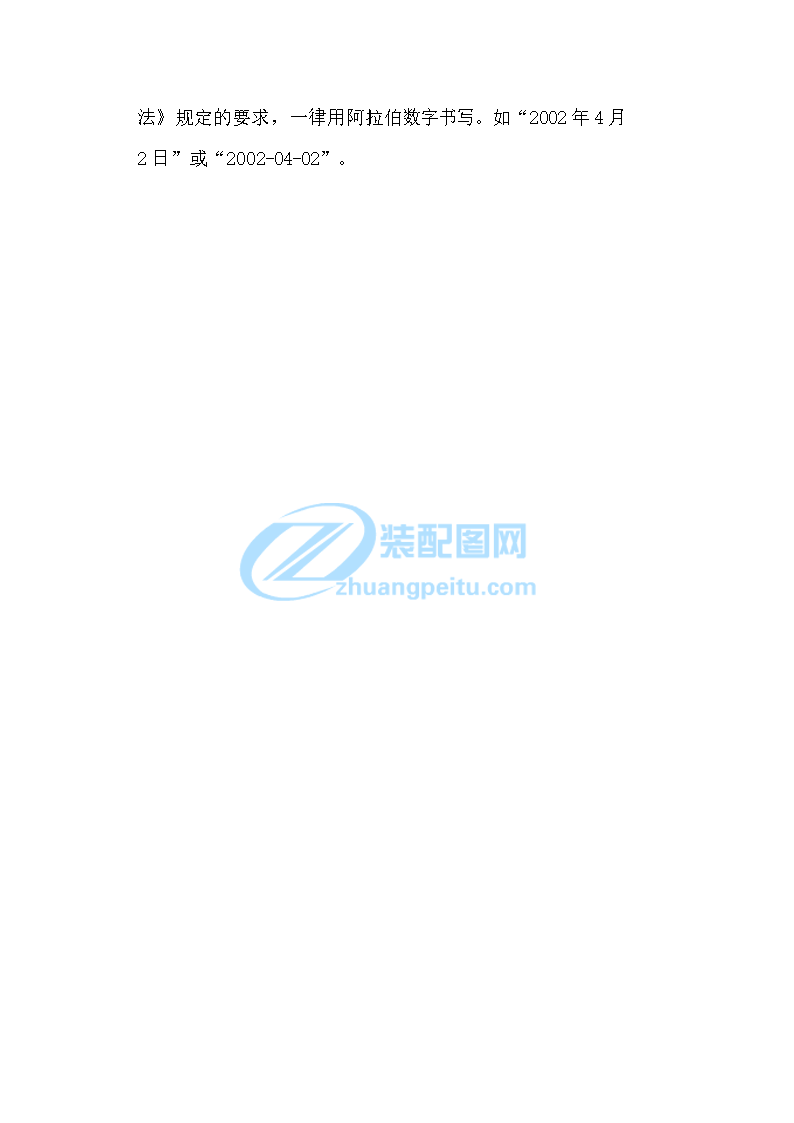
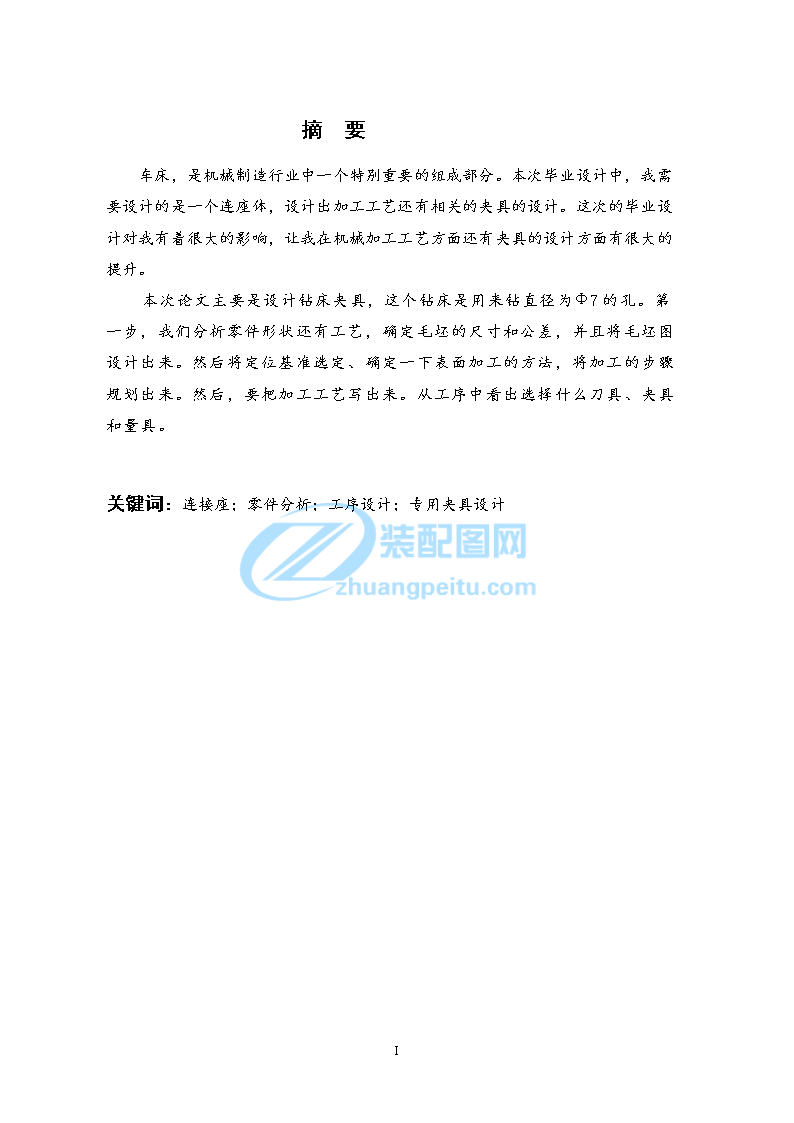
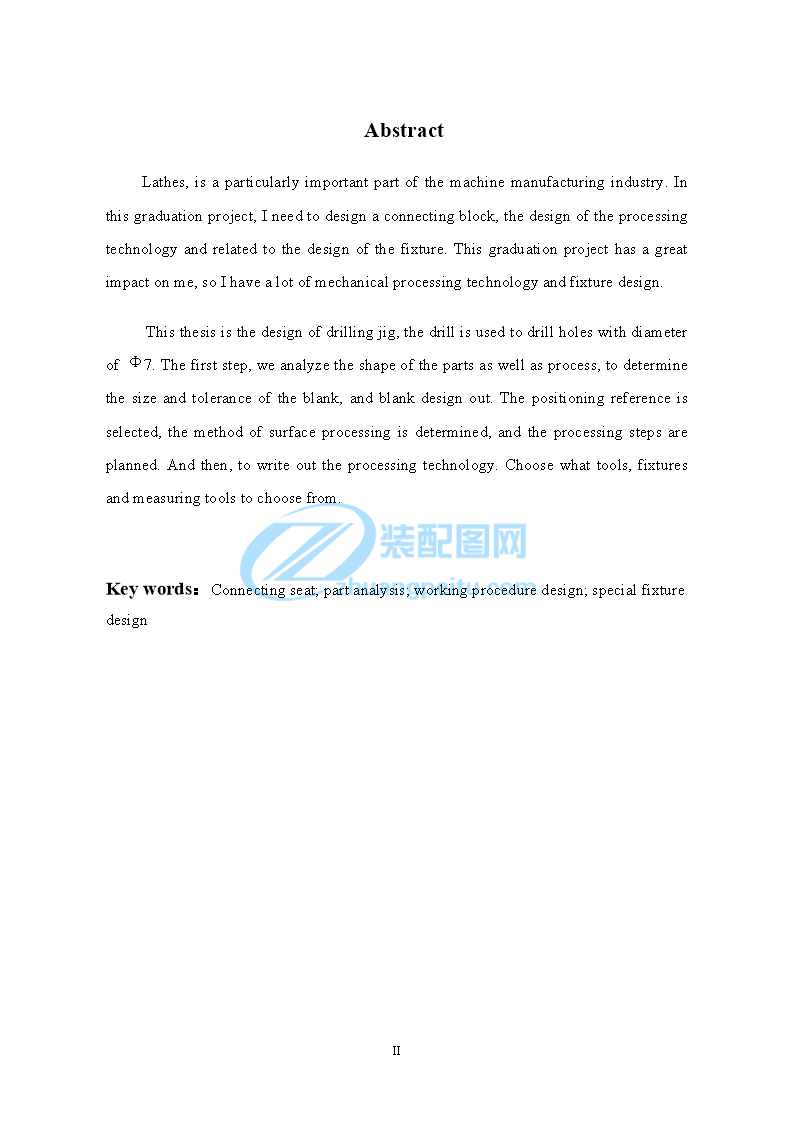
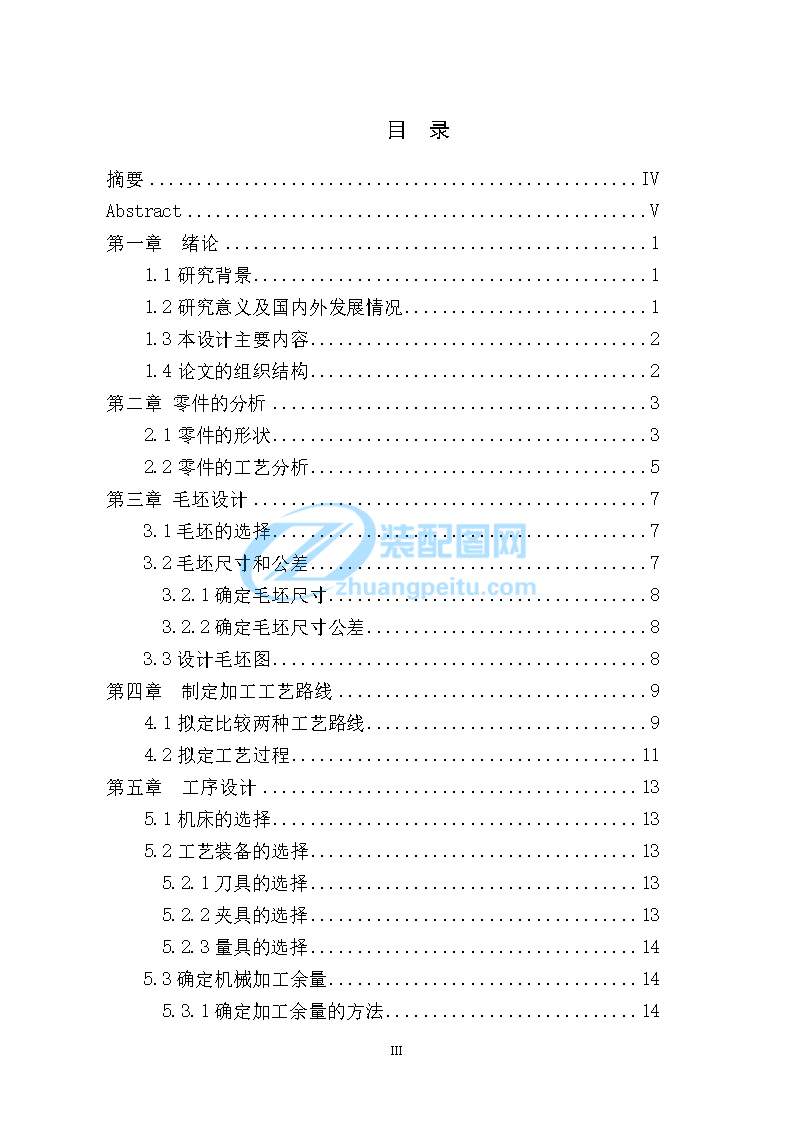


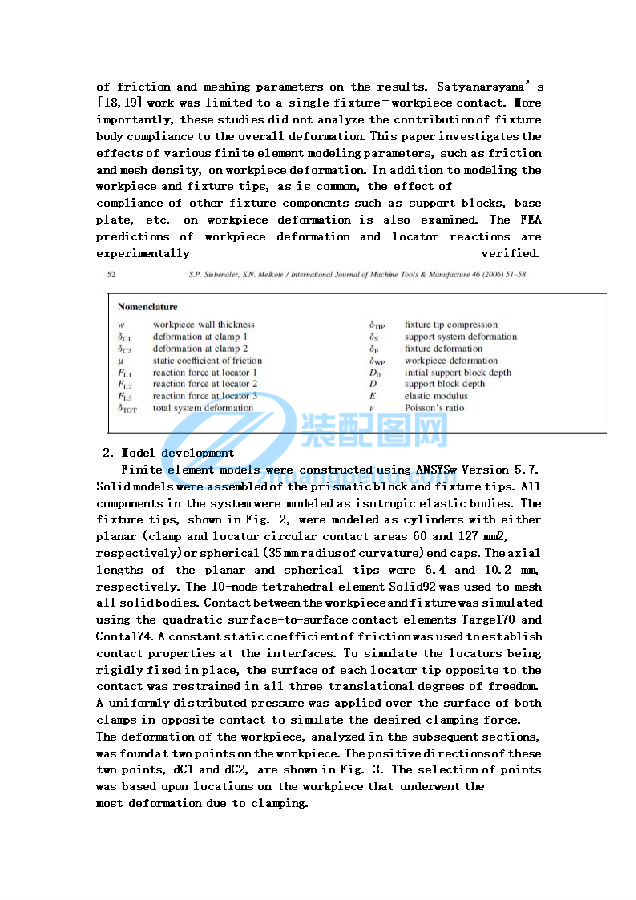
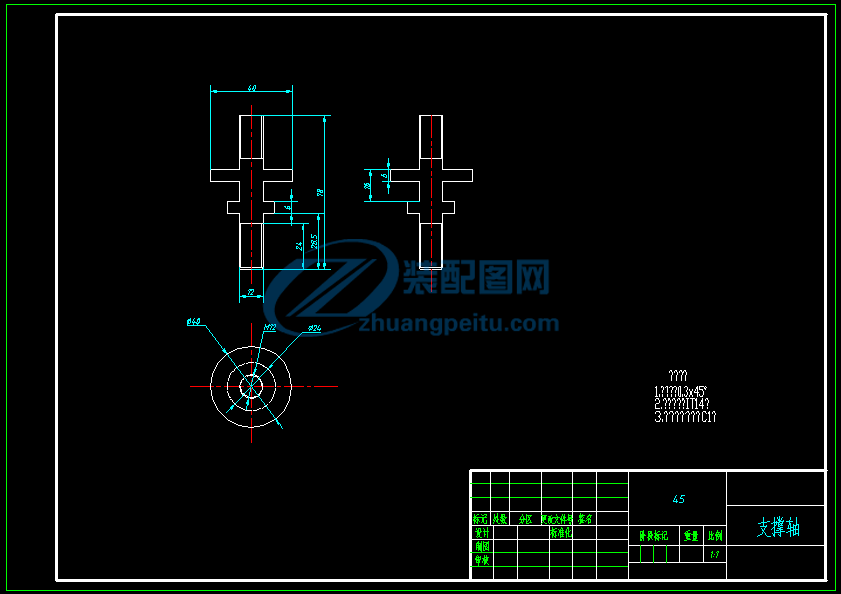
畢 業(yè) 設(shè) 計(jì)(論 文)外 文 參 考 資 料 及 譯 文
譯文題目: Prediction of workpiece deformation in a fixture systemusing the finite element method
利用有限元法預(yù)測(cè)夾具系統(tǒng)的工件變形
學(xué)生姓名: 學(xué) 號(hào):
專 業(yè):
所在學(xué)院:
指導(dǎo)教師:
職 稱:
20xx年 2月 27日
Prediction of workpiece deformation in a fixture system
using the finite element method
1. Introduction
Methods for analyzing fixtures are essential to the practice and economics of machining. In particular, the ability to model and accurately predict workpiece deformation induced by fixturing loads and/or predict the unknown fixture–workpiece contact forces are crucial for designing functional fixtures. The most common modeling and analysis approaches used for fixture–workpiece systems include the rigid body approach, the
contact mechanics based approach and the finite element modeling approach. Of these approaches, the rigid body modeling approach [1–3] is by definition incapable of predicting workpiece deformations and is therefore unsuitable for analysis of the impact of fixturing on part quality. The contact mechanics approach, although attractive from a
standpoint of computational effort, is limited to parts that can be approximated as elastic half-spaces. Models derived fromthis approach are capable of accurately predicting unknown locator reaction forces and localized contact deformations [4–6]. However, they are not applicable for thin, compliant parts. Finite element models on the other hand are very powerful and are capable of accounting for all compliances and nonlinearities present in the system. Although use of finite element models has been widely reported in the literature and employed in practice, a clear understanding of the role of the different fixture compliances on the prediction accuracy of workpiece deformation is lacking. Also knowledge of the effects of different finite element model parameters on workpiece deformation is lacking.
A common assumption in application of Finite Element Analysis (FEA) to analyze a fixture–workpiece system is that the fixture is completely rigid since it is much stiffer than the workpiece in many applications. In most such cases, the workpiece is modeled and nodes at the location of fixture contact are completely restrained. This formulation is commonly referred to as a single-point contact [7–12]. Omitting fixture elements does not allow for the model to account for compliance in the fixture and neglects frictional contact effects between the fixture and workpiece. Other researchers [13–16] have utilized linear springs to approximate the stiffness of the fixture components. However, such an approach requires the stiffness to be measured or approximated, adding time and introducing potential error into the analysis.
Recent work [17–19] has explored the use of surface-tosurface contact elements. Such an approach allows frictional effects to be modeled. This methodology was used for the work reported in this paper. Liao et al. [17] used FEA with contact elements to model a multiple-contact fixture system. They, however, did not investigate the effects of friction and meshing parameters on the results. Satyanarayana’s [18,19] work was limited to a single fixture–workpiece contact. More importantly, these studies did not analyze the contribution of fixture body compliance to the overall deformation. This paper investigates the effects of various finite element modeling parameters, such as friction and mesh density, on workpiece deformation. In addition to modeling the workpiece and fixture tips, as is common, the effect of
compliance of other fixture components such as support blocks, base plate, etc. on workpiece deformation is also examined. The FEA predictions of workpiece deformation and locator reactions are experimentally verified.
2. Model development
Finite element models were constructed using ANSYSw Version 5.7. Solid models were assembled of the prismatic block and fixture tips. All components in the system were modeled as isotropic elastic bodies. The fixture tips, shown in Fig. 2, were modeled as cylinders with either planar (clamp and locator circular contact areas 60 and 127 mm2,
respectively) or spherical (35 mm radius of curvature) end caps. The axial lengths of the planar and spherical tips were 6.4 and 10.2 mm, respectively. The 10-node tetrahedral element Solid92 was used to mesh all solid bodies. Contact between the workpiece and fixture was simulated using the quadratic surface-to-surface contact elements Targe170 and Conta174. A constant static coefficient of friction was used to establish contact properties at the interfaces. To simulate the locators being rigidly fixed in place, the surface of each locator tip opposite to the
contact was restrained in all three translational degrees of freedom. A uniformly distributed pressure was applied over the surface of both clamps in opposite contact to simulate the desired clamping force.
The deformation of the workpiece, analyzed in the subsequent sections, was found at two points on the workpiece. The positive directions of these two points, dC1 and dC2, are shown in Fig. 3. The selection of points was based upon locations on the workpiece that underwent the
most deformation due to clamping.
2.1 Sensitivity to friction coefficient
Laboratory tests conducted by Satyanarayana [18] on the
same fixture–workpiece system found an average static coefficient of friction (m) of 0.18 between the workpiece and fixture tips. The average was in a range of experimental values from 0.15 to 0.25. To test the effect of friction of workpiece deformation prediction, FEA models were constructed for workpiece wall thicknesses of 6–10 mm restrained in the fixture previously described. A spectrum of m from 0.15 to 0.30 was tested in combination with the various wall thicknesses. A summary of the deformation results is given in Table 2. An average difference of 3.1%
in deformation prediction was found for a change in m of 0.05. These results show that the effect of small variations in the friction coefficient on the workpiece deformation is quite small.
2.2 Treatment of primary plane locators
A series of models were constructed to determine the influence of the primary plane locators. For a properly designed 3-2-1 layout in which workpiece rotation is prevented, the only normal load taken by the three primary plane locators is the weight of the workpiece. The frictional
force produced by such a small load is often dwarfed by the much larger clamping loads. An analysis was performed to determine if the frictional effects at these locators must be accounted for in a modeling approach.
Two sets of boundary conditions were applied to blocks with wall thicknesses of 7, 8, and 9 mm. The first set, Case A, included all three primary plane locators subjected to the previously described surface-to-surface contact boundary conditions. A value of 0.18 was specified for m. The second configuration, Case B, removed all three of
the primary plane locators and simply restrained the bottom surface of the workpiece from translating in the z-direction. A summary of the results is given in Table 3. The FEA showed that the predicted deformations differed between the two boundary condition sets by an average of only 1.31%. This small impact of the bottom locators allows the FEA models to be constructed without the primary plane locators,
thus saving considerable computational time. This (Case B) boundary condition set used only 77 and 69% of the complete model computational time for the planar and spherical tips, respectively. The omission of the three primary plane locators coupled with restraining the bottom
surface of the workpiece was the configuration used for subsequent models. It should be pointed out that this approximation may not be valid when machining loads are also taken into account.
利用有限元法預(yù)測(cè)夾具系統(tǒng)的工件形
1. 介紹
分析裝置的方法是必不可少的實(shí)踐加工和經(jīng)濟(jì)學(xué),尤其是能力模型。準(zhǔn)確預(yù)測(cè)工件變形誘導(dǎo)夾具負(fù)載或預(yù)測(cè)未知的夾具工件。接觸力是關(guān)鍵設(shè)計(jì)功能的裝置。最常見的用于建模和分析方法。夾具 - 工件系統(tǒng)包括剛體方法,聯(lián)系力學(xué)為基礎(chǔ)的方法和有限元建模方法。這些建模方法[ 1-3 ]是無法通過的定義預(yù)測(cè)工件變形,因此不適宜夾具對(duì)零件質(zhì)量的影響分析。 聯(lián)系力學(xué)的方法,雖然從一個(gè)具有吸引力,計(jì)算努力的立場(chǎng),零件可以是有限的,近似為彈性半空間。這種方法能夠準(zhǔn)確地預(yù)測(cè)未知,定位反應(yīng)部隊(duì)和本地化的接觸變形[4 - 6]。然而,他們不適用兼容的零部件。另一方面,有限元模型是非常強(qiáng)大的,會(huì)計(jì)能為所有符合和非線性系統(tǒng)中存在。雖然利用有限元模型已beenwidely文獻(xiàn)報(bào)道,受雇于在實(shí)踐中,明確了不同的作用的認(rèn)識(shí).預(yù)測(cè)精度對(duì)工件的夾具符合變形是缺乏。也是知識(shí)的影響.不同的有限元模型參數(shù)對(duì)工件變形缺乏。
在應(yīng)用中的一個(gè)共同的假設(shè)的有限元分析(FEA)分析工件夾具系統(tǒng)是夾具是完全剛性的,因?yàn)樗沁h(yuǎn)遠(yuǎn)高于圍追堵截。在許多應(yīng)用中的工件。在大多數(shù)這種情況下,是仿照工件夾具的位置和節(jié)點(diǎn)聯(lián)系被完全抑制。這一提法普遍被稱為單點(diǎn)接觸[ 7-12 ] 。夾具元件不允許帳戶模型遵守夾具和忽略摩擦接觸效果夾具和工件之間,其他研究人員[ 13-16 ]利用線性彈簧,近似夾具部件的剛度。然而,這種方法需要?jiǎng)偠葴y(cè)量或近似,添加時(shí)間和引入潛在的錯(cuò)誤分析。
最近的工作[ 17-19 ]探索的表面使用接觸單元。這種做法使摩擦為藍(lán)本的影響。這種方法被用于本文報(bào)道的工作等。 [ 17 ]使用有限元分析接觸單元來模擬多接觸夾具系統(tǒng)。然而,沒有調(diào)查摩擦的影響嚙合參數(shù)的結(jié)果[ 18,19]。工作僅限于一個(gè)單一夾具 - 工件接觸。更多重要的,這些研究中沒有分析的貢獻(xiàn)夾具的身體符合整體變形。
本文探討各種有限的影響元建模參數(shù),如摩擦和網(wǎng)密度工件變形。除了造型工件和夾具的秘訣,是常見的的效果。如支持符合其他夾具元件塊底座工件變形等也是檢查工件變形的有限元分析預(yù)測(cè)實(shí)驗(yàn)驗(yàn)證和定位反應(yīng)。
2.模型開發(fā)
有限元模型構(gòu)建使用ANSYSw.版本5.7。實(shí)體模型組裝的棱柱塊夾具提示。系統(tǒng)中的所有組件為各向同性彈性體建模。夾具的秘訣顯示圖。 2無論是平面建模作為氣瓶.(夾具和定位圓形接觸面積的60和127 mm2的分別)或球( 35毫米的曲率半徑)結(jié)束上限。平面和球面提示軸向長度分別為:6.4和10.2毫米, 10節(jié)點(diǎn)的四面體.元素SOLID92用于所有實(shí)體網(wǎng)格。
工件和夾具之間的接觸進(jìn)行了數(shù)值模擬使用二次曲面表面接觸.元素TARGE170和CONTA174 。恒定的靜態(tài)摩擦系數(shù)是用來建立聯(lián)系的屬性在接口。到模擬地方的定位器,每個(gè)定位器尖端對(duì)面的表面接觸被限制在所有三個(gè)平移度自由。適用于一個(gè)均勻分布的壓力超過雙方夾相反的接觸面模擬所需的鎖模力
工件變形,分析了隨后的章節(jié),被發(fā)現(xiàn)在兩個(gè)點(diǎn)上工件。這兩點(diǎn)正方向DC1和DC2,如圖。 3點(diǎn)的選擇.根據(jù)工件的位置,經(jīng)歷了因?yàn)橐獖A緊大部分變形。
2.1 摩擦系數(shù)的敏感性
Satyanarayana [18 ]進(jìn)行的實(shí)驗(yàn)室測(cè)試.相同的工件夾具系統(tǒng)發(fā)現(xiàn)平均靜態(tài)和工件之間的摩擦系數(shù)為0.18 (米)夾具的提示。在實(shí)驗(yàn)范圍內(nèi)的平均值從0.15至0.25 。為了測(cè)試摩擦的影響.工件變形預(yù)測(cè),有限元模型構(gòu)建工件壁的厚度6-10毫米在前面所述的夾具抑制。頻譜從0.15到0.30 m的測(cè)試結(jié)合各種墻體的厚度。變形摘要結(jié)果列于表2 。 3.1%的平均差異在變形預(yù)測(cè)中被發(fā)現(xiàn)為一米的變化0.05。這些結(jié)果表明,在小的變化的影響對(duì)工件變形的摩擦系數(shù)相當(dāng)小。
2.2 治療的主要平面定位
構(gòu)建了一系列車型確定主平面定位的影響。對(duì)于正確.設(shè)計(jì)的3-2-1布局,工件旋轉(zhuǎn)阻止,三個(gè)主要采取的正常負(fù)荷平面定位工件的重量。摩擦這樣一個(gè)小負(fù)載所產(chǎn)生的力量往往相形見絀更大的夾持負(fù)荷。進(jìn)行了分析,確定是否必須在這些定位器的摩擦效應(yīng)占建模方法。
兩套邊界條件被應(yīng)用到塊與壁厚7,8,9毫米。第一組,案件一,包括所有三個(gè)主要的飛機(jī)受到定位.先前所描述的表面到表面的接觸邊界條件。被指定為M值0.18 。 第二個(gè)配置,案例B,刪除了所有三主平面定位,只是抑制了在翻譯的工件表面底部z方向。
表3給出了一個(gè)結(jié)果摘要。有限元分析結(jié)果顯示,預(yù)測(cè)變形之間的不同兩個(gè)邊界條件設(shè)置由平均只有1.31% 。這小的沖擊,使有限元分析的底部定位無主平面定位將建造的模型從而節(jié)省了大量的計(jì)算時(shí)間。這個(gè)(案例B )邊界條件設(shè)置使用的只有77和69 %。完成平面模型的計(jì)算時(shí)間和球技巧,分別遺漏的三個(gè)加上主平面與制約的底部定位.工件表面是用于配置隨后模型。應(yīng)當(dāng)指出,這逼近未必有效加工負(fù)載時(shí)還考慮到。