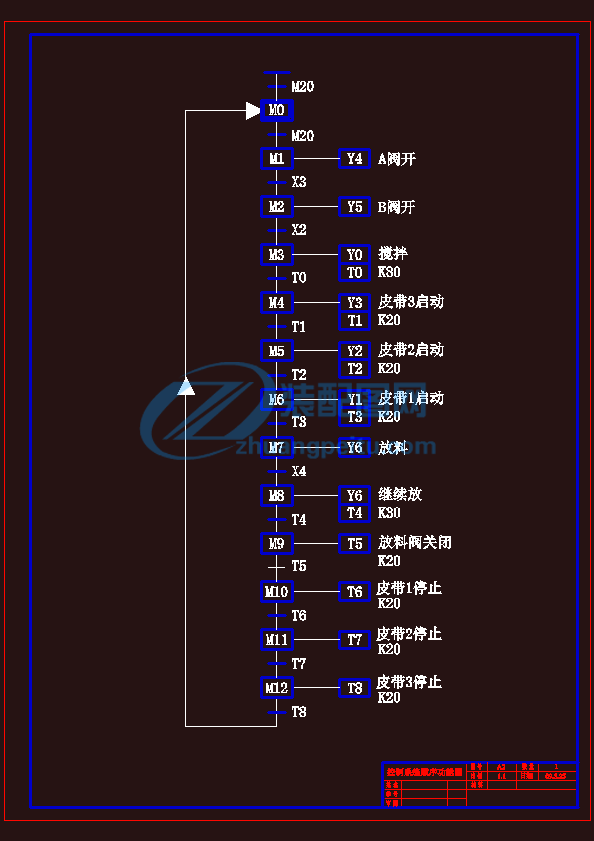
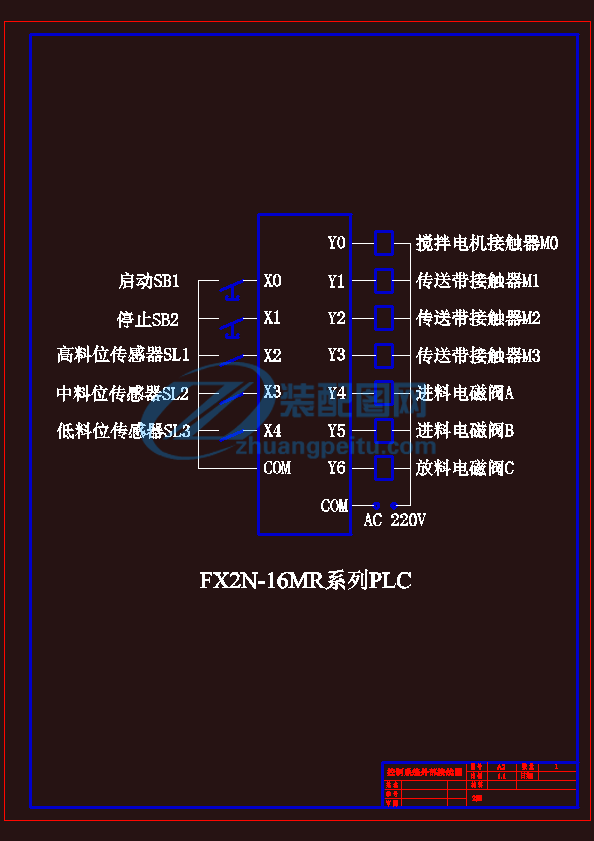
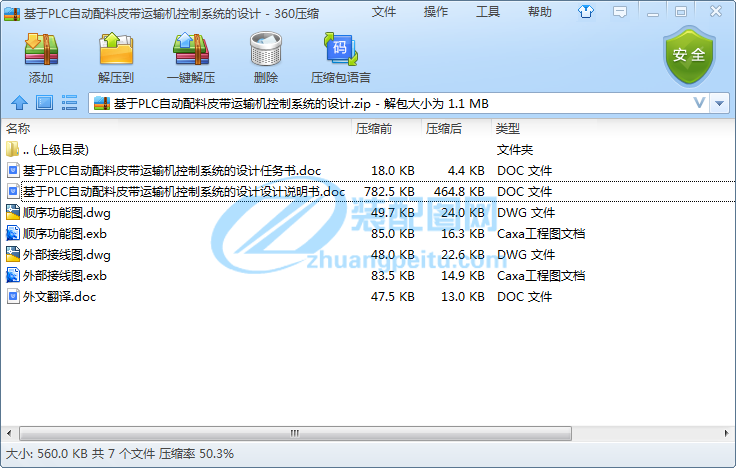
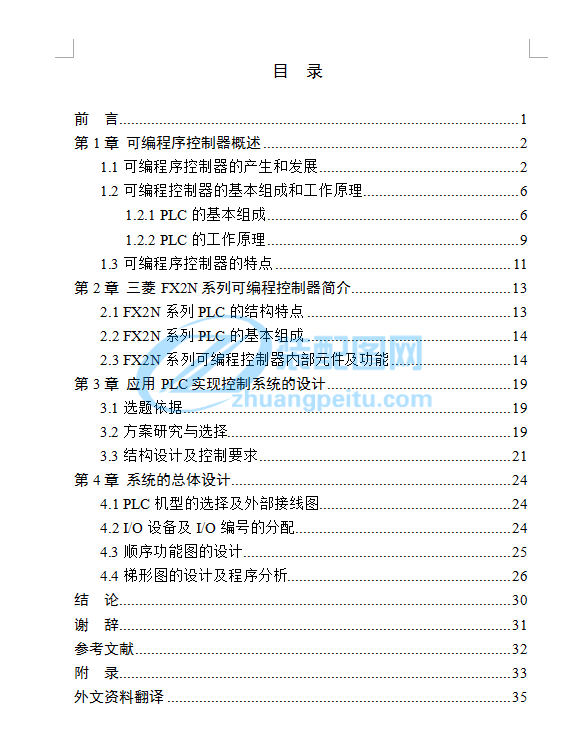
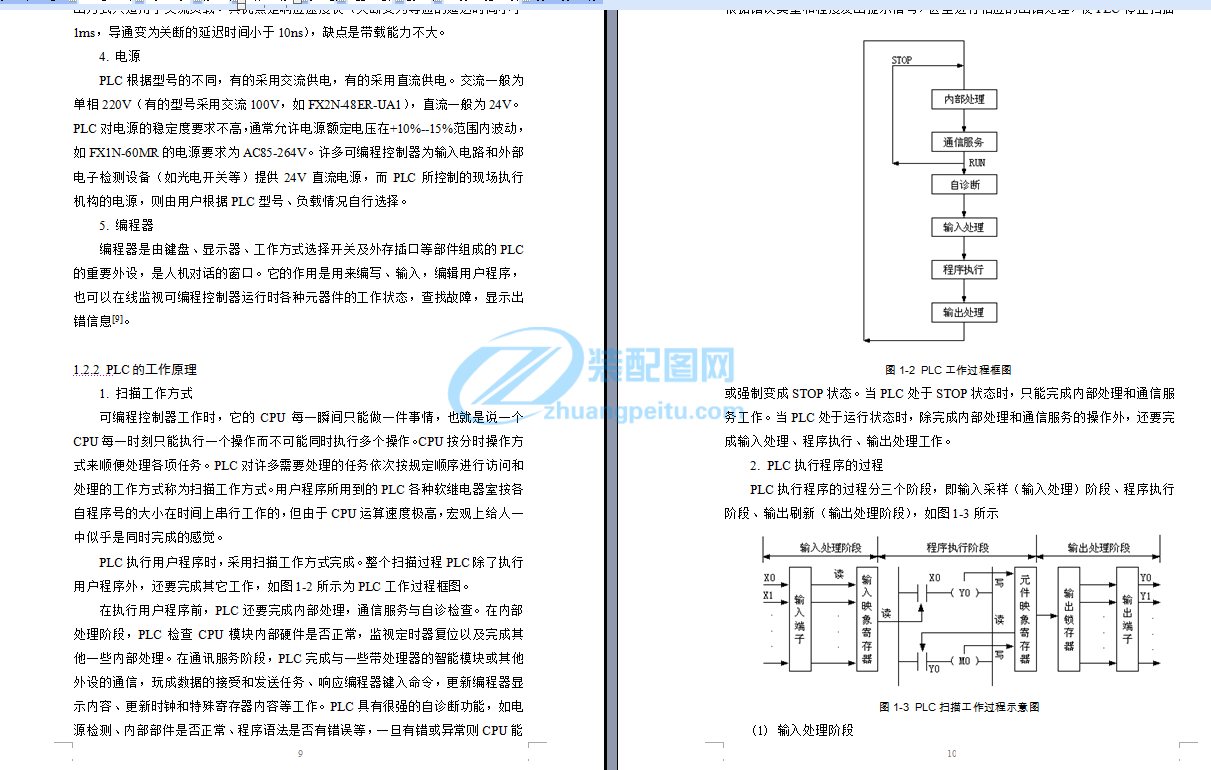
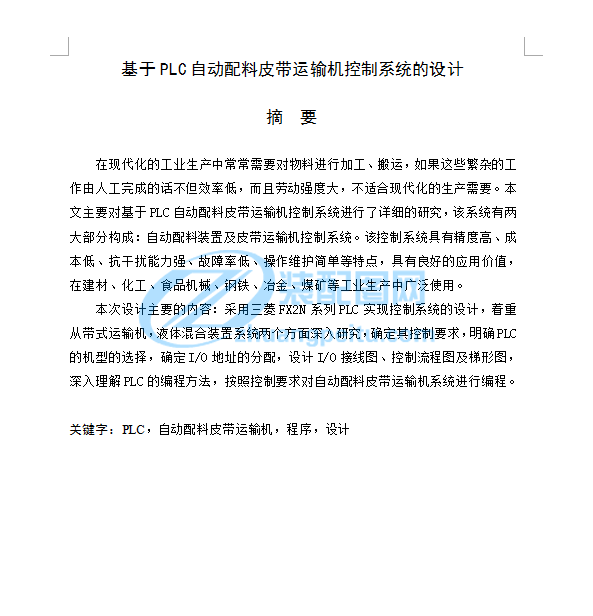
附 錄
語 句 表
外文資料翻譯
The future development trend of PLC
In the field of industrial automation control is divided into PLC, industrial control and embedded control, and the PLC since 1968 after the birth at an alarming rate in this area has become the dominant service provider, for a wide range of automation control equipment to provide a very reliable control applications. The main reason is that it is able to control the application of automation to provide a safe, reliable and fairly complete solutions for industrial enterprises in the current automation needs.
1. PLC characteristics and application
(1) reliability
The reliability of the product's effectiveness and maintainability. Programmable controller and high reliability, performance in the following areas:
a. does not require a large number of programmable logic controller moving parts and electronic components, greatly reducing wiring, at the same time, simple in-house maintenance, maintenance time, so reliability is improved.
b. the reliability of programmable logic controller design method using a series of design, such as redundant design, brown-out protection, fault diagnosis, alarm and operation of information display and information protection and recovery.
c. Programmable Controller ease stronger, it has programmed a simple, easy to operate, programming error rate substantially reduced, and the poor operating environment for the industrial design of hardware reliability greatly increased.
d. programmable logic controller hardware design, using a series of measures to improve reliability. For example, the use of high-reliability industrial grade components, the use of advanced electronic processing technology (SMT) manufacturing, to interfere with the use of shielding, isolation and filtering; memory content protection, the use of watchdog and self-diagnostic measures designed to facilitate maintenance and so on.
(2) ease
a. easy to operate: the operation of the PLC including the procedure to change the input and process operation, the majority of PLC programmer to carry out procedures for the use of input and change the operation. The PLC is now the majority of the programmer can use the computer directly, to change the present procedure may also be required to address the basis of number, relay number or contact number, or search directly in order to find, and then changes can be online or offline;
b. programming: PLC There are many programming languages can be used, ladder and electrical schematic diagram similar; programming language is an acronym for functional, easy to remember; functional language to the process flow chart the progress of the main line, very suitable for designers and Process design of communication professionals. Function Block Diagram and Structured Text language, features a clear, easy to understand and so on.
c. easy maintenance: PLC has a self-diagnostic function of the technical requirements for maintenance personnel low, when the system failure, a hardware and software through self-diagnosis, maintenance personnel can be in accordance with the relevant fault code and fault display hints, such as signal information, or through programming and HMI configuration screen, direct the site to find fault where, for the rapid troubleshooting and repair saves time and reduces MTTR.
(3) Flexibility
a. flexibility of programming: PLC standard programming languages used are Ladder Diagram, Instruction List, function chart, function block diagram and structured text programming language. Users to master a programming language which can be programmed, the diversity of programming to make programming easy.
b. expand the flexibility of: PLC expansion flexibility is an important feature of it. It can be based on expanding the scale of application, namely the expansion of capacity, the expansion of functions, applications and the control of the expansion. It can not only by increasing the input and output cards increase the points, through the expansion unit to expand capacity and function, can also be more than one PLC to expand the communications capacity and capabilities,
c. operating flexibility: the flexibility of operation means the design work, programming work, and installation to reduce the workload of the construction. Operation has become very convenient and flexible to monitor and control has become very easy. Relay control system in the order of the number of operations needed to be simplified, the production process can be different from the same console and control screens.
(4) Mechatronics
In order to make industrial production process control is more stable, more reliable, high quality, high yield, low efficiency of process control equipment and devices to the mechanical and electrical integration, that is, instruments, electronics, computer integrated the requirements of the PLC is this the product of a request, it is specifically designed for industrial process control equipment, small size, function, and the advantages of a good anti-jamming, mechanical and electrical components will be combined in one device, the instrumentation, electronics and the functions of the computer integrated together, therefore,
It has become today's CNC technology, industrial robotics, discrete manufacturing and process areas such as the main process control equipment, to become the three pillars of industrial automation (PLC, robotics, CAD / CAM) one.
Programmable logic controller has become an irreplaceable control systems, they can communication with other systems to provide product statements, production scheduling, and equipment for self-diagnosis of failures, these technical improvements, so that the PLC has become today, each of industry quality and output of the important contributors.
It is easy to see from the above characteristics, PLC in the field of industrial control, not only will not be introduced gradually and will continue to expand his market share. The surface appearance of IPC PLC to bring a certain degree of impact, but a closer look at if we can see that the IPC has helped to some extent, in fact, the development of PLC, because PLC-high reliability, easy-to-use, but the operator station and a number of functions, such as curve processing, data recording and other functions, far less than IPC, and IPC's fatal flaw is poor reliability. Therefore, the present situation combined IPC and PLC control system more perfect.
The emergence of IPC to promote the development of the PLC.
2. PLC direction
In fact, since its birth PLC is also in constant development to improve innovation.
The introduction of a new, advanced microprocessors and electronic technology to achieve fast scan time;
Small, low-cost PLC, can replace the relay 4-10, greater driving force for development;
High-density I / O systems to provide low-cost space-saving interface;
Microprocessor-based Intelligent I / O interface, extends the ability of distributed control. A typical interface, such as: PID, network, CAN bus, field bus, ASCII communications, positioning, the host communication module, and support high-level language programming of the module (such as BASIC, PASCAL);
Including input-output module and the structural design of terminal improvements, so that a more integrated terminal;
Special interface to allow certain devices directly from the controller, such as thermocouple, thermal resistance, stress measurement, fast response pulse;
And as a result of IPC, DCS control system, such as the emergence of function will force the PLC toward more openness in the direction of greater compatibility of the continuous development.
3. To integrate multiple functions, a more open integration PLC
(1) more advanced features, but also simple and quick to use
Simple logic of traditional PLC control functions are gradually unable to meet the requirements of the current field of industrial control, many new control system is no longer just simple logic control, an increase of many new functional requirements, such as a large number of data processing, storage, graphics processing, and so on are displayed.
In addition to the requirements of the powerful features, many project developers and end-users, but also hope that the structure of control system is more simple, the development of more efficient use of other control systems compatibility, opening up more.
For these needs, the United States HORNER Company (GE important partner companies) in the 20th century, the early 80s, first put forward the "Allinone" the concept of the integration of control and has been committed to the idea of product development, launched the world's first integrated controller - OCS (Operator Control Station).
Traditional control system, the local display and PLC is separate from the general, respectively, use different editing software, to connect between the serial communication, so developers need a lot of time and effort spent on software development training and procedures, the and serial communications are relatively poor reliability, easy to be interfered with.
OCS controller and not a simple PLC, nor is it simply shows the human-machine interface, it would PLC, HMI, I / O and powerful network functions into a perfect one. Man-machine interface and PLC control program using the same set of programming developed by HORNER industrial programming software CsCAPE completed (five kinds of programming language support, standard for the ladder) to complete, allows the user to use faster and more convenient.
OCS is not only PLC, HMI, I / O and network integration simple and increase the number of industrial control computer or software configuration. Such as floating-point operations, advanced mathematical calculations, graphics curve (time curve, X-Y curve), the local historical data records (large-capacity removable storage card, 2G, HORNER first use of MicroSD storage), video input and output, the expert system interface , data monitoring, recording and printing documents.
(2) better communications, better open
In recent years, with the popularity of Internet technology and to promote, Ethernet has been the rapid development, especially the rate of increase in Ethernet communications, Ethernet switching technology, to solve the problem of non-deterministic Ethernet brought a new opportunity: First of all, Ethernet communication rate has increased from 10Mbps, to 100Mbps and even 10Gbps,; Second, the Ethernet switch to connect its port in each network node bandwidth provided by an independent connecting the switches in the same equipment on different resources do not exist, which is equivalent to each device of a network segment exclusive; Third,
Full-duplex technology for each device and between the switch port provides a dedicated send and receive channel, so different Ethernet devices greatly reduce the conflict between the (half-duplex switched), or completely avoid (full-duplex switched). Therefore, the Ethernet network has become established, so as it applies to industrial automation and control to eliminate the main obstacles.
With other fieldbus or industrial communications networks, Ethernet has a wide range of applications, low-cost, high speed communications, hardware and software resource-rich, easy to connect with the INTERNET, and sustainable development potential advantages, not only the monopoly of a comprehensive factory automation information management network, but also in the process of monitoring the network layer has also been widely used and has a direct downward extension used in the industrial field device layer network trend.
The future development of PLC in addition to the development of the product itself, a greater extent depend on the users and the development of the market, the existence of any product is to users and the basic needs of the market. PLC to its high reliability and easy operation, led the industrial sector for decades, I believe it will continue to exist and continue the development of a strong.
PLC未來發(fā)展趨勢
在工業(yè)自動化控制領(lǐng)域主要分為PLC,工控機(jī)和嵌入式控制,而PLC自1968年誕生以后以驚人的速度成為了這一領(lǐng)域的主導(dǎo)者,為各種各樣的自動化控制設(shè)備提供了非??煽康目刂茟?yīng)用。其主要原因,在于它能夠?yàn)樽詣踊刂茟?yīng)用提供安全可靠和比較完善的解決方案,適合于當(dāng)前工業(yè)企業(yè)對自動化的需要。
1. PLC的特點(diǎn)及應(yīng)用
(1) 可靠性
可靠性包括產(chǎn)品的有效性和可維修性??删幊炭刂破鞯目煽啃愿?,表現(xiàn)在下列幾個方面:
a. 可編程控制器不需要大量的活動部件和電子元件,接線大大減少,與此同時,系統(tǒng)的維修簡單,維修時間縮短,因此可靠性得到提高。
b. 可編程控制器采用一系列可靠性設(shè)計方法進(jìn)行設(shè)計,例如冗余設(shè)計,掉電保護(hù),故障診斷,報警和運(yùn)行信息顯示和信息保護(hù)及恢復(fù)等。
c. 可編程控制器有較強(qiáng)的易操作性,它具有編程簡單,操作方便,編程的出錯率大大降低,而為工業(yè)惡劣操作環(huán)境設(shè)計的硬件使可靠性大大提高。
d. 可編程控制器的硬件設(shè)計方面,采用了一系列提高可靠性的措施。例如,采用可靠性高的工業(yè)級元件,采用先進(jìn)的電子加工工藝(SMT)制造,對干擾采用屏蔽、隔離和濾波等;存儲器內(nèi)容的保護(hù),采用看門狗和自診斷措施,便于維修的設(shè)計等。
(2) 易操作性
a. 操作方便:對PLC的操作包括程序的輸入和程序更改操作,大多數(shù)PLC采用編程器進(jìn)行程序輸入和更改操作?,F(xiàn)在的PLC的編程器大部分可以用電腦直接進(jìn)行,更改程序也可根據(jù)所需地址編號、繼電器編號或接點(diǎn)號等直接進(jìn)行搜索或按順序?qū)ふ?,然后可以在線或離線更改;
b. 編程方面:PLC有多種程序設(shè)計語言可以使用,梯形圖與電氣原理圖相似;編程語句是功能的縮寫,便于記憶;功能圖表語言以過程流程進(jìn)展為主線,十分適合設(shè)計人員與工藝專業(yè)人員設(shè)計思想的溝通。功能模塊圖和結(jié)構(gòu)化文本語言,功能清晰,易于理解等優(yōu)點(diǎn)。
c. 維修方便:PLC所具有的自診斷功能對維修人員的技術(shù)要求較低,當(dāng)系統(tǒng)發(fā)生故障時,通過硬件和軟件的自診斷,維修人員可以根據(jù)有關(guān)故障代碼的顯示和故障信號燈的提示等信息,或通過編程器和HMI屏幕的設(shè)定,直接找到故障所在的部位,為迅速排除故障和修復(fù)節(jié)省了時間,降低了MTTR。
(3) 靈活性
a. 編程的靈活性:PLC采用的標(biāo)準(zhǔn)編程語言有梯形圖、指令表、功能圖表、功能模塊圖和結(jié)構(gòu)化文本編程語言等。使用者只要掌握其中一種編程語言就可進(jìn)行編程,編程方法的多樣性使編程方便。
b. 擴(kuò)展的靈活性:PLC的擴(kuò)展靈活性是它的一個重要特點(diǎn)。它可以根據(jù)應(yīng)用的規(guī)模不斷擴(kuò)展,即進(jìn)行容量的擴(kuò)展、功能的擴(kuò)展、應(yīng)用和控制范圍的擴(kuò)展。它不僅可以通過增加輸入輸出卡件增加點(diǎn)數(shù),通過擴(kuò)展單元擴(kuò)大容量和功能,也可以通過多臺PLC的通信來擴(kuò)大容量和功能,
c. 操作的靈活性:操作的靈活性指設(shè)計工作量、編程工作量、和安裝施工的工作量的減少。操作變得十分方便和靈活,監(jiān)視和控制變得很容易。在繼電器順序控制系統(tǒng)中所需的一些操作得到簡化,不同生產(chǎn)過程可采用相同的控制臺和控制屏等。
(4) 機(jī)電一體化
為了使工業(yè)生產(chǎn)的過程控制更平穩(wěn),更可靠,向優(yōu)質(zhì)、高產(chǎn)、低耗要效益,對過程控制設(shè)備和裝置提出了機(jī)電一體化,即儀表、電子、計算機(jī)綜合的要求,而PLC正是這一要求的產(chǎn)物,它是專門為工業(yè)過程而設(shè)計的控制設(shè)備,具有體積小、功能強(qiáng),抗干擾性好等優(yōu)點(diǎn),它將機(jī)械與電氣部件有機(jī)地結(jié)合在一個設(shè)備內(nèi),把儀表、電子和計算機(jī)的功能綜合集成在一起,因此,它已經(jīng)成為當(dāng)今數(shù)控技術(shù)、工業(yè)機(jī)器人、離散制造和過程流程等領(lǐng)域的主要控制設(shè)備,成為工業(yè)自動化三大支柱(PLC,機(jī)器人,CAD/CAM)之一。
可編程控制器現(xiàn)在已經(jīng)成為了一個不可代替的控制系統(tǒng),它們可以與其它系統(tǒng)通訊,提供產(chǎn)品報表,生產(chǎn)調(diào)度,診斷自身和設(shè)備的故障,這些技術(shù)上的改進(jìn),讓PLC成為今天的各行各業(yè)的高質(zhì)量和產(chǎn)量的重要的貢獻(xiàn)者。
由以上特點(diǎn)不難看出,PLC在工業(yè)控制領(lǐng)域,不僅不會逐漸推出,而且會不斷擴(kuò)大他的市場份額。表面上看工控機(jī)的出現(xiàn)給PLC帶來了一定程度的沖擊,但如果我們仔細(xì)分析一下可以看到,工控機(jī)在某種程度上其實(shí)幫助了PLC的發(fā)展,因?yàn)镻LC的可靠性高,易操作,但對與操作員站的一些功能,如曲線處理,數(shù)據(jù)記錄等功能,遠(yuǎn)不及工控機(jī),而工控機(jī)的致命缺陷是可靠性差。所以目前來看工控機(jī)與PLC結(jié)合的控制系統(tǒng)更為完美。工控機(jī)的出現(xiàn)推動了PLC的發(fā)展。
2. PLC發(fā)展的方向
其實(shí)PLC自誕生以來也是在不斷發(fā)展改進(jìn)創(chuàng)新的。
采用新的、先進(jìn)的微處理器和電子技術(shù)達(dá)到快速的掃描時間;
小型的、低成本的PLC,可以替代4到10個繼電器,獲得更大的發(fā)展動力;
高密度的I/O系統(tǒng),以低成本提供了節(jié)省空間的接口;
基于微處理器的智能I/O接口,擴(kuò)展了分布式控制能力。典型的接口如:PID,網(wǎng)絡(luò),CAN總線,現(xiàn)場總線,ASCII通信,定位,主機(jī)通訊模塊,和支持高級語言編程的模塊(如BASIC,PASCAL);
包括輸入輸出模塊和端子的結(jié)構(gòu)設(shè)計改進(jìn),使端子更加集成;
特殊接口允許某些器件可以直接接到控制器上,如熱電偶、熱電阻、應(yīng)力測量、快速響應(yīng)脈沖等;
并且由于工控機(jī),DCS等控制系統(tǒng)的出現(xiàn),將迫使PLC向著功能更多,開放性兼容性更強(qiáng)的方向不斷發(fā)展。
3. 整合多種功能,更加開放的一體化PLC
(1) 更多的高級功能,更簡單快捷的使用
傳統(tǒng)PLC簡單的邏輯控制功能已漸漸不能滿足目前工控領(lǐng)域的要求,許多新的控制系統(tǒng)不再是簡單的邏輯控制而已,增加了許多新的功能要求,如大量數(shù)據(jù)處理,存儲,圖形處理,現(xiàn)地顯示等。
除了要求功能的強(qiáng)大,許多工程開發(fā)人員,以及最終用戶,還希望控制系統(tǒng)的結(jié)構(gòu)更為簡單,開發(fā)使用過程更為快捷,對其他控制系統(tǒng)兼容性,開放性更強(qiáng)。
對于這些需求,美國HORNER公司(GE公司重要合作伙伴)于20世紀(jì)80年代初,最早提出了“Allinone”的一體化控制理念,并一直致力于這一理念產(chǎn)品的研發(fā),推出了世界上最早的一體化控制器――OCS(Operator Control Station)。
傳統(tǒng)的控制系統(tǒng),本地的顯示和PLC一般是分開的,分別用不同的軟件進(jìn)行編輯,之間通過串口通訊連接,這樣開發(fā)人員需要許多時間和精力用在軟件的培訓(xùn)和程序的開發(fā)上,并且串口通訊的可靠性也比較差,易于受到干擾。
而OCS控制器不是單純的PLC,也不是單純的人機(jī)顯示界面,它將PLC,HMI,I/O和強(qiáng)大的網(wǎng)絡(luò)功能完美的結(jié)合到了一體。人機(jī)界面和PLC控制程序的編程用同一套由HORNER開發(fā)的工業(yè)編程軟件CsCAPE完成(支持5種編程語言,標(biāo)配為梯形圖)完成,使用戶使用起來更加方便快捷。
OCS不僅僅是PLC,HMI,I/O和網(wǎng)絡(luò)的簡單整合,并且增加了許多工控機(jī)或組態(tài)軟件的功能。如浮點(diǎn)運(yùn)算,高級數(shù)學(xué)運(yùn)算,圖形曲線(時間曲線,X-Y曲線),歷史數(shù)據(jù)本地記錄(大容量移動存儲卡,2G,HORNER最早采用MicroSD存儲),視頻輸入輸出,專家系統(tǒng),操作界面,數(shù)據(jù)監(jiān)測,文件記錄和打印等。
(2) 更強(qiáng)的通訊功能,更好的開放性
近幾年來,隨著互聯(lián)網(wǎng)技術(shù)的普及與推廣,以太網(wǎng)也得到了飛速發(fā)展,特別是以太網(wǎng)通訊速率的提高、以太網(wǎng)交換技術(shù)的發(fā)展,給解決以太網(wǎng)的非確定性問題帶來了新的契機(jī):首先,以太網(wǎng)的通信速率一再提高,從10Mbps,到100Mbps甚至到10Gbps,;其次,以太網(wǎng)交換機(jī)為連接在其端口上的每個網(wǎng)絡(luò)節(jié)點(diǎn)提供了獨(dú)立的帶寬,連接在同一個交換機(jī)上的不同的設(shè)備不存在資源的爭奪,這就相當(dāng)于每個設(shè)備獨(dú)占一個網(wǎng)段;第三,全雙工技術(shù)又為每個設(shè)備與交換機(jī)端口之間提供了發(fā)送與接收的專用通道,因此使不同的以太網(wǎng)設(shè)備之間的沖突大大降低(半雙工交換式)或完全避免(全雙工交換式)。因此,以太網(wǎng)成了確定的網(wǎng)絡(luò),從而為它應(yīng)用于工業(yè)自動化控制消除了主要的障礙。
與其它現(xiàn)場總線或工業(yè)通信網(wǎng)絡(luò)相比,以太網(wǎng)具有應(yīng)用廣泛、成本低廉、通信速率高、軟硬件資源豐富、易于與INTERNET連接、可持續(xù)發(fā)展?jié)摿Υ蟮葍?yōu)點(diǎn),不僅壟斷了工廠綜合自動化的信息管理層網(wǎng)絡(luò),而且在過程監(jiān)控層網(wǎng)絡(luò)也得到了廣泛應(yīng)用,并有直接向下延伸,應(yīng)用于工業(yè)現(xiàn)場設(shè)備層網(wǎng)絡(luò)的趨勢。
PLC的未來發(fā)展除了產(chǎn)品本身的發(fā)展,更大程度上取決于用戶和市場的發(fā)展,任何產(chǎn)品存在的根本在于用戶和市場的需求。PLC以它的高可靠性和易操作性,主導(dǎo)了工控行業(yè)數(shù)十年,相信它將繼續(xù)存在且發(fā)展強(qiáng)大下去。
10