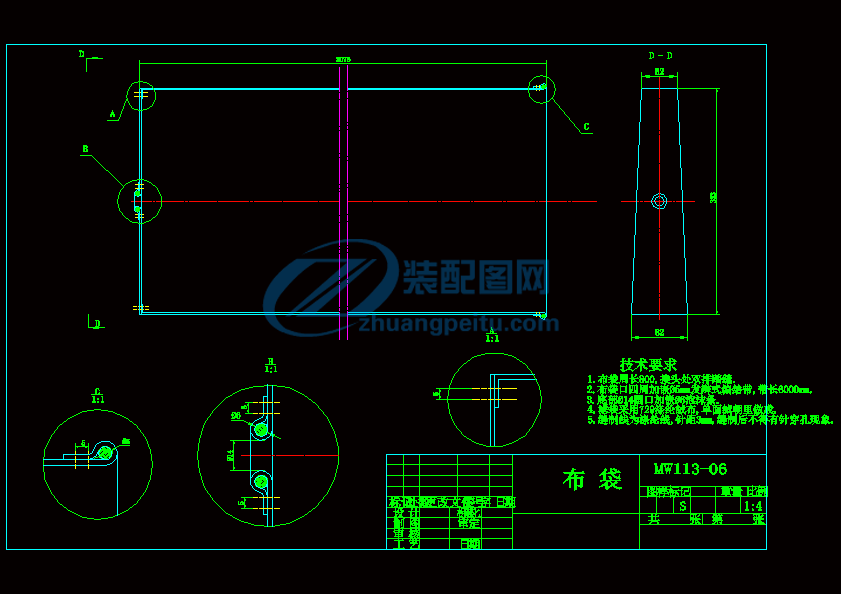
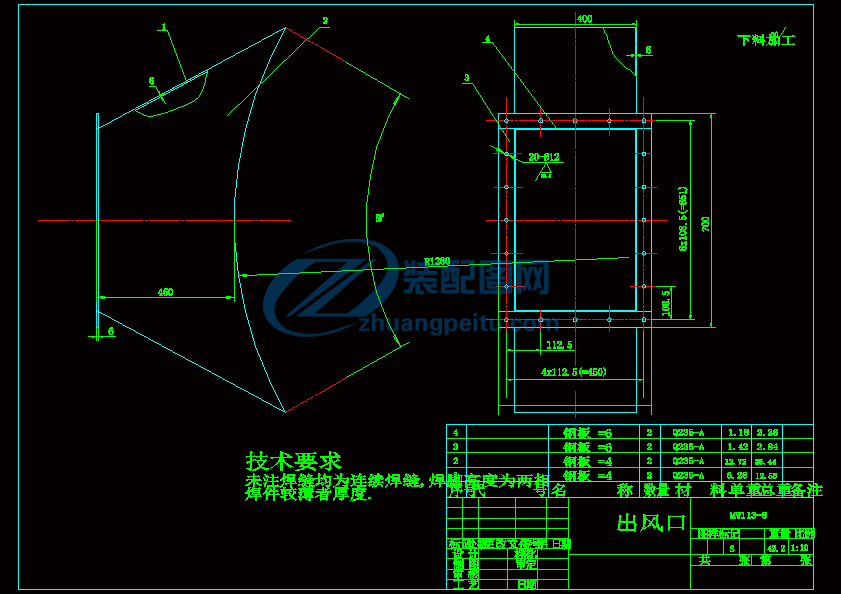
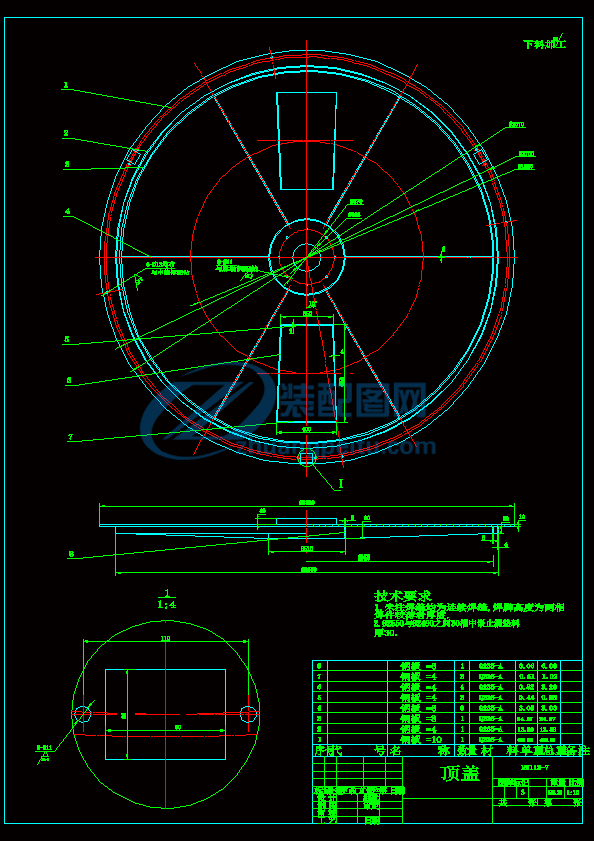
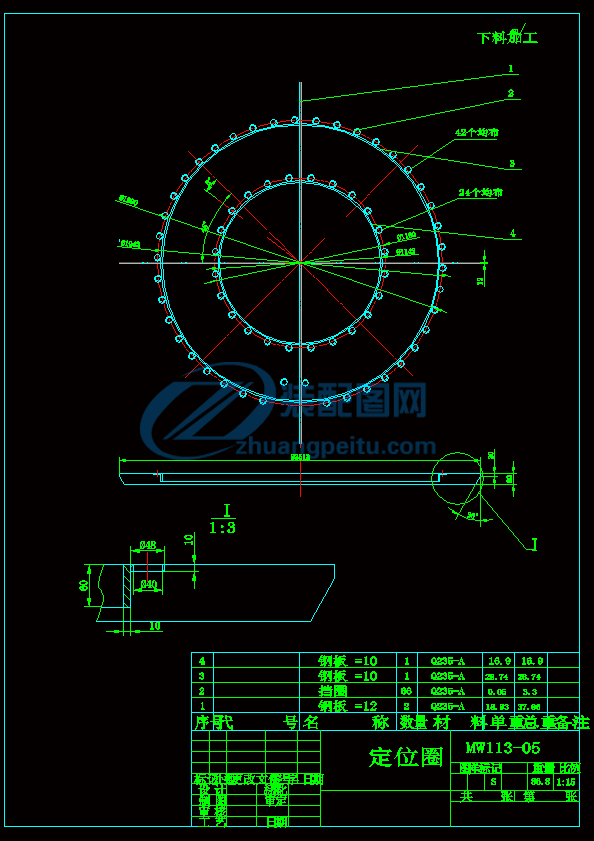
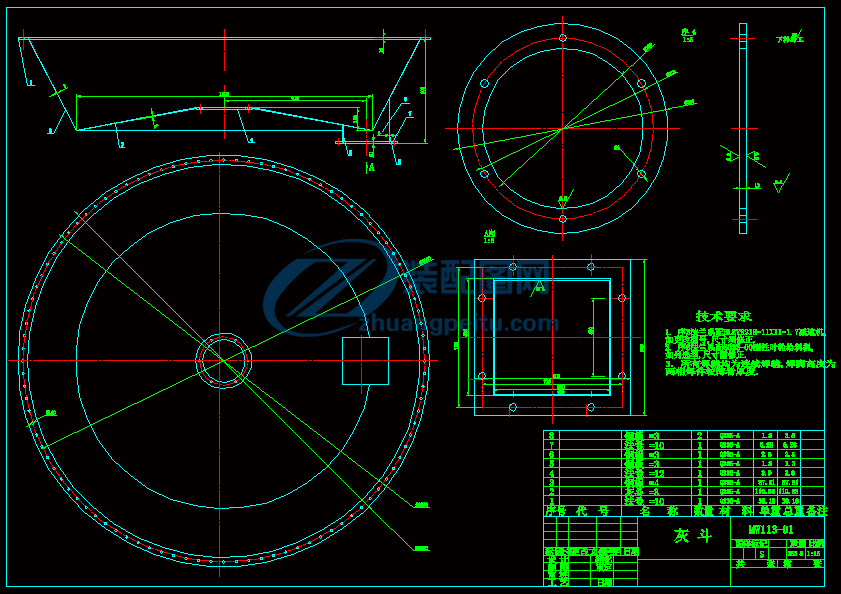

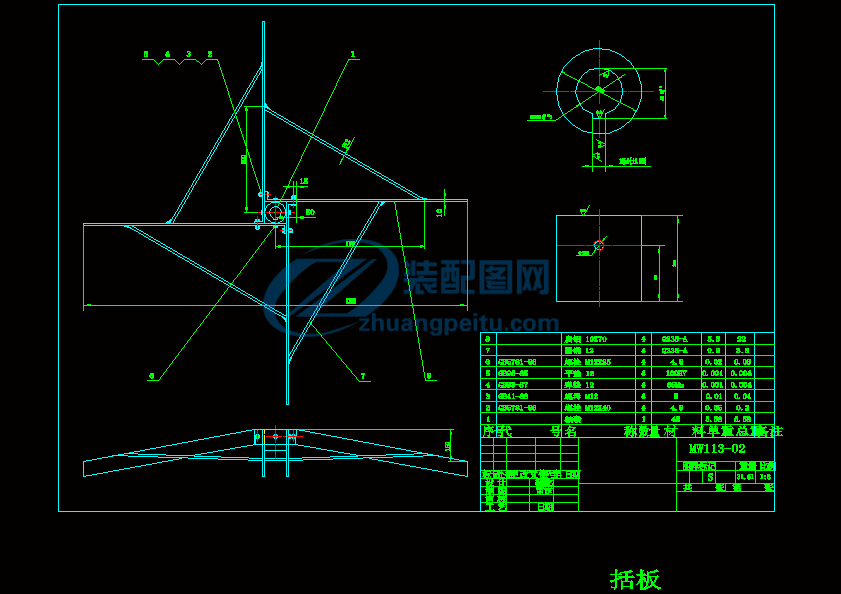

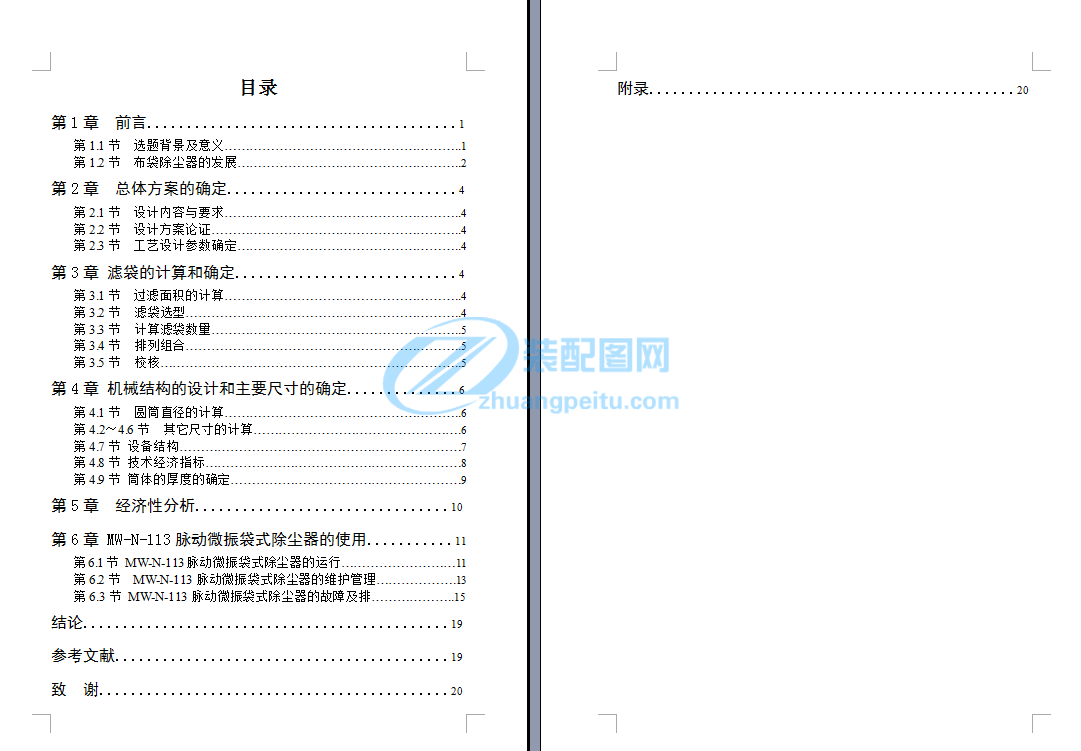
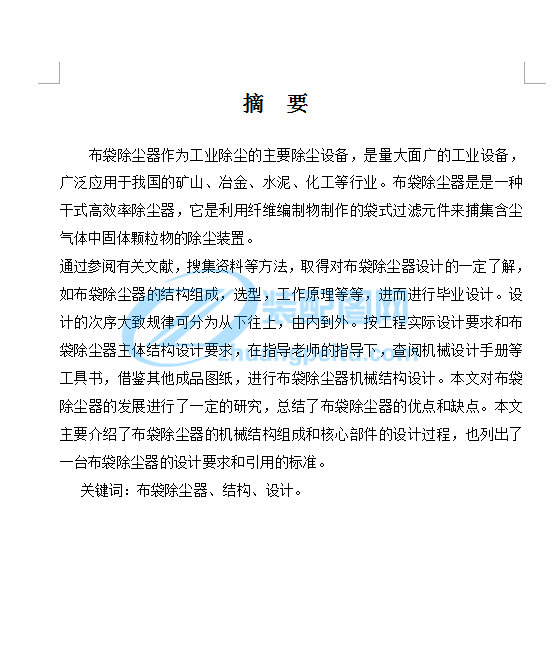
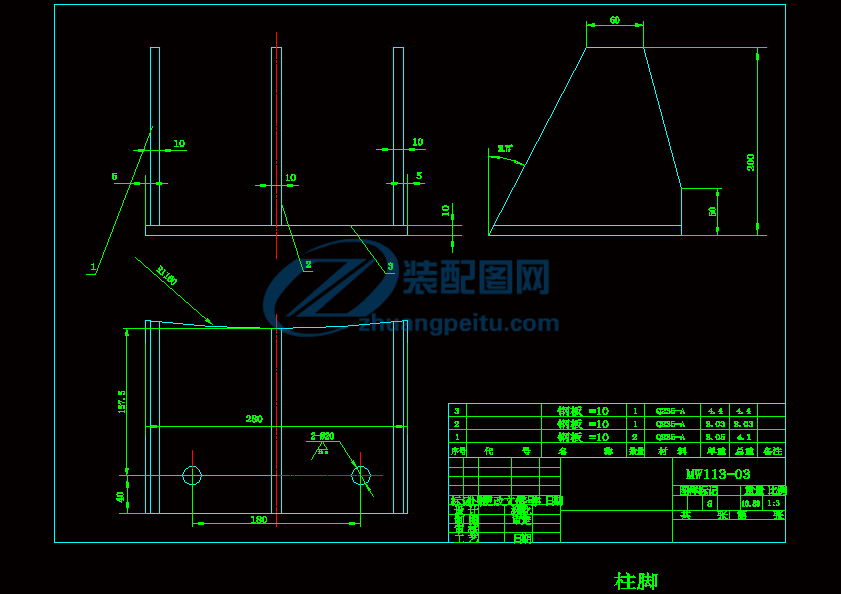
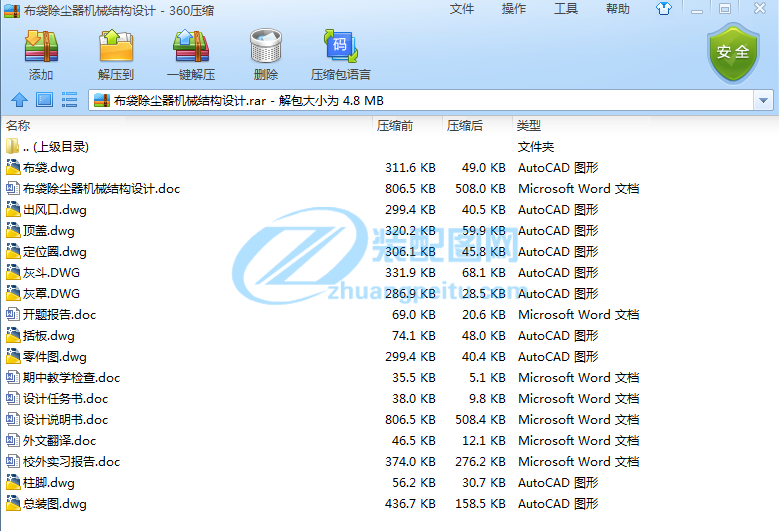
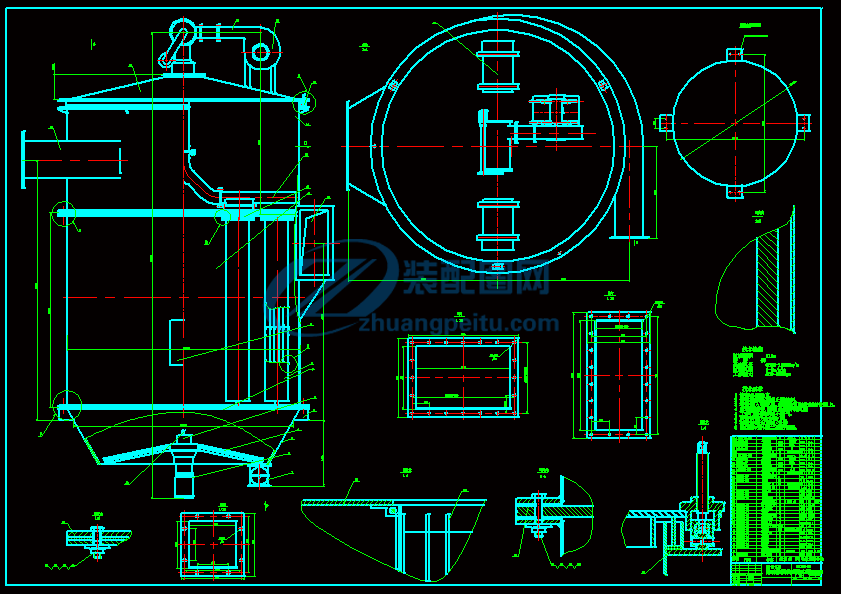
1附錄1)外文翻譯Part 1 Performance characteristicsPlenum pulse bag type collector is a kind of de-dusting equipment with high efficiency. It combines many advantages of collectors including loculose anti-blow and pulse blow, and it has solved the disadvantages of deficiency of kinetic energy strength in loculose anti-blow and pulse blow de-dusting running in the same time, improved the applicability and de-dusting efficiency, extended life span of the bag. There’s no venturi tube in the mouth of bag or blowing tube, that reduces working resistance and makes examining and repairing easy. Electromagnetic pulse valve is of these characters: be sensitive to control, high efficiency, long life span and so on. At present, this type dust collector has been used widely.Part 2 Basic structure and working principle1 StructureMain structures of plenum pulse bag type collector are as followers: box body and bag compartment (integrative), dust store bin, wind inlet and outlet (including screw conveyer and cinder valve), ladder, baluster, air passage system (including offline pneumatic cylinder, electromagnetic pulse valve, compressed air bag), de-dusting controller and so on.(1) Box bodyBox body is mainly used to fix cage, filter bag and air passage components, made into whole close from. Compressed air enters into box body first, and crushes inside of the filter bag while collector is de-dusting. Box body is made into 1.5 degree inclined plane, that can be prevented from seeper when used in 2the open air. There’s a door where someone can examine and repair on the top, installing and replacing cage, filter bag are all done here, that is very convenient. According to the difference of specification, box body is divided into some compartments separated by armor plate between them and impermeable by air, offline de-dusting will come true. There’s a lift valve in each compartment, which breaks and filtrate smoke current of air.(2)Bag compartmentBag compartment is in the below of the box body, mainly used to contain cage and filter bag and from a filtration space, cleaning of smoke is mostly done here. Like the box body, according to the difference of specification, bag compartment is divided into some compartments separated by armor plate between them and prevented from disturbing, at the same time it forms one sedimentation space.There’s a leaked explosive hole on the wainscot of each compartment, the number of leaked explosive hole is 8.Coal preparation equipment, there’re some coal fines produced in the process of coal preparation, but concentration of coal fine is far less than 65g/m3, so collector must not set leaked explosive holes. Even so, the filter bag should adopt antistatic filter material. You set leaked explosive hole whose area is 0.3m2 according to the structure of wainscot position. Choose the material whose thickness is equal to 1 mm L2-M anneal industrial pure aluminum plank, and the anti-pulls strength of industrial pure aluminum plank is 60Mpa, compared with the anti-pulls strength that is not less than 375Mpa of the carbon structure steel wall plank that the thickness is equal to 4 mm. The leaked explosive hole can ensure that dust collector operates in a safe condition.3(3)Dust store binDust store bin is below of the bag compartment, used to store collected dust. Dust-laden gas enter into dust store bin first before into bag compartment, that the speed of gas falls and the direction of current.(4)Wind inlet and outletThere are two kinds of wind inlet and outlet according to the structure of the duster. The wind inlet of the 32 series is a cylinder type, and is directly welded on the lateral plate of the dust store bin. The wind outlet is in the bottom, at the side of the bag compartment, connected with inner side of the bag compartment by the plate hole of the lift valve to, other series of wind inlet and outlet are made into to a whole, put on the side of the bag compartment. The bag compartmentis separated two parts from the dust store bin by a slant board, with one part as the inlet and the other outlet. Though this structure is of a big volume, the air is evenly distributed, with a good effect, and suitable for occasions where dust-laden gas is of a great concentration.2 Working principle of plenum pulse bag type collectorWhen dust-laden gas enters the dust store bin from the inlet, some heavier dust drops into the dust store bin as a result of habitual collision and free settling, large amount of dust follow the rising air current and enter into the inside of bag compartment. Dust is detained outside the filter bag after being filtered by filter bags, and the purified gas goes into the bag compartment from inside the filter bag, then discharged into the air through the hole of the valve board and the outlet. As it goes on and on, the dust detained outside the filter bag increases, so it causes operating resistance of dust collector rising. If the resistance rises to the 4pre-set number(1245-1470Pa), the controller will send out signals, first to control the lift valve to do these operations: close the hole of the valve board to cut air current and stop filtering, and then to open the electromagnetic pulse valve to blow compressed air whose pressure is 0.5-0.7Mpa into filter bag with a short time(0.01-0.12s). The compressed air immediately expands and swarms into filter bag, that make the bag to distort and vibrate, adding the effect of adverse air current, the dust detained outside of filter bag is dropped into the dust store bin. After the de-dusting is finished, lift valve open again, and dust collector begin filtering once more.Plenum pulse bag type collector is made up of several compartments, where de-dusting is in order, and this is compartment-by-compartment off-line de-dusting. Its advantages are that the de-dusting compartment and the filtering compartment do not interfere each other, help realizing long-term consecutive operating and improve de-dusting effect. Dust collector using purse-type filter cloth 2Hereinafter, a preferred embodiment of the present invention will be described in detail with reference to FIGS. 2-7. A preferred embodiment of the present invention is constructed so that mixed current containing dust is sucked into the filtering/dust collecting area through the top of the housing to remove fine solid material such as dust, and then purity air is discharged from the bottom of the housing. In purse-type filter cloth 11 shown in FIG. 3, an important component of the present invention, retainers 12 of metal are installed in stack according to the vertical length of the purse-type filter cloth, as shown in FIGS. 5 and 6. 5According to this design, in order to increase the filtering area, the arrangement of the retainers is continuous not intermittent, and in turn the purging area of filtered clean air (purity air) increases in the respective units. Purse-type filter cloth 11 employed into the dust collector of the present invention are divided into various areas as shown in FIGS. 4A-4D so that the purging of purity air is optimally performed independent of the load pressure loss of the filtering area and the length of the filter cloth, greatly reducing current resistance. In purse-type filter cloth 11, as shown in FIG. 5, the unit of retainer is established in such a manner that at least one, or multiple, if necessary, retainers 12 are stacked from the top 11a to the bottom 11b of filter cloth 11. In order to prevent filter cloth 11 from being deformed or distorted due to the mechanical operation of the dust collector, as shown in FIGS. 5 and 6, after a plurality of retainers 12 are stacked in filter cloth 11, a push plate 13 are put on a circular portion 11c formed on the mouth of the filter cloth, and then fastened by bolt 14 and nut 15. Referring to FIGS. 7A, 7B and 7C, purse-type filter cloth 11 of the present invention is made in which purity air purging velocity Vpa, intermediate entry velocity Vmi, and filtering position entry velocity Fev are distributed uniformly. In other words, the purse-type filter cloth becomes the core of combining dust settling area 16, filtering/dust collecting area 17, purity air purging area 18, and dust discharging area 19. For the respective explanations to the various shapes of the filter cloth such as bag, envelope and purse, the bag-shaped filter cloth is cylindrical as shown in FIG. 1C. When this is fixed onto the filter cloth mounting plate, its filtering 6surfaces are trihedron (upper and lower surfaces and circumferential surface). In order to increase the filtering area, the circumferential surface must be increased in length (Fx) while diameter D is constant. The envelope-shaped filter cloth is rectangular and dihedral. In this case, in order to increase its filtering area, the length of envelope must become longer, its width be changed, or the length and width of the envelope be increased simultaneously to thereby increase both sides thereof. This type of filter cloth is unfavorable to large or middle-sized dust collectors in structure. The purse-shaped filter cloth of the present invention is hexahedral, whose top and bottom have similar areas in the original form. In the present invention, two surfaces (upper and lower surfaces) of the hexahedron are set to be constant, and four sides of the twelve sides related to the remaining four surfaces are changed. As the filtering areas of two surfaces increase, the mouth area of the purse increases proportionally to optimally maintain the purging velocity of purity air. By doing so, the pressure loss of the dust collector is compensated to be favorable to the dust collecting function. Though this may be seen as a simple principle, it will be found in the later description that optimal filtering function is exhibited by harmonizing six (front, rear, upper, lower, left and right) kinds of velocity of the filter cloth. Purse-type filter cloth 11 of the present invention assists many functions, and has significantly more advantages than well-known filter cloths. According to these advantages, filter cloth 11 can be easily manufactured. In addition, compared with the conventional filter cloths whose filtering capacity is determined in design and thus extremely limited, the filter cloth of the present invention can exert the maximum of the filtering capacity according 7to the front, rear, left, right, upper and lower flow of mixed current from the center thereof. As shown in FIG. 2, the velocity of the current entering housing 1 through hood 5 from the dust source can be divided into a settling tank entry velocity at which mixed current (dust+air) goes into the housing having purse-type filter cloth 11, a dust settlement velocity inside the housing, an initial entry velocity at which the mixed current directed toward the area of purse-type filter cloth 11 changes its first direction and then enters the filter cloth, an entry velocity at which the mixed current enters the filtering area from the direction-changed initial entry velocity, a velocity, that is, entry velocity for filtering, at which the mixed current goes to a filtering position in the filtering area, a filtering velocity at which the mixed current passes through the filter cloth, and a purging velocity for purity air filtered. 一 性能特點(diǎn)脈沖袋除塵器是一種高效除塵器。它綜合分室反吹和噴吹脈沖等除塵器的優(yōu)點(diǎn),克服了分室反吹時(shí)動(dòng)能強(qiáng)度不夠和噴吹脈沖清灰過(guò)濾同時(shí)進(jìn)行的缺點(diǎn),因而增強(qiáng)了使用適應(yīng)性,提高了收塵效率,延長(zhǎng)了濾袋使用壽命。濾袋上口不設(shè)文氏管,也沒(méi)有噴吹管,降低了工作阻力,使檢修、維護(hù)都相當(dāng)簡(jiǎn)便,電磁脈沖閥具有控制靈敏、效率高、壽命長(zhǎng)等特點(diǎn)。目前,這種型式的袋除塵器已被廣泛選用。二 基本結(jié)構(gòu)及工作原理1 結(jié)構(gòu):氣箱脈沖式袋除塵器的主要結(jié)構(gòu)是,主體由箱體和袋室(一體) ,灰斗、進(jìn)出風(fēng)口(包括螺旋輸送機(jī)和卸灰閥) ,爬梯、欄桿、氣路系統(tǒng)(包括離線氣缸、電磁脈沖閥、壓力氣包等) 、清灰控制器等。8(1)箱體箱體主要是固定袋籠、濾袋及氣路元件之用,并制成全密閉形式,清灰時(shí),壓縮空氣首先進(jìn)入箱體,并沖入各濾袋內(nèi)部。箱體頂部做成 1.5 度斜面,在戶外使用時(shí)可防止積水,頂部還設(shè)有人孔檢修門,安裝和更換袋籠、濾袋全部在這里進(jìn)行,十分方便。根據(jù)規(guī)格不同,箱體內(nèi)又分成若干個(gè)室,相互之間均用鋼板隔開(kāi),互不透氣,以實(shí)現(xiàn)離線清灰,每個(gè)室內(nèi)均設(shè)有一個(gè)提升閥,以通斷過(guò)濾煙氣流。(2)袋室袋室在箱體的下部,主要用來(lái)容納袋籠和濾袋,并形成一個(gè)過(guò)濾空間,煙氣的凈化主要在這里進(jìn)行,同箱體一樣,根據(jù)規(guī)格的不同也分成若干個(gè)室,并用鋼板隔開(kāi),以防在清灰時(shí)各室之間的相互干擾,同時(shí)形成一定的沉降空間。在袋室的壁板上,每個(gè)室設(shè)一個(gè)泄爆孔,共 8 個(gè)泄爆孔。選煤設(shè)備,在選煤的過(guò)程中,雖有些煤粉產(chǎn)生,進(jìn)入除塵的煤粉濃度又遠(yuǎn)小于 65g/m3,除塵器可不設(shè)泄爆孔。雖然如此,除塵器的濾袋采用防靜電濾料。在袋室壁板上按壁板位置結(jié)構(gòu)設(shè)泄爆孔,泄爆孔面積 0.3m2,材質(zhì)選用厚度等于 1mm 的 L2-M 退火的工業(yè)純鋁板,工業(yè)鋁板的抗拉強(qiáng)度約為 60Mpa,與厚度等于 4mm 的碳結(jié)構(gòu)鋼壁板抗拉強(qiáng)度不小于 375Mpa 的抗拉強(qiáng)度比較,泄爆孔是可以起到泄爆作用,保證除塵器安全運(yùn)行。(3)灰斗灰斗布置在袋室的下部,它存放收集下來(lái)的粉塵。當(dāng)含塵氣體進(jìn)入袋室前先進(jìn)入灰斗,由于灰斗內(nèi)容積大,使得氣流速度降低,加之氣流方向的改變,使得較粗的塵籽在這里得到分離,灰斗內(nèi)布置有螺旋輸送機(jī)設(shè)備,出口還設(shè)有回轉(zhuǎn)卸料器或翻板閥等鎖風(fēng)設(shè)備,可連續(xù)進(jìn)行排灰。(4)進(jìn)出風(fēng)口9進(jìn)出風(fēng)口根據(jù)除塵器的結(jié)構(gòu)形式分二種,32 系列的進(jìn)風(fēng)口為圓筒型,直接焊在灰斗的側(cè)板上,出風(fēng)口安排在箱體下部,袋室側(cè)面,通過(guò)提升閥板孔與箱體內(nèi)部相通,其它系列的進(jìn)出風(fēng)口制成一體,安排在袋室側(cè)面,箱體和灰斗之間,中間用斜隔板隔成互不透氣的二部分,分別為進(jìn)氣和出氣口,這種結(jié)構(gòu)形式體積雖大一些,但氣流分布均勻,灰斗內(nèi)預(yù)收塵效果好,適合于煙氣含塵濃度較大的場(chǎng)合使用。2 氣箱脈沖式袋除塵器的工作原理:當(dāng)含塵煙氣由進(jìn)風(fēng)口進(jìn)入灰斗以后,一部分較粗塵料在這時(shí)由于慣性碰撞、自然沉降等原因落入灰斗,大部分塵粒隨氣流上升進(jìn)入袋室,經(jīng)濾袋過(guò)濾后,塵粒被阻留在濾袋外側(cè),凈化的煙氣由濾袋內(nèi)部進(jìn)入箱體,再由閥板孔、出風(fēng)口排入大氣,達(dá)到收塵的目的,隨著過(guò)濾過(guò)程的不斷進(jìn)行,濾袋外側(cè)的積塵也逐漸增多,從而使除塵器的運(yùn)行阻力也逐漸增高,當(dāng)阻力增到預(yù)先設(shè)定值(1245-1470Pa)時(shí),清灰控制器發(fā)生信號(hào),首先控制提升閥將閥板孔關(guān)閉,以切斷過(guò)濾煙氣流,停止過(guò)濾過(guò)程,然后電磁脈沖閥打開(kāi),以極短時(shí)間(0.01-0.12s)向箱體內(nèi)噴入壓力為 0.5-0.7Mpa的壓縮空氣,壓縮空氣在箱體內(nèi)迅速膨脹,涌入濾袋內(nèi)部,使濾袋產(chǎn)生變形、震動(dòng),加上逆氣流的作用,濾袋外部的粉塵便清除下來(lái)掉到灰斗,清灰完畢之后,提升閥再次打開(kāi),除塵器又進(jìn)入過(guò)濾狀態(tài)。氣箱脈沖式袋除塵器是由多個(gè)室組成的,清灰時(shí),各室分別順序進(jìn)行,這就是分室離線清灰,其優(yōu)點(diǎn)是清灰的室和正在過(guò)濾的室互不干擾,實(shí)現(xiàn)了長(zhǎng)期連續(xù)作業(yè),提高了清灰效果。小型濾袋除塵器在下文中,現(xiàn)有發(fā)明的一種優(yōu)先具體化將會(huì)被參照于圖 2-7 詳細(xì)描述。這種除塵器如此構(gòu)造是為了將當(dāng)前含塵氣體從除塵室的頂部吸入進(jìn)入除塵室,以便去除氣體中的細(xì)小顆粒如灰塵。凈化后的氣體由除塵室底部排出。10在圖 3 中的手提包式濾袋,是除塵器的重要組成部分。底座安裝在垂直于除塵器的方向,如圖 5 和 6 所示。根據(jù)設(shè)計(jì)的要求,為了增加過(guò)濾面積,底座的安排是連體的而不是分開(kāi)的。這樣,凈塵室的過(guò)濾面積就會(huì)在各自單元上增加。如圖 4A-4D 所示,除塵器內(nèi)部安裝的濾袋被分為若干個(gè)區(qū)域,這樣純凈空氣的清洗過(guò)程就獨(dú)立于過(guò)濾面積的負(fù)荷壓力損失而適宜完成。濾袋的長(zhǎng)度會(huì)大大減小流通阻力。在此除塵器中,如圖 5 所示,固定器的單位建立了這樣一種方式——至少一位或多個(gè),如果有必要,固定器 12 堆積從濾布 11 的頂部 11a 到底部11b。為了防止濾布由于除塵器的機(jī)械運(yùn)轉(zhuǎn)而被扭曲或彎折,如圖 5 和 6所示,除了一組濾組安裝于除塵器內(nèi),推板上會(huì)放一個(gè)圓形的部分 11c 于濾布的口上,然后通過(guò)螺栓和螺母牢 14 15。如圖 7A,7B,7C 所示,除塵器的純凈空氣凈化速度和中部入口速度以及過(guò)濾入口流速分布均勻。換句話說(shuō),濾布是結(jié)合粉塵過(guò)濾/收塵面積,純潔空氣凈化的地區(qū) 17 18 和塵埃放電區(qū) 19 的核心部分。對(duì)各個(gè)解釋各種形狀的濾布如袋,信封和錢包,濾布的形狀是圓柱形,如圖 1C。當(dāng)這是固定在安裝板,濾布過(guò)濾的表面是上下表面和圓周表面。為了增加過(guò)濾面積,焊縫表面必須增加的長(zhǎng)度(Fx),直徑 D 是不變的。除塵器的濾袋為矩形兩面的。在這種情況下,為了提高過(guò)濾面積、長(zhǎng)度的濾袋必須變的更長(zhǎng),其寬度被改變,或者長(zhǎng)度和寬度增加同時(shí)從而使雙方同時(shí)增強(qiáng)。這種類型的濾布不宜對(duì)大型或中等大小的含塵濃度在結(jié)構(gòu)。除塵器的濾布是立體的,其頂部和底部在原來(lái)的形狀上有相似的領(lǐng)域在本除塵器中,兩個(gè)表面(上部和下部的表面)的六面體走向是不變的,和四個(gè)側(cè)面的十二個(gè)方面相關(guān)的其他四個(gè)表面將被改變。作為過(guò)濾領(lǐng)域的11兩個(gè)平面口面積增加,增加的比例來(lái)最大化保持除塵器凈化空氣的速度。通過(guò)這么做,壓力損失的補(bǔ)償?shù)某龎m器向有利于除塵功能。盡管這可能被看成是一個(gè)簡(jiǎn)單的原則,它將被發(fā)現(xiàn)在以后的描述狀態(tài)最優(yōu)濾波函數(shù)所展現(xiàn)出協(xié)調(diào)六(前、后、上,降低,左和右)種速度的濾布。濾布具有許多功能,并具比知名濾布顯著更多的好處。根據(jù)這些優(yōu)點(diǎn),可以很容易地完成濾布 11 的制造。此外,傳統(tǒng)的濾布的過(guò)濾能力取決于設(shè)計(jì),因此極其有限, 本濾布的發(fā)明能發(fā)揮最大的過(guò)濾能力,根據(jù)前、后、左、右、高低流量的混合電流中心,制定本辦法。如圖 2,進(jìn)入除塵室的液體速度可分為入口速度,混合流體剛剛進(jìn)入除塵定入口的速度,濾袋過(guò)濾速度,進(jìn)入濾袋過(guò)濾面積內(nèi)的流體速度,塵粒沉積下降速度,混合氣流進(jìn)入除塵器,這時(shí)含塵氣體開(kāi)始改變流動(dòng)方向,進(jìn)入過(guò)濾袋。其中一個(gè)就是,入口速度進(jìn)行濾波相結(jié)合的方法,在從混合氣流到過(guò)濾位置,在過(guò)濾面積,過(guò)濾速度相混合的氣流通過(guò)濾布,凈化空氣從而得到清潔的空氣。2)MW-N-113 脈動(dòng)微振袋式除塵器工程總圖(另外打?。?)MW-N-113 脈動(dòng)微振袋式除塵器零件圖(另外打?。?/div>
收藏