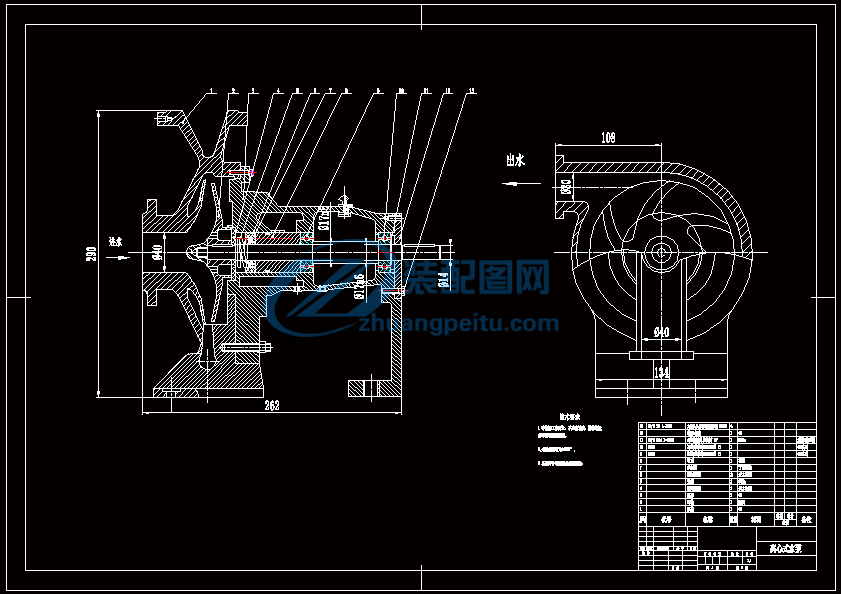
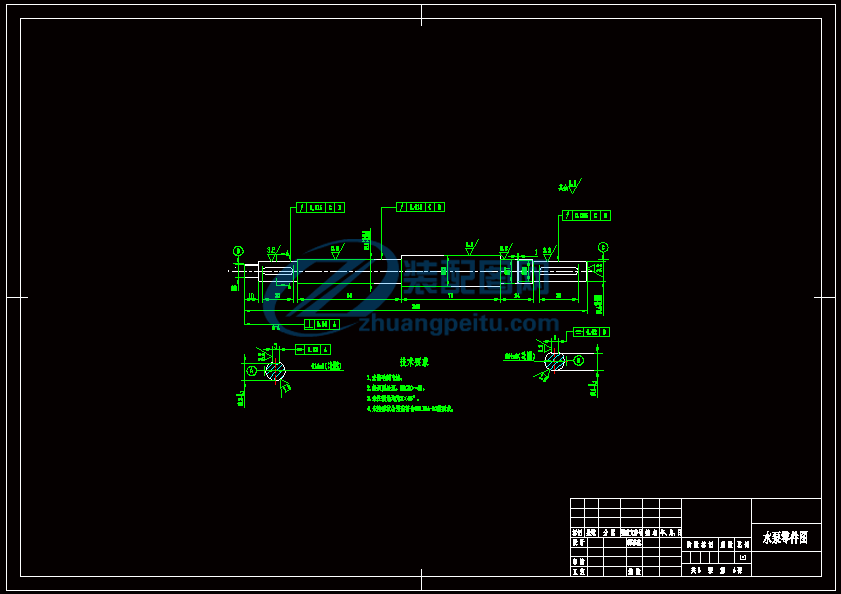
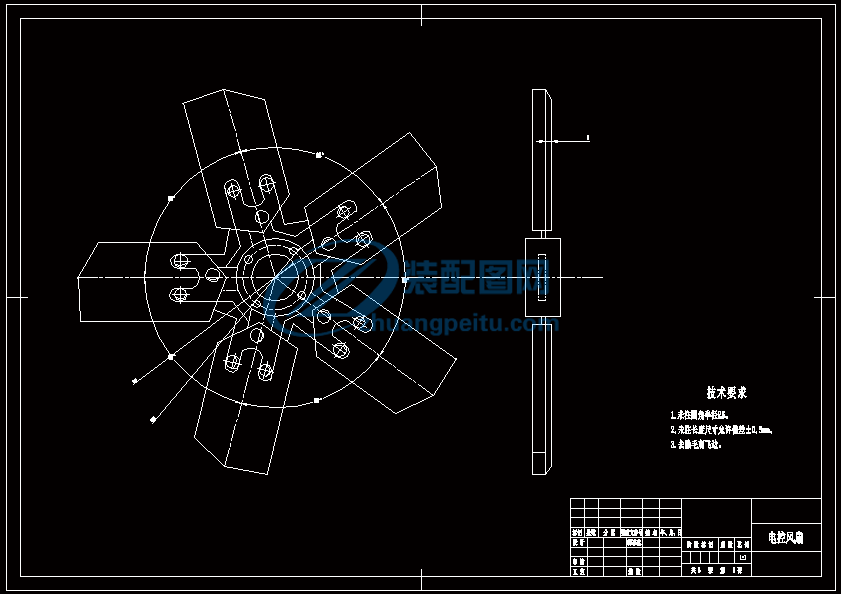
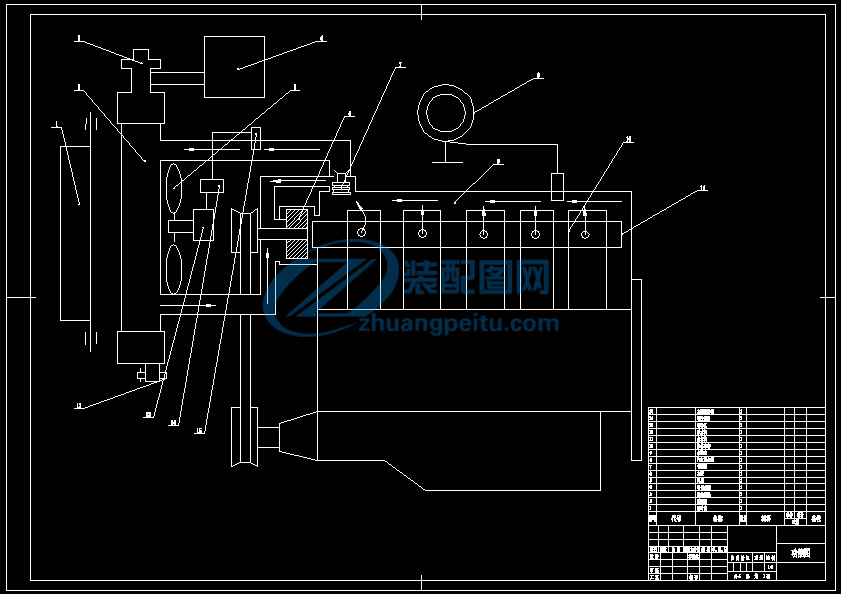
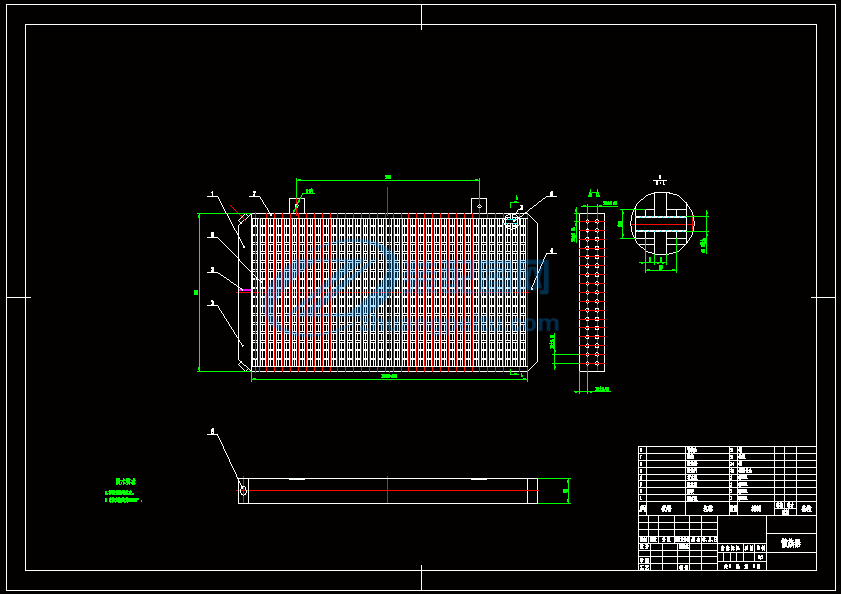

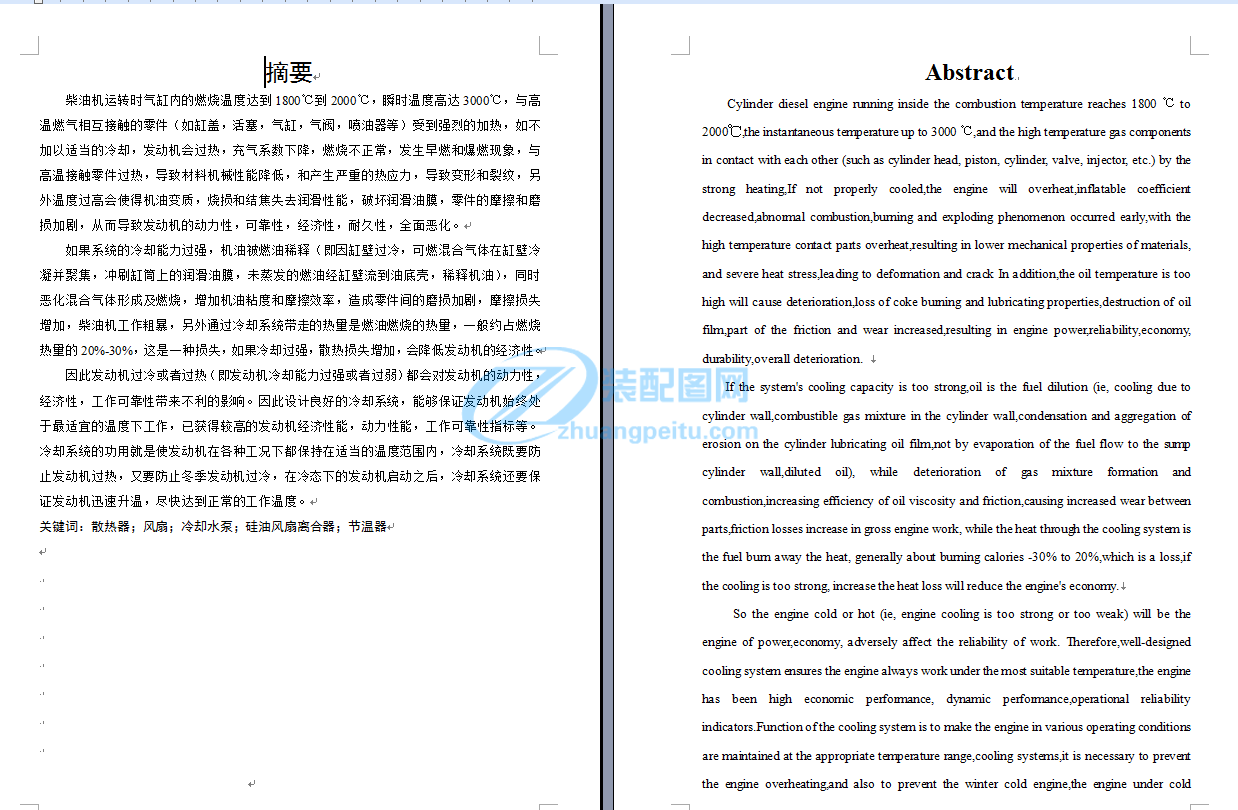
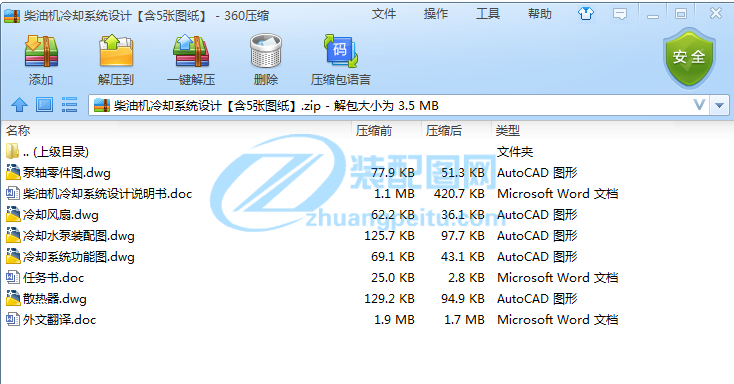
附錄A譯文
非線性不確定系統(tǒng)汽車結(jié)構(gòu)的優(yōu)化設(shè)計(jì)
閻浮
福特汽車公司,MD2115,SRL2122,Dearborn,MI48142,美國
KEMAL H.SAHIN
Hechshermer str.2/Geb.51,CPC系統(tǒng) GmbH,D-55131 Mainz,德國
摘要:隨著計(jì)算機(jī)應(yīng)用的不斷發(fā)展,汽車結(jié)構(gòu)設(shè)計(jì)恰當(dāng)?shù)膽?yīng)用計(jì)算機(jī)方法并給新車的開發(fā)帶來了更大的效率。大多數(shù)以虛擬為基礎(chǔ)的優(yōu)化方法的產(chǎn)生確定性最優(yōu)化沒有考慮到在模型虛擬和制造方面的多種影響。這種遺漏的主要原因是因?yàn)槠嚱Y(jié)構(gòu)設(shè)計(jì)的單一碰撞分析的計(jì)算時(shí)間即使用美國最先進(jìn)的計(jì)算機(jī)也需要大量的時(shí)間。這就需要不確定性優(yōu)化方法的發(fā)展和執(zhí)行效率。在這篇文章中,一種包含元模型優(yōu)勢(shì)技術(shù)和非線性不確定性優(yōu)化方法的綜合的隨機(jī)優(yōu)化方法被提出以用于汽車的側(cè)面碰撞設(shè)計(jì)。非線性元模型用逐步回歸方法去代替昂貴的計(jì)算模型和應(yīng)用BONUS來得到不確定性的優(yōu)化設(shè)計(jì)。汽車安全設(shè)計(jì)的基準(zhǔn)問題曾經(jīng)用來描述這種方法。這一案例研究的目的是維持和加強(qiáng)汽車側(cè)面碰撞測(cè)試實(shí)驗(yàn),盡量減少汽車重量。
關(guān)鍵詞:元模型,非線性規(guī)劃,不確定性優(yōu)化,隨機(jī)優(yōu)化,汽車側(cè)面碰撞
1. 簡(jiǎn)介
汽車碰撞的計(jì)算機(jī)分析對(duì)于減少新產(chǎn)品的開發(fā)時(shí)間是一個(gè)有效的工具?,F(xiàn)在非線性有限元基礎(chǔ)碰撞分析代碼普遍應(yīng)用與模擬汽車碰撞試驗(yàn)例如,前懸的影響,邊緣的影響,內(nèi)部前面影響,后懸影響。
數(shù)字優(yōu)化是有用的系統(tǒng)的工具對(duì)于自動(dòng)選擇優(yōu)先設(shè)計(jì)參數(shù)。這種方法在汽車工業(yè)得到了廣泛應(yīng)用并且取得了顯著效果。然而為了保證產(chǎn)品質(zhì)量和產(chǎn)品使用性,在模型模擬,和制造上的不確定因素需要考慮。一種新的隨機(jī)優(yōu)化方法被稱作bonus由Sahin和Diwekar開發(fā)。Bonus用樣本估算目標(biāo)和約束因素通過不確定因素。這種技術(shù)在優(yōu)化過程中通過重復(fù)衡量的方法減少了過度繁瑣計(jì)算的重?fù)?dān)。然而汽車碰撞分析是密集的計(jì)算,它通過用當(dāng)前的計(jì)算機(jī)花費(fèi)幾小時(shí)到幾天的時(shí)間來控制一個(gè)虛擬。因此工程師利用許多元模型及時(shí)被用來建立代理模型(也被叫做元模型或響應(yīng)表面模型)去代替昂貴的計(jì)算模型以及時(shí)的方法去解決現(xiàn)實(shí)問題。本期刊提出了結(jié)合元模型和非線性系統(tǒng)的優(yōu)化設(shè)計(jì)的綜合方法進(jìn)行汽車結(jié)構(gòu)設(shè)計(jì)。
車輛側(cè)面碰撞的問題,是眾所周知的自動(dòng)化工業(yè)的基準(zhǔn)問題,被用來描述集成方法。這種方法被產(chǎn)業(yè)和學(xué)術(shù)研究者廣泛應(yīng)用區(qū)描述各種在元模型上的新方法,可靠性基礎(chǔ)設(shè)計(jì)優(yōu)化,隨機(jī)優(yōu)化設(shè)計(jì)和多學(xué)科設(shè)計(jì)優(yōu)化。表面模型的全球反映產(chǎn)生于用逐步回歸耦合優(yōu)化超立方體樣本的設(shè)計(jì)實(shí)驗(yàn),該實(shí)驗(yàn)被認(rèn)為是這種研究的真正模型。傳統(tǒng)的Monte Carlo方法和BONUS是用來解決不確定性的優(yōu)化問題。通過Monte Carlo方法和BONUS的大量對(duì)比試驗(yàn)出來這樣的結(jié)論,優(yōu)化過程是通用的也同樣能夠應(yīng)用在其他工程領(lǐng)域。
接下來的部分簡(jiǎn)要的介紹了綜合BONUS算法,第三部分介紹了汽車側(cè)面碰撞問題目的在于盡量減少汽車重量以維持和加強(qiáng)汽車側(cè)面碰撞測(cè)試實(shí)驗(yàn)。第四部分提出了魯棒性基線和確定性優(yōu)化設(shè)計(jì)以及考慮到多種不確定性的隨機(jī)優(yōu)化設(shè)計(jì)的方法,即傳統(tǒng)的設(shè)計(jì)方法和BONUS算法。最后第五部分得出結(jié)論。
2. 一種綜合的BONUS算法
常用的隨機(jī)優(yōu)化方法包括兩種密集遞歸循環(huán):(1)內(nèi)部樣本循環(huán),和(2)外部?jī)?yōu)化循環(huán)。內(nèi)部樣本循環(huán)普遍應(yīng)用的方法是Monte Carlo技術(shù),這種技術(shù)是從假象輸入分布中隨機(jī)進(jìn)行樣本選擇來得到輸出分布和相關(guān)的統(tǒng)計(jì)特性,比如平均值,方差,或百分率。一種解決非線性規(guī)劃問題的外部?jī)?yōu)化設(shè)計(jì)數(shù)字方法是序列二次規(guī)劃。隨著優(yōu)化過程和新設(shè)計(jì)變量的確定,不確定變量的改變導(dǎo)致新的輸出分布。在優(yōu)化迭代中,甚至是小的樣本數(shù)據(jù),對(duì)模型的重復(fù)評(píng)價(jià)是顯著的瓶頸。
以有限元為基礎(chǔ)的整車結(jié)構(gòu)碰撞模擬式汽車工業(yè)用于評(píng)價(jià)汽車碰撞性能常用的設(shè)計(jì)工具。對(duì)于大多數(shù)的應(yīng)用中,為了解決問題及時(shí)的優(yōu)化和魯棒性分析用在元模型上,用不同的元模型方法以小數(shù)量的有限元模擬建立的。在衡量了一些元模型技術(shù)后,yang推薦使用第二多項(xiàng)式回歸模型和移動(dòng)最小二乘回歸模型進(jìn)行汽車安全性優(yōu)化。
在優(yōu)化過程中由Sahin和Diwekar開發(fā)的BONUS算法用來有效地估計(jì)隨機(jī)目標(biāo)和約束職能。傳統(tǒng)的方法依賴于開發(fā)一個(gè)樣本循環(huán)和評(píng)估由輸入分布產(chǎn)生的每一個(gè)樣本循環(huán)。另外,BONUS算法是通過整個(gè)輸入空間對(duì)均勻分布參數(shù)運(yùn)行模型首先產(chǎn)生基本分布的所有響應(yīng),然后在對(duì)輸出分布的概率進(jìn)行密度估計(jì)的基礎(chǔ)上用衡量的方法對(duì)輸出分布進(jìn)行估算。在Sahin和Diwekar的期刊中可以找到BONUS算法的具體闡釋。這種技術(shù)的有點(diǎn)事在每一次迭代中對(duì)新樣本模型通過性的評(píng)估是對(duì)隨機(jī)優(yōu)化的計(jì)算集中。對(duì)于優(yōu)化計(jì)算來說利用每一次設(shè)計(jì)變量在目標(biāo)和約束職能上的小的增量和計(jì)算變量的無數(shù)的梯度擾動(dòng)是至關(guān)重要的。另外一個(gè)優(yōu)勢(shì)是這種算法無需額外的昂貴的模型模擬便提供了開發(fā)完全設(shè)計(jì)空間的收斂概率。
圖一顯示了用傳統(tǒng)的Monte Carlo方法和新的綜合BONUS方法進(jìn)行不確定性過程的優(yōu)化。首先,實(shí)驗(yàn)技術(shù)設(shè)計(jì)是通過輸入空間產(chǎn)生統(tǒng)一樣本,接下來用有限元模型進(jìn)行設(shè)計(jì)。第二,利用有限元模型模擬結(jié)果通過元模型技術(shù)建立元模型。第三,最優(yōu)化解決方案是通過從不同初始點(diǎn)開始的大量樣本用Monte Carlo方法得到的。同BONUS算法比較這種設(shè)計(jì)被認(rèn)為是全面的真正的全面的解決方案。BONUS在最優(yōu)化設(shè)計(jì)中提出了魯棒評(píng)價(jià),該評(píng)價(jià)開始與相同設(shè)置的不同初始點(diǎn),一個(gè)對(duì)比得到了。最后得到了兩種算法的比較結(jié)果。
圖1. 在不確定性下利用傳統(tǒng)Monte Carlo方法和新的綜合BONUS方法優(yōu)化
3. 汽車側(cè)向碰撞設(shè)計(jì)問題
汽車的側(cè)向碰撞模型在圖2中列舉出來。系統(tǒng)模型包括一個(gè)整車有限元結(jié)構(gòu)模型,一個(gè)有限元側(cè)向碰撞模擬模型,和有限元側(cè)面碰撞變形障礙模型。系統(tǒng)模型包括85941個(gè)外殼元素和96122個(gè)節(jié)點(diǎn)。在有限元模擬側(cè)面碰撞試驗(yàn)中,障礙物有48.89千米每小時(shí)的初始速率和碰撞汽車結(jié)構(gòu)。在一個(gè)原始的SGI2000的計(jì)算機(jī)上用RADIOSS軟件進(jìn)行非線性有限元模擬需要20小時(shí)。設(shè)計(jì)的目標(biāo)是盡量減少汽車重量以維持和加強(qiáng)側(cè)面碰撞性能。
對(duì)于汽車的側(cè)面保護(hù),汽車設(shè)計(jì)需要滿足或者超過汽車市場(chǎng)對(duì)側(cè)面碰撞需要和指定的規(guī)定。兩個(gè)基本的側(cè)面碰撞保護(hù)規(guī)則是美國聯(lián)邦汽車安全標(biāo)準(zhǔn)214號(hào)和美國經(jīng)濟(jì)委員會(huì)歐洲規(guī)則95號(hào)
圖2.汽車側(cè)面碰撞模型
在這項(xiàng)研究中,ECE側(cè)面碰撞試驗(yàn)被應(yīng)用。在側(cè)面碰撞的研究中的模擬響應(yīng)時(shí)主公制。ECE側(cè)面碰撞規(guī)定中指定的碰撞模擬標(biāo)準(zhǔn)包括腹路粘性標(biāo)準(zhǔn)車身轉(zhuǎn)向和公共symphysis力。模擬響應(yīng)必須滿足或超過ECE標(biāo)準(zhǔn)。其它側(cè)面碰撞設(shè)計(jì)的內(nèi)容是在中點(diǎn)時(shí)的B-Pillar速率和前門的B-Pillar速率。
對(duì)于側(cè)面碰撞,厚度設(shè)計(jì)變量的增加在某種程度上可能會(huì)加強(qiáng)模擬實(shí)驗(yàn)性能。然而,他也會(huì)增加汽車重量,緊接著會(huì)造成燃料經(jīng)濟(jì)性上的欠缺。因此,必須尋找減輕重量和增加安全性能之間的平衡。這次研究的目標(biāo)就是在減輕汽車重量的同時(shí)保證汽車模擬測(cè)試性能。表1列舉了ECE規(guī)則和基準(zhǔn)模型的設(shè)計(jì)規(guī)則。因?yàn)楸酒诳难芯糠秶顷U述綜合BONUS方法的好處所以注意那些數(shù)字變量和設(shè)計(jì)目標(biāo)是illustrative。
應(yīng)用于汽車側(cè)面碰撞試驗(yàn)的九個(gè)設(shè)計(jì)變量被汽車工程師證明了。設(shè)計(jì)變量是厚度和重要部分的material properties。所有的厚度設(shè)計(jì)變量都是連續(xù)的在一定范圍內(nèi)變化的x0是設(shè)計(jì)變量的基準(zhǔn)。這兩種材料設(shè)計(jì)變量是分離的,并且是低碳鋼或者高碳鋼。在側(cè)面碰撞模型中假設(shè)這些變量是在這9個(gè)設(shè)計(jì)變量周圍獨(dú)立的正常分布的非確定性變量。兩個(gè)輔助的不確定分離變量需要高碳鋼和低碳鋼材料的代替,兩個(gè)額外的不確定因素是障礙高度和碰撞位置,他們也符合正常分布。不確定變量的標(biāo)準(zhǔn)分布列在表2中。
在這篇期刊中Gu建立的元模型用在了這一基本問題上。元模型技術(shù)在33個(gè)優(yōu)化超立方樣本上用二次方程式后退回歸的方法解決汽車側(cè)面碰撞問題,所有的這11個(gè)響應(yīng)的元模型總結(jié)如下:
4. 隨機(jī)優(yōu)化設(shè)計(jì)
在工程設(shè)計(jì)中,確定優(yōu)化設(shè)計(jì)在降低系統(tǒng)設(shè)計(jì)費(fèi)用和提高使用性能上得到了廣泛應(yīng)用,然而在制造或工程模擬中實(shí)際上存在的不確定因此需要包括不確定性的隨機(jī)優(yōu)化設(shè)計(jì)。為了比較確定優(yōu)化設(shè)計(jì)和不確定優(yōu)化設(shè)計(jì)的表現(xiàn),這一部分首先解決確定性優(yōu)化設(shè)計(jì)的問題,見表三。確定性優(yōu)化設(shè)計(jì)在不考慮不確定性因素的情況下通過基線設(shè)計(jì)提高了汽車側(cè)面碰撞測(cè)試性能同時(shí)減低了汽車重量。
汽車碰撞隨機(jī)優(yōu)化問題在2中得以確切的闡述:
可以注意到如果一個(gè)分布響應(yīng)符合正常分布,一個(gè)特定限制的約束與百分之九十的可靠性是相同的。還可以了解到本文提出的這種方法可以很容易的通過改變目標(biāo)變量去執(zhí)行魯棒設(shè)計(jì)以達(dá)到盡量減小響應(yīng)的差異,比如重量。
基于曲面元模型,傳統(tǒng)的方法解決了隨機(jī)優(yōu)化的問題,Monte Carlo利用魯棒評(píng)定對(duì)大量的樣本進(jìn)行了模擬。然后用開始于200個(gè)初始點(diǎn)的SQP尋找設(shè)計(jì)變量的優(yōu)化方法。表四列舉了用傳統(tǒng)方法進(jìn)行基線魯棒評(píng)定的結(jié)果和確定性及隨機(jī)優(yōu)化設(shè)計(jì)。這一結(jié)果顯示了不確定因素對(duì)基線設(shè)計(jì)和確定優(yōu)化設(shè)計(jì)的影響。另一方面,隨機(jī)優(yōu)化設(shè)計(jì)提高了汽車側(cè)面碰撞性能并減小了汽車的重量。傳統(tǒng)方法中隨機(jī)優(yōu)化設(shè)計(jì)的應(yīng)用獎(jiǎng)拿來與BONUS算法中的優(yōu)化設(shè)計(jì)進(jìn)行比較。因?yàn)锽ONUS得主要優(yōu)勢(shì)是在反復(fù)優(yōu)化中用衡量的方法估算目標(biāo)函書和約束函數(shù)去代替模型模擬,這種方法成功的主要是對(duì)相應(yīng)的真實(shí)價(jià)值的準(zhǔn)確預(yù)測(cè)。為了證明用反復(fù)衡量的方法估算的準(zhǔn)確性,在研究中用到了同一分布的200個(gè)獨(dú)立設(shè)計(jì)設(shè)置。為提供更全面的準(zhǔn)確圖片,應(yīng)用了三種不同的方法:絕對(duì)誤差平均值、絕對(duì)誤差分離標(biāo)準(zhǔn)、絕對(duì)誤差最大值。這些方法的方程式在方程式(3)(4)(5)準(zhǔn)確的給出。
Yi代表50000次在元模型基礎(chǔ)上的Monte Carlo模擬得到的真實(shí)響應(yīng)標(biāo)準(zhǔn),另一字母代表相應(yīng)的BONUS預(yù)測(cè)標(biāo)準(zhǔn)。ARAE代表從真實(shí)響應(yīng)標(biāo)準(zhǔn)中分離出來的BONUS估算平均值。ARAE的標(biāo)準(zhǔn)值越小,BONUS估算越精確。
SRAE代表絕對(duì)誤差的延伸,對(duì)于證明ARAE的主要區(qū)別是很有用的。
即使在總體上ARAE的評(píng)定結(jié)果是精確的,在設(shè)計(jì)范圍內(nèi)一個(gè)大的MRAE暗示一個(gè)大的誤差。因此應(yīng)選擇小的MRAE值。
計(jì)算ARAE,SRAE和MRAE的過程包括四步。它們分別是:
第一步,在設(shè)計(jì)空間隨機(jī)生成200個(gè)相同分布的獨(dú)立設(shè)計(jì)。
第二步,根據(jù)它們的不確定性分布生成50000個(gè)MCS值,啟用元模型得到響應(yīng)標(biāo)準(zhǔn),然后計(jì)算每個(gè)響應(yīng)的平均值和差值。
第三步,生成一定數(shù)量的HSS樣本,運(yùn)用元模型得到基本分布的響應(yīng)標(biāo)準(zhǔn),并用BONUS中的衡量方法估算第一步中的200個(gè)設(shè)計(jì)中的每個(gè)響應(yīng)的平均值和差值。
第四步,計(jì)算ARAE,SRAE和MRAE。
表5代表與Monte Carlo模擬的200個(gè)獨(dú)立設(shè)計(jì)的所有響應(yīng)相比較下的BONUS估算中的ARAE,SRAE和MRAE值。通常,估算技術(shù)為真實(shí)響應(yīng)標(biāo)準(zhǔn)提供真實(shí)預(yù)測(cè)。ARAE的生成趨勢(shì)是隨著HSS樣本數(shù)量的增多誤差減少。然而在一些情況下,為了增加HSS樣本的數(shù)量,ARAE標(biāo)準(zhǔn)值也略有增長,但是這些并不是十分重要,事實(shí)上SRAE標(biāo)準(zhǔn)值比兩個(gè)ARAE標(biāo)準(zhǔn)值的差值要大的多。有兩個(gè)比10%大得多的ARAE響應(yīng);它們因?yàn)檫@些約束的相互作用它們并不會(huì)產(chǎn)生負(fù)面的結(jié)果。這些至關(guān)重要的約束,像公共symphysis力量,低骨架轉(zhuǎn)向和B-Pillar速率顯示更好的精確性。令一個(gè)趨勢(shì)是隨著HSS樣本數(shù)量的增加SRAE標(biāo)準(zhǔn)值的減少,這意味著絕對(duì)誤差的擴(kuò)大在縮減。甚至在設(shè)計(jì)中BONUS估算的整車性能是好的,依然會(huì)在一些設(shè)計(jì)空間的一些范圍中存在著困難。這可以從MRAE標(biāo)準(zhǔn)中看出來。通常HSS樣本數(shù)量的增加時(shí)有幫助的,然而,這增加了計(jì)算時(shí)間,這是沒有預(yù)料到的。
根據(jù)不同大量不同的HSS樣本數(shù)據(jù)用BONUS算法得到的結(jié)果見表六。多種優(yōu)化方式會(huì)出現(xiàn)在來自200個(gè)不同起始點(diǎn)的BONUS算法,表六僅僅列舉出了最好的方法。這些結(jié)果顯示:由于估算精確性的問題,樣本數(shù)量越少比如100和150個(gè)HSS點(diǎn),用BONUS算法的優(yōu)化設(shè)計(jì)可能不會(huì)滿足5000個(gè)MCS點(diǎn)所有的約束條件。結(jié)果顯示了用300個(gè)HSS點(diǎn),BONUS算法能得到預(yù)想的滿足所有約束條件并且有好的目標(biāo)值的設(shè)計(jì)。當(dāng)樣本的數(shù)量繼續(xù)增加由500增大到2000,和300個(gè)HSS點(diǎn)比起來BONUS算法的優(yōu)化方式很容易的就可以滿足所有約束上的限制,但是在目標(biāo)值上有一點(diǎn)犧牲。可以看出來在考慮不確定性的情況下,BONUS算法的優(yōu)化設(shè)計(jì)比那些基線設(shè)計(jì)更加輕量化并且在汽車側(cè)面碰撞上有更好的測(cè)試性能。
5. 結(jié)論
一種新的包含有模型技術(shù)和BONUS的綜合隨機(jī)優(yōu)化方法成功的應(yīng)用在汽車側(cè)面碰撞的基本問題上。結(jié)果闡述了綜合BONUS方法能夠在優(yōu)化循環(huán)中用元模型和近似技術(shù)代替模型模擬估算可能的約束和目標(biāo)值,這就減少了計(jì)算量。結(jié)果也顯示了BONUS算法在變量不確定性的條件下盡量減小汽車重量方面是以中很有價(jià)值的工具。
此研究結(jié)論是在假想曲面元模型和FE模型有效和分布于不確定變量準(zhǔn)確地情況下得到的,。然而,模型的有效性和不確定性的系統(tǒng)分析的超出了論文的研究范圍。
致謝
我要感謝Urmila Diwekar先生在BONUS算法上的指導(dǎo)和支持。接下來,我要感謝兩位審閱者提供的寶貴意見。最后我要感謝Sandia 國家實(shí)驗(yàn)室在經(jīng)濟(jì)上對(duì)BONUS算法的援助。
參考文獻(xiàn)
Choi, K.K. and B.D. Youn. (2001). “Hybrid Analysis Method for Reliability-Based Design Optimization.”
In Proceedings of ASME Design Engineering Technical Conferences, Pittsburgh, PA, paper
DETC2001/DAC-21044, pp. 1–10.
Choi, K.K., B.D. Youn, and R.J. Yang. (2001). “Moving Least Square Method for Reliability-Based Design
Optimization.” In Proceedings of 4th World Congress of Structural and Multidisciplinary Optimization,
Dalian, China, pp. 1–6.
Du, X. and W. Chen. (2002). “Sequential Optimization and Reliability Assessment Method for Efficient
Probabilistic Design.” In Proceedings of ASME 2002 Design Automation Conference, Montreal, Canada,
paper DETC2002/DAC-34127, pp. 1–14.
Fu, Y. (2003). “A New Hybrid Stochastic Optimization Method for Vehicle Structural Design.” In Proceedings
of SAE World Congress, Detroit, MI, paper 2003-01-0881, pp. 1–10.
Fu, Y., S. Wang, U.M. Diwekar, and K.H. Sahin. (2002). “A Stochastic Optimization Application for Vehicle
Structures.” In Proceedings of ASME 2002 Design Engineering Technical Conferences, Montreal,
Canada, paper DETC2002/DAC-34075, pp. 1–10.
Gu, L. and R.J. Yang. (2002). “Large-Scale Reliability Based Optimization for Vehicle Crash Safety.” In
Proceedings of the American Statistical Association, Statistical Computing Section (CD-ROM), pp. 1–
10. Alexandria, VA: American Statistical Association.
Gu, L. and R.J. Yang. (2003). “Recent Applications on Reliability-Based Optimization of Automotive
Structures.” In Proceedings of SAE 2003 World Congress and Exhibition, Detroit MI, paper 2003-01-
0152, pp. 1–12.
Gu, L., R.J. Yang, C.H. Tho, M. Makowski, O. Faruque, and Y. Li. (2001). “Optimization and Robustness
for Crashworthiness of Side Impact.” International Journal of Vehicle Design 26(4), 348–360.
Koch, P.N., R.J. Yang, and L. Gu. (2004). “Design for Six Sigma through Robust Optimization.” in Structural
and Multidisciplinary Optimization 26, 235–248.
Kodiyalam, S., R.J. Yang, L. Gu, and C.H. Tho. (2004). “Multidisciplinary Design Optimization of a Vehicle
System in a Scalable, High Performance Computing Environment.” Structural and Multidisciplinary
Optimization 26, 256–263.
Sahin, K.H. and U.M. Diwekar. (2004). “Better Optimization of Nonlinear Uncertain Systems (BONUS):
A New Algorithm for Stochastic Programming Using Reweighting for Density Estimation.” Annals of
Operational Research 132, 47–68.
Silverman, B.W. (1998). Density Estimation for Statistics and Data Analysis. Boca Raton, FL: Chapman &
Hall.
Yang, R.J. and L. Gu. (2004). “Experience with Approximate Reliability-Based Optimization Methods.”
Structural and Multidisciplinary Optimization 26, 152–159.
Yang, R.J., L. Gu, L. Liaw, C. Gearhart, C.H. Tho, X. Liu, and B.P. Wang. (2000). “Approximations for
Safety Optimization of Large Systems.” In Proceedings of ASME Design Engineering Technical Conferences,
Baltimore, MD, paper DETC2000/DAC-14245, pp. 1–10.
Yang, R.J., L. Gu, C.H. Tho, K.K. Choi, and B.D. Youn. (2002a). “Reliability-Based Multidisciplinary
Design Optimization of a Full Vehicle System.” In Proceedings of 43rd AIAA SDM Conference, Denver,
CO, paper AIAA-2002-1758, pp. 1–9.
Yang, R.J., L. Gu, C.H. Tho, K.K. Choi, and B.D. Youn. (2002b). “Reliability-Based Multidisciplinary
Design Optimization of Vehicle Structures.” In Proceedings of IMechE Statistics and Analytical Methods
in Automotive Engineering, London, UK, pp. 1–9.
Yang, R.J., C.H. Tho, and L. Gu. (2002). “Recent Development in Multidisciplinary Design Optimization
of Vehicle Structures.” In Proceedings of 9th AIAA/ISSMO Symposium on MAO, Atlanta, GA, paper
AIAA-2002-5606, pp. 1–8.
Youn, B.D., K.K. Choi, and R.J. Yang. (2003). “Efficient Evaluation Approaches for Probabilistic Constraints
in Reliability-Based Design Optimization.” In Proceedings of 5th World Congress on Structural
and Multidisciplinary Optimization, Venice, Italy, pp. 1–10.
Youn, B.D., K.K. Choi, R.J. Yang, and L. Gu. (2004). “Reliability-Based Design Optimization for Crashworthiness
of Vehicle Side Impact.” Structural and Multidisciplinary Optimization 26, 272–283.
附錄B外文文獻(xiàn)
29