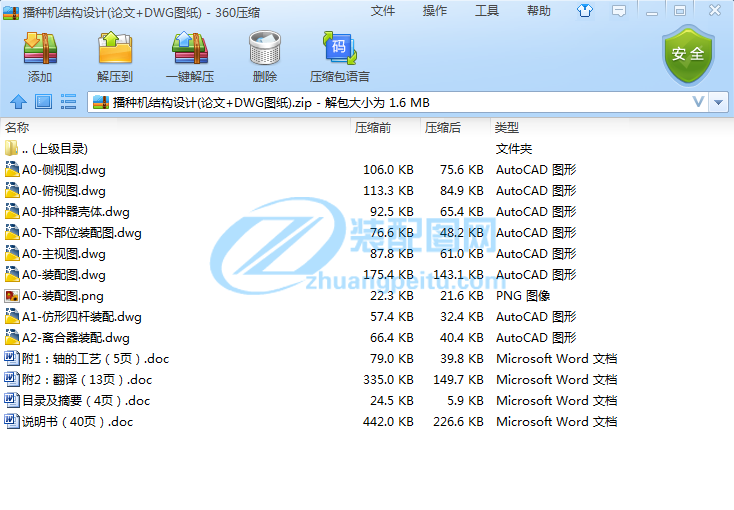
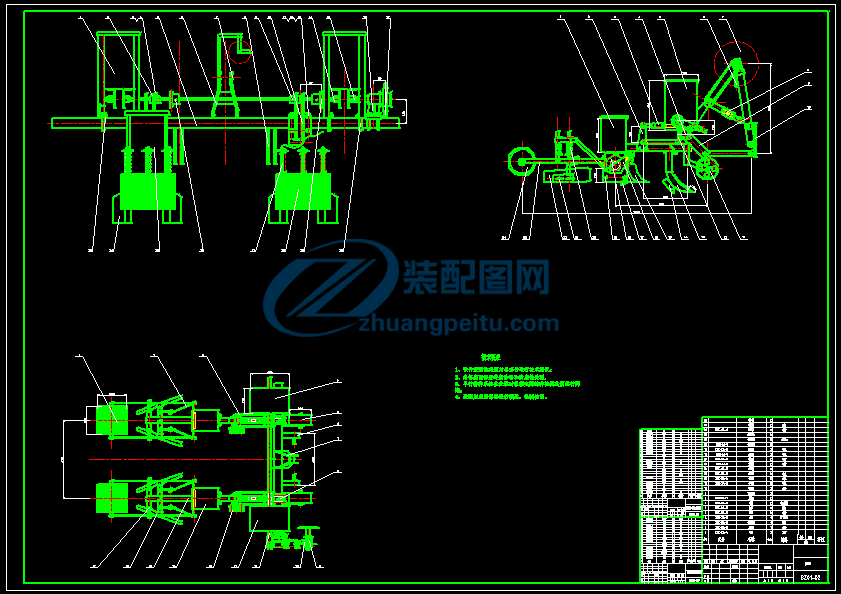

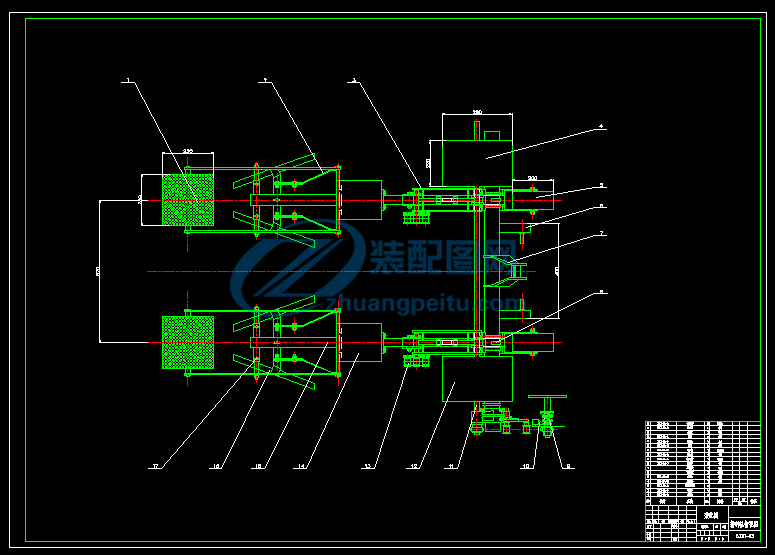

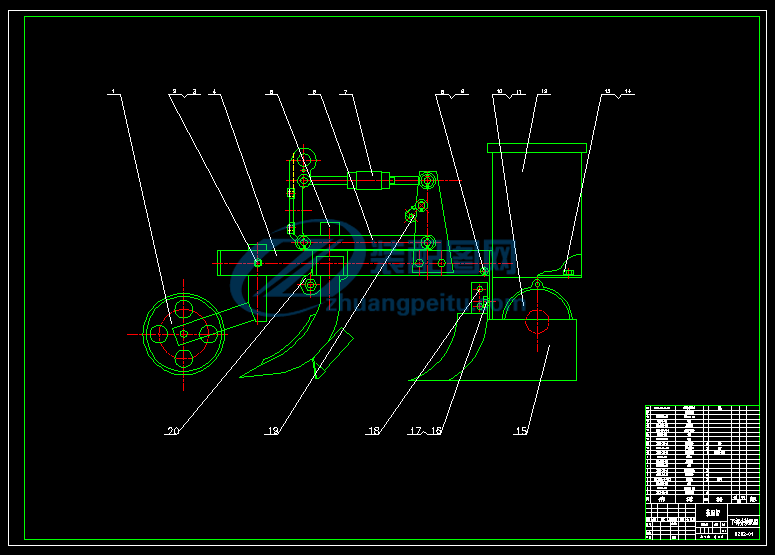
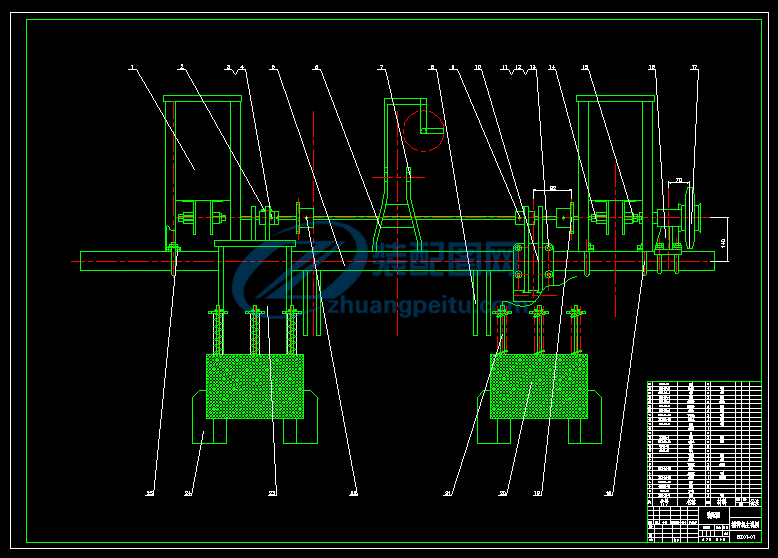
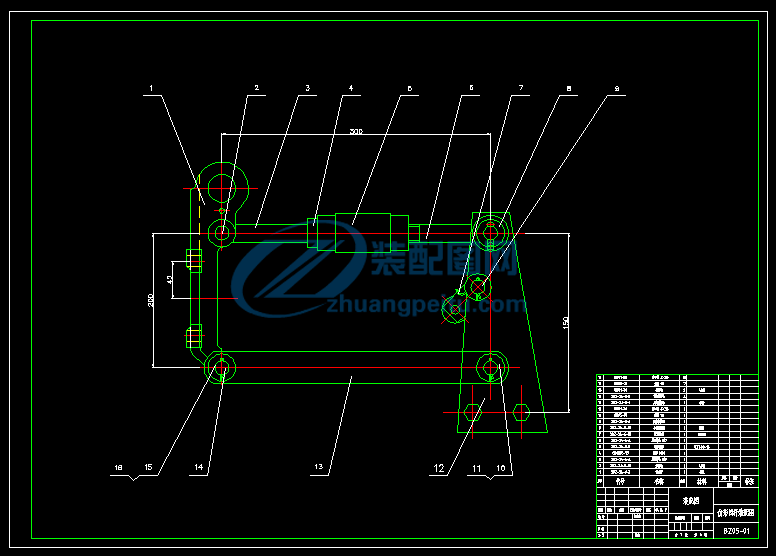
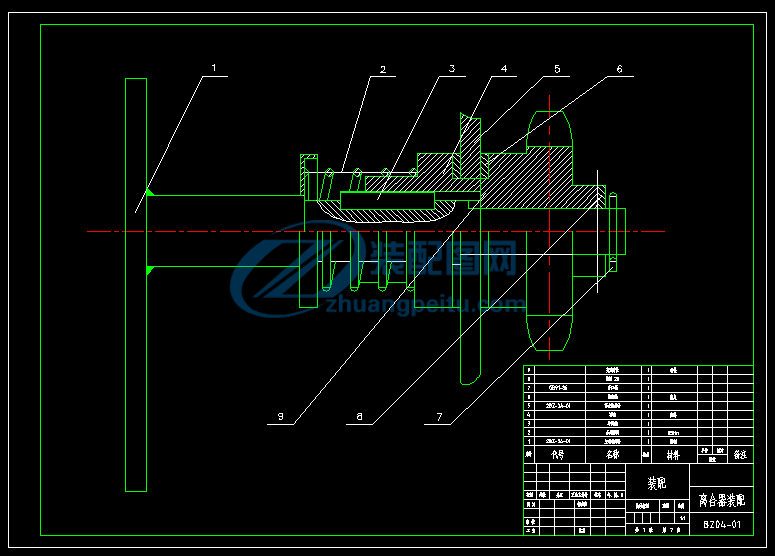
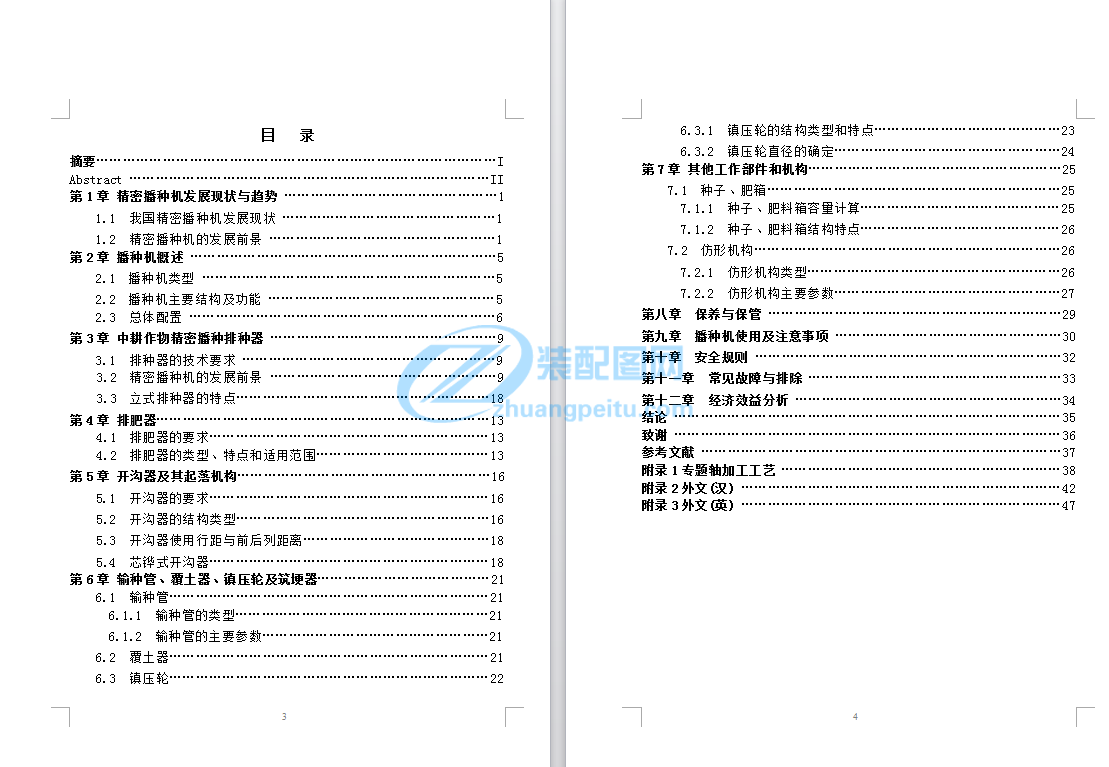
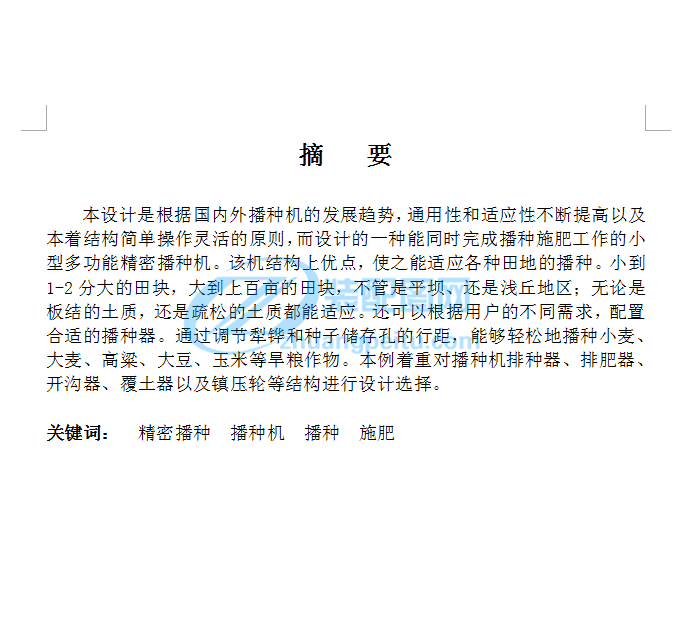
附錄 2快速原型技術及在模具制造中的應用摘要:論述了快速原型技術的工藝原理、加工特點、形成與發(fā)展概況以及在模具制造中的應用,指出該項技術可構成一種應用范圍十分廣泛、新穎的加工體系,市場前景廣闊。關鍵詞:快速原型技術 模具制造 產品開發(fā)快速原型技術是一種涉及多學科的新型綜合制造技術。80 年代后,隨著計算機輔助設計的應用,產品造型和設計能力得到極大提高,然而在產品設計完成后,批量生產前,必須制出樣品以表達設計構想,快速獲取產品設計的反饋信息,并對產品設計的可行性作出評估、論證。在市場競爭日趨激烈的今天,時間就是效益。為了提高產品市場競爭力,從產品開發(fā)到批量投產的整個過程都迫切要求降低成本和提高速度??焖僭图夹g的出現,為這一問題的解決提供了有效途徑,倍受國內外重視。 1 快速原型技術的基本原理 快速原型技術是用離散分層的原理制作產品原型的總稱,其原理為:產品三維 CAD 模型→分層離散→按離散后的平面幾何信息逐層加工堆積原材料 →生成實體模型。該技術集計算機技術、激光加工技術、新型材料技術于一體,依靠 CAD 軟件,在計算機中建立三維實體模型,并將其切分成一系列平面幾何信息,以此控制激光束的掃描方向和速度,采用粘結、熔結、聚合或化學反應等手段逐層有選擇地加工原材料,從而快速堆積制作出產品實體模型。 2 快速原型技術的加工特點 快速原型技術突破了“毛坯→切削加工→成品”的傳統(tǒng)的零件加工模式,開創(chuàng)了不用刀具制作零件的先河,是一種前所未有的薄層迭加的加工方法。與傳統(tǒng)的切削加工方法相比,快速原型加工具有以下優(yōu)點: (1)可迅速制造出自由曲面和更為復雜形態(tài)的零件,如零件中的凹槽、凸肩和空心部分等,大大降低了新產品的開發(fā)成本和開發(fā)周期。 (2)屬非接觸加工,不需要機床切削加工所必需的刀具和夾具,無刀具磨損和切削力影響。 (3)無振動、噪聲和切削廢料。 (4)可實現夜間完全自動化生產。 (5)加工效率高,能快速制作出產品實體模型及模具。下表為快速原型技術與傳統(tǒng)切削方法的比較。快速原型技術與傳統(tǒng)切削方法比較表3 快速原型技術的發(fā)展 快速原型技術概念即 RP(Rapid Prototyping Technology)概念的提出可追朔到 1979 年,日本東京大學生產技術研究所的中川威雄教授發(fā)明了疊層模型造型法,1980 年小玉秀男又提出了光造型法,該設想提出后,由丸谷洋二于 1984年繼續(xù)研究,并于 1987 年進行產品試制。1988 年,美國 3D Systems 公司率先推出快速原型實用裝置—激光立體造型即 SLA(Stereo Lightgraphy Apparatus),并以年銷售增長率為 30%~40%的增幅在世界市場出售。近年來,隨著掃描振鏡性能的提高,以及材料科學和計算機技術的發(fā)展,快速原型技術已日趨成熟,并于 1994 年正式進入推廣普及階段。按照所用材料的形態(tài)與種類不同,快速原型技術目前有以下四種類型。 3.1 利用激光固化樹脂材料的光造型法 光造型裝置一直以美國 3D Systems 公司的 SLA 型產品獨占鰲頭,并形成壟斷市場。其工作原理如圖 1 所示。由激光器發(fā)出的紫外光,經光學系統(tǒng)匯集成一支細光束,該光束在計算機控制下,有選擇的掃描液激光器掃描鏡升降裝置容器光敏樹脂體光敏樹脂表面,利用光敏樹脂遇紫外光凝固的機理,一層一層固化光敏樹脂,每固化一層后,工作臺下降一精確距離,并按新一層表面幾何信息使激光掃描器對液面進行掃描,使新一層樹脂固化并緊緊粘在前一層已固化的樹脂上,如此反復,直至制作生成一零件實體模型。激光立體造型制造精度目前可達±0.1mm,主要用作為產品提供樣品和實驗模型。此外,日本帝人制機開發(fā)的 SOLIFORM 可直接制作注射成型模具和真空注塑模具 圖 1 立體光造型技術原理圖3.2 紙張疊層造型法 紙張疊層造型法目前以 Helisys 公司開發(fā)的 LOM 裝置應用最廣。該裝置采用專用滾筒紙,由加熱輥筒使紙張加熱聯(lián)接,然后用激光將紙切斷,待加熱輥筒自動離開后,再由激光將紙張裁切成層面要求形狀,如圖 2 所示。 圖 2 紙張疊層造型原理圖LOM 可制作一些光造型法難以制作的大型零件和厚壁樣件,且制作成本低廉(約為光造型法的 1/2)、速度高(約為木模制作時間的 1/5 以下),并可簡便地分析設計構思和功能。 3.3 熔融造型法 熔融造型法以美國 Stratasys 公司開發(fā)的產品 FDM(Fused Deposition Modelling)應用最為廣泛。工作時,直接由計算機控制噴頭擠出熱塑材料并按照層面幾何信息逐層由下而上制作出實體模型。FDM 技術的最大特點是速度快(一般模型僅需幾小時即可成型)、無污染,在原型開發(fā)和精鑄蠟模等方面得到廣泛應用。 3.4 熱可塑造型法 熱可塑造型法以 DTM 公司開發(fā)的選擇性激光燒結即 SLS(Selective Laser Sintering)應用較多。該方法是用 CO2 激光熔融燒結樹脂粉末的方式制作樣件。工作時,由 CO2 激光器發(fā)出的光束在計算機控制下,根據幾何形體各層橫截面的幾何信息對材料粉末進行掃描,激光掃描處粉末熔化并凝固在一起。然后,鋪上一層新粉末,再用激光掃描燒結,如此反復,直至制成所需樣件。如圖 3所示。圖 3 選擇性激光燒結原理圖SLS 技術造型速度快(一般制品,僅需 1 天~2 天即可完成)、造型精度高(每層粉末最小厚度約 0.07mm,激光動態(tài)精度可達±0.09mm,并具有自動激光補償功能)、原型強度高(聚碳酸脂其彎曲強度可達 34.5MPa,尼龍可達 55MPa),因此,可用原型進行功能試驗和裝配模擬,以獲取最佳曲面和觀察配合狀況。 在快速原型技術的開發(fā)應用方面,美國和日本走在前列。近年來,我國快速原型技術的發(fā)展已十分迅速。華中理工大學在 1994 年開發(fā)研制成功兩種快速成型系統(tǒng)樣機 HRP 和 RPS,目前已進入商品市場,廣泛應用于汽車、玩具、航空航天、造船、軍工等行業(yè)。 4 快速原型技術在模具制造中的應用 4.1 快速制模鑄造將需鑄零件的 CAD 模型轉換為快速模殼制造,按模殼每層截面的幾何形狀生成陶瓷模殼然后按快速熔模鑄造方法即可快速制造金屬零件。此外,可將快速原型技術制作生成的樣件作為鑄造模具的原模,實現零件的快速鑄造,其過程為:零件 CAD 三維設計→計算流體動力學分析(CFD)→LOM 模型制造→熔模鑄造金屬零件。 4.2 快速模具制造 傳統(tǒng)的模具制造方法周期長、成本高,一套簡單的塑料注塑模具其價值也在 10 萬元以上。設計上的任何失誤反映到模具上都會造成不可挽回的損失??焖僭图夹g可精確制作模具的型心和型腔,也可直接用于注射過程制作塑料樣件,以便發(fā)現和糾正出現的錯誤。 美國愛達荷國家工程與環(huán)境試驗中心采用快速凝固工藝即 RSP 技術實現了注塑模具的快速經濟制造。該方法采用快速原型技術制作的樣件作為母體樣板,通過噴涂到母體樣板的金屬或合金熔滴的沉積制造模具。其工藝過程為:熔融的工具鋼或其它合金被壓入噴嘴,與高速流動的隋性氣體相遇而形成直徑約0.05mm 的霧狀熔滴,噴向并沉積到母體樣板上,復制出母樣的表面結構形狀,借助脫模劑使沉積形成的鋼制模具與母樣分離,即可制出所需模具。 母樣使用的材料取決于噴涂其上的合金材料。對于噴涂工具鋼來說,可選用陶瓷材料,類似材料還有鋁氧粉和氧化鋯可供選擇。該方法制作精度高(噴涂工具鋼時最小表面涂層可達0.038mm,制造精度可達±0.025mm~±0.05mm)、時間短(普通模具一周之內即可成型)、造價低(一般為傳統(tǒng)模具制造費用的1/2~1/10)。 4.3 快速鑄造模具 以聚碳酸脂為材料,用SLS快速制出母型,并在母體表面制出陶瓷殼型,焙燒后用鋁或工具鋼在殼內進行鑄造,即得到模具的型心和型腔。該方法制作周期不超過4周,制造的模具可生產250000個塑料制品。 5 結論 綜上所述,RP是一種正在進一步發(fā)展和完善且已獲得了廣泛應用的高技術??梢灶A見,隨著CAD的廣泛應用、市場競爭日趨激烈、快速造型技術本身和快速模具制造成套技術的完善,快速成形技術將發(fā)展為一種能被企業(yè)普遍采用的技術手段,并將給企業(yè)帶來巨大的經濟效益,這應引起各方面的高度重視。附錄 3The Rapid Prototyping Manufacturing and its application in molding manufacturingAbstract: By discussing the rapid prototyping technology the craft principle, characteristic of the processes, formation and the general situation of the develop of fast prototype and its application in molding, point out the technique can form a kind of a process system of extensive application and novel, and its foreground is vast.Key Words: rapid prototyping technology; molding manufacturing; development of productRapid prototyping technology is a new type of multidisciplinary integrated manufacturing technology. After the 1980s, following the application of computer-aided design, product shape and design capabilities have greatly improved, however, product design has completed, production, a system must be designed to convey the concept of samples, rapid feedback to product design, product design and assess the feasibility, and feasibility studies. The increasingly fierce competition in the market today, the time is effective. To enhance the competitiveness of products, from product development to volume production of the whole process are urgently required to reduce costs and increase speed. Rapid prototype technology appearance provides an effective solution to this problem which much attention at home and abroad.1. The basic principle of Rapid Prototyping TechnologyThe RP is the generic name of the principle creation product prototype that uses the long-lost layering, its principle is: Produce CAD model? Stratified separated ?according to the plan geometry information which is dispersed to pile up the original material? generating entity models.This technology integrates of computer technology, laser processing technology, new material technology, relying on CAD software in the creation of 3D computer models entities, and is divided into a series of plane geometry information to control the scanning laser beam direction and speed, using sinter, pooling or chemical reaction means exhaustive selective processing of raw materials, thus rapid accumulation manufacture products entities models.2. The characteristics of Rapid Prototyping TechnologyRapid Prototyping Technology breaks the traditional way to produce spare parts of “roughcast ?slice to pare to process?finished”, Needless cutlery created the first production of spare parts, is an unprecedented lamina reducing processing methods. Comparing to tradition, the fast prototype processes the following advantage:(1)Produce the spare parts of the curved face and more complicated appearance quickly, such as shoulder within spare parts and hollow and parts of etc.s, consumedly lowered the development cost of the new product and development period.(2)Is a non-contact processing, machine tool cutting processing is necessary cutlery and jig without cutlery wear and cutting force.(3)Without vibration, noise and slice to pare the waste.(4)Can carry out the nighttime over full-automatic production.(5)Process with high efficiency, produces the article entity model and molding tools quickly.The form follows the comparison of the method for the Rapid Prototyping Technology and tradition.Processing technologyComparison the itemThe tool machine slices to pare to processRP(Light shape method)processThe method of processDo away with the surplus material processFold the layer processThe object of process SolidLiquid, portrait, powderToolThe tool of slice to pareLight beamMinimum processing unitsDot’s diameter is about 1μmsTriangles of 200μms longProduction of spare partsThe least processes come together the body of the unitThe least processes come together the body of the unitThe RP and traditions slice to pare the method comparison sheet3. The develop of RPRapid prototyping technology concept that the concept RP (Rapid Prototyping Technology) could be back to 1979. the profess of Zhong Chuan Weixiong in produce and technique institute of Japanese University of Tokyo invent the method of fold the layer model, the Xiao Yu Xiunan put forward the light shape method again in 1980, after the conceive put forward, it was continued to study in 1984 by Wan Gu Yanger, and carried on to produce manufacture on a trial basis in 1987.1988, the United States rapidly prototype 3D Systems Corporation was the first to introduce practical devices-laser three-dimensional shapes that SLA (Stereo Lightgraphy Apparatus), and annual sales growth rate 30%~40% increase in the world market. In recent years, with increasing performance scanning-a mirror, and the development of materials science and computer technology, rapid prototyping technology matures, and in 1994 to promote universal access to the formal stage. In accordance with the patterns and materials used in the different types of rapid prototyping technology currently has the following four types.3.1 Solidification resin materials using laser light shapes lawThe light shape equipment is excellent with a product of the 3D Systems company of the United States, and the formation of a monopoly. Figure 1 shows the operating principles. Issued by the laser light, the optical system to compile into a small beam, the beam in the computer controlled, selective scanning resin surface, using an ultraviolet resin Frozen mechanisms, a layer of solidification resin, each layer of solidification, precision workstations in a distance with the new layer of surface geometric information to the laser scanner for scanning reading, solidification of the new layer of resin and firmly stick to the previous layer has solidification resin, so repeatedly until the production of spare parts entities generated a model. The laser stereoscopic shape manufacturing accuracy can reach the ±0.1 mms, mainly used to provide the sample and the experiment models for the product. In addition, the SOLIFORM of the Japanese system machine developed can manufacture to inject to model the molding tool and vacuum molding tools directly.Figure 1 Stereoscopic light shape technique principle diagram3.2The paper folds the layer shape methodThe paper folds the LOM that the layer shape method develops with the Helisys company currently applicant most widely. The devices used for roller paper from the paper heating roller cylinders connectivity, and then using the laser to cut paper, the question heating roller cylinders automatically leave, the paper will be ready by laser level requirements into shape, as shown in figure 2. Figure 2 Principle diagram of the paper folds the layer shapeThe LOM can manufacture some large spare parts and the thick wall kind pieces of the hard creation with lights shape method and create cost is cheap (about for the light shape method of 1/2), the speed is high (about manufacture time for the wood mold of below 1/5), and can simply analytic the design conceive outline and function.3.3 meltdown shape methods The meltdown shape method is most extensive used with the product FDM which is developed in American Stratasys,(the Fused Deposition Modeling), when it is working, the plastics material with hot extrusion sprayed directly by sprinkler head controlled by computer combine to layer to create an entity model from bottom to top according to several information of level. The biggest characteristics in FDM technical is a quick(general the model need several hours and can immediately model) and free from pollution, to get the extensive application in prototype, develop and cast wax mole and so on.3.4 hot and fictile shape methodsThe hot and fictile shape method burns the knot with the selectivity laser of the DTM company development namely the SLS (the Selective Laser Sintering) application is the most. That method is a way manufacture kind piece that burns with the CO2 laser machine controls by the calculator, carry on scanning on the material powder according to several information for faces of several pieces with horizontal each layer of the body, the powder is scanning by laser and solidify together. Then, spread up a new powder of layer, then scan to burn the knot with the laser, thus again and again, keep to go to make the kind piece which needed. As figure 3 shows.Figure 3 The principle chart of selectivity laser sinteringThe SLS technique shape speed is fast(general ware, need one or two days to complete), the shape accuracy is high(the minimum thickness of each layer powder is about 0.07 mms, the laser dynamic state accuracy can reach the ±0.09 mms, and have the automatic laser repair function), the prototype strength is high(gather its bent strength of the carbonic acid fat and can amount to the 34.5MPa,the nylon can reach 55MPa), therefore, can carry on function’s experiment and assemble the emulation with the prototype, to obtain the best curved face to match with the observation the condition.Develop and applied aspect technically in RP, the United States and Japans are the best. In Huazhong University develops two kinds of model system machine HRP and RPSs which is research to manufacture in 1994 successful quickly, have already entered the commodity market currently, be applied in the professions extensively, such as automobile, toy, aviation aerospace, shipbuilding and the soldier work etc.4. The application of the RP in molding manufacture4.1 Making the mold foundry fastPut the spare part CAD model converse to fast method, produce metal spare parts quickly according to each layer shape of face to for ceramic mold and then accord to fast method. In addition, can carry out the original mold that the fast prototype technique manufactures a conduct and actions founder molding tool, spare parts of fast cast, its process is: Design the spare parts CAD 3D ?the calculation hydrodynamics analysis(CFD)?the LOM model manufacturing?cast the metals spare parts.4.2 fast molding tool manufacturingThe traditional molding tool manufacturing method period is long, the cost is high, a set of simple plastics molding tool is worth above 100,000 dollars. Any error of design reflects the molding tool make the loss that can’t be retrieved. Fast prototype technique can a heart and bodies of the accurate manufacture molding tool, also can used for injecting process to produce manufacture plastics piece directly, for the purpose of detection and the mistake that rectify to appear.The center of national engineering in American Idaho and environments experiment adopt the fast concretion craft namely the technique of RSP carried out the fast and economy of the plastics molding manufacture. That method adopt fast prototype technique produce sample to be sample product sink to accumulate to make the mold. The craft process is steel or tool used for other alloys of the meltdown were pressed to go in to the mouth of spray meet high speed Sui air to form fog of liquid which diameter about 0.05mms, spay to maternal sample and sink to accumulate on it, make duplicate the surface structure shape of maternal sample, with the help of chemical to separate the steel mold which was sink to accumulated and maternal sample, then produce the mold needed.The material of maternal sample decided by the alloy material which was spray on it. For the spray stool steel, can chose ceramic materials, still have similar material as Aluminum Oxygen powder and provided as choice. That method manufacture accuracy is high (when spray to draw the tool steel, the minimum layer and can amount to the 0.038mms, manufacture accuracy can reach the ±0.025mms~±0.05mms),time is short (common molding tool can be modeled in a week ) the price is low.(General is 1/2~1/10 of the traditional molding tool manufacture).4.3 Fast cast moldingThe carbonic as the material, use the SLS to make a female type quickly, and in the maternal surface produce the shape of ceramics hull, use the aluminum or the tool steels to carry on the foundry in the hull after baking to burn, then get the inner part and the shape of the molding tool. That method manufacture period not over 4 weeks, the molding tool of the manufacturing can produce 250000 plastics wares.5 ConclusionBased on the above, the RP is a further development and refinement technology which has been extensive and high-tech applications. It can be predicted that along with the wider using of CAD, the increasingly fierce market competition, rapid shaped mould manufacturing technology itself and the rapid improvement of technology packages, will be developed rapidly emerging technology enterprises to be a common technical means, and bring huge economic benefits to the enterprise, which should have aroused great attention.