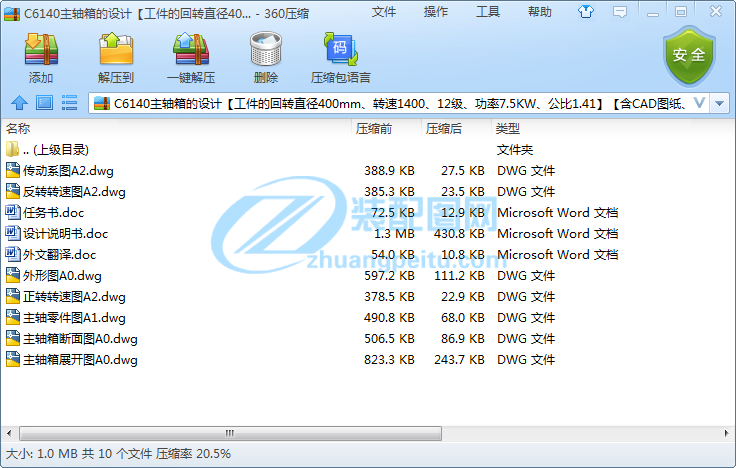

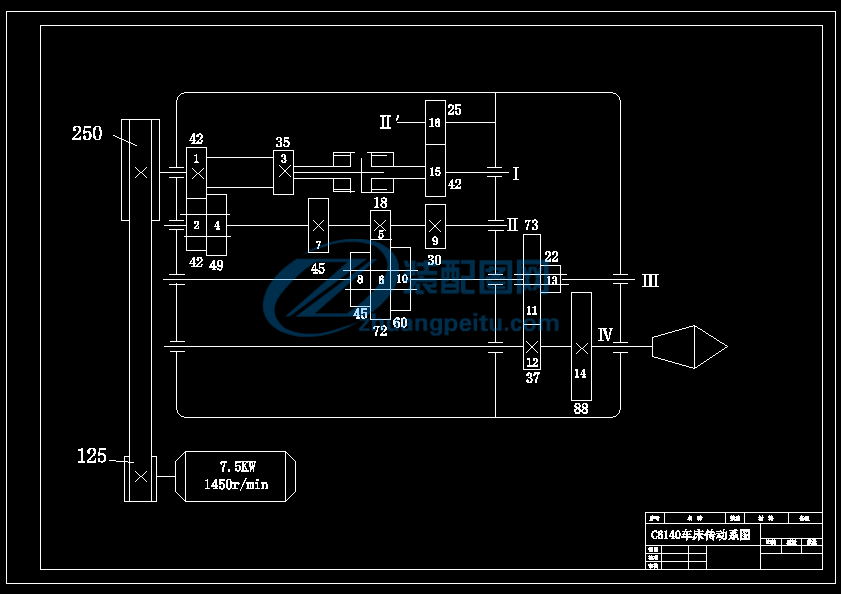
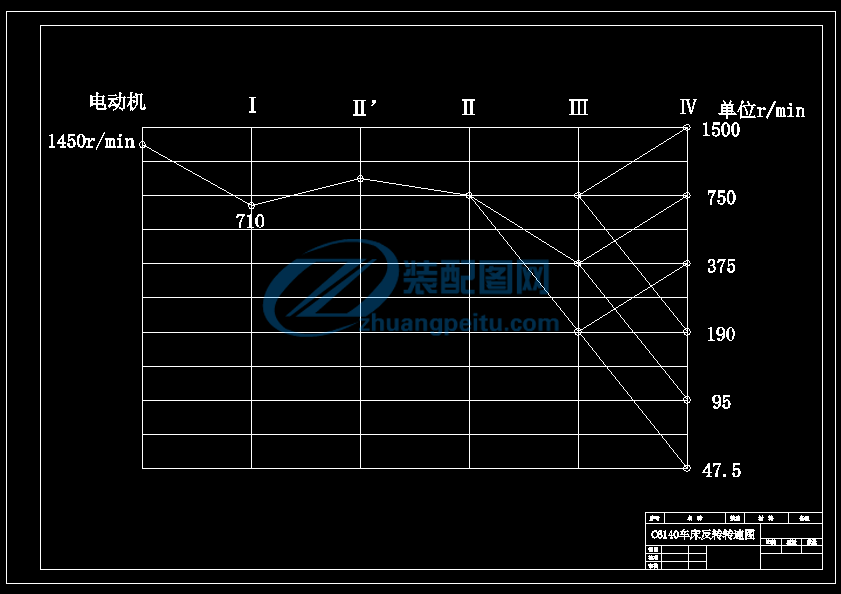
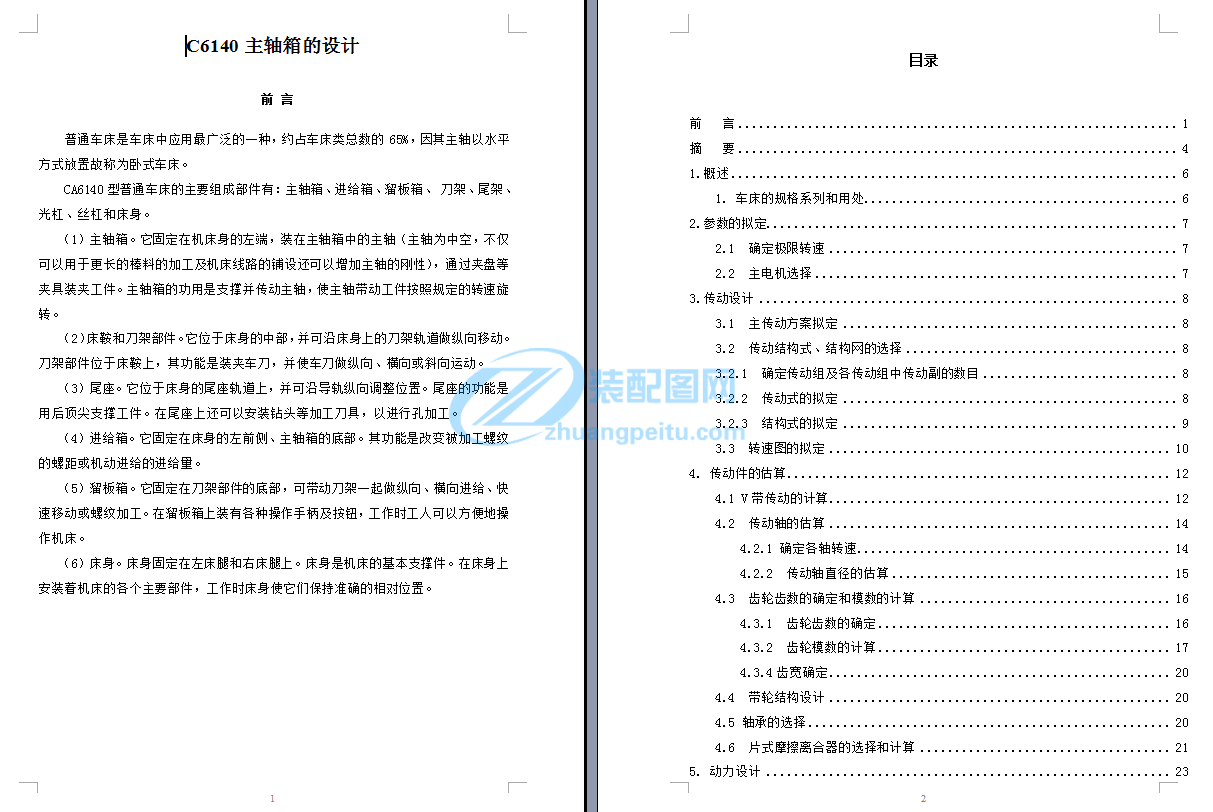
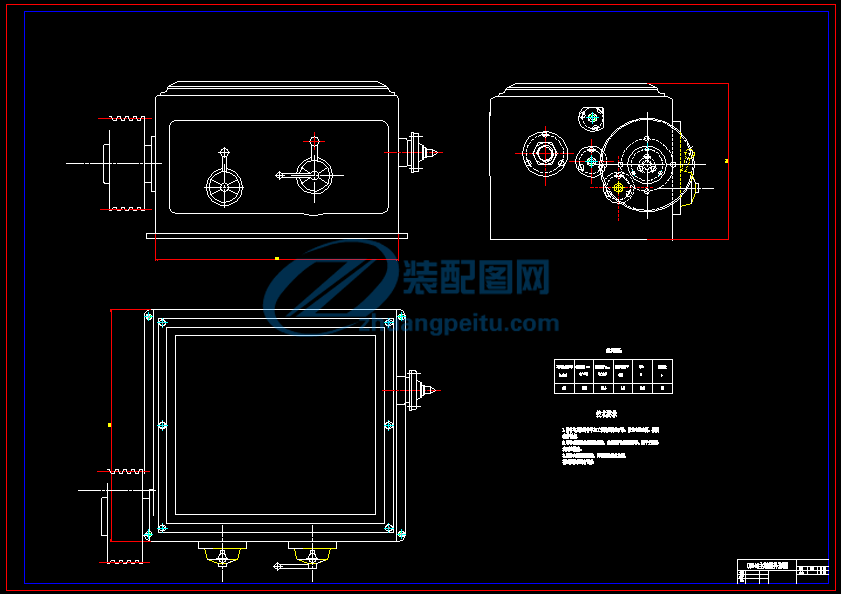
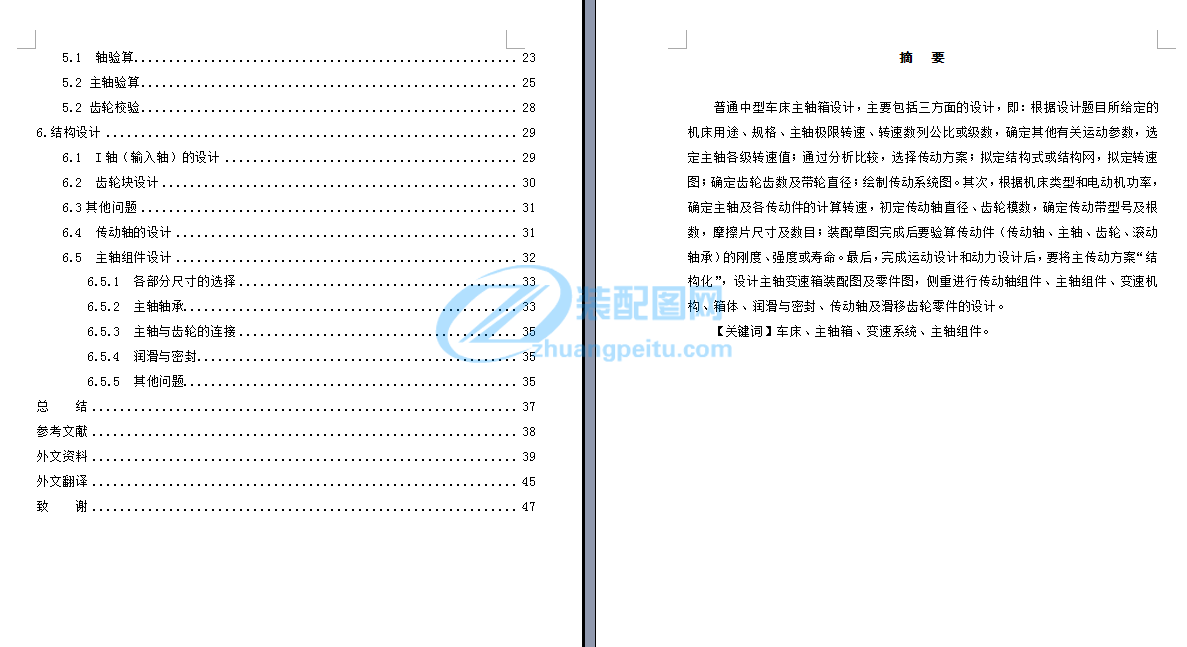
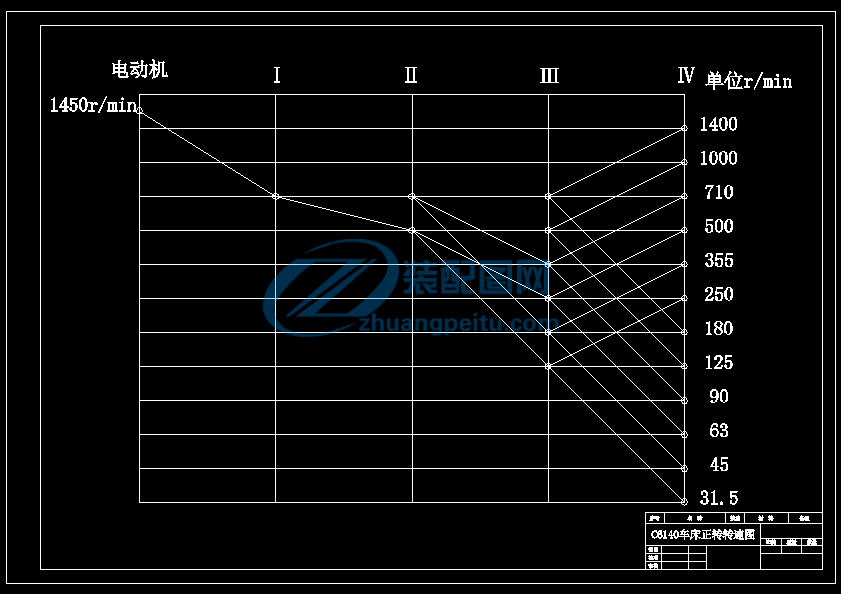

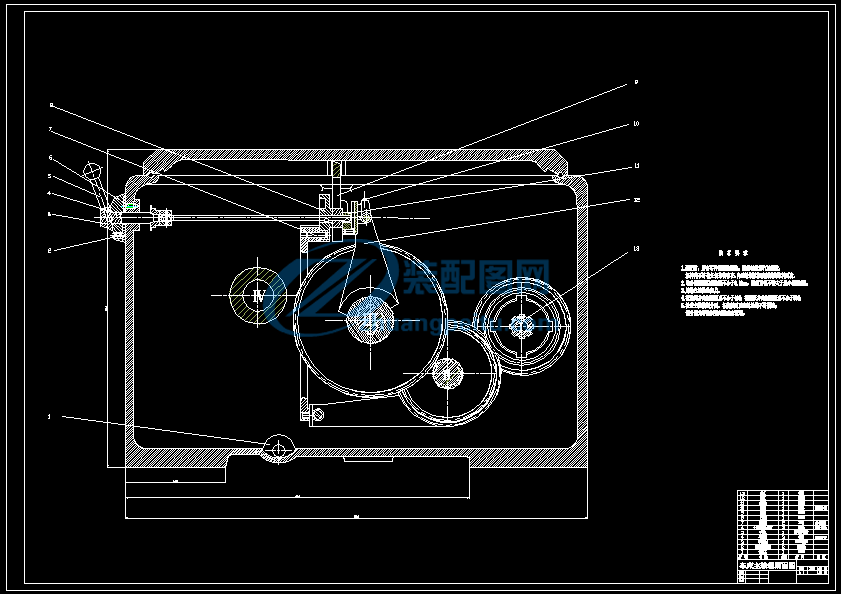
1C6140 主軸箱的設計前 言 普通車床是車床中應用最廣泛的一種,約占車床類總數(shù)的 65%,因其主軸以水平方式放置故稱為臥式車床。 CA6140型普通車床的主要組成部件有:主軸箱、進給箱、溜板箱、 刀架、尾架、光杠、絲杠和床身。(1)主軸箱。它固定在機床身的左端,裝在主軸箱中的主軸(主軸為中空,不僅可以用于更長的棒料的加工及機床線路的鋪設還可以增加主軸的剛性) ,通過夾盤等夾具裝夾工件。主軸箱的功用是支撐并傳動主軸,使主軸帶動工件按照規(guī)定的轉速旋轉。(2)床鞍和刀架部件。它位于床身的中部,并可沿床身上的刀架軌道做縱向移動。刀架部件位于床鞍上,其功能是裝夾車刀,并使車刀做縱向、橫向或斜向運動。(3)尾座。它位于床身的尾座軌道上,并可沿導軌縱向調整位置。尾座的功能是用后頂尖支撐工件。在尾座上還可以安裝鉆頭等加工刀具,以進行孔加工。(4)進給箱。它固定在床身的左前側、主軸箱的底部。其功能是改變被加工螺紋的螺距或機動進給的進給量。(5)溜板箱。它固定在刀架部件的底部,可帶動刀架一起做縱向、橫向進給、快速移動或螺紋加工。在溜板箱上裝有各種操作手柄及按鈕,工作時工人可以方便地操作機床。(6)床身。床身固定在左床腿和右床腿上。床身是機床的基本支撐件。在床身上安裝著機床的各個主要部件,工作時床身使它們保持準確的相對位置。2目錄前 言 .1摘 要 .41.概述 61. 車床的規(guī)格系列和用處 .62.參數(shù)的擬定 72.1 確定極限轉速 .72.2 主電機選擇 .73.傳動設計 83.1 主傳動方案擬定 .83.2 傳動結構式、結構網的選擇 .83.2.1 確定傳動組及各傳動組中傳動副的數(shù)目 .83.2.2 傳動式的擬定 .83.2.3 結構式的擬定 .93.3 轉速圖的擬定 104. 傳動件的估算 124.1 V帶傳動的計算 124.2 傳動軸的估算 144.2.1 確定各軸轉速 .144.2.2 傳動軸直徑的估算 154.3 齒輪齒數(shù)的確定和模數(shù)的計算 164.3.1 齒輪齒數(shù)的確定 164.3.2 齒輪模數(shù)的計算 174.3.4齒寬確定 204.4 帶輪結構設計 204.5 軸承的選擇 .204.6 片式摩擦離合器的選擇和計算 215. 動力設計 2335.1 軸驗算 235.2 主軸驗算 .255.2 齒輪校驗 .286.結構設計 .296.1 I軸(輸入軸)的設計 .296.2 齒輪塊設計 306.3其他問題 316.4 傳動軸的設計 316.5 主軸組件設計 326.5.1 各部分尺寸的選擇 336.5.2 主軸軸承 336.5.3 主軸與齒輪的連接 356.5.4 潤滑與密封 356.5.5 其他問題 35總 結 .37參考文獻 .38外文資料 .39外文翻譯 .45致 謝 .474摘 要普通中型車床主軸箱設計,主要包括三方面的設計,即:根據設計題目所給定的機床用途、規(guī)格、主軸極限轉速、轉速數(shù)列公比或級數(shù),確定其他有關運動參數(shù),選定主軸各級轉速值;通過分析比較,選擇傳動方案;擬定結構式或結構網,擬定轉速圖;確定齒輪齒數(shù)及帶輪直徑;繪制傳動系統(tǒng)圖。其次,根據機床類型和電動機功率,確定主軸及各傳動件的計算轉速,初定傳動軸直徑、齒輪模數(shù),確定傳動帶型號及根數(shù),摩擦片尺寸及數(shù)目;裝配草圖完成后要驗算傳動件(傳動軸、主軸、齒輪、滾動軸承)的剛度、強度或壽命。最后,完成運動設計和動力設計后,要將主傳動方案“結構化” ,設計主軸變速箱裝配圖及零件圖,側重進行傳動軸組件、主軸組件、變速機構、箱體、潤滑與密封、傳動軸及滑移齒輪零件的設計?!娟P鍵詞】車床、主軸箱、變速系統(tǒng)、主軸組件。5AbstractOrdinary medium-sized lathe headstock design, including the three aspects of the design, namely: According to a design by the use of a given machine, specifications, spindle speed limit, speed series of common ratio or series, to determine other relevant motion parameters, the selected axis of the grade speed value; through analysis and comparison, select the drive scheme; proposed structure or structure network, development of speed diagram; determine gear and pulley diameter; drawing transmission system map. Secondly, according to machine type and motor power, and the transmission parts to determine the calculation of the spindle speed, an initial diameter of shaft, gear module to determine the belt type and root number, size and number of friction plate; Assembly Draft Checking transmission parts after completion of (shaft, spindle, gear, bearing) stiffness, strength or life. Finally, the complete design and dynamic design exercise, the main transmission scheme to the “structural“, the design of spindle gearbox assembly drawing and part drawings, focusing on the drive shaft assembly, spindle assembly, transmission organizations, box, lubrication and sealing , drive shaft and the sliding gear with the design. Key words :lathe, the spindle box, transmission, shaft components. 61.概述1. 車床的規(guī)格系列和用處普通機床的規(guī)格和類型有系列型譜作為設計時應該遵照的基礎。因此,對這些基本知識和資料作些簡要介紹。本次設計的是普通型車床 CA6140主軸變速箱。主要用于加工回轉體。車床的主參數(shù)(規(guī)格尺寸)和基本參數(shù)(GB1582-79,JB/Z143-79)工件最大回轉直徑D (mm)max正轉最高轉速( maxN)inr電機功率N(kw)公比 ?轉速級數(shù) Z反轉400 1450 7.5 1.41 12級數(shù) Z反=Z 正/2;n 反max≈1.07n 正max72.參數(shù)的擬定2.1 確定極限轉速, nR?miax ???zn?又∵ =1.41∴ 得 =43.79. 取 =45;?nR,去標準轉速列 .mi/1.3i/4510/axin rrn min/5.31inr?所以正轉轉速數(shù)列是n1 =31.5r/min n2 =45r/min n3 =63r/min n4 =90r/min n5 =125r/min n6 =180r/min n7 =250r/min n8 =355r/minn9 =500r/min n10 =710r/min n11 =1000r/min n12 =1400r/min。反轉轉速最大為 ,則反轉轉速數(shù)列是mi/15040.7.1maxmax r???正反n1 =47.5r/min n2 =95r/min n3 =190r/min n4 =375r/min n5 =750r/min n6 =1500r/min。2.2 主電機選擇合理的確定電機功率 N,使機床既能充分發(fā)揮其使用性能,滿足生產需要,又不致使電機經常輕載而降低功率因素。已知電動機的功率是 7.5KW,根據《車床設計手冊》附錄表 2選 Y132M-4,額定功率 7.5 ,滿載轉速 1440 ,最大轉距/額定轉矩 2.2倍。kwminr83.傳動設計3.1 主傳動方案擬定擬定傳動方案,包括傳動型式的選擇以及開停、幻想、制動、操縱等整個傳動系統(tǒng)的確定。傳動型式則指傳動和變速的元件、機構以及組成、安排不同特點的傳動型式、變速類型。傳動方案和型式與結構的復雜程度密切相關,和工作性能也有關系。因此,確定傳動方案和型式,要從結構、工藝、性能及經濟等多方面統(tǒng)一考慮。傳動方案有多種,傳動型式更是眾多,比如:傳動型式上有集中傳動,分離傳動;擴大變速范圍可用增加傳動組數(shù),也可用背輪結構、分支傳動等型式;變速箱上既可用多速電機,也可用交換齒輪、滑移齒輪、公用齒輪等。顯然,可能的方案有很多,優(yōu)化的方案也因條件而異。此次設計中,我們采用集中傳動型式的主軸變速箱。3.2 傳動結構式、結構網的選擇結構式、結構網對于分析和選擇簡單的串聯(lián)式的傳動不失為有用的方法,但對于分析復雜的傳動并想由此導出實際的方案,就并非十分有效。3.2.1 確定傳動組及各傳動組中傳動副的數(shù)目級數(shù)為 Z的傳動系統(tǒng)由若干個順序的傳動組組成,各傳動組分別有 、?Z、……個傳動副。即 ? ??321Z?傳動副中由于結構的限制以 2或 3為合適, 可以有三種方案: 12=3×2×2;12=2×3×2;12=2×2×3;3.2.2 傳動式的擬定12級轉速傳動系統(tǒng)的傳動組,選擇傳動組安排方式時,考慮到機床主軸變速箱9的具體結構、裝置和性能。在Ⅰ軸如果安置換向摩擦離合器時,為減少軸向尺寸,第一傳動組的傳動副數(shù)不能多,以 2為宜。主軸對加工精度、表面粗糙度的影響很大,因此主軸上齒輪少些為好。最后一個傳動組的傳動副常選用 2。綜上所述,傳動式為 12=2×3×2。3.2.3 結構式的擬定對于 12=2×3×2傳動式,有 6種結構式。分別為:, , ,??????????????????, , ,? ?? ?根據傳動順序與擴大順序相一致的原則,選 的方案。1263最后擴大組變速范圍 符合要求,其他變速組變速范圍也,0~841.)2(6??R肯定符合要求。103.3 轉速圖的擬定圖 3-1 正轉轉速圖圖 3-2 反轉轉速圖11圖 3-3主傳動系圖124. 傳動件的估算4.1 V 帶傳動的計算V帶傳動中,軸間距 A可以加大。由于是摩擦傳遞,帶與輪槽間會有打滑,宜可緩和沖擊及隔離振動,使傳動平穩(wěn)。帶輪結構簡單,但尺寸大,機床中常用作電機輸出軸的定比傳動。(1)選擇 V帶的型號根據機械設計公式 8.18 KWPKac 25.871.???式中 P---電動機額定功率, --工作情況系數(shù)(此處取為 1.1)。 查《機械設計》圖 8.6,因此選擇 A型帶,尺寸參數(shù)為頂寬 ,節(jié)寬m13b,高度 ,槽角 。m1bp?8h???40?(2)確定帶輪的計算直徑 ,?D?帶輪的直徑越小帶的彎曲應力就越大。為提高帶的壽命,小帶輪的直徑 不?D宜過小,即 。查 《機械設計》取主動輪基準直徑 =125 。min?? ?Dm由公式 ?????12式中: -小帶輪轉速, -大帶輪轉速, -帶的滑動系數(shù),一般取 0.02。?n?n所以 ,??mD.50.157042?由《機械設計》V 帶帶輪基準直徑的標準系列,取圓整為 250mm。實際傳動比 ???042.1502.12 ?????Di?傳動比誤差相對值 %9.4.??i一般允許誤差 5%,所選大帶輪直徑可選。(3)確定三角帶速度13按公式 smnDv /48.9106524.3106?????在 5~ 25m/s之間,滿足帶速要求。v初定中心距(4)初定中心距帶輪的中心距,通常根據機床的總體布局初步選定,一般可在下列范圍內選?。焊鶕C械設計公式 即 ,取hDD???)(7.0A)(22121 263A750?=700mm.0A(5)三角帶的計算基準長度 ?L??02121042ADDAL???????3.94755720 ???由 《機械設計》表 8-2,圓整到標準的計算長度 m20L(6)驗算三角帶的撓曲次數(shù),符合要求。 10.3140smvuL??次(7)確定實際中心距 A2mm8-)D(4D-A???? 2 DD=D 12m ?2- DD= 12?703195201952022???)((8)驗算小帶輪包角 ?,主動輪上包角合適。oo12o1 3.6AD-80??????(9)確定三角帶根數(shù) Z根據《機械設計》式 8-22得0calpzk????傳動比.271452vi14查表 8.11,8.9 得 = 0.17KW, = 1.93KW0p?0p查表 8.8, =0.973;查表 8.3, =1.03k?lk9.30.17).0931(258???=Z所以取 Z=4根(10)驗算 V帶的撓曲次數(shù),符合要求。sLmvu次406.170??(11)計算帶的張緊力和軸上載荷查《機械設計》表 8.5,q=0.1kg/m單根帶的張緊力 NqvkvzPFca 1784.90198.524.50. 22?????????????帶輪軸的壓軸力 zF.3.6sin7sin210??4.2 傳動軸的估算傳動軸除應滿足強度要求外,還應滿足剛度的要求,強度要求保證軸在反復載荷和扭載荷作用下不發(fā)生疲勞破壞。機床主傳動系統(tǒng)精度要求較高,不允許有較大變形。因此疲勞強度一般不失是主要矛盾,除了載荷很大的情況外,可以不必驗算軸的強度。剛度要求保證軸在載荷下不至發(fā)生過大的變形。因此,必須保證傳動軸有足夠的剛度。4.2.1 確定各軸轉速 (1) 確定主軸計算轉速:主軸的計算轉速為 90r/min?IV(2) 各傳動軸的計算轉速: 軸Ⅲ可從主軸 90r/min找上去,軸Ⅲ的計算轉速125r/min;軸Ⅱ的計算轉速為 500r/min;軸Ⅰ的計算轉速為 710r/min。154.2.2 傳動軸直徑的估算根據傳動軸傳動的功率大小,用扭轉剛度公式進行初步的計算。4jnPKAd??式中 d——受扭部分的最小直徑(mm) ,計算值應圓整為標準直徑系列;K——鍵槽系數(shù),按表選取;A——根據許用扭轉角確定的系數(shù),按表 2.1選取;d——傳動軸受扭部分的直徑(mm) ;P——電動機額定功率 (kW) ;η——從電動機到所計算的軸的機械效率,見表 2——被估算的傳動軸的計算轉速( ) 。jn minr表 2.1 估算軸徑時 A和 K值[ ]???m?0.25 0.5 1 1.5 2A 130 110 83 77無鍵 單鍵 雙鍵 花鍵K1 1.04~1.05 1.07~1.1 1.05~1.09表 2.2各傳動機械效率的概略值類別 傳動件 平均機械效率齒輪傳動 直齒圓柱齒輪,磨齒 0.99帶傳動 V帶 0.96滾動軸承 滾子軸承 0.99電動機的額定功率 。kWP5.7?各軸計算轉速: min/90in,/125min,/0in,/10 ⅠⅠⅠⅠ rrrrn ??(1)Ⅰ軸軸徑的估算由于Ⅰ軸為花鍵軸,所以取 ,7?A9.K509.60軸 承帶1 ???且 min7rn16mnPkAd 6.271095.09.1441 ?????根據機械零件手冊取 d31(2)Ⅱ軸軸徑的估算由于Ⅱ軸為花鍵軸,所以取 ,7?A09.1K39.05齒軸 承12 ???且 min3rnmPkAd 9.2850.7.4422 ??根據機械零件手冊取 d32(3)Ⅲ軸軸徑的估算由于Ⅲ軸為花鍵軸,所以取 ,7?A09.1K9.03齒軸 承23 ???且 min18rnmPkAd 6.40125.7.4433 ??根據機械零件手冊取取 d3(4)主軸軸徑的估算由于主軸為空心軸,根據機械制造裝備設計表 3-1確定主軸前軸頸直徑,后軸頸直徑 ,取mD10?12)85.0~7(D?m802?主軸內孔直徑 ,取d 54~65210 ???????? md482?4.3 齒輪齒數(shù)的確定和模數(shù)的計算4.3.1 齒輪齒數(shù)的確定當各變速組的傳動比確定以后,可確定齒輪齒數(shù)。對于定比傳動的齒輪齒數(shù)可依據機械設計手冊推薦的方法確定。對于變速組內齒輪的齒數(shù),如傳動比是標準公17比的整數(shù)次方時,變速組內每對齒輪的齒數(shù)和 及小齒輪的齒數(shù)可以從表 3-9(機zS械制造裝備設計)中選取。一般在主傳動中,最小齒數(shù)應大于 18~20。采用三聯(lián)滑移齒輪時,應檢查滑移齒輪之間的齒數(shù)關系:三聯(lián)滑移齒輪的最大齒輪之間的齒數(shù)差應大于或等于 4,以保證滑移是齒輪外圓不相碰。第一組齒輪:傳動比: , 10u??21.4u?查《機械制造裝備設計》表 3-9,齒數(shù)和 取 84zS=42, =42, =35, =49;?Z23Z4第二組齒輪:傳動比: , ,10u??21?241u??齒數(shù)和 取 90:zS=45, =45, =30, =60, =18, =72;5Z67Z89Z10第三組齒輪:傳動比: ,21u??241?齒數(shù)和 取 110:zS=73, =37, =22, =88,1Z1213Z14反轉齒輪:傳動比: , 68.12071??nu 19.5022??nu,5/1916?Z4/2Z4.3.2 齒輪模數(shù)的計算(1)初步計算齒輪模數(shù)時,按簡化的接觸疲勞強度公式進行。一般同一變速組中的齒輪取同一模數(shù),選擇負荷最重的小齒輪進行計算。從等強度的觀點出發(fā),可減小其它齒輪的寬度,使齒輪基本上處于在相近的接觸應力或彎曲應力狀態(tài)下工作。這樣一來,還可以縮短該傳動組的軸向尺寸。18式中 ——按接觸疲勞強度估算的齒輪模數(shù)(mm) ,應圓整為標準值;jmP——電動機額定功率(kW) ;——被估算齒輪的計算轉速(r/min) ;jnu——大齒輪與小齒輪齒數(shù)之比;Z——小齒輪齒數(shù);φ m——齒寬系數(shù), φ m=B/m=6~10,B 為齒寬,m 為模數(shù);[σ j]——許用接觸應力( ) 。MPa齒輪計算轉速:軸Ⅲ-Ⅳ ,軸Ⅱ-Ⅲ ,軸Ⅰ-Ⅱin/35rnj?in/475rnj?in/670rnj?根據指導書表 2.3選擇齒輪材料為 45鋼(淬火處理) ,其接觸應力 σ j, 取MPa1258m??1)第一組齒輪: ; ; ;?in6701rn301?Z4.1u??????1.26701.85.633222 ??????uPjm??取標準值 12)第二對齒輪: ; ; ;?in4752rn?182?Z42u??????7.24510.6301630 22?????uPmjm??取標準值 23)第三對齒輪: ; ; ;?min35rn?23?Z41u??????67.235108.6011603223233 ?????uPj??取標準值??32)1(160jmj nuZP????19(2) 標準齒輪: **20h1c0.25???度 , ,從機械原理 表 5-3查得以下公式:齒頂圓 mzdaa)+(=*1齒根圓 ??chf ???2分度圓 z齒頂高 a*=齒根高 mchf)+(齒輪的具體值見表齒輪尺寸表齒輪 齒數(shù) z 模數(shù) m 分度圓 d 齒頂圓 a齒根圓 fd齒頂高 ah齒根高 f1 42 3 126 132 118.5 3 3.752 42 3 126 132 118.5 3 3.753 35 3 105 111 97.5 3 3.754 49 3 147 153 139.5 3 3.755 18 3 54 60 46.5 3 3.756 72 3 216 222 208.5 3 3.757 45 3 135 141 127.5 3 3.758 45 3 135 141 127.5 3 3.759 30 3 90 96 82.5 3 3.7510 60 3 180 186 172.5 3 3.7511 73 3 219 225 211.5 3 3.7512 37 3 111 117 103.5 3 3.7513 22 3 66 72 58.5 3 3.7514 88 3 264 270 256.5 3 3.7515 42 3 126 132 118.5 3 3.752016 25 3 75 81 67.5 3 3.754.3.4 齒寬確定由公式 ( 6~10,m 為模數(shù))得:mB??第一套嚙合齒輪 m25~1.0~Ⅰ??第二套嚙合齒輪 ??380I::第三套嚙合齒輪 6IB反轉嚙合齒輪 ??V10I??一對嚙合齒輪,為了防止大小齒輪因裝配誤差產生軸向錯位時導致嚙合齒寬減小而增大輪齒的載荷,設計上,應主動輪比小齒輪齒寬大所以 , , ,128,1Bm?318Bm?418,20,5,20,5,05 1976 ?Bm, 1413121865?4.4 帶輪結構設計查《機械設計》表 8-5確定參數(shù)得:????? 38,6,10,5,7.8,5.2,1min??fehbfap帶輪寬度: ????ezB213????大帶輪外徑: Da460小帶輪外徑: hd7852??4.5 軸承的選擇Ⅰ軸: 深溝球軸承Ⅱ軸: 圓錐滾子軸承Ⅲ軸: 圓錐滾子軸承 深溝球軸承21Ⅳ軸: 雙向推力球軸承 雙列圓柱滾子軸承4.6 片式摩擦離合器的選擇和計算片式摩擦離合器目前在機床中應用廣泛,因為它可以在運轉中接通或脫開,具有結合平穩(wěn)、沒有沖擊、結構緊湊的特點,部分零件已經標準化,多用于機床主傳動。(1) 確定摩擦片的徑向尺寸:摩擦片的外徑尺寸受到外形輪廓的限制,內徑又由安裝它的軸徑 d來決定,而內外徑的尺寸決定著內外摩擦片的環(huán)形接觸面積的大小,直接影響離合器的結構與性能。表示這一特性系數(shù) 是外片內徑 D1與內片外徑 D2之比,即??21?一般外摩擦片的內徑可?。篋 1=1.5d=1.5 36=42mm;?機床上采用的摩擦片 值可在 0.57~0.77 范圍內,此處取 =0.67,則內摩擦片外徑 ,取2?1?m7.62.04632?(2) 按扭矩確定摩擦離合面的數(shù)目 Z:Z≥ ZmVfKrSPT?][其中 T為離合器的扭矩 ;mNnNj ????? 48.795.06950?K——安全系數(shù),此處取為 1.3;[P]——摩擦片許用比壓,取為 1.2MPa;f——摩擦系數(shù),查得 f=0.06;S——內外片環(huán)行接觸面積,S (D 22 — D12)=1730.93mm 2;4??——誘導摩擦半徑,假設摩擦表面壓力均勻分布,則fr fr=37.53mm;)(3213?KV——速度修正系數(shù),根據平均圓周速度查表取為 1.08;22——結合次數(shù)修正系數(shù),查表為 1.5;mK——摩擦結合面數(shù)修正系數(shù), 查表取為 1;Z將以上數(shù)據代入公式計算得 Z=11.8≥11.1,圓整為整偶數(shù) 12,離合器內外摩擦片總數(shù) i=Z+1=13。(3) 計算摩擦離合器的軸向壓力 Q:??NKPSQv 3.2408.193.17???(4) 摩擦片厚度 b = 1, 1.5,1.75,2 毫米,一般隨摩擦面中徑增大而加大。內外片分離時的最小間隙為(0.2~0.4)mm。(5) 反轉時摩擦片數(shù)的確定:普通車床主軸反轉時一般不切削,故反向離合器所傳遞的扭矩可按空載功率損耗確定。普通車床主軸高速空轉功率 Pk一般為額定功率 P的 20~40%,取 Pk = 0.4P,計算反轉靜扭矩為 Pk = 2.2KW,代入公式計算出 Z=6.98≥4.5,圓整為整偶數(shù) 8,離合器內外摩擦片總數(shù)為 9。根據 JB/T9190-1999選用機械式多片雙聯(lián)離合器,因為安裝在箱內,所以采取濕式。查表可得離合器參數(shù) H=2.5,模數(shù) m=2.5。查《離合器手冊》表 1.2.6選用編號為 2的離合器。235. 動力設計5.1 軸驗算按彎扭合成校核經分析選危險軸Ⅰ軸進行校驗(1)畫受力簡圖畫軸空間受力簡圖,將軸上作用力分解為垂直面受力圖和水平面受力圖分別求出垂直面上的支反力和水平面內的支反力。對于零件作用于軸上的分布載荷或轉矩當作集中力作用于軸上零件的寬度中心。(2)軸上受力分析軸傳遞的轉矩: ?1T NmnP7466095.15.905.96 ????齒輪的圓周力: NdFt 8.423齒輪的徑向力:由機械設計取 ,??20?tgFr32.516??(3)計算作用于軸上的支反力水平面內的支反力:,NFRtHA84953?RHB56垂直面內的支反力, rVA310VB20(4)計算軸的彎、轉矩,并畫彎、轉矩圖分別作出垂直面和水平面上的彎矩圖,并按 進行彎矩合成 .畫轉矩圖。HVM??(5)校驗軸的強度一般而言,軸的強度是否滿足只需對危險截面進行校驗即可,而軸的當量彎矩較大且軸的直徑最小處。24截面處的當量彎矩為 ??22HVMaT??轉矩按脈動循環(huán)變化計算,取 ,則6.0??mNT??45676.0?=12836722213?? mN?強度校合:考慮鍵槽的影響,查機械設計附表 12.8計算,MPaW54.70.863??選擇軸材料為 45鋼,經調質處理,查機械設計表 12.3??MPa60b1???顯然, 校驗合格,故軸安全。??b1??軸上受力分析及彎矩、轉矩圖255.2 主軸驗算5.2.1 選定前端懸伸量 a,參考《機械裝備設計》P121,根據主軸端部的結構,前支承軸承配置和密封裝置的型式和尺寸,這里選定 a=120mm.5.2.2 主軸支承跨距 L的確定一般最佳跨距 考慮到結構以及支承剛度因磨損會,420~)5.32(0 ma?不斷降低,應取跨距 L比最佳支承跨距 大一些,再考慮到結構需要,這里取LL=540mm。5.2.3 計算 C點撓度1)周向切削力 的計算tP429510dtjNpDn???其中 89.0.,5.3 ??????齒軸 承?KWNdmin/8,240 ,24~40)6.~()6~(axrDmjj ?取26故, ,Npt 341059.48520.19????,Pt 3.1 NPr 3310.214.504. ????軸上受力分析 mdpTt 96283?, 2trM??合 ???????223)(4)(ptzrrM2)驅動力 Q的計算參考《車床主軸箱指導書》 , 72.10Nnz??其中27min/85,372,895.4.05 rZKWNd ?????所以 NQ37109.4852.1.2?3)軸承剛度的計算這里選用雙列圓柱滾子軸承根據 求得:0.13.82.5Cd??mNBA /102.97.2.058.13 ???4)確定彈性模量,慣性距 I; ;和長度 。c,abs①軸的材產選用 45鋼,查《簡明機械設計手冊》P6,有 52.10EMP??②主軸的慣性距 I為:??464.27106DI m?????外 內主軸 a段的慣性距 可近似地算:c??446425106cI?????11③切削力 P的作用點到主軸前支承支承的距離 S=C+W,對于普通車床,W=0.4H, (H 是車床中心高,設 H=200mm)。則: 120.420Sm????④根據齒輪、軸承寬度以及結構需要,取 b=60mm⑤計算切削力 P作用在 S點引起主軸前端 C點的撓度??23226cspcAALSsscy mEIIL?? ???? ?? ?代入數(shù)據并計算得 =0.1299mm。csp⑥計算驅動力 Q作用在兩支承之間時,主軸前端 C點的撓度 cmqy28????2226cmq BAbLbLCbcyQmEI L????? ??? ?? ?計算得: =-0.0026mmcq⑦求主軸前端 C點的終合撓度 cy水平坐標 Y軸上的分量代數(shù)和為 oscsos,pmqcmyy????,計算得: =0.0297mm. 。6,270,18pqm??????其 中 c0.928z?綜合撓度 。綜合撓度方向角.cycz?,又 。因為ar72.5zyccytg????0.2.06.12L??,所以此軸滿足要求。???5.2 齒輪校驗在驗算算速箱中的齒輪應力時,選相同模數(shù)中承受載荷最大,齒數(shù)最小的齒輪進接觸應力和彎曲應力的驗算。這里要驗算的是齒輪 2,齒輪 7,齒輪 12這三個齒輪。齒輪 12的齒數(shù)為 18,模數(shù)為 4,齒輪的應力:1)接觸應力: ??4108vasf jukNQzmBn????u----大齒輪齒數(shù)與小齒輪齒數(shù)之比;---齒向載荷分布系數(shù); ----動載荷系數(shù); ----工況系數(shù); ----壽命k? vkAksk系數(shù)查《機械設計》表 10-4及圖 10-8及表 10-2分布得1.5,.20;1.5,.2HBFBvAkk??假定齒輪工作壽命是 48000h,故應力循環(huán)次數(shù)為 96051480.1hNnjL???次查《機械設計》圖 10-18得 ,所以:.9,.FHNK?2923 3721.501.297.506.98208 1.047148f MPa????????????? ??2)彎曲應力:52190vaswjkNQzmBYn???查《金屬切削手冊》有 Y=0.378,代入公式求得: =158.5Mpa wQ查《機械設計》圖 10-21e,齒輪的材產選 45鋼(整淬處理) ,大齒輪、小齒輪的硬度為 60HRC,故有 ,從圖 10-21e讀出 。1650fMPa?????? ??920wMPa??因為:,故滿足要求,另外兩齒輪計算方法如上,均符合要求。??,ffw??????6.結構設計6.1 I 軸(輸入軸)的設計將運動帶入變速箱的帶輪一般都安裝在軸端,軸變形較大,結構上應注意加強軸的剛度或使軸部受帶的拉力(采用卸荷裝置) 。I 軸上裝有摩擦離合器,由于組成離合器的零件很多,裝配很不方便,一般都是在箱外組裝好 I軸在整體裝入箱內。我們采用的卸荷裝置一般是把軸承裝載法蘭盤上,通過法蘭盤將帶輪的拉力傳遞到箱壁上。車床上的反轉一般用于加工螺紋時退刀。車螺紋時,換向頻率較高。實現(xiàn)政反轉的變換方案很多,我們采用正反向離合器。正反向的轉換在不停車的狀態(tài)下進行,常采用片式摩擦離合器。由于裝在箱內,一般采用濕式。在確定軸向尺寸時,摩擦片不壓緊時,應留有 0.2~0.4 的間隙,間隙應能m調整。離合器及其壓緊裝置中有三點值得注意:1) 摩擦片的軸向定位:由兩個帶花鍵孔的圓盤實現(xiàn)。其中一個圓盤裝30在花鍵上,另一個裝在花鍵軸上的一個環(huán)形溝槽里,并轉過一個花鍵齒,和軸上的花鍵對正,然后用螺釘把錯開的兩個圓盤連接在一起。這樣就限制了軸向和周向德兩個自由度,起了定位作用。2) 摩擦片的壓緊由加力環(huán)的軸向移動實現(xiàn),在軸系上形成了彈性力的封閉系統(tǒng),不增加軸承軸向復合。3) 結構設計時應使加力環(huán)推動擺桿和鋼球的運動是不可逆的,即操縱力撤消后,有自鎖作用。I軸上裝有摩擦離合器,兩端的齒輪是空套在軸上,當離合器接通時才和軸一起轉動。但脫開的另一端齒輪,與軸回轉方向是相反的,二者的相對轉速很高(約為兩倍左右) 。結構設計時應考慮這點。齒輪與軸之間的軸承可以用滾動軸承也可以用滑動軸承?;瑒虞S承在一些性能和維修上不如滾動軸承,但它的徑向尺寸小。空套齒輪需要有軸向定位,軸承需要潤滑。6.2 齒輪塊設計齒輪是變速箱中的重要元件。齒輪同時嚙合的齒數(shù)是周期性變化的。也就是說,作用在一個齒輪上的載荷是變化的。同時由于齒輪制造及安裝誤差等,不可避免要產生動載荷而引起振動和噪音,常成為變速箱的主要噪聲源,并影響主軸回轉均勻性。在齒輪塊設計時,應充分考慮這些問題。齒輪塊的結構形式很多,取決于下列有關因素:1) 是固定齒輪還是滑移齒輪;2) 移動滑移齒輪的方法;3) 齒輪精度和加工方法;變速箱中齒輪用于傳遞動力和運動。它的精度選擇主要取決于圓周速度。采用同一精度時,圓周速度越高,振動和噪聲越大,根據實際結果得知,圓周速度會增加一倍,噪聲約增大 6dB。工作平穩(wěn)性和接觸誤差對振動和噪聲的影響比運動誤差要大,所以這兩項精度應選高一級。為了控制噪聲,機床上主傳動齒輪都要選用較高的精度。大都是用 7—6—6,